By Ron Ceridono – -Images by Chadly Johnson
Go to any automotive event and chances are the cars with the most outrageous features will draw the attention of the casual onlooker. But for true enthusiasts it’s the subtle details, like the extra effort put into body fit and panel alignment that catch the eye of the knowledgeable. These are the cars that get better the more you look at them, which is typical of the cars that come out of MetalWorks Classic Auto Restoration in Eugene, Oregon.
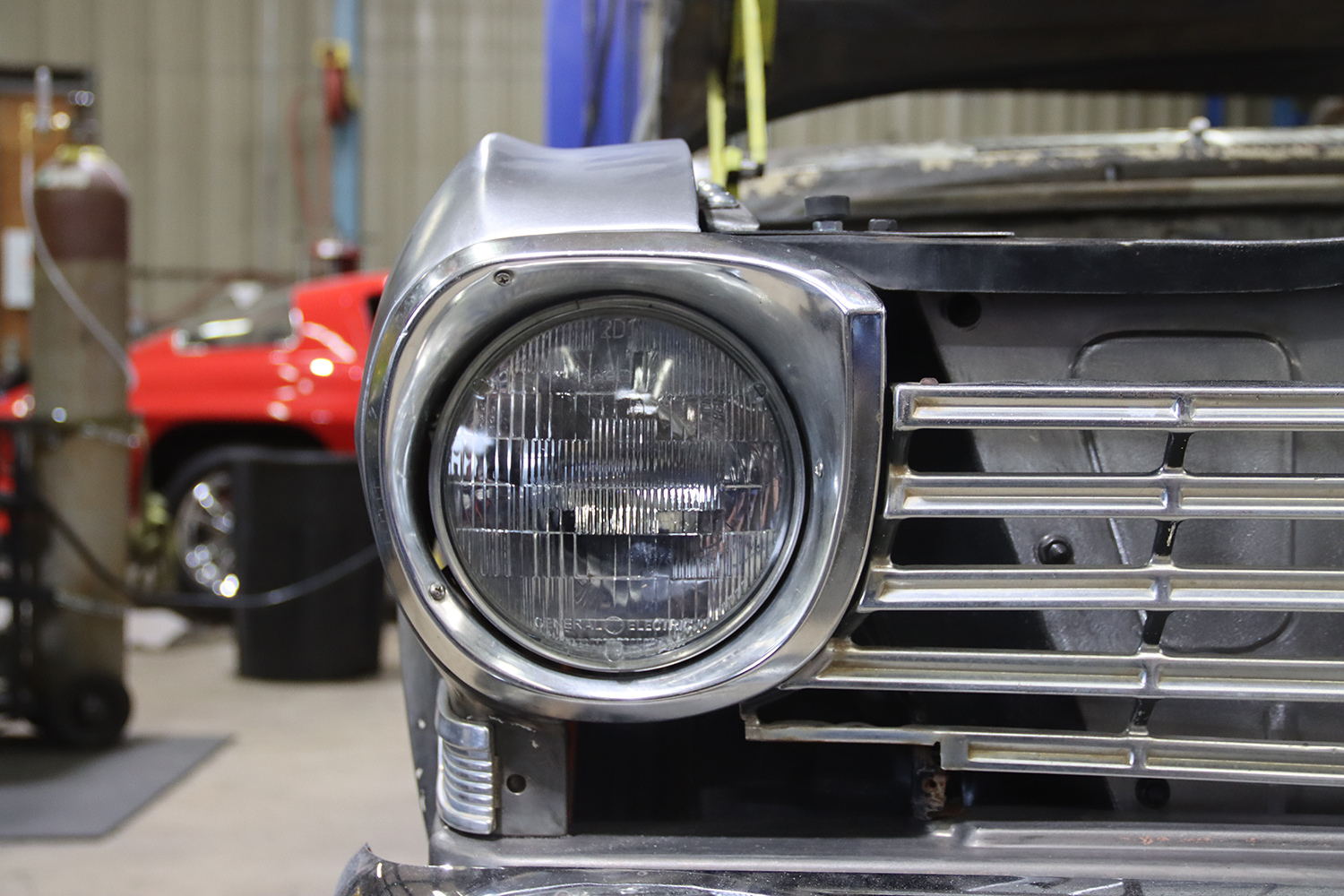
Case in point is a 1963 Chevy II. This GM line of compact cars was meant to compete with the likes of the Rambler, Ford’s Falcon, Chrysler’s Valiant/Lancer, and a number of GM products, including Chevy’s own Corvair. Like all the cars in this class, the Chevy II was affordable with a base price around $2,100.
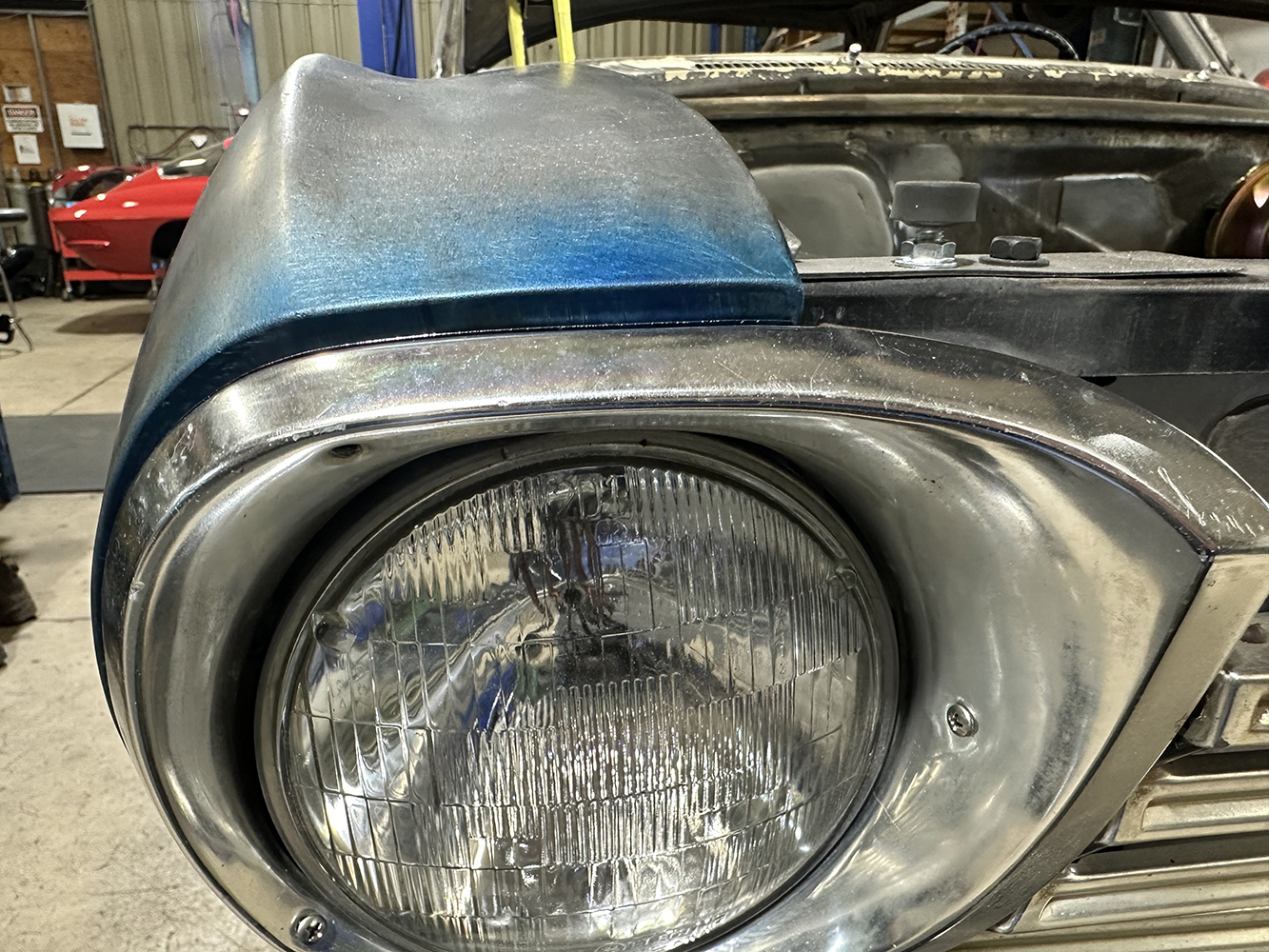
Like most cars of the era, Chevy’s quality control was described by some automotive writers as “lacking” in 1963. Poor door and window fit were common