By Ron Covell – Images by Gary’s Rods & Restorations
Classic trucks were designed to be used and abused; some of the details of construction can be a bit crude. When it came to the running boards on the Souza F-100 project, a lot of work was required by the crew at Gary’s Rods & Restorations to make them fit the cab, bed, and fenders in a way that is smooth and refined.
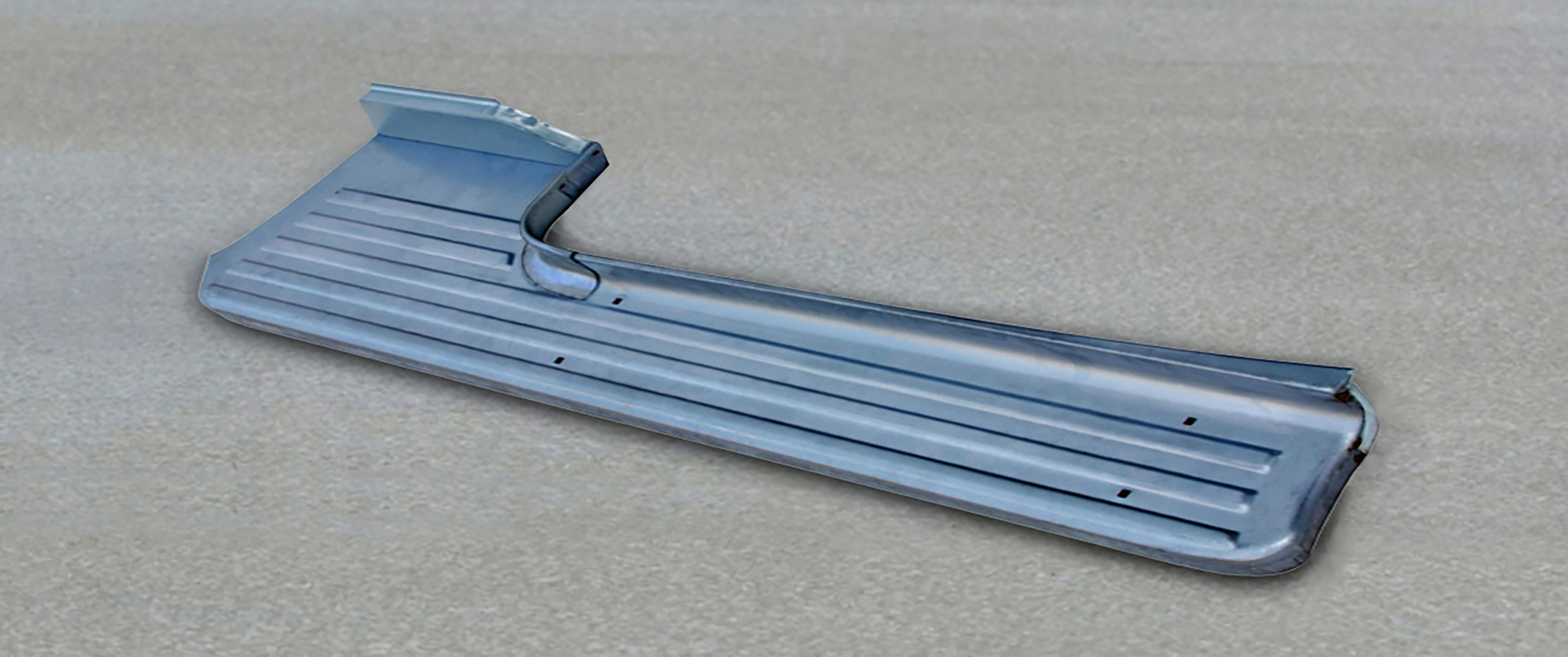
The original running boards jutted out from the fenders in an odd way, so the first step to enhance them was to remove some excess width. The boards were made with three full-length ribs plus two shorter ones placed behind the cab. One long rib was removed from the outer edge, which narrowed the running board about 2 inches.
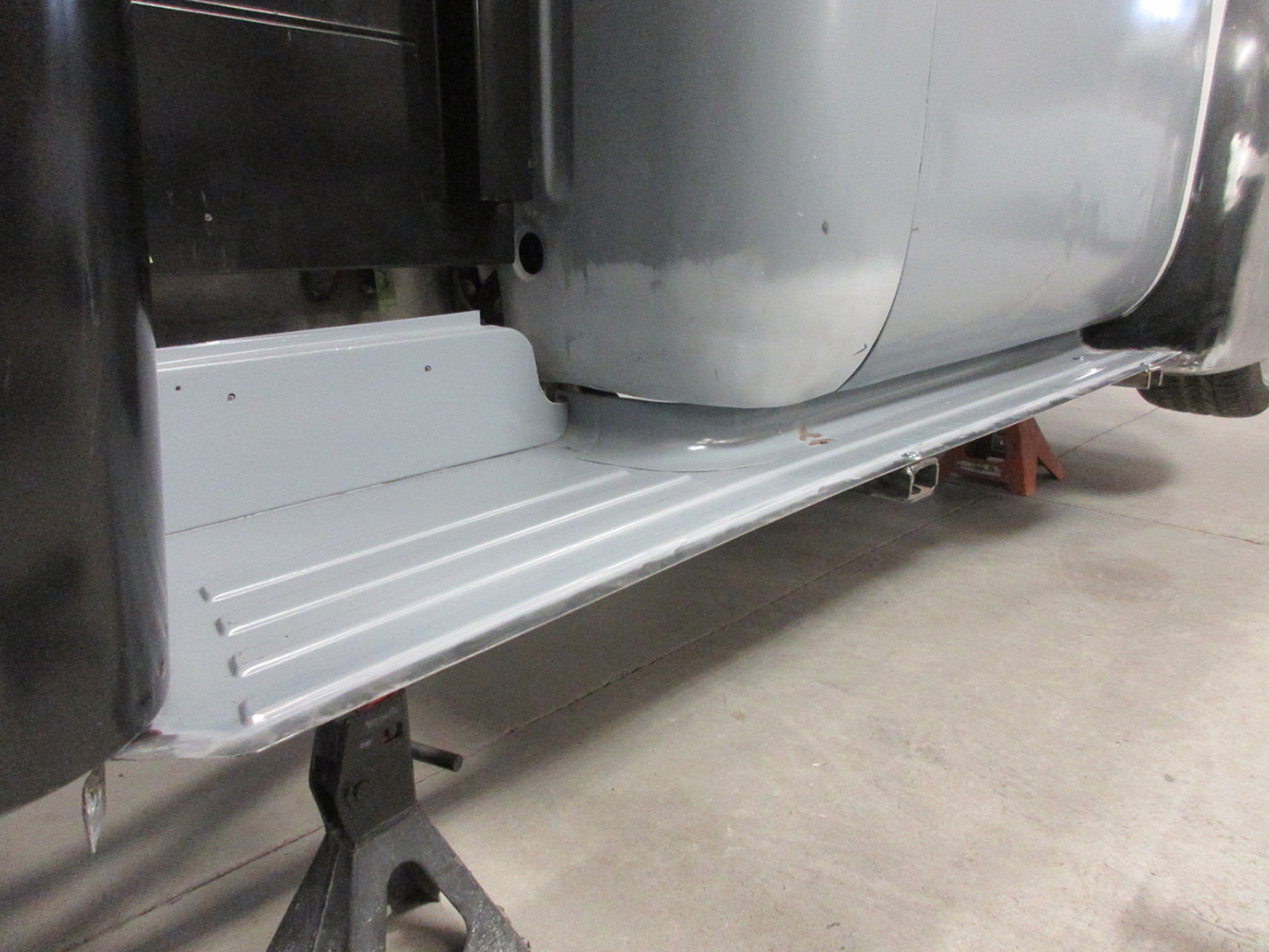
There is a vertical flange on the running board that follows the perimeter of the cab, and to ease the manufacturing of this challenging detail, a C-shaped stamping was spot welded to the original boards. This was OK for a work truck, but it wasn’t in keeping for this project. The spot welds were drilled out to remove the flange, and the parts were reshaped so they could be butt-welded together. The photos show what a huge difference this seemingly small detail makes. In one more step of refinement, a wedge of metal was removed from the front of the running board, allowing the edge to be pulled in about ½ inch to better follow the shape of the cab.
