Everything You Need To Know About TIG Welding
By Ron Covell – Photography By the Author
We’ve covered MIG welding, which for many years has been the most widely used process for both amateur and professional car builders. Since MIG welds are strong and fast, and the learning curve is easy to master, why would you consider anything else? That’s exactly what we’ll cover in the basics of TIG welding.
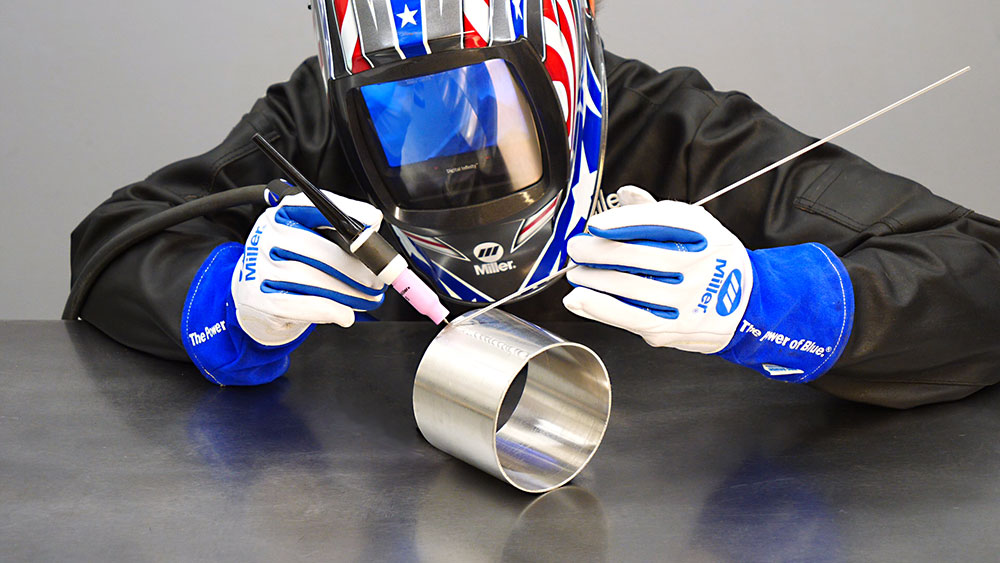
MIG Vs TIG Welding
Fundamentally, it comes down to the degree of control that TIG welding offers, and the broader spectrum of metals it is suited for. MIG is used primarily for carbon steel and stainless steel, and certain MIG welding machines can be equipped to weld aluminum, but the TIG process works with virtually any weldable metal. There may be times when you need to weld magnesium, copper, bronze, titanium, or Inconel, and the TIG process is well suited for all of these—and more.
Read More: How to MIG Weld
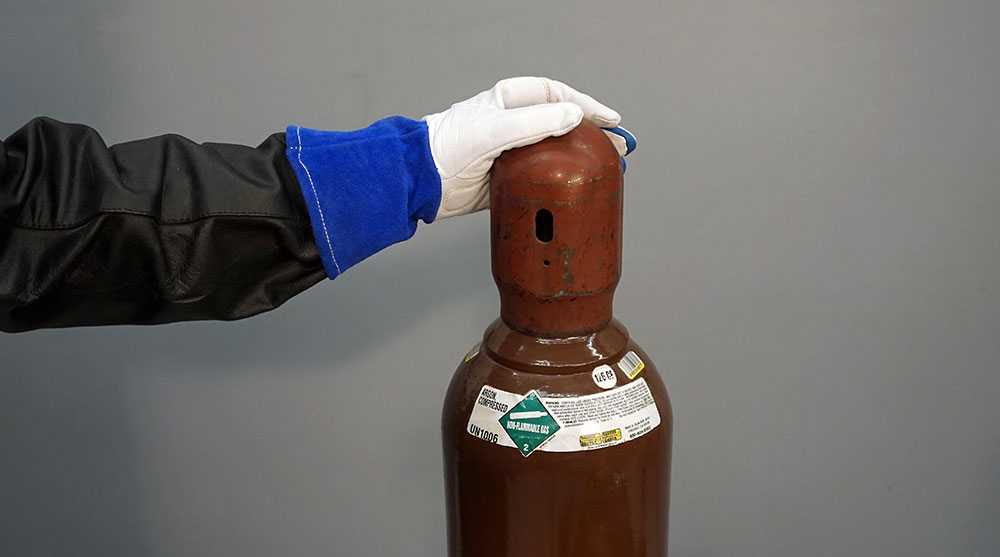
Having more control over each parameter of the welding process also makes it easier to get the dime-on-dime look that many builders prize. It can also help with getting sufficient penetration in challenging situations, and to tailor the welding arc to make it ideal for any weld joint configuration and for a broad range of material thicknesses.