complaints and body panels were often gapped and aligned poorly. But one of the most noticeable issues with the Chevy II shown here was the mismatch between the headlight bezels and the front fenders. It makes one wonder if the team designing the fenders and those responsible for the headlight bezels ever met. There was no way the crew at MetalWorks was going to let something like this go unresolved, so master metal man Dave Williams was assigned the task of making things right.
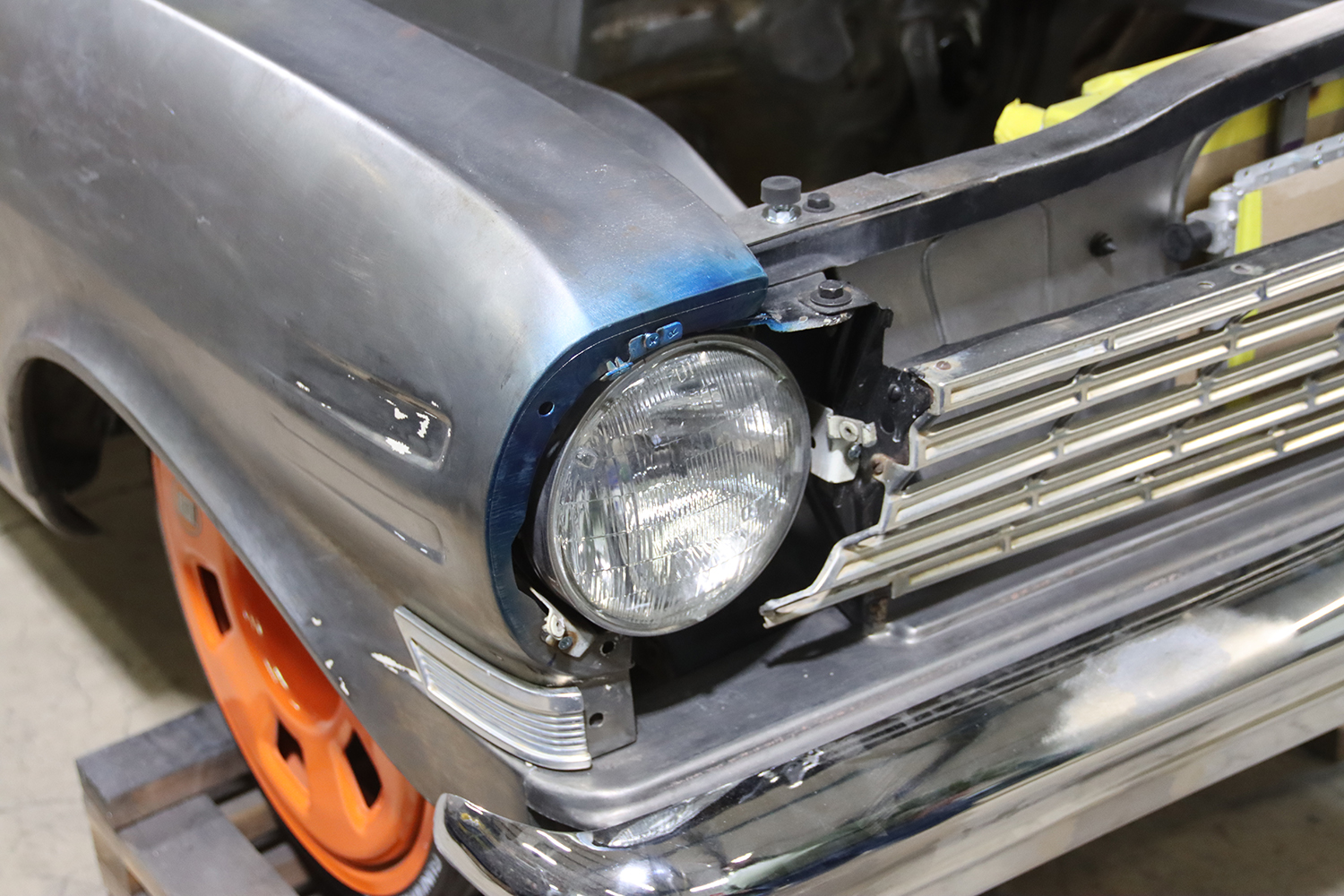
The first step in resolving the Chevy’s fitment issue was to come up with replacements for the rough original headlight bezels—fortunately a new old stock set was found on eBay. The next chore was to modify the fenders to make them fit. Williams carefully split the front edge of the first fender. He then made horizontal relief cuts to allow it to be recontoured to fit the headlight bezels properly. With the first fender altered, cardboard templates were made to be used to make the second fender the exact same shape.