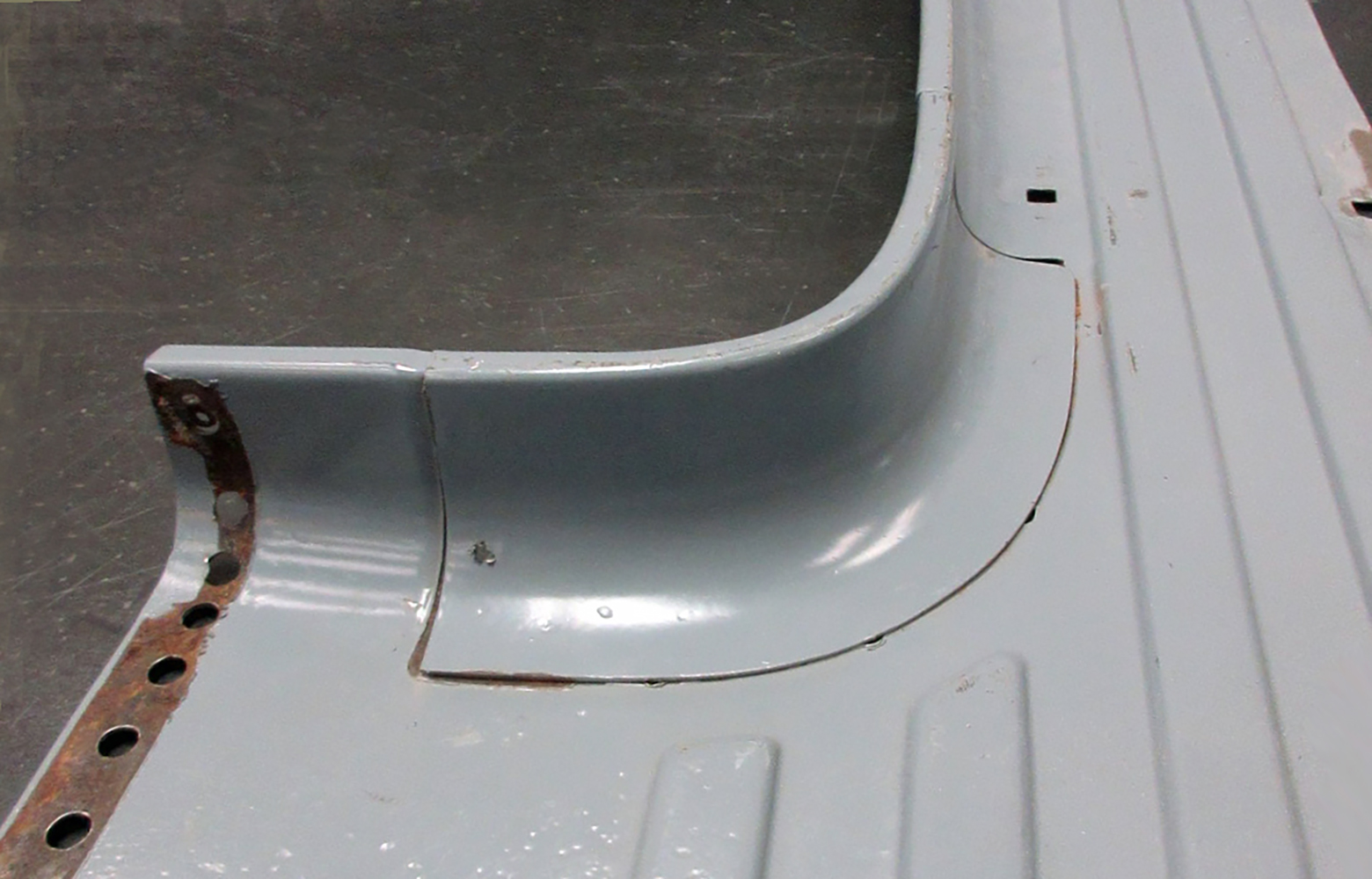
A new outer edge was made for the running boards from a strip of 16-gauge steel, bent into a U-shape. This channel was butt-welded onto the boards and metalfinished. The tips of this channel were flared out slightly to meet the fenders in a more pleasing manner.