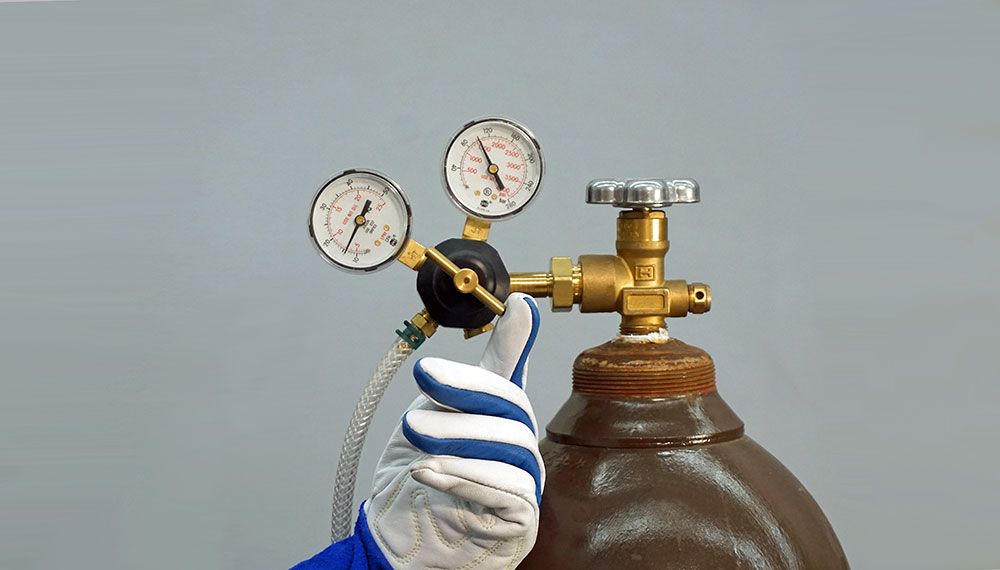
Inert Gas
One key difference between MIG and TIG is how the filler wire is added to the weld. With MIG welding, the wire feeds automatically whenever the trigger on the gun is pulled, and if shielding gas is used the gas flow is started and stopped with the trigger, too. With TIG welding, the torch has a non-consumable tungsten electrode that the arc emanates from. The arc is normally started and terminated with a foot or hand control, which also starts and stops the flow of the shielding gas. Many machines allow you to set both pre and post flow of the gas, which helps prevent the electrode and base metal from oxidizing.
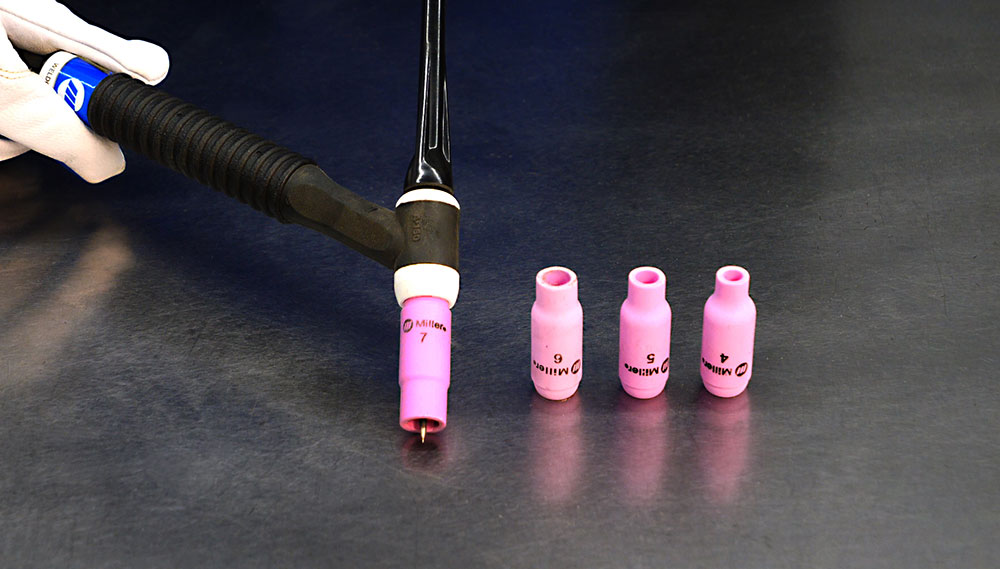
TIG welding is always shielded with an inert gas (usually argon), and if filler rod is used, it is added by hand. Feeding the right amount of filler rod, at just the right time, into just the right place, is a skill that takes time to master, and this is one of many factors that makes TIG welding more challenging to become proficient with.