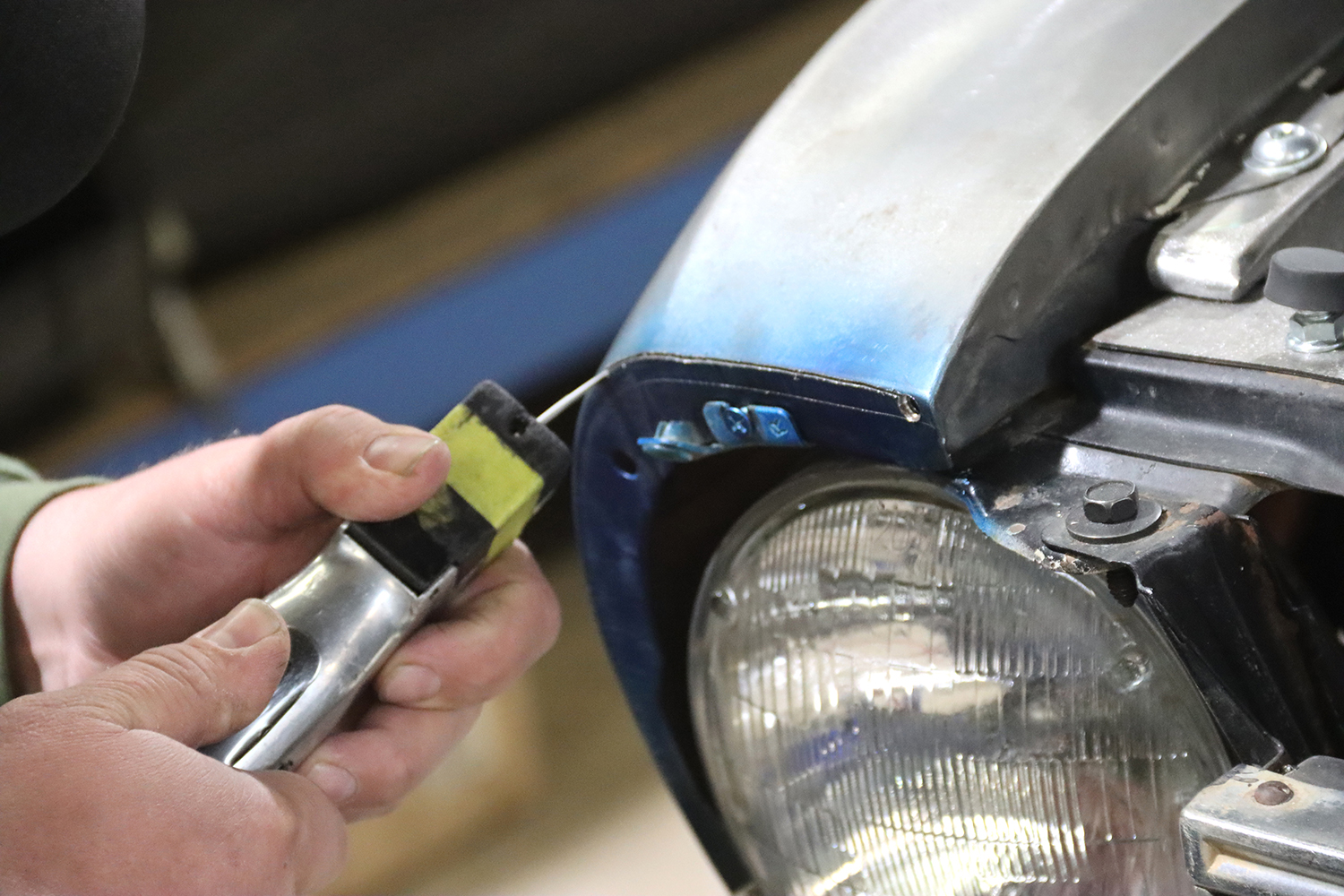
While talking to Williams about what was done, he did offer some advice. Although some builders use straight carbon dioxide when MIG welding mild steel (because it’s cheap), Williams suggests 75 percent argon and 25 percent carbon dioxide. He also suggests 0.023 “EZ Grind” welding wire. This softer wire makes grinding the welds much easier.
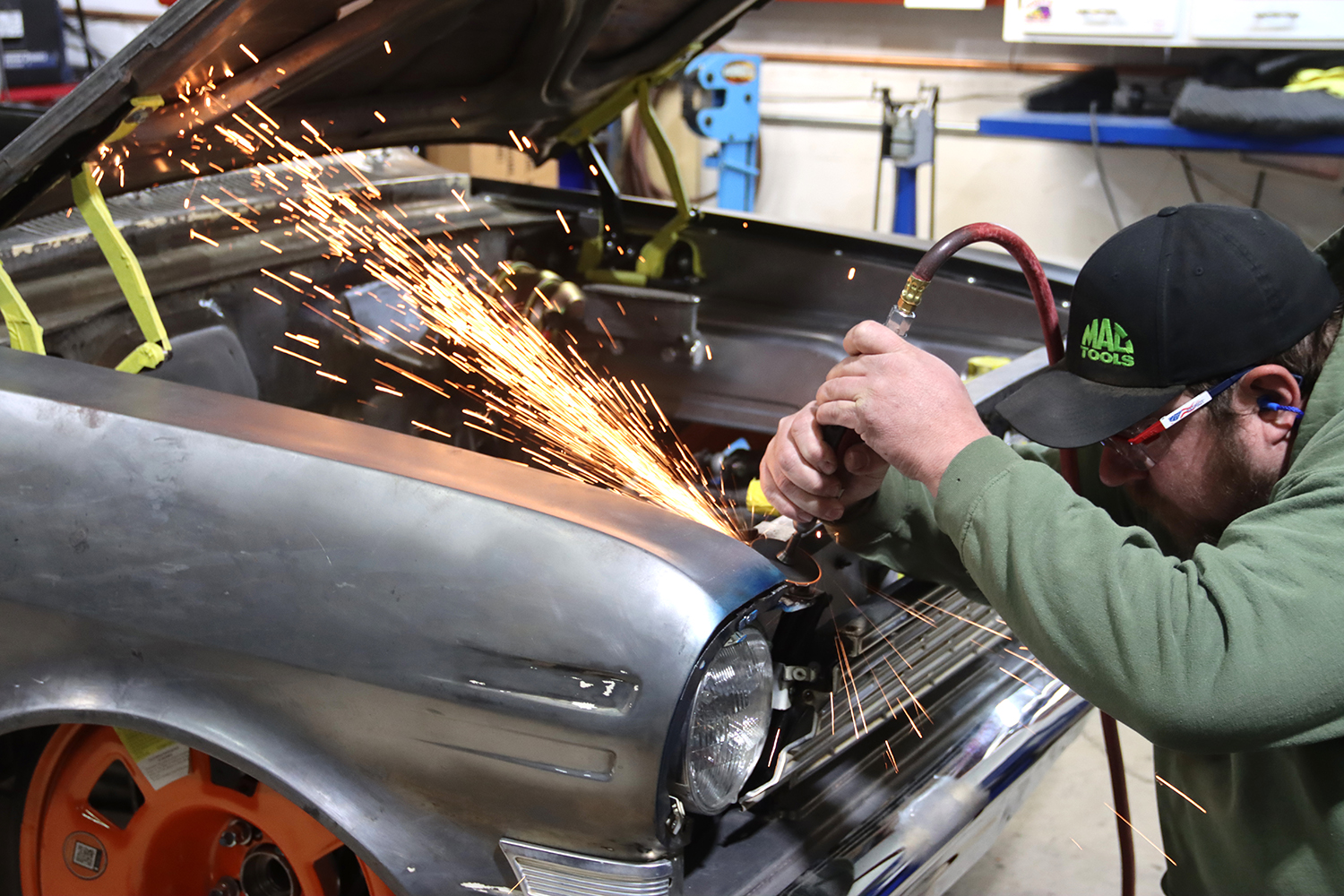
There’s no question that over-the-top modifications are attention getters, but it’s often the simple details that make a car standout. Sometimes a nip and a tuck are all it takes.