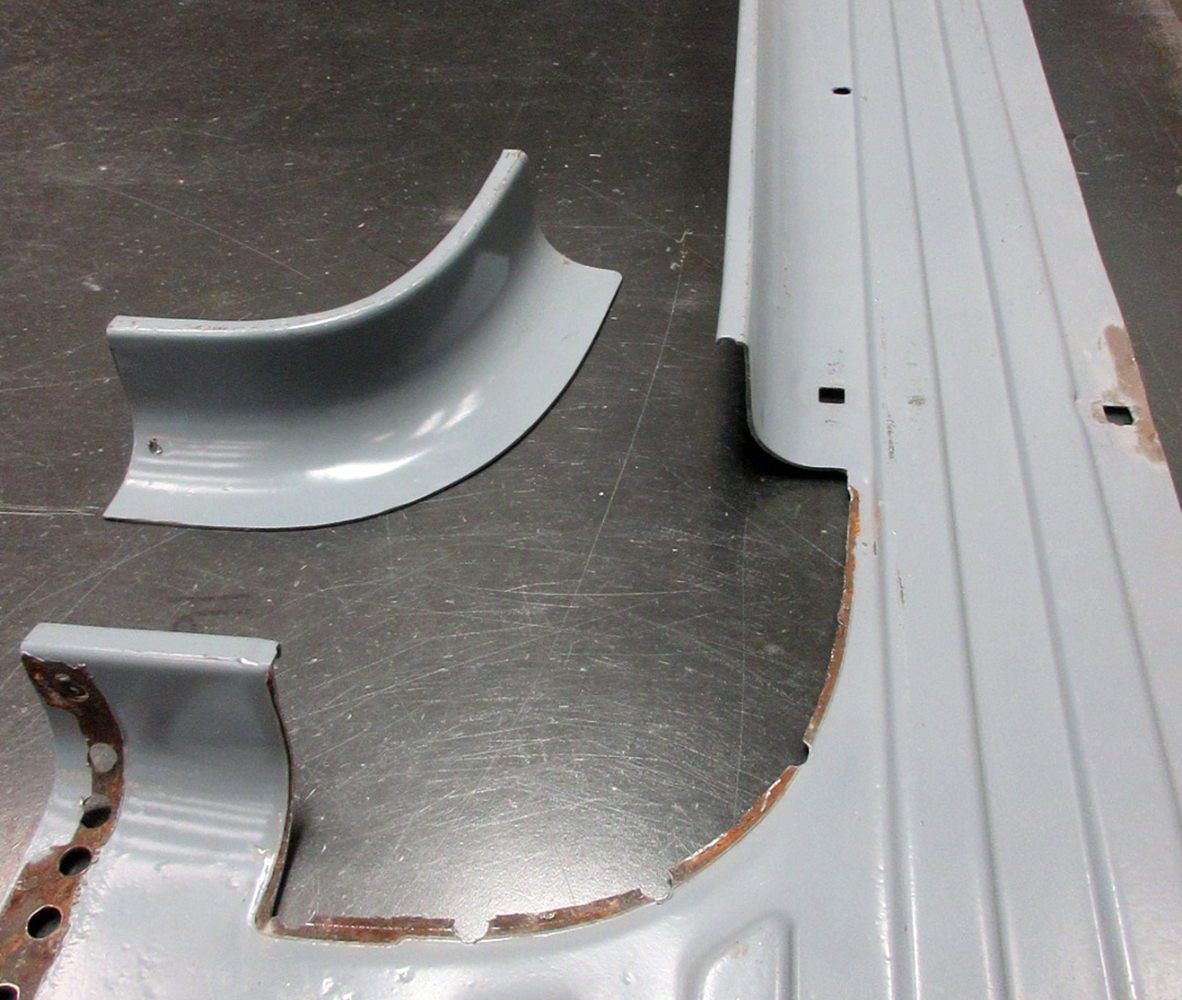
The original running boards were bolted to the truck chassis with carriage-head bolts, which were visible of the top surface. New mounts were made and welded under the boards with studs that extend through the mounting brackets. This way, all the fasteners are hidden on the top side.
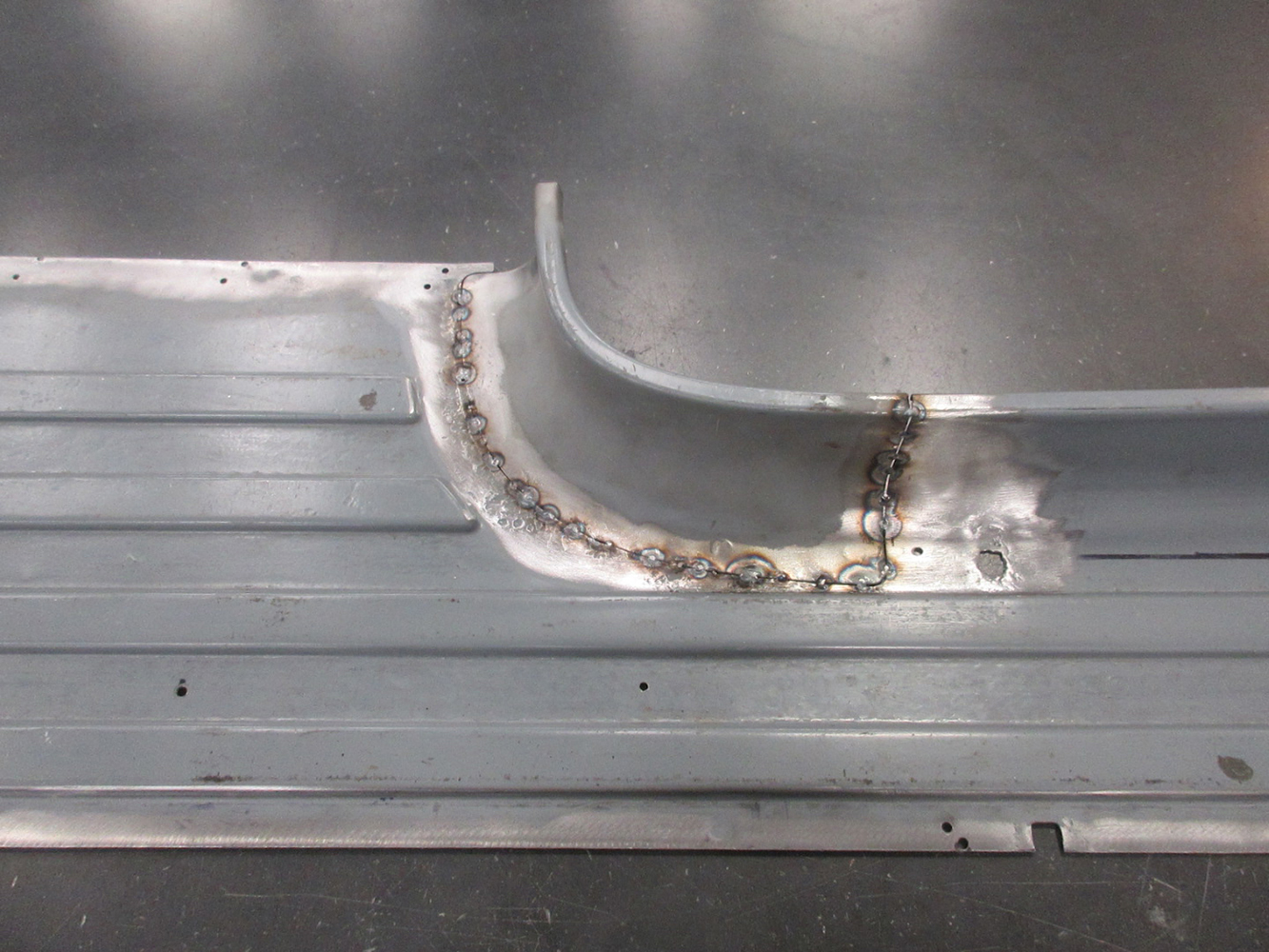
A new piece of metal was formed, positioned, and welded to the bottom of the front fender, to match the level of the running board. Once the bottom of the fender was at the right height, a flange was carefully fitted to the front of the running board, ensuring the junction was clean and tight.