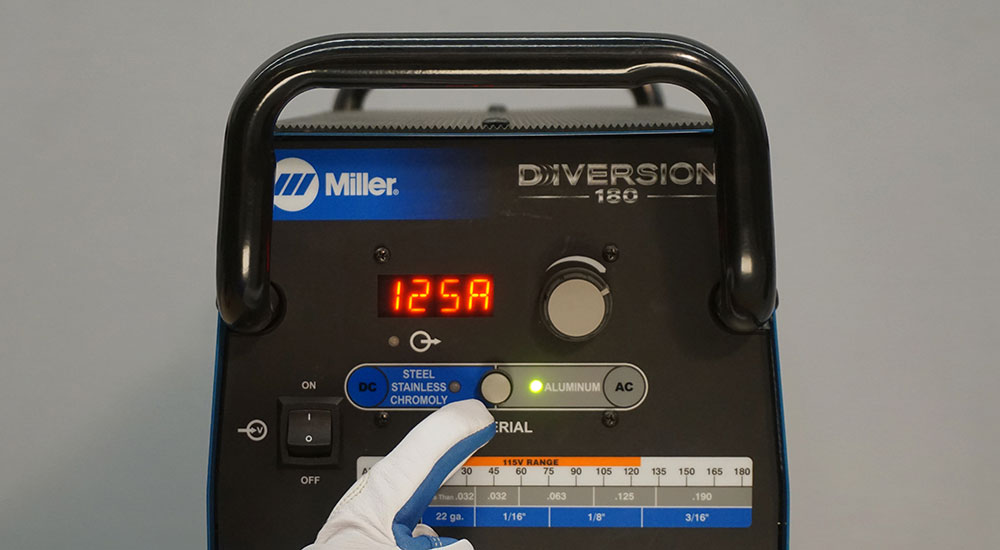
Amperage Control
TIG welding machines have a control for amperage, which is essentially the amount of heat that goes into the workpiece. On the most basic, entry-level welding machines the amperage is controlled solely by a dial on the face panel, but I strongly recommend stepping up to a machine that has a foot (or hand) control, allowing you to use any portion of the maximum value set on the face panel. There are many reasons why you may want to change the heat “on the fly.” Often you will need a large amount of heat to establish a weld puddle when the metal starts at room temperature, and once you have welded an inch or so you will notice that the base metal is building up heat, so less heat from the torch is needed to keep the puddle the ideal size. As you reach the end of a weld seam the heat at the weld tends to build up more rapidly, and you may need to decrease the heat even further. This is easy with a foot or hand control, but you run the risk of making welds that start too cold and end too hot if your machine doesn’t have this capability.
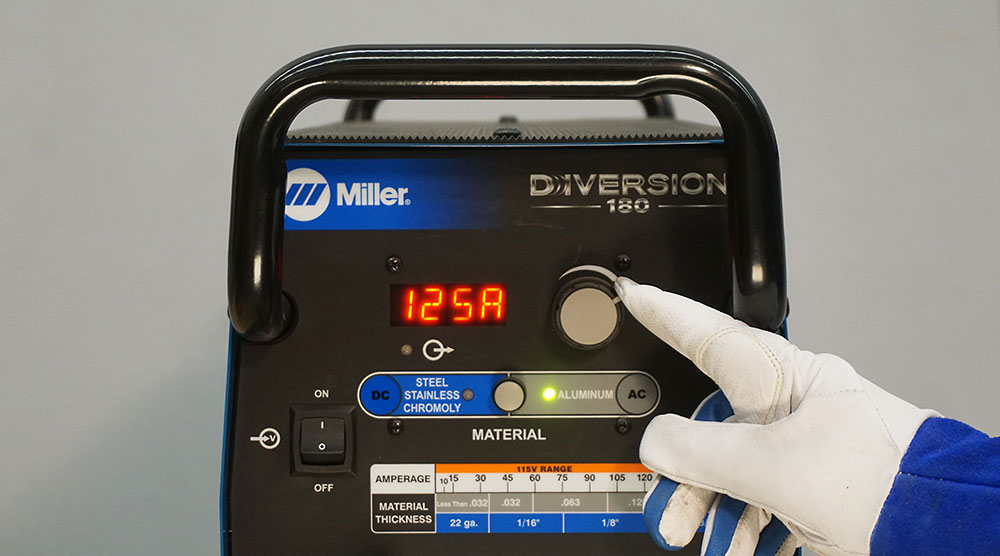
Welding Arc Differences and Filler Rod
One of the things people really appreciate about TIG welding is the smoothness and cleanliness of the welding arc. MIG welding always throws out a shower of sparks, but TIG welding only sparks on rare occasions—usually when there is some impurity in the weld zone. The other side of this is that TIG welding requires that the base metal and the filler rod be squeaky-clean, while MIG welding can tolerate a certain amount of surface contamination.