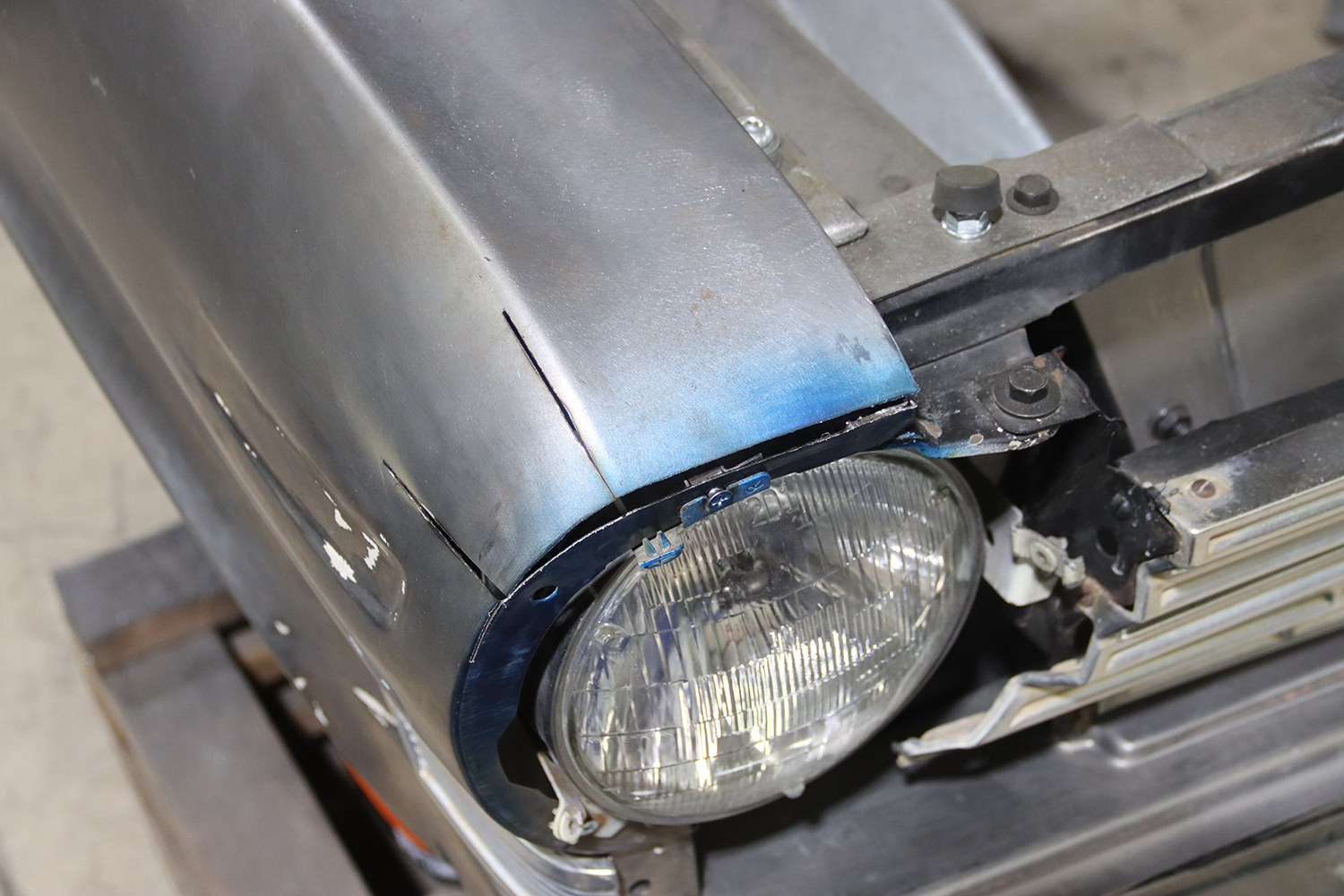
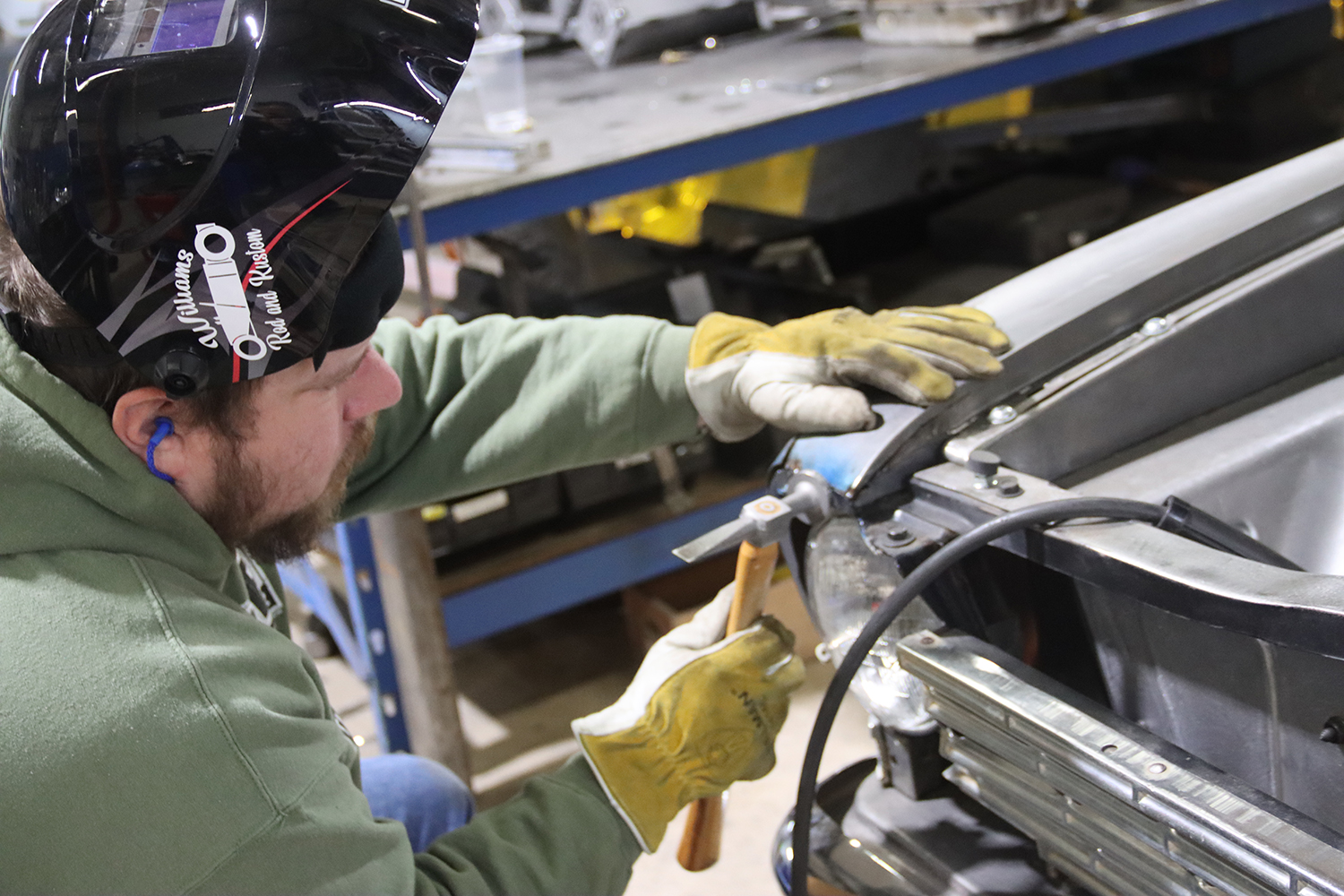