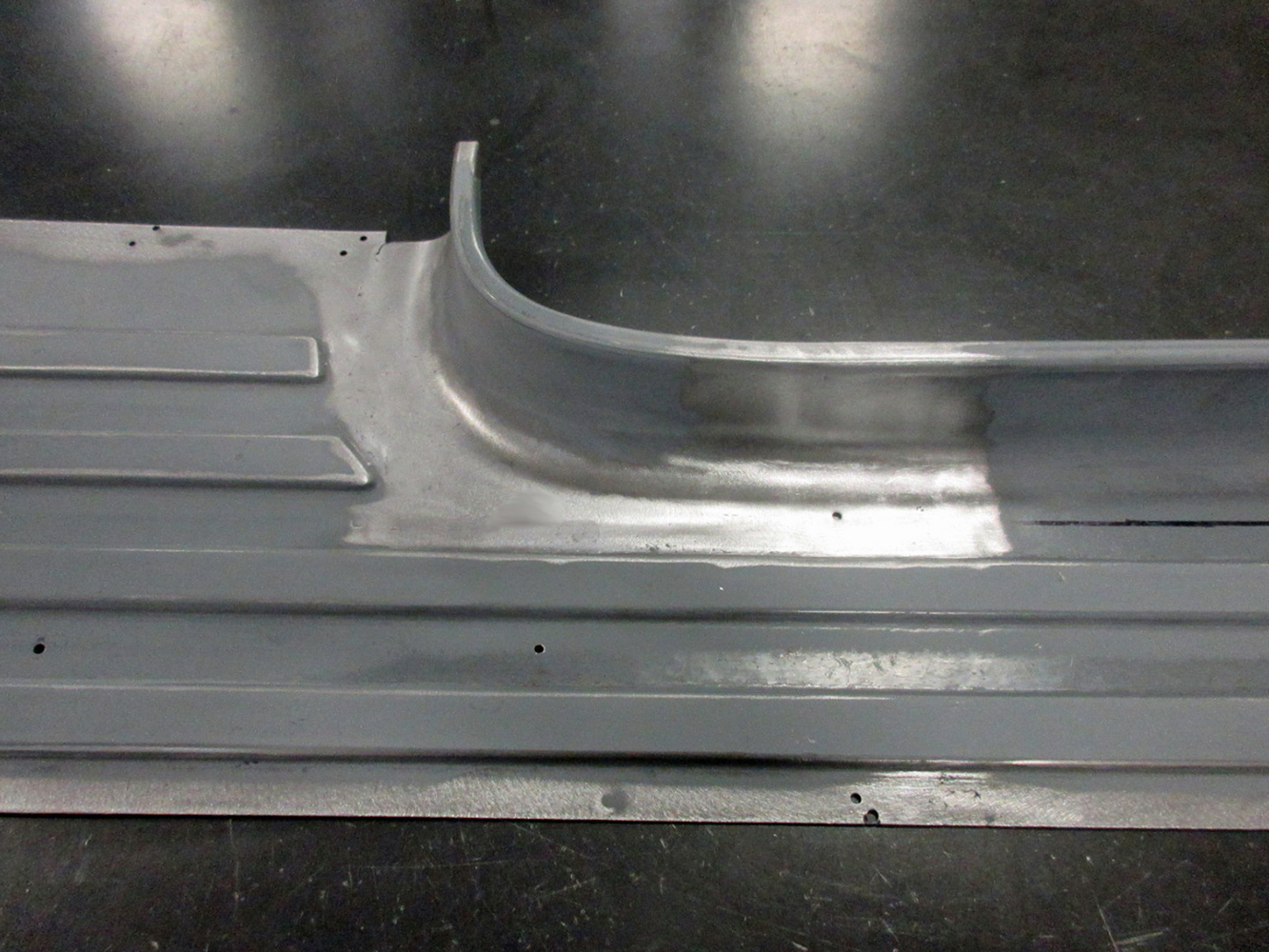
The rear fender needed similar modifications. An oversize piece of metal was grafted onto the front edge of the fender, then the running board was fitted into place and a flange was added to the running board to match the fender perfectly.
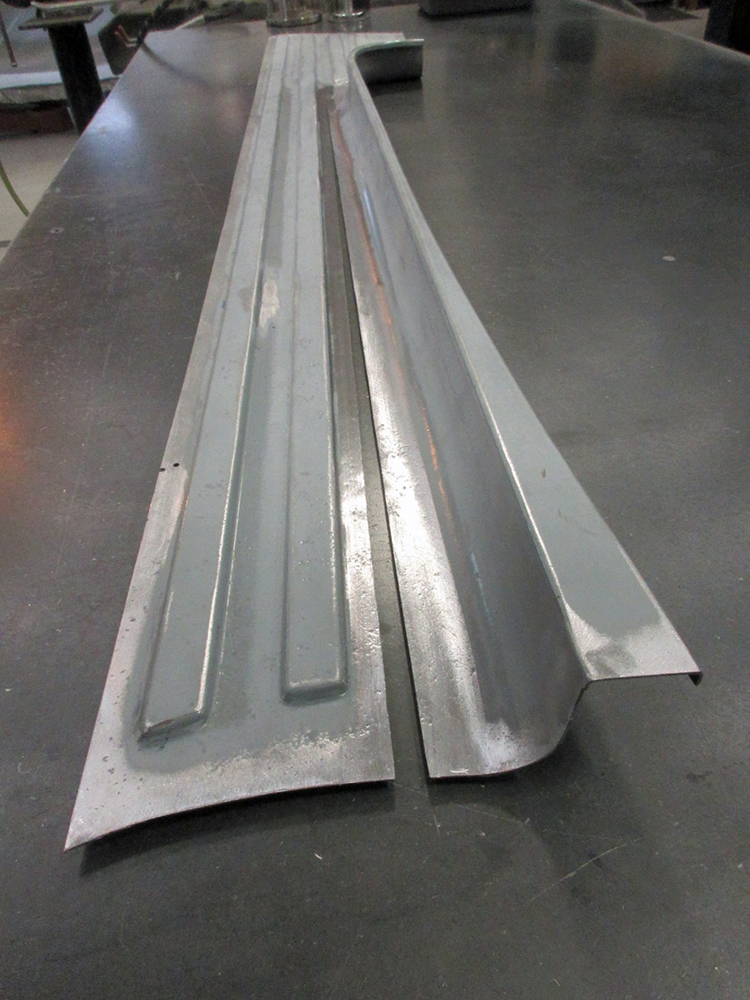
A flange was originally spot-welded to the top of the running board right under the bed and Gary’s crew wanted to clean up this area, too. A gracefully curved flange was fabricated from many pieces of steel, and it joins to a mating surface that was attached to the running board. This is some very complex metalworking indeed, and Gary credits his lead metalman, Emilio Belmonte, who pulled it off to perfection.
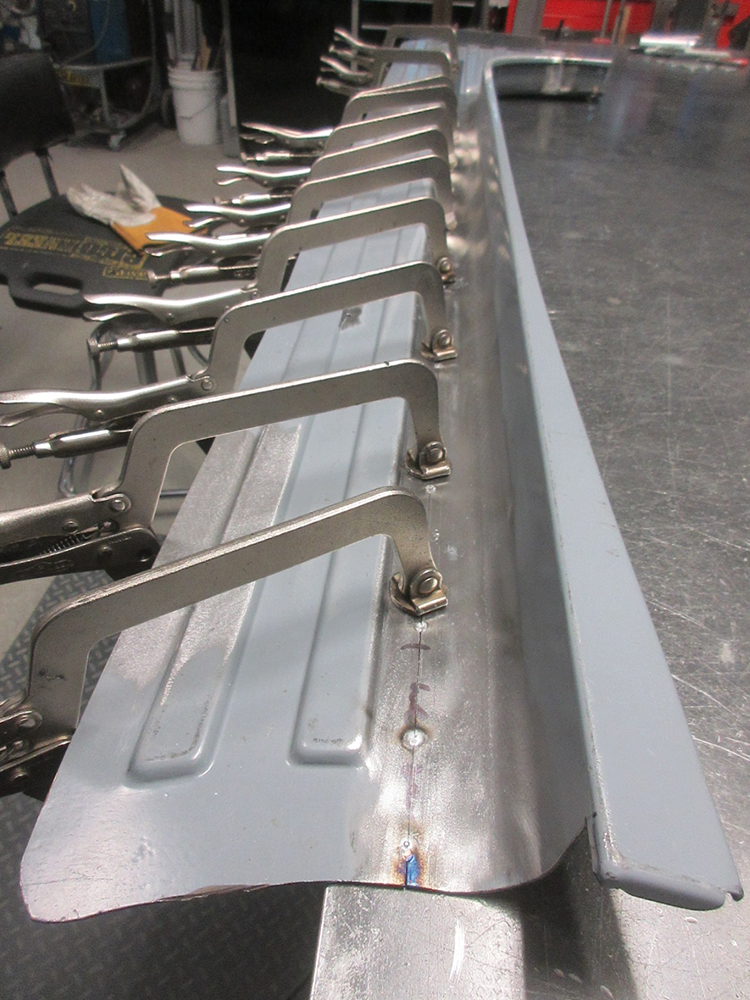
The final step was fitting a small piece of carefully formed metal to the rear fender, continuing the stepped edge around the wheelwell opening into the running board. This part required an intricate hammerform made from solid steel, which you’ll see in the photos.
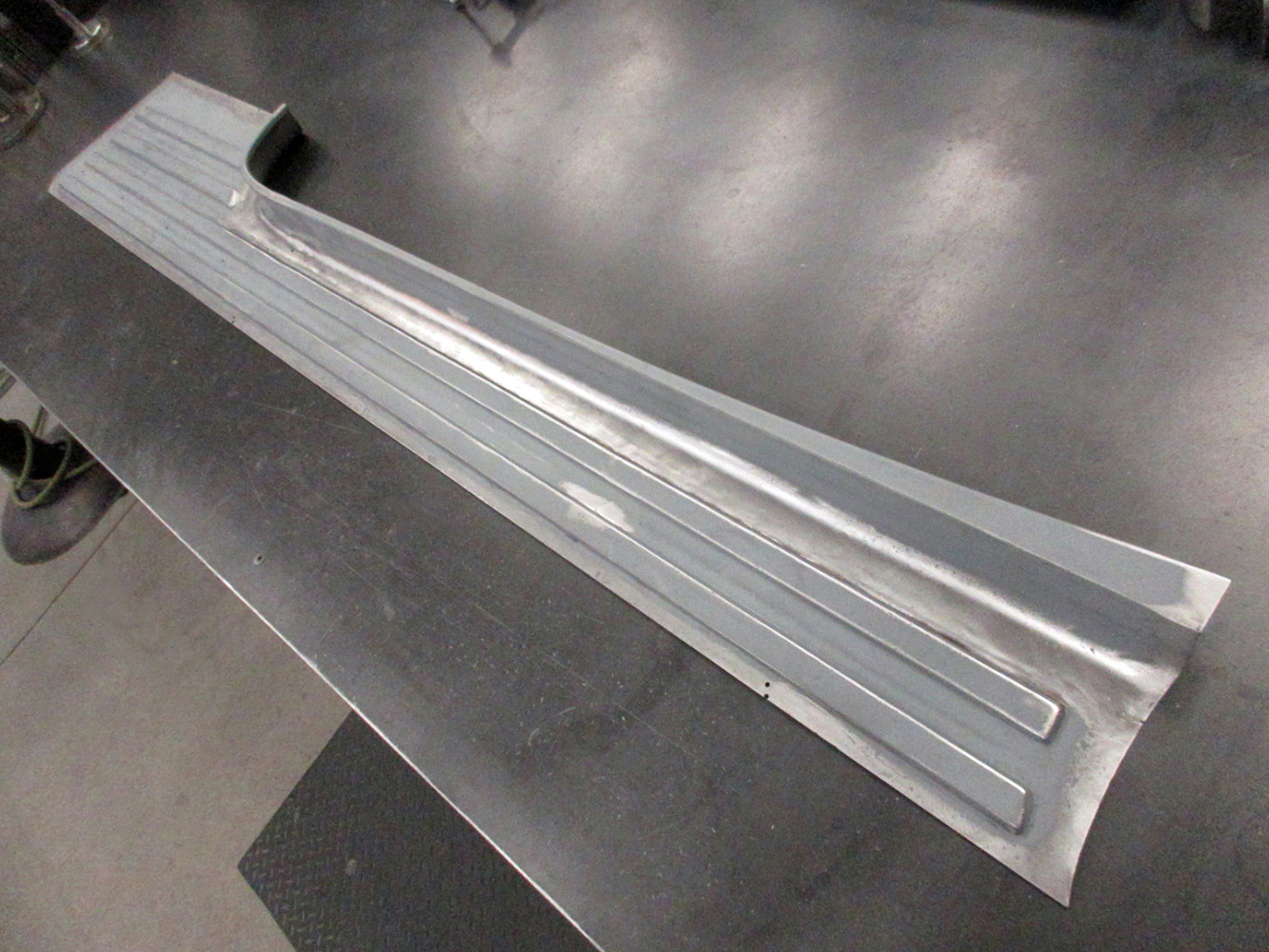
Stay tuned for the next episode of this ongoing series. We’re sure you’ll like what you see!
