By Ron Covell – Photography By Shawn Holloway – Artwork By Eric Brockmeyer
From 1949-1951, the Mercury was the premier car to be customized in the post–World War II era. Scott’s Hotrods ’N Customs, in Knoxville, Tennessee, has embarked on a project to build a state-of-the-art 1951 Merc convertible in the traditional style. These cars are very difficult to find these days, and after stripping their customer’s car down to bare metal, they uncovered a lot of sub-standard work. Fortunately, the customer had the will and the means to make everything top notch, so the crew at Scott’s cut away the defective work and ensured the project’s foundation was in shipshape before embarking on the modifications.
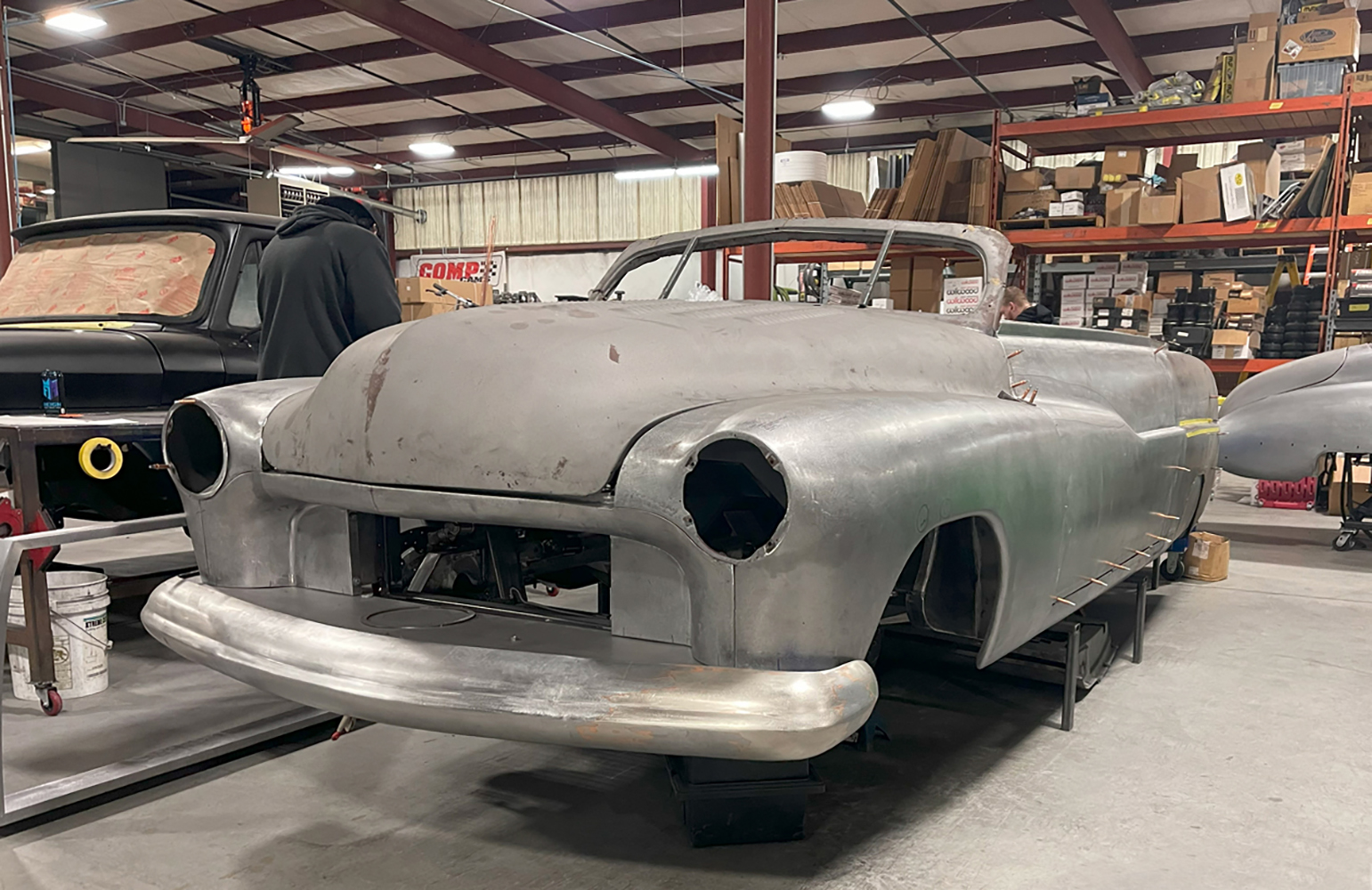
Eric Brockmeyer was called in to make renderings to guide the construction. The car they started with was originally a four-door sedan, and when the previous builder turned it to a convertible, the front doors were left stock length, which was badly out of proportion for a two-door body style. Since much of the four- to two-door conversion had to be redone, they decided to make the doors even longer than the OEM convertible doors would have been. They extend back to the point where the roof fabric meets the quarter-panel, giving the car a very sleek look and making it much easier to enter and exit the rear seats.