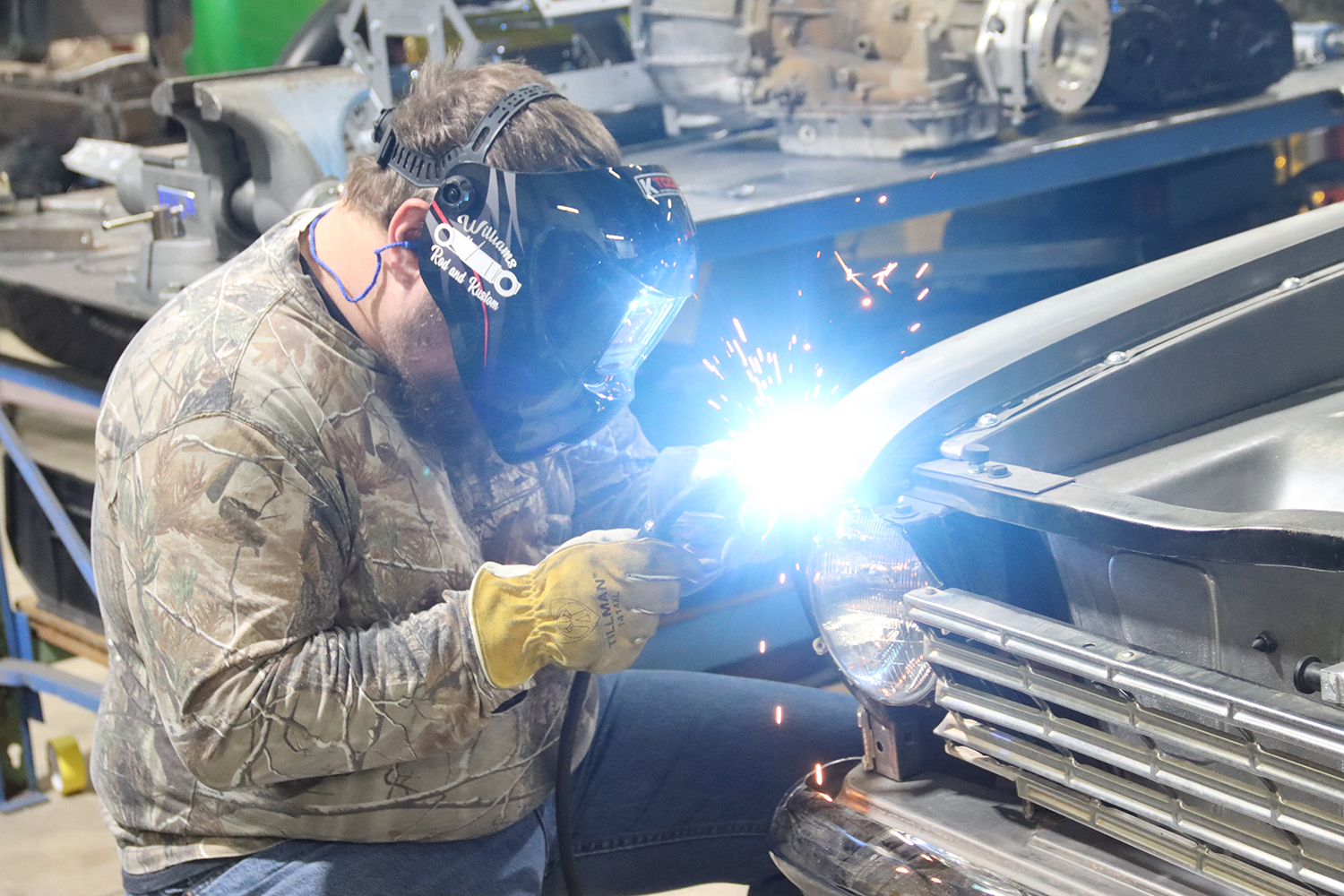
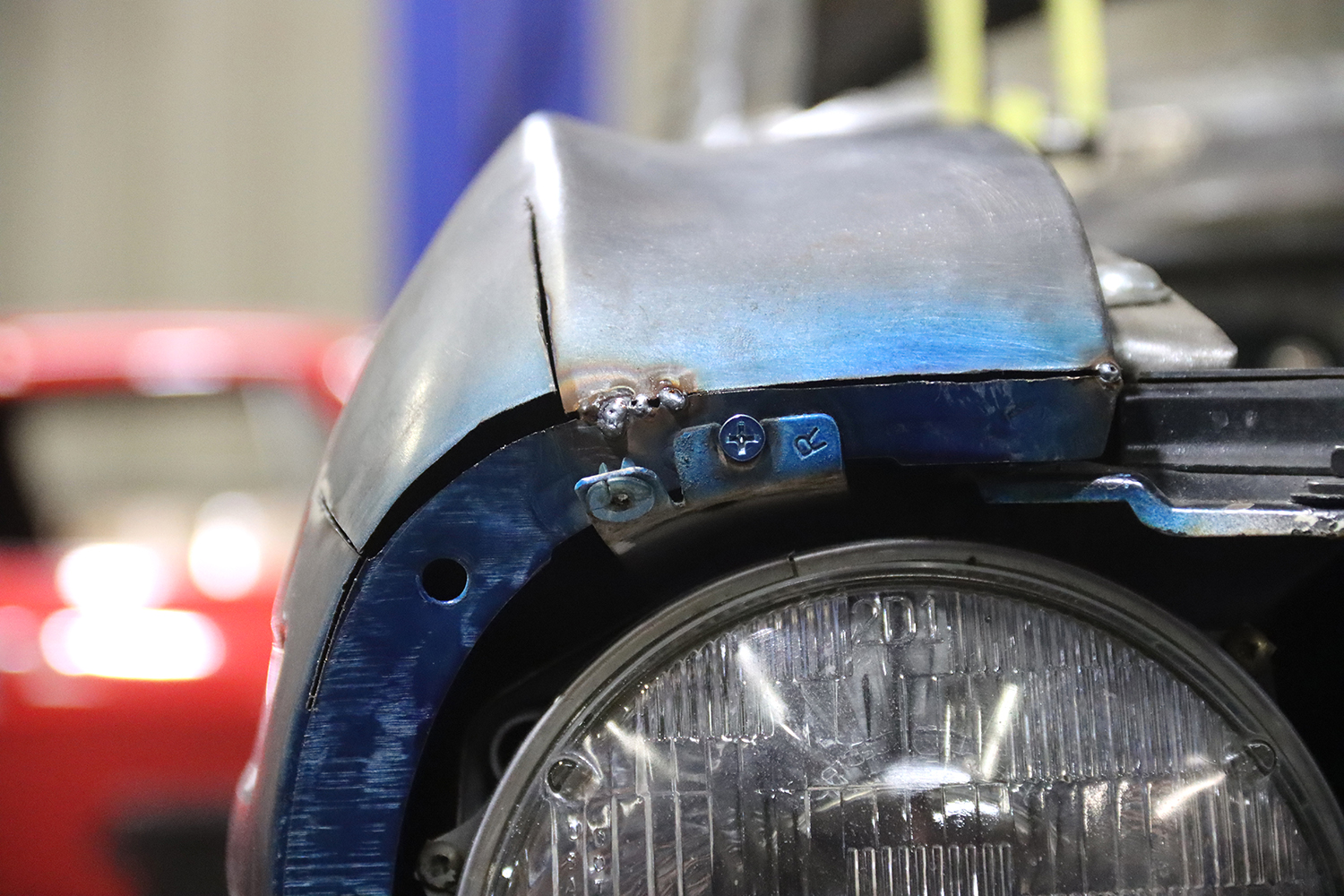
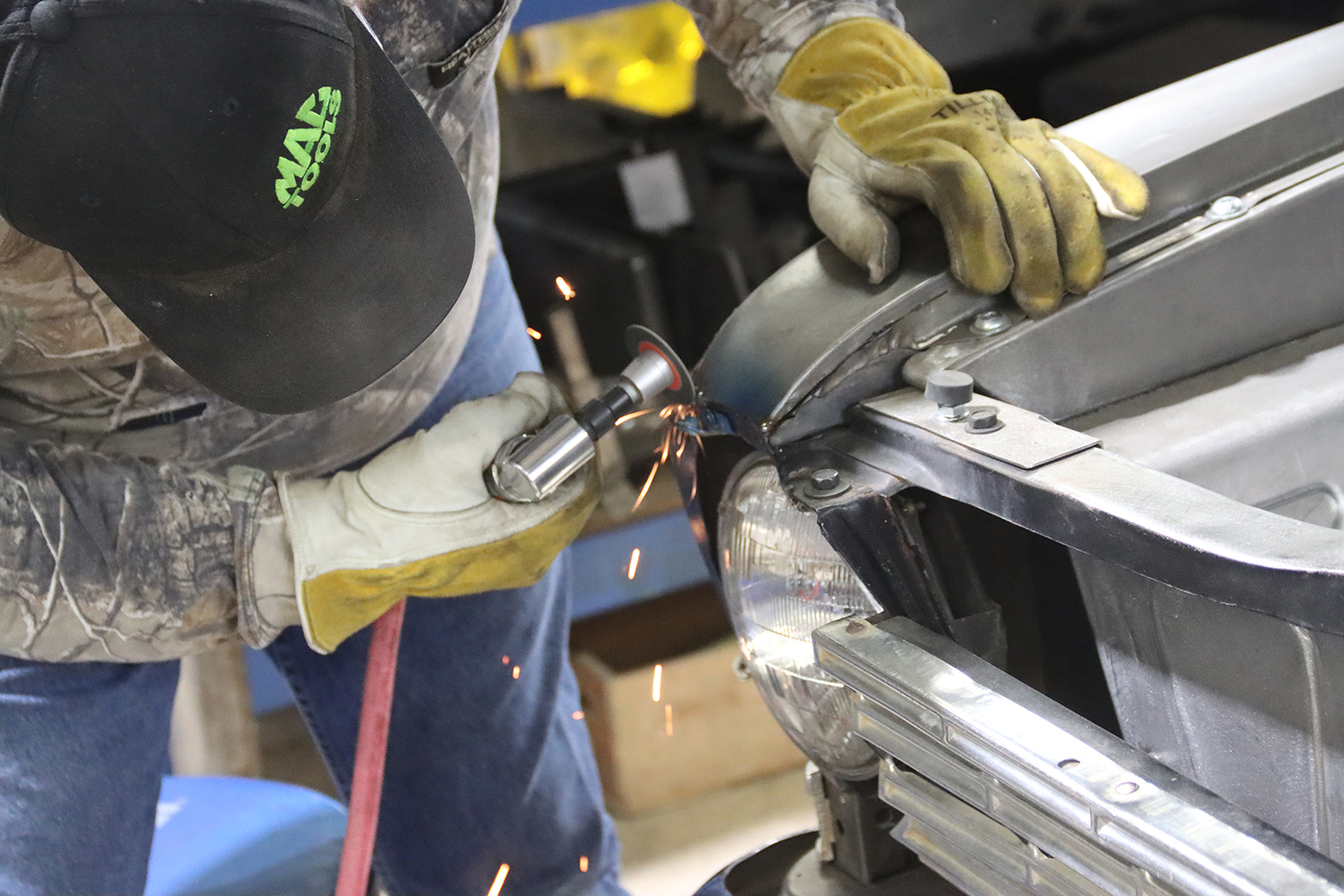

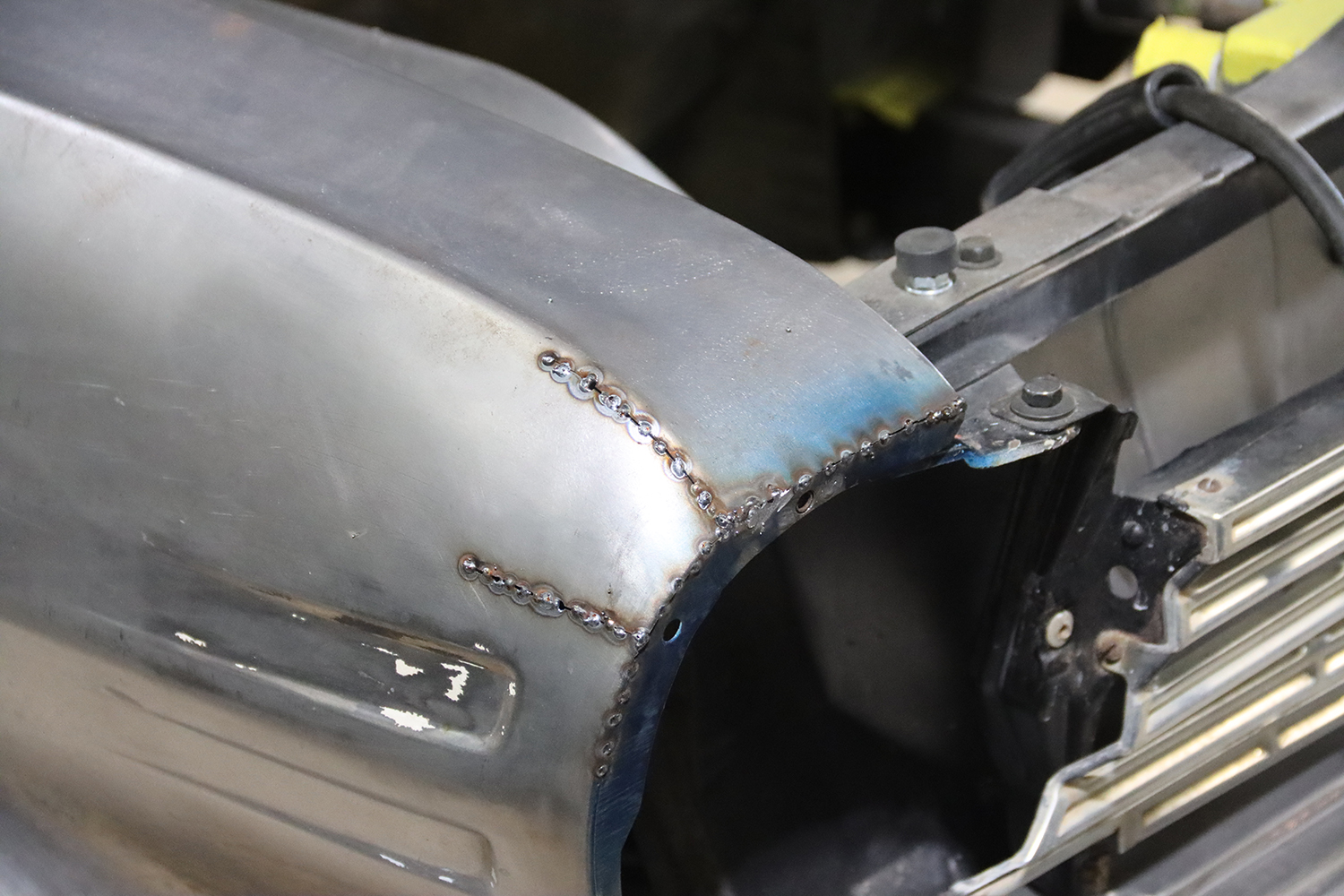
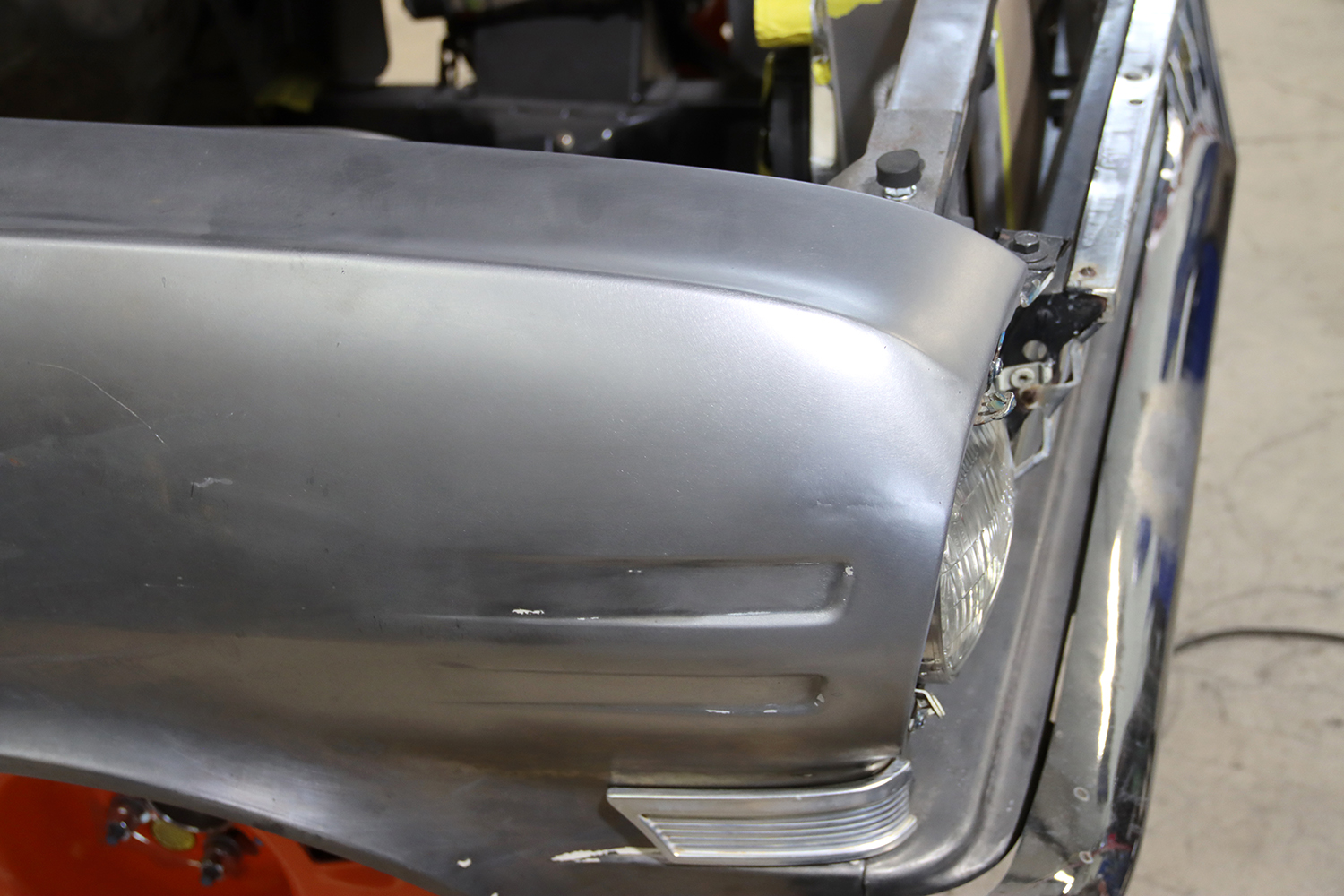
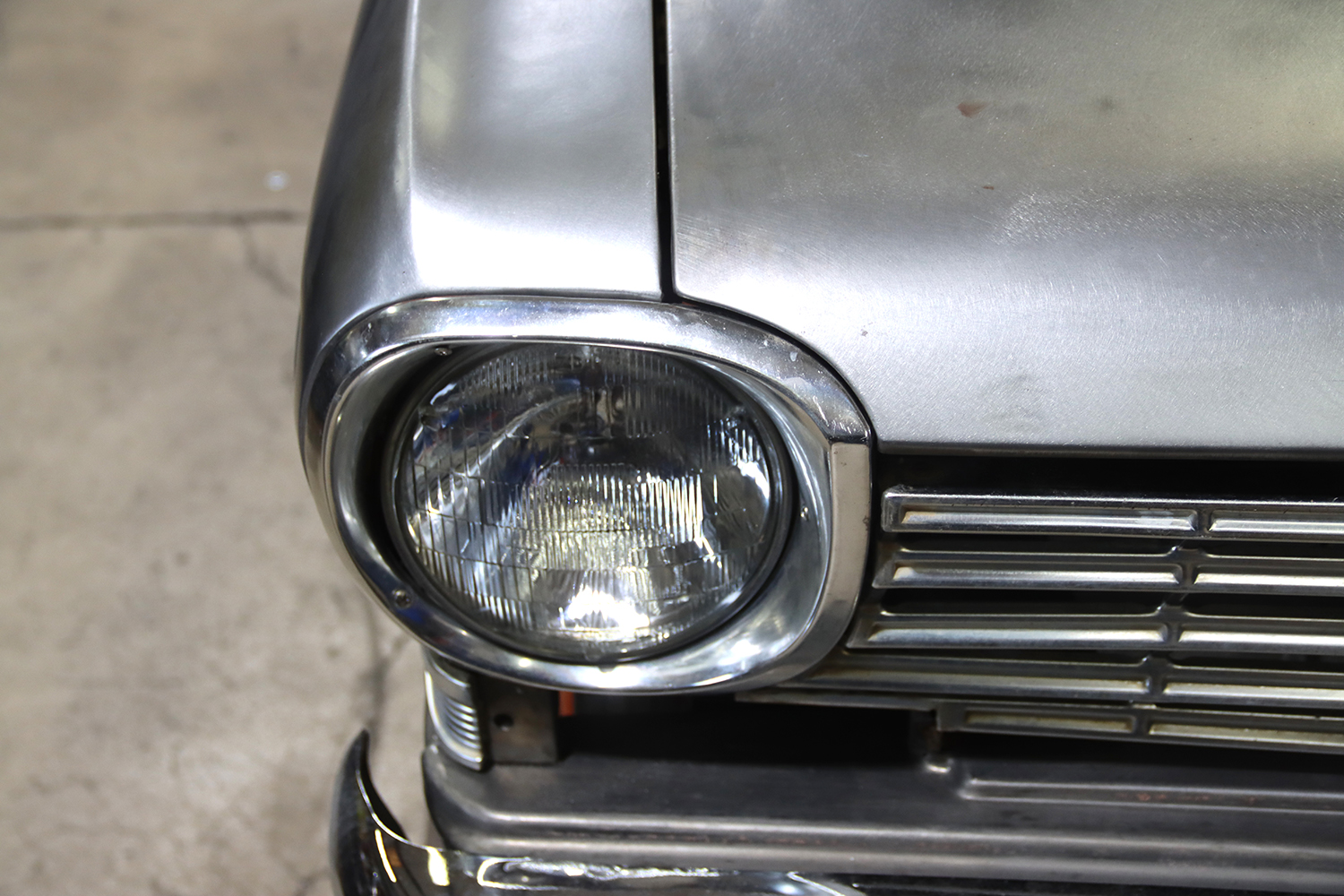
Check out this story in our digital edition here.
Source
MetalWorks Classic Auto Restoration
(541) 592-7894
metalworksclassics.com