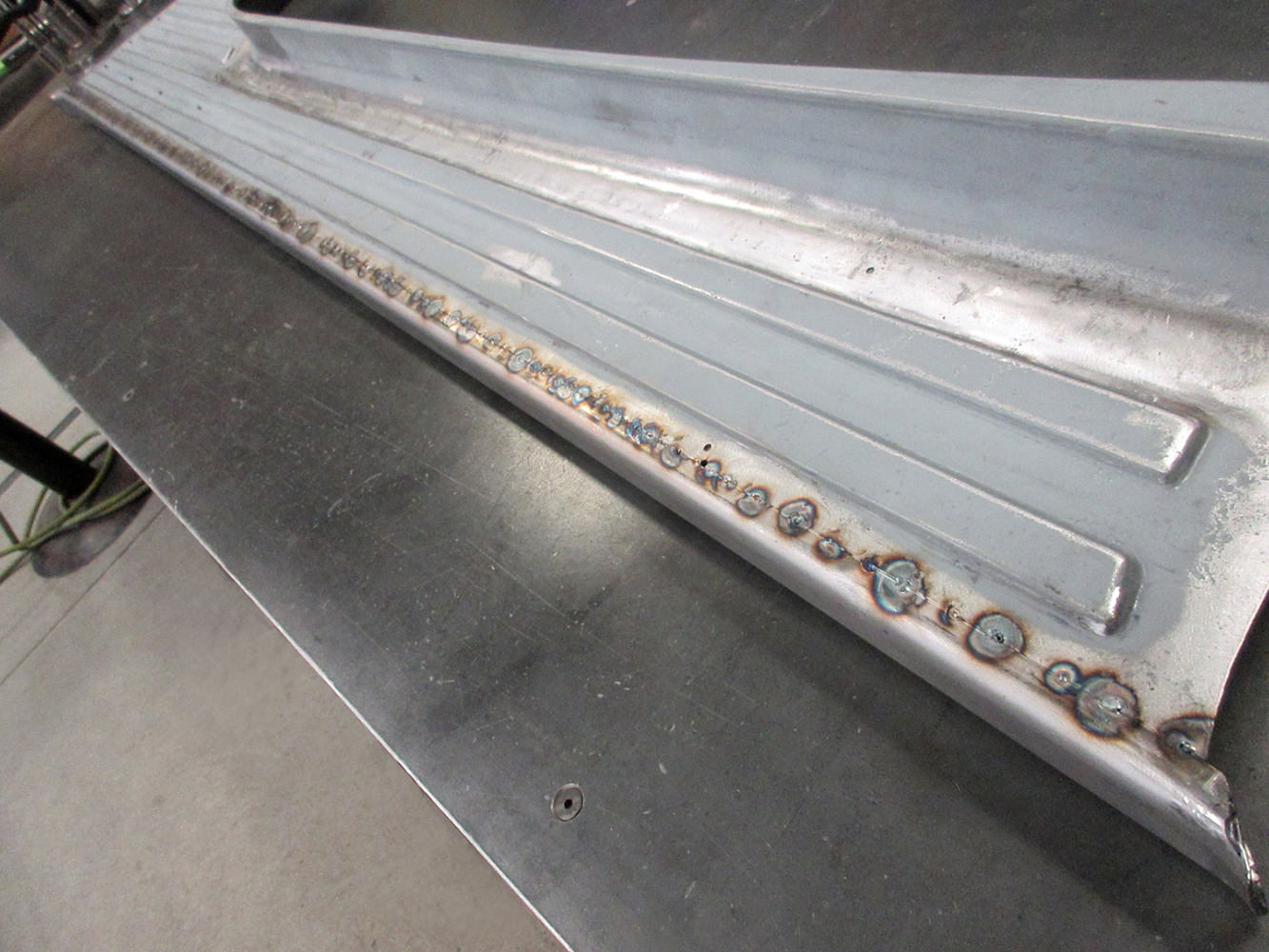
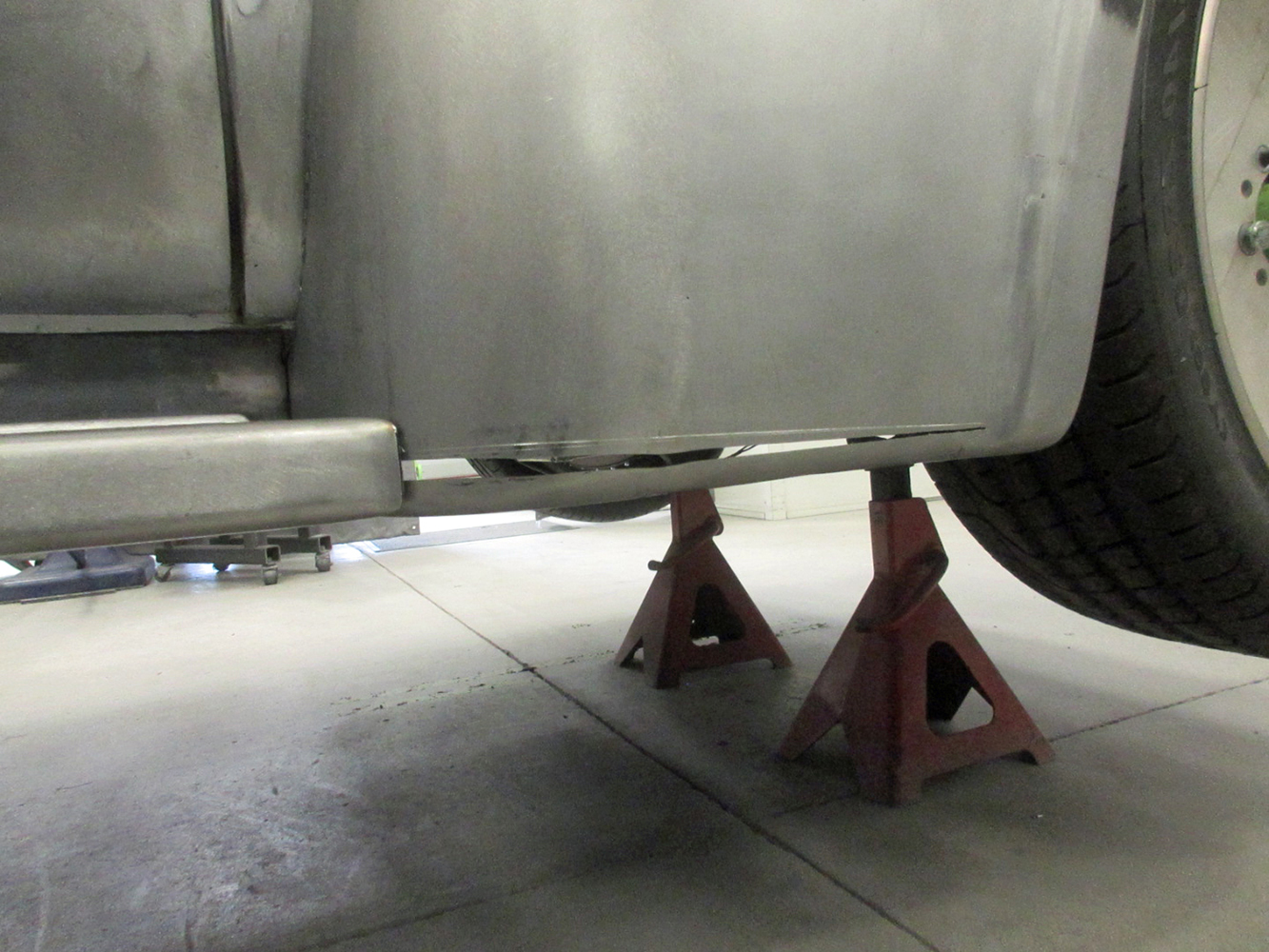
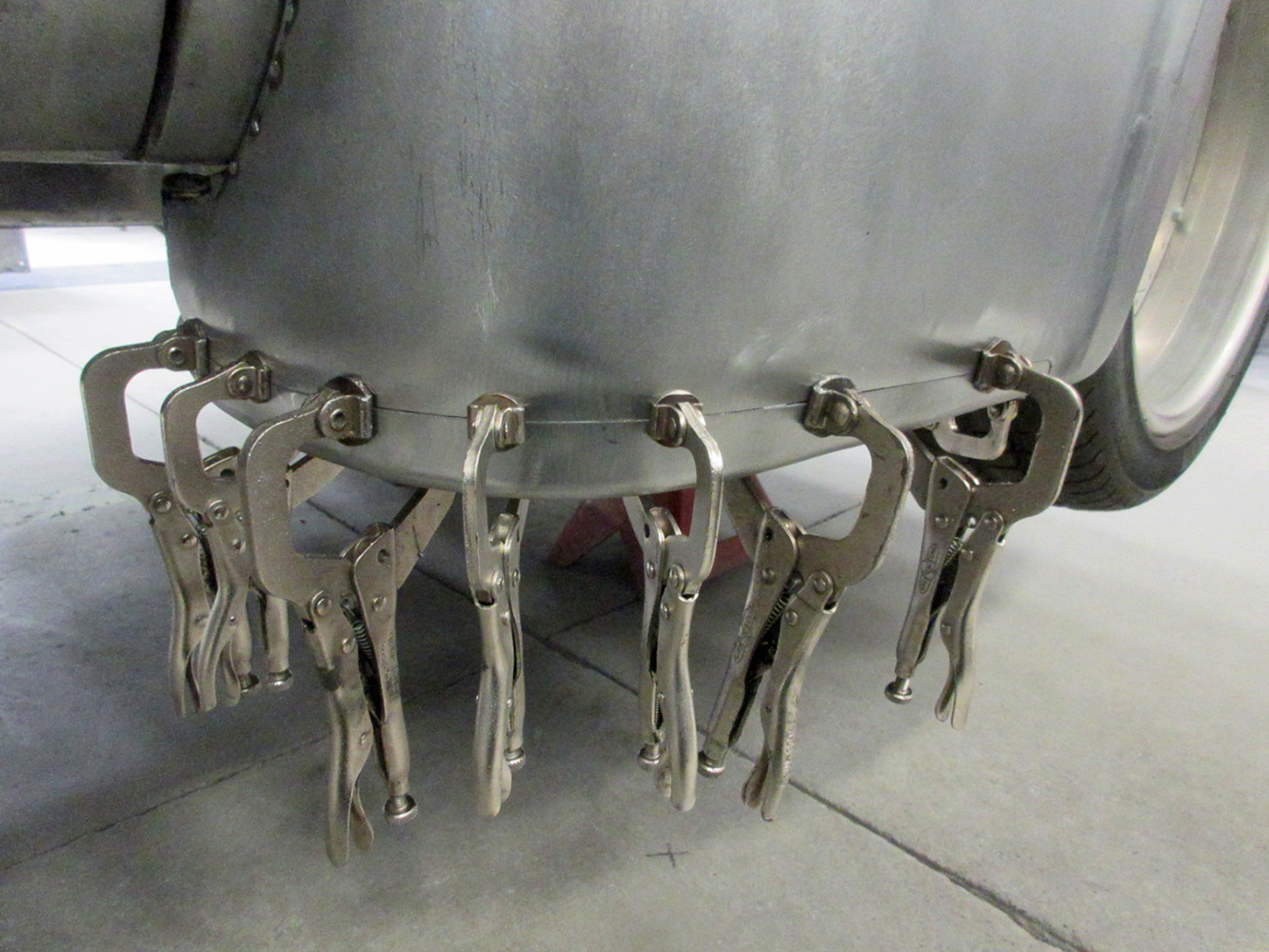
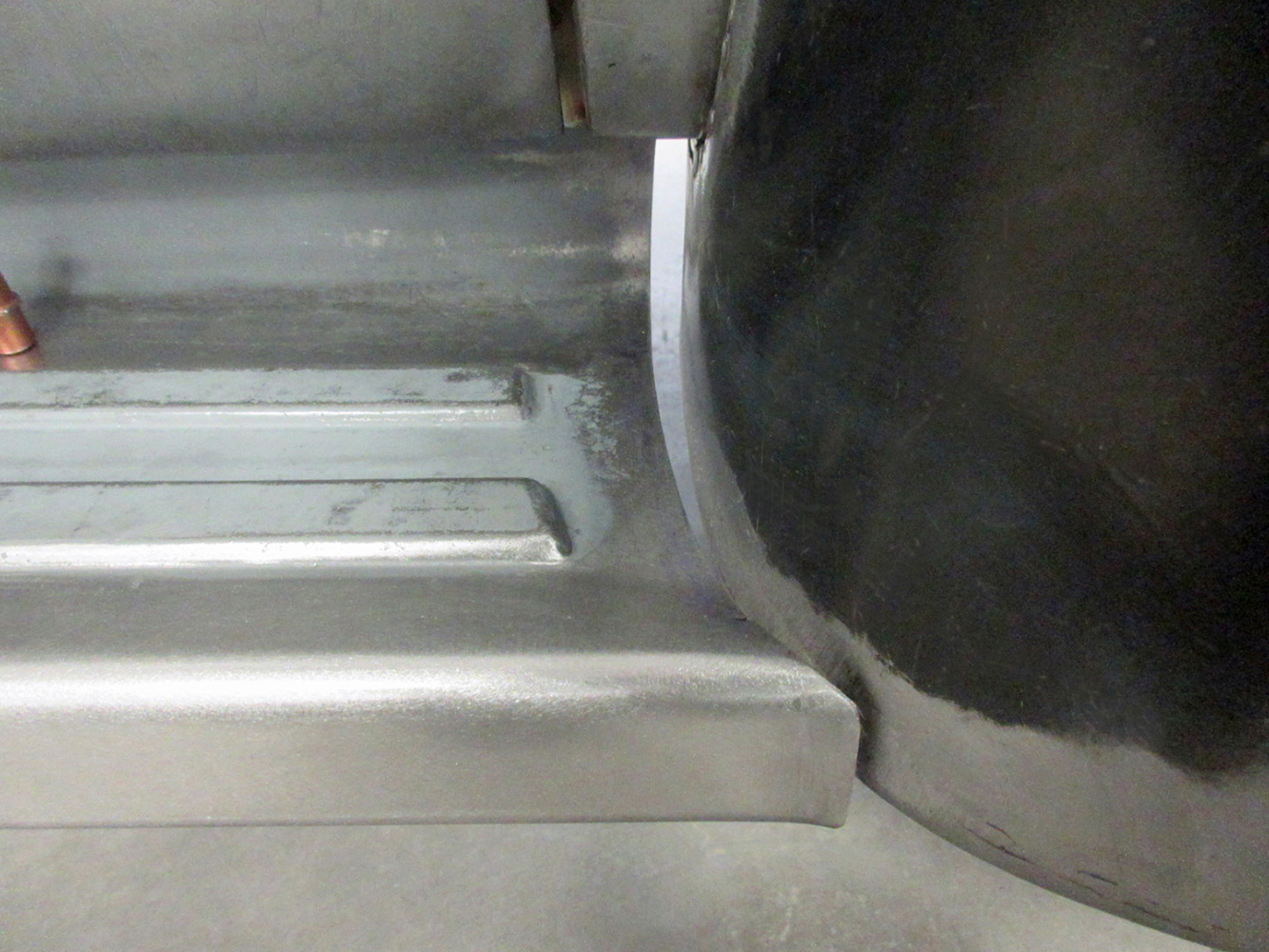
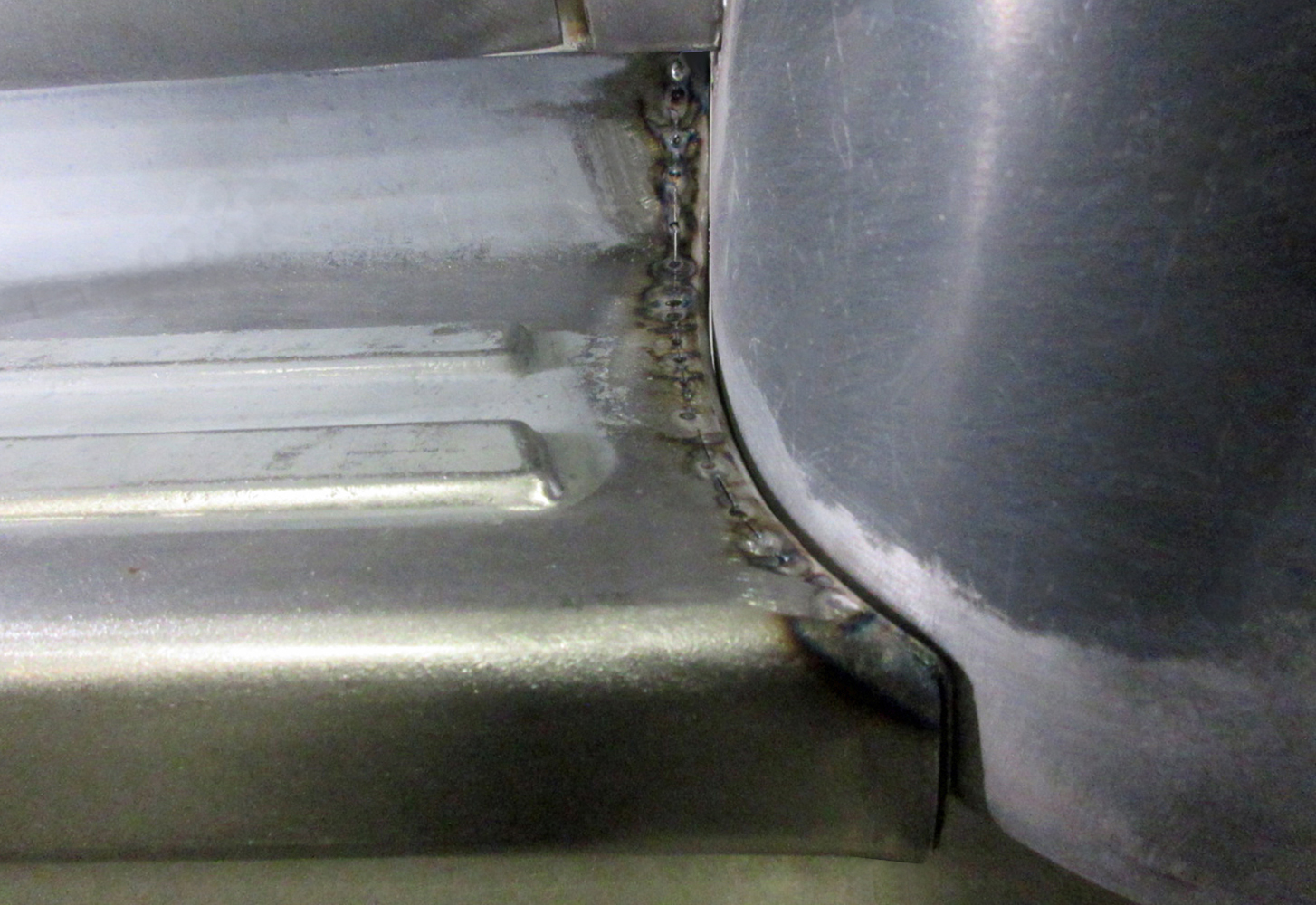
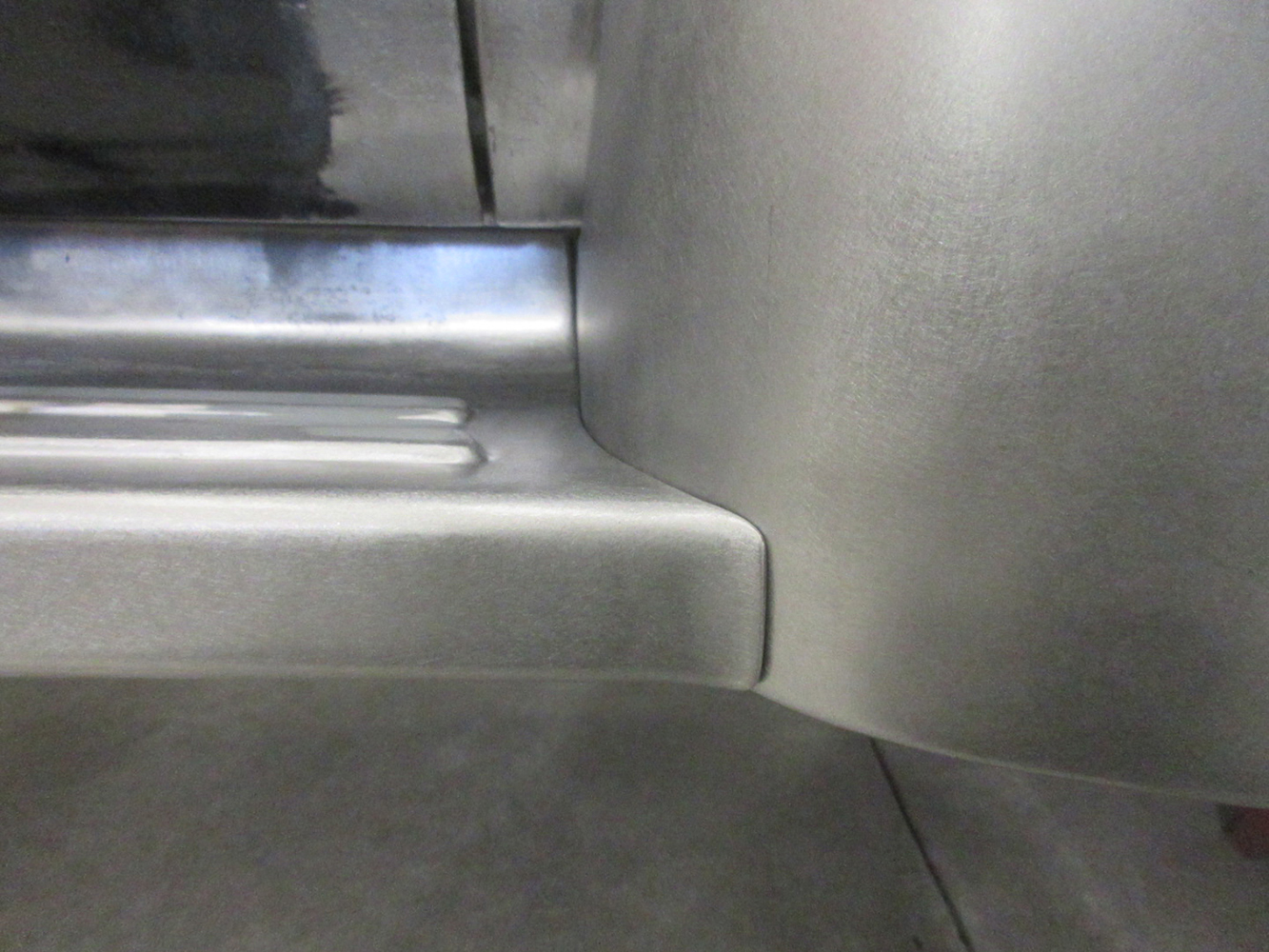