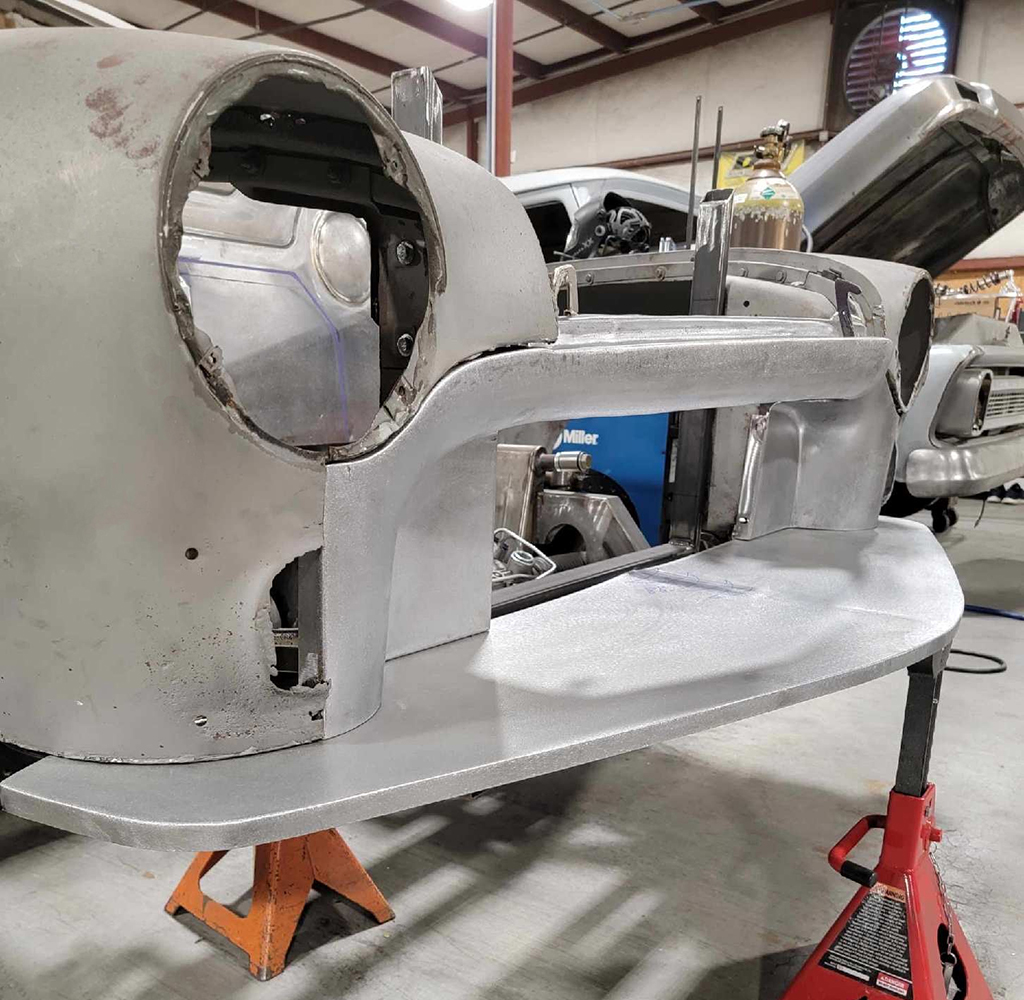
Scott’s built the custom airbag chassis for the car. The windshield and custom-made convertible top will be tastefully chopped, a modified 1957 Corvette grille will be fitted, and the hood and decklid corners will be rounded. A one-piece, curved glass windshield will be fitted, the bumpers will be smoothed and black-chrome plated, and the headlights will be frenched (recessed). This article will look at extending the front fenders and Frenching the headlights. Shawn Holloway, one of the leading sheetmetal fabricators at Scott’s, was called on to take charge of this project.
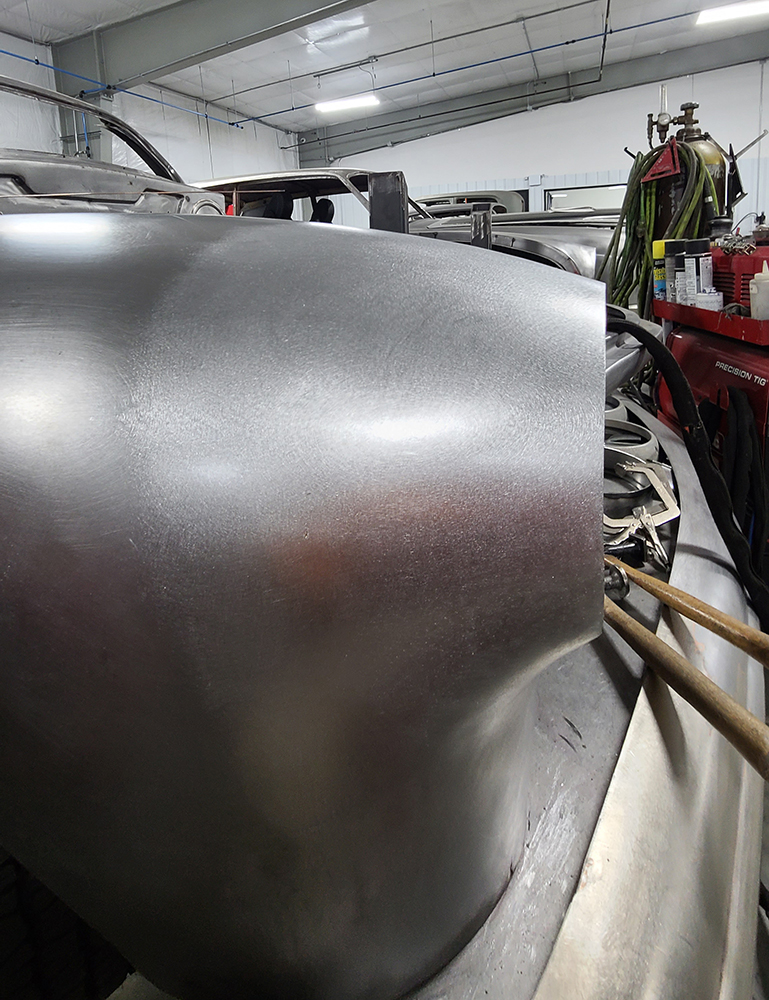
The original headlights on the Merc were nearly flush with the hood, so the first step was to shape new metal to extend the fenders by about 1-1/2 inches. Once the new metal was welded in place and metal finished, work could begin on the rings that would be used to recess the headlights.
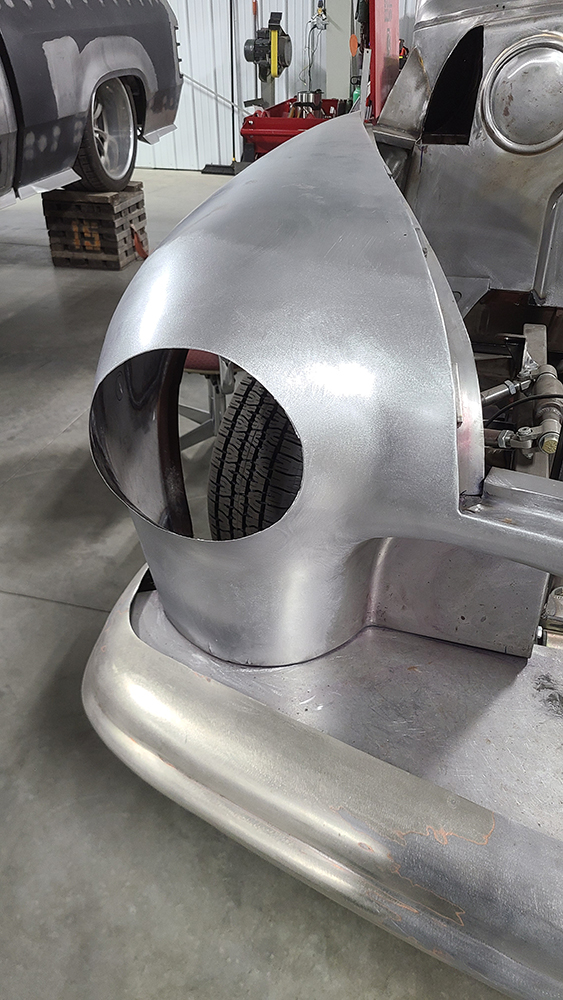
The tunneled section is a ring rolled from 18-gauge sheetmetal, but it needed flanges on both the front and rear edges to facilitate attachment to the fenders and to mount the sealed-beam lights and adjusters. These flanges were made from 1/8-inch plates to give them more rigidity. This becomes important when welded into place since thinner metal could easily warp from welding heat.
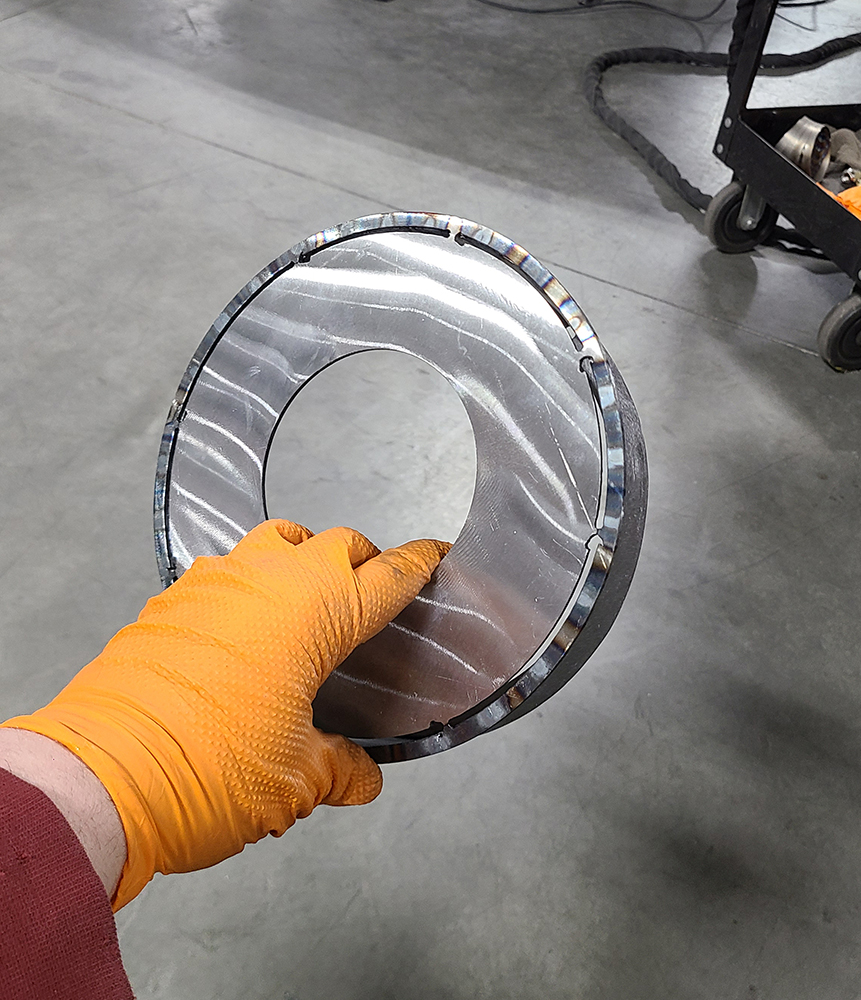
Once the flanges were welded to the tunnels and the welds were smoothed, the openings in the fenders were trimmed to fit. This is a very sensitive job since both lights must be at the same height, the same distance from the center, and in the same plane. Lots of measuring and adjusting were done at this stage to ensure symmetry.
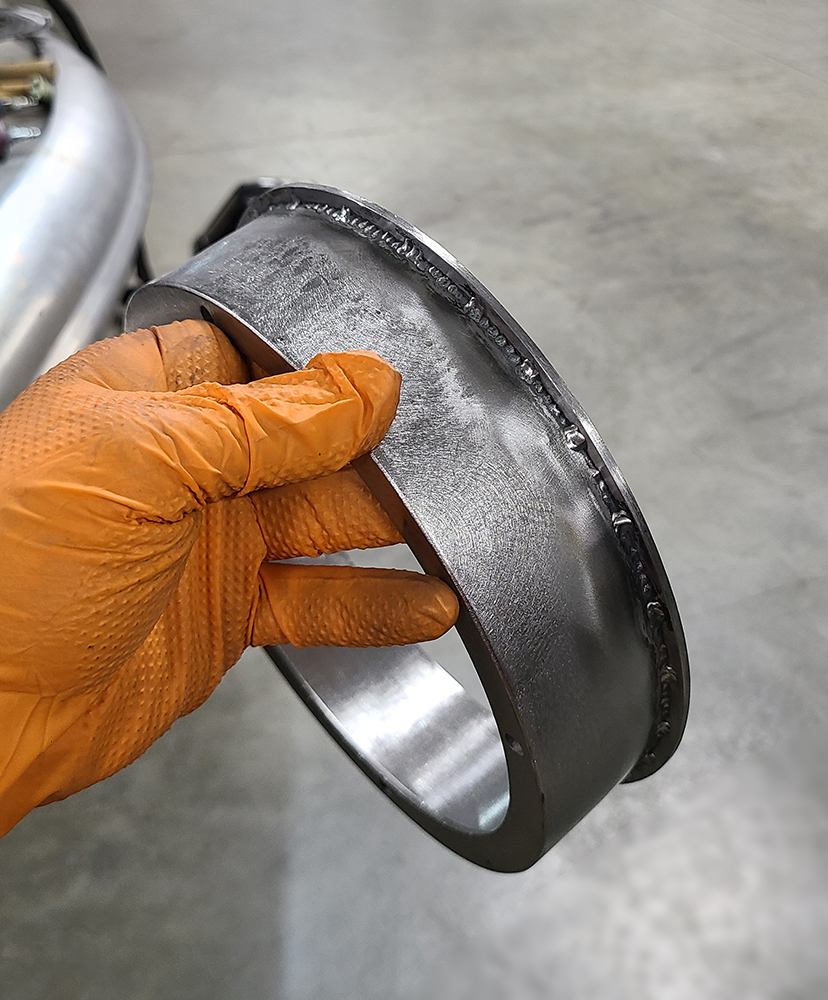
The headlight tunnels were tack welded into place and everything was double-checked before finishing welding. After welding, all the exterior joints were metal-finished to perfection, the headlight buckets were installed, and the job was complete.
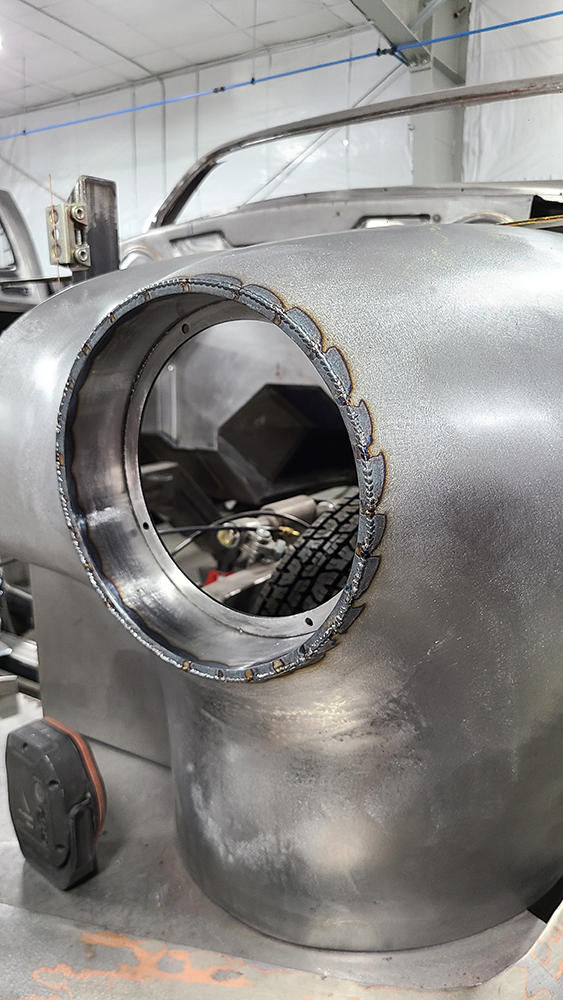
The same techniques used for this job could be applied to virtually any car, and Frenching headlights is a custom car tradition that has been popular for generations. Check out this story in our digital edition here.
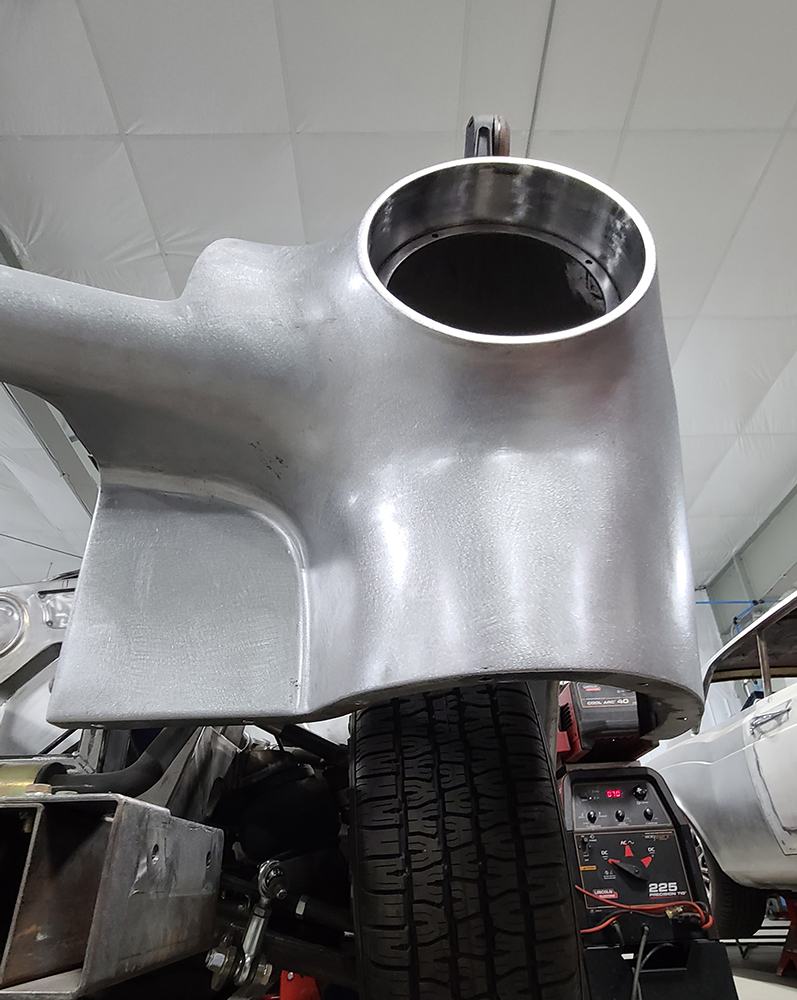
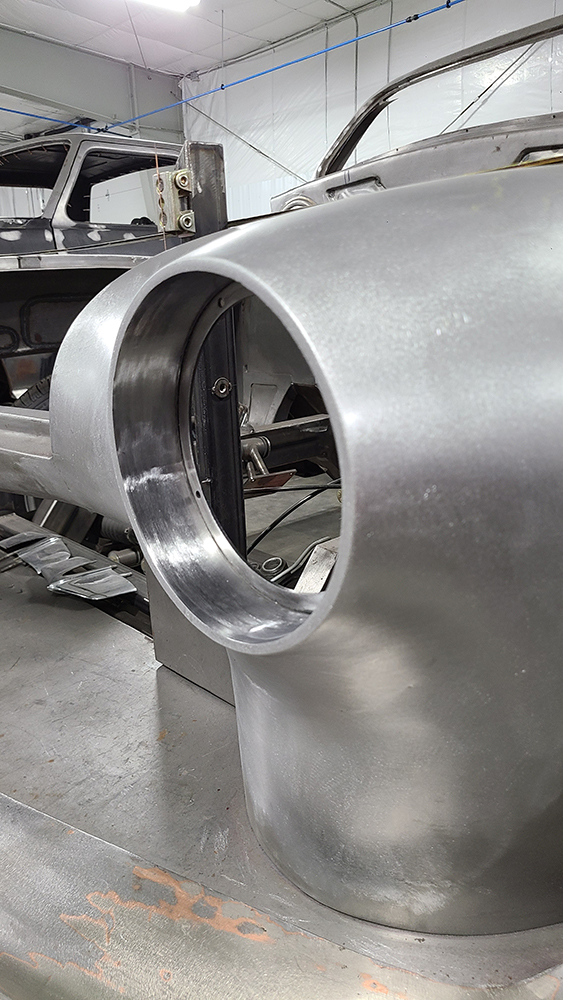
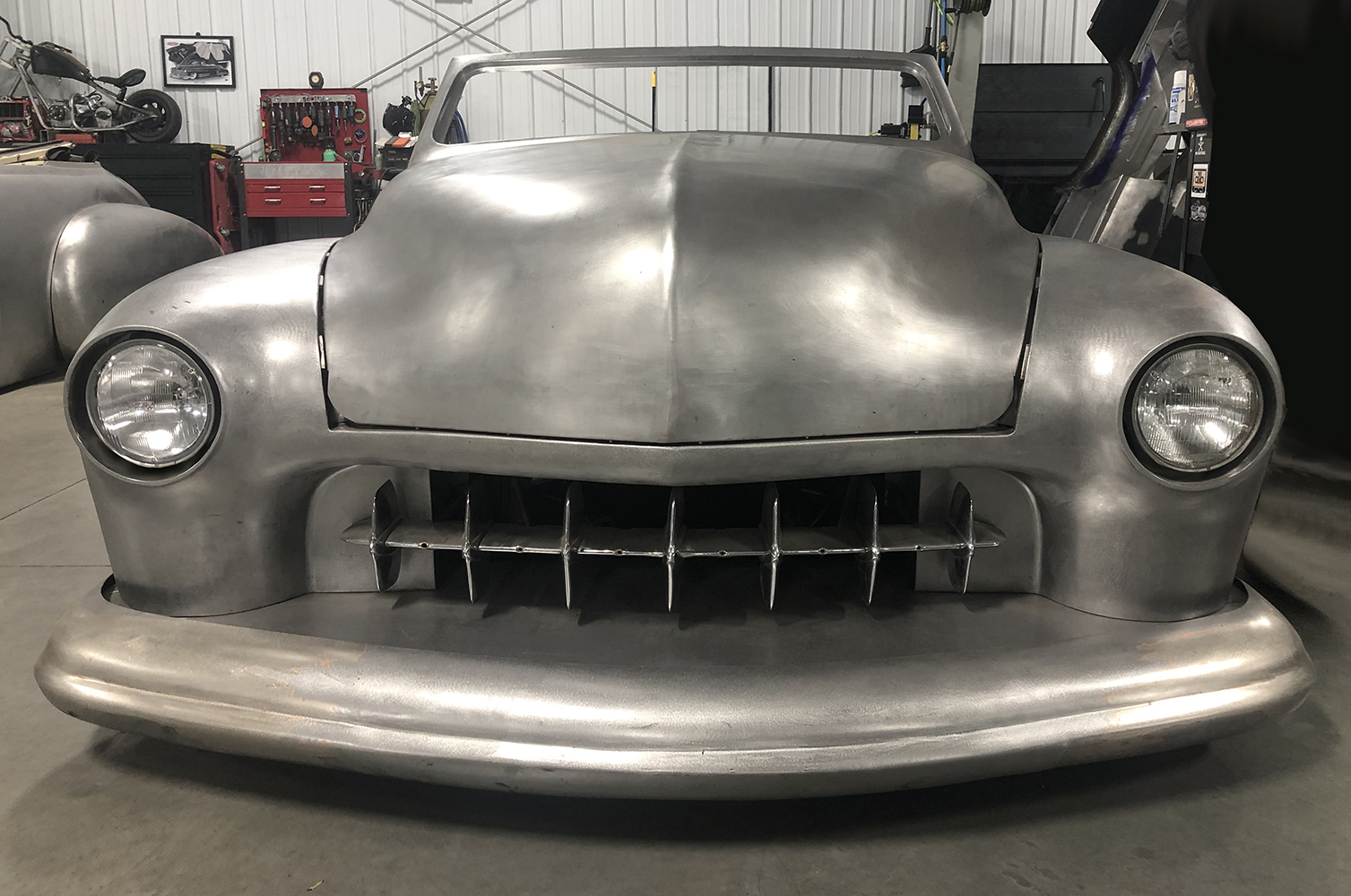
Source
Scott’s Hotrods ‘N Customs
(865) 951-2081
scottshotrods.com