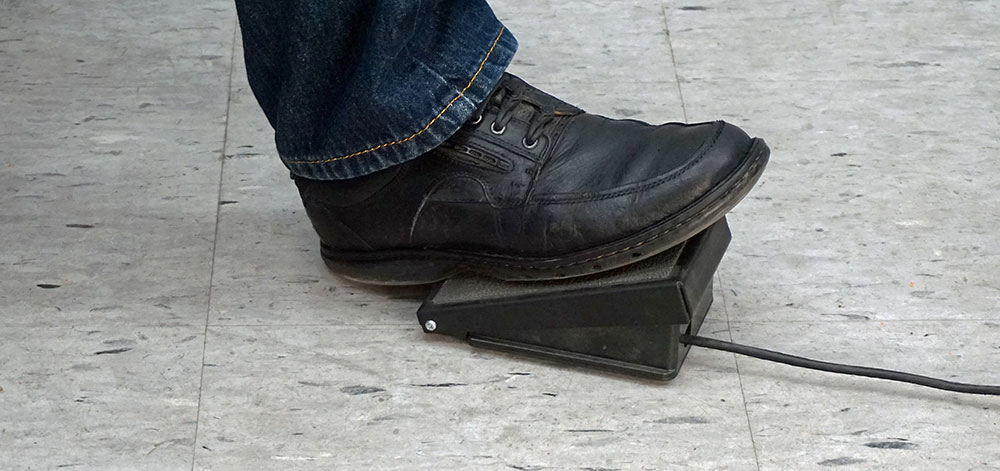
Read More: The Metalwork Behind The GNRS 2022 Al Slonaker Award Winning Highboy Coupe
The More Higher-end TIG machines give you advanced functions, like waveform controls and pulsing. These are beyond the scope of this introductory article, and most car builders don’t really require them, but they do make certain challenging welding situations easier to manage—like welding extremely thin or delicate materials, for example. MR
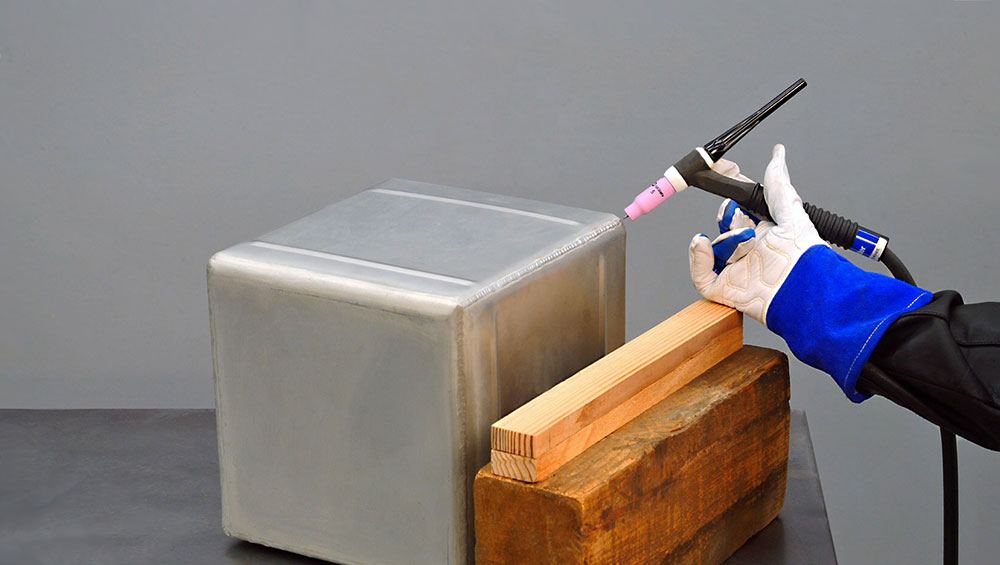
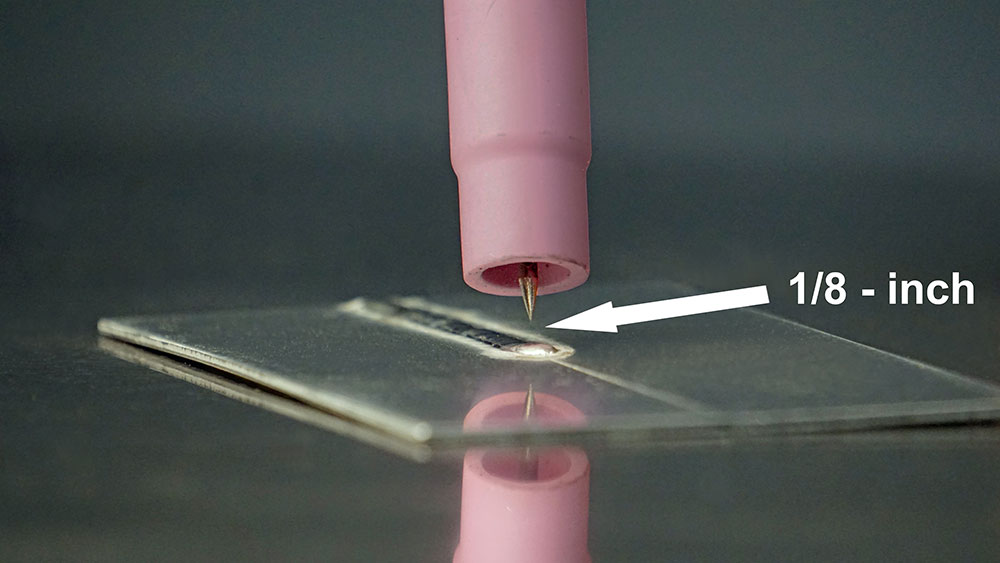
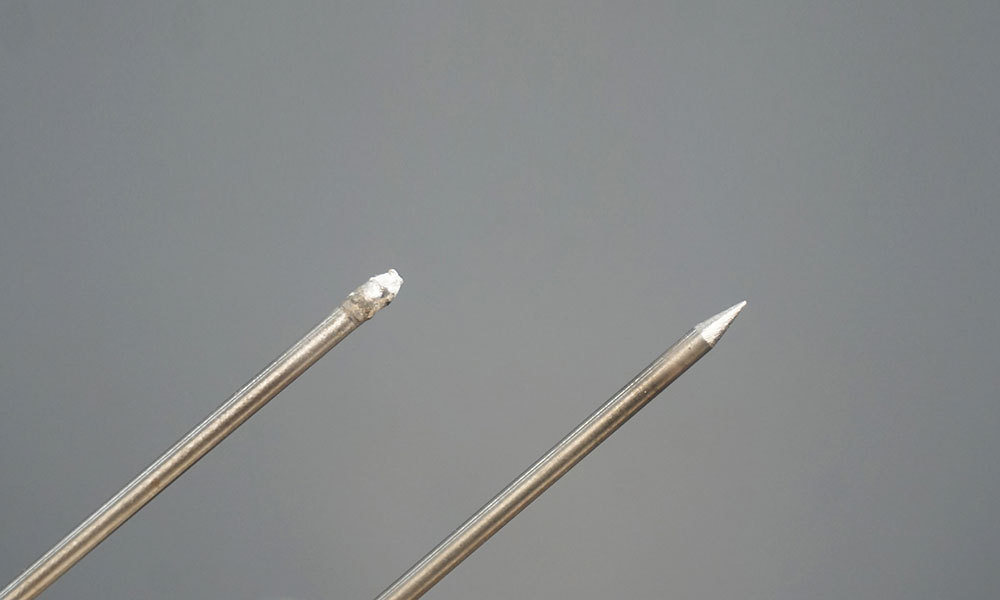
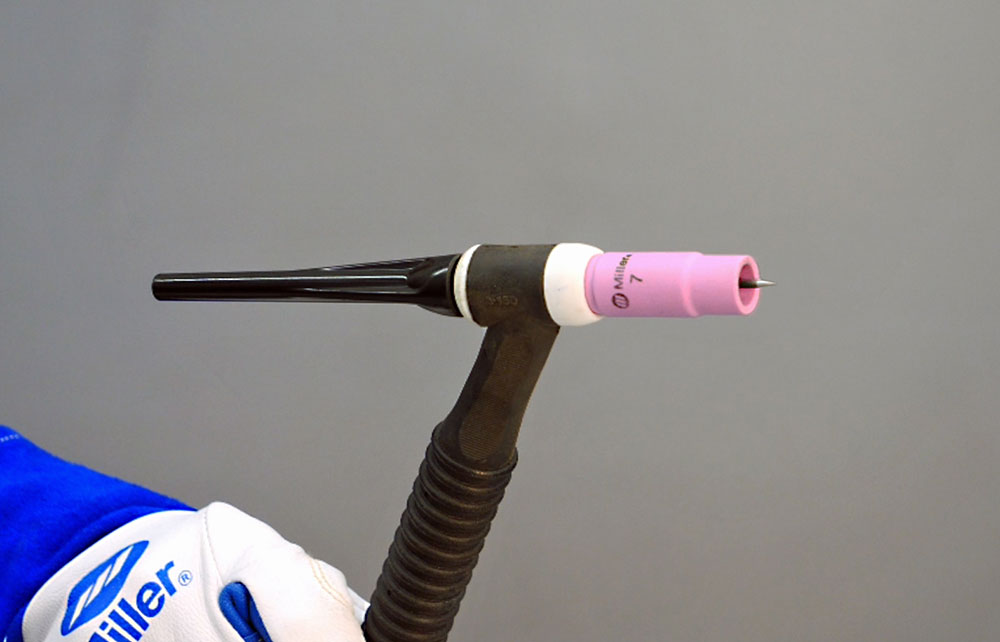
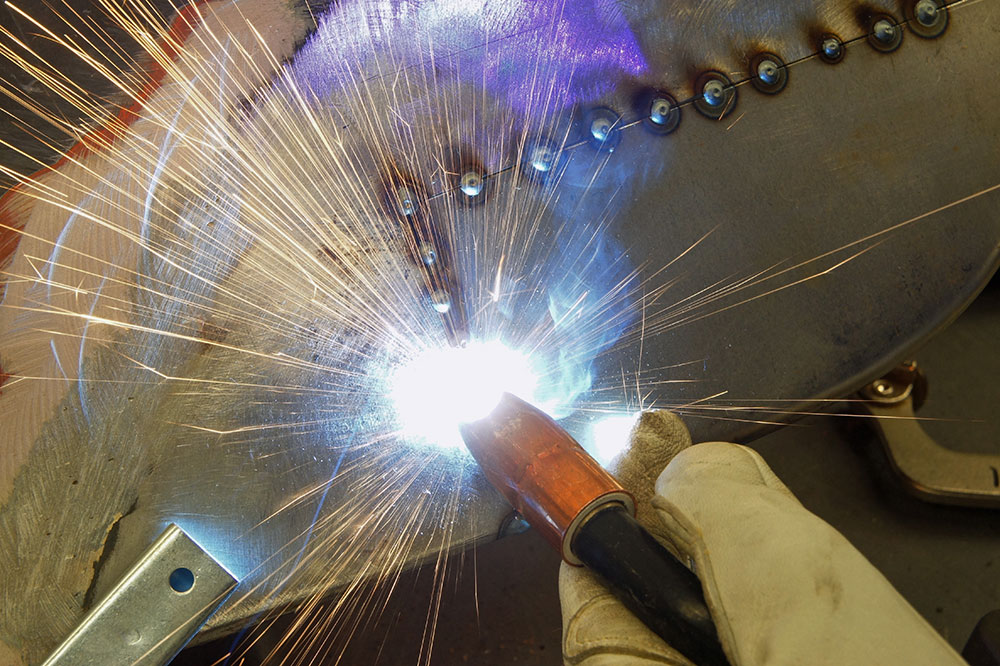
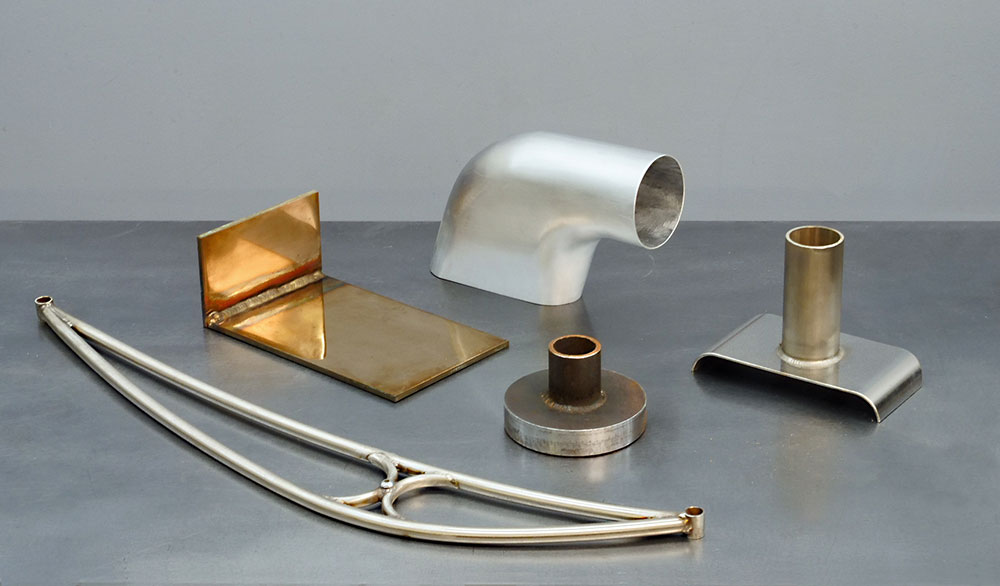
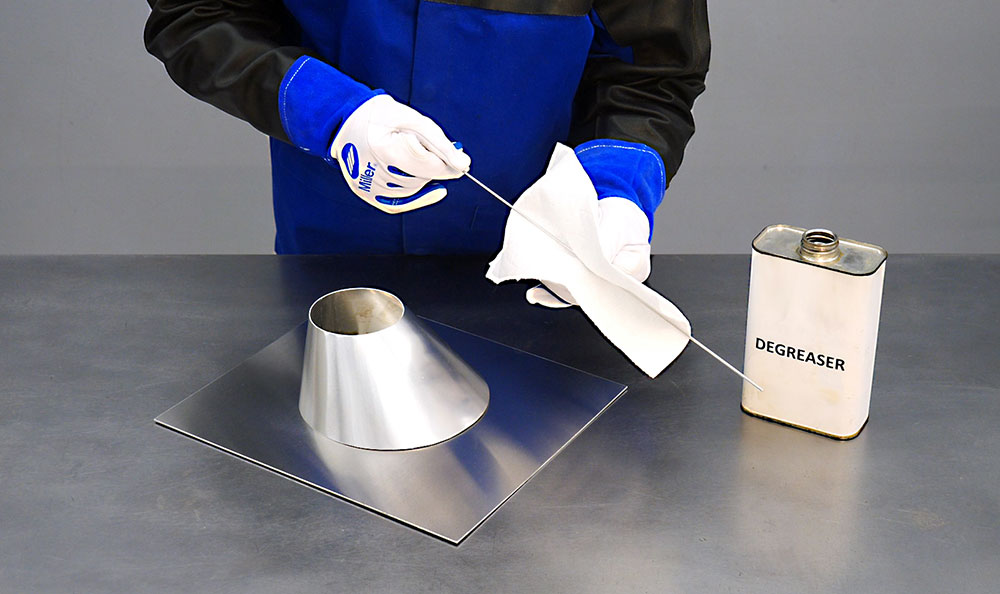
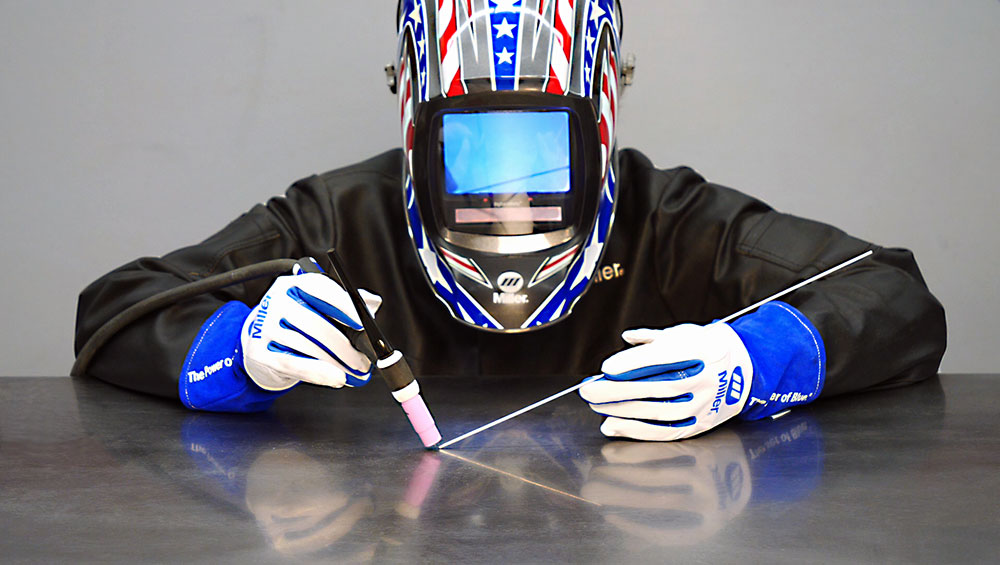
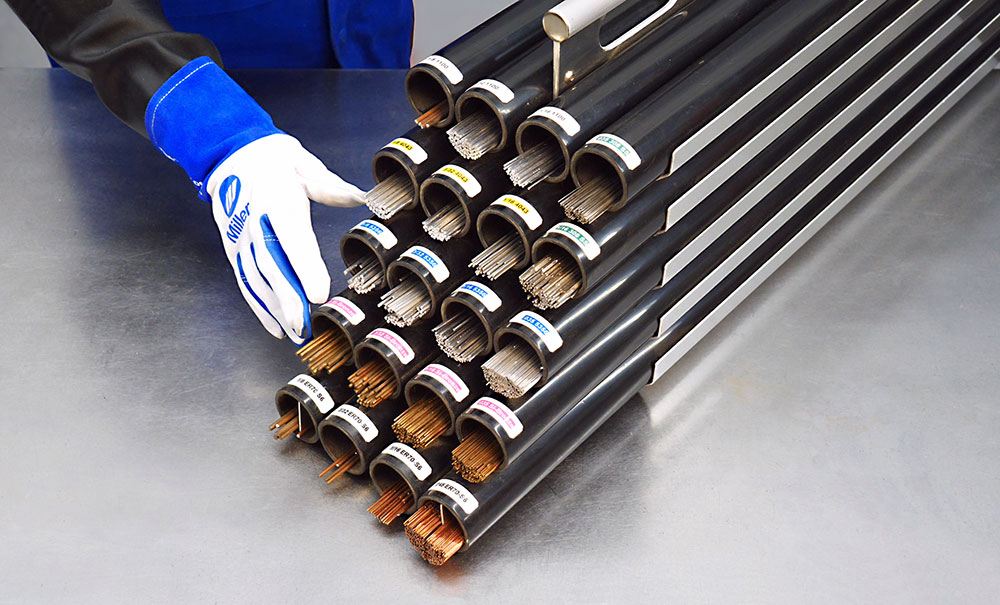
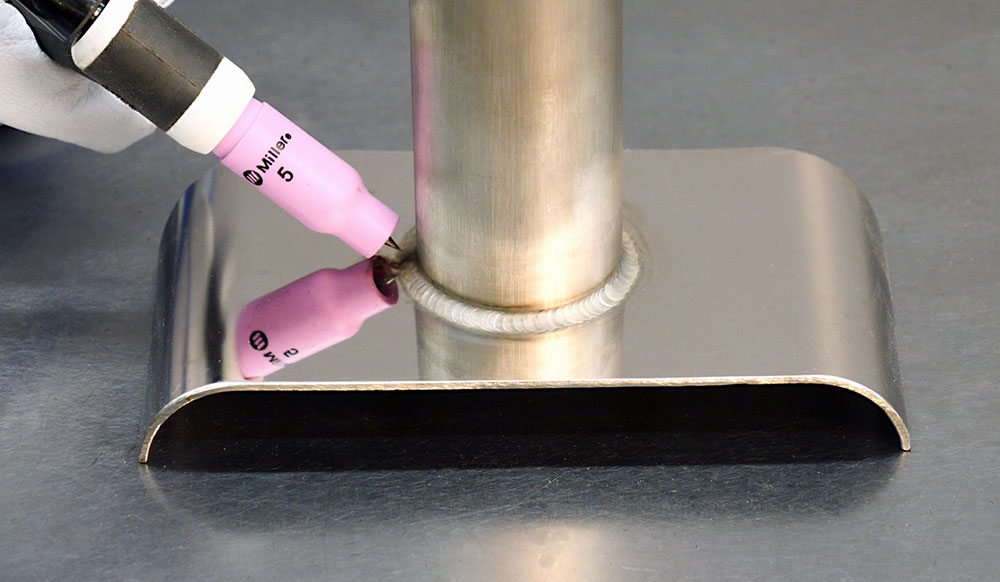
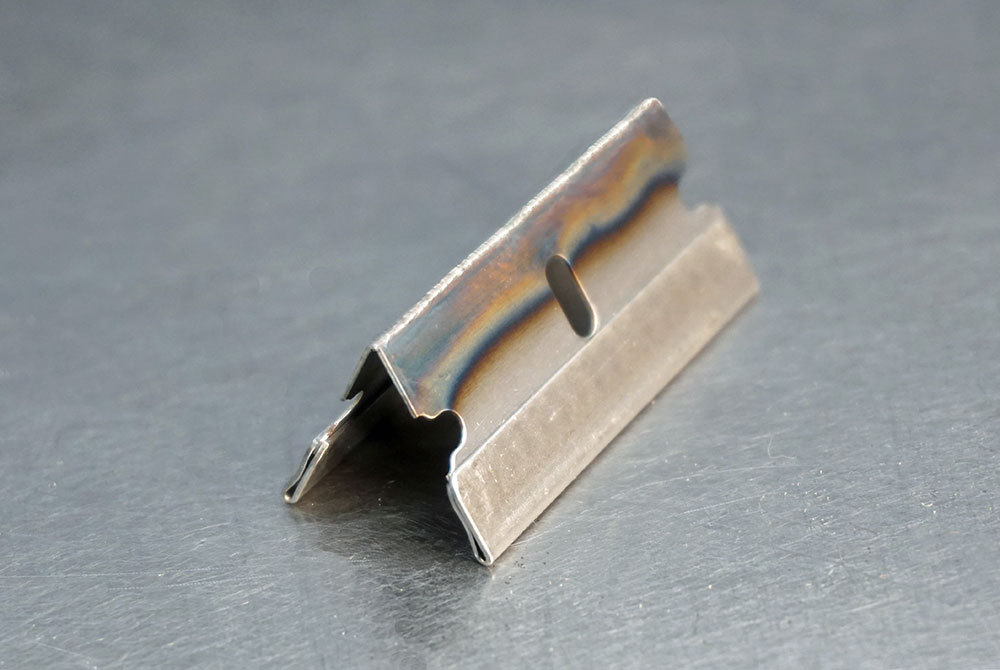
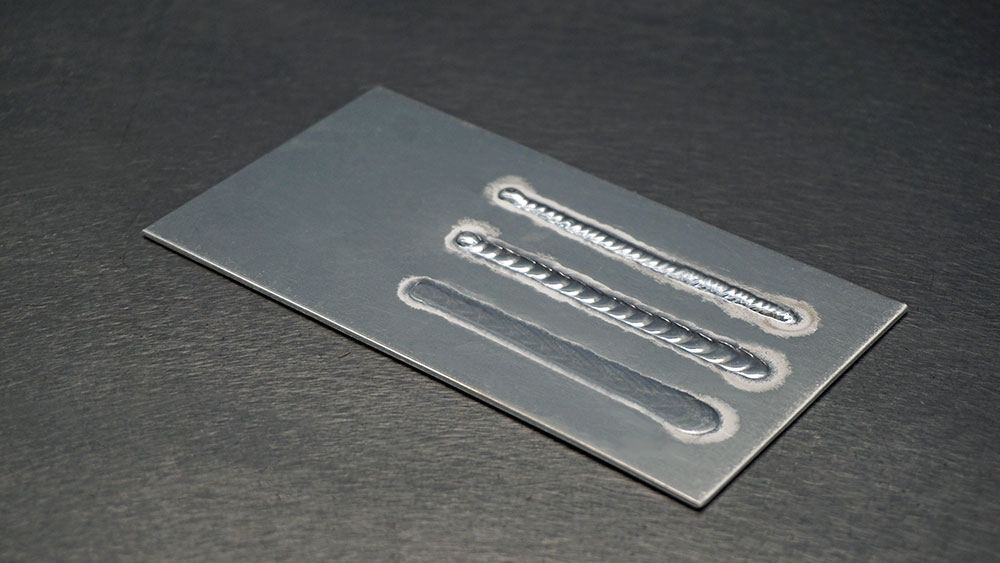
Source
Miller Electric Manufacturing Co.
(920) 734-9821
millerwelds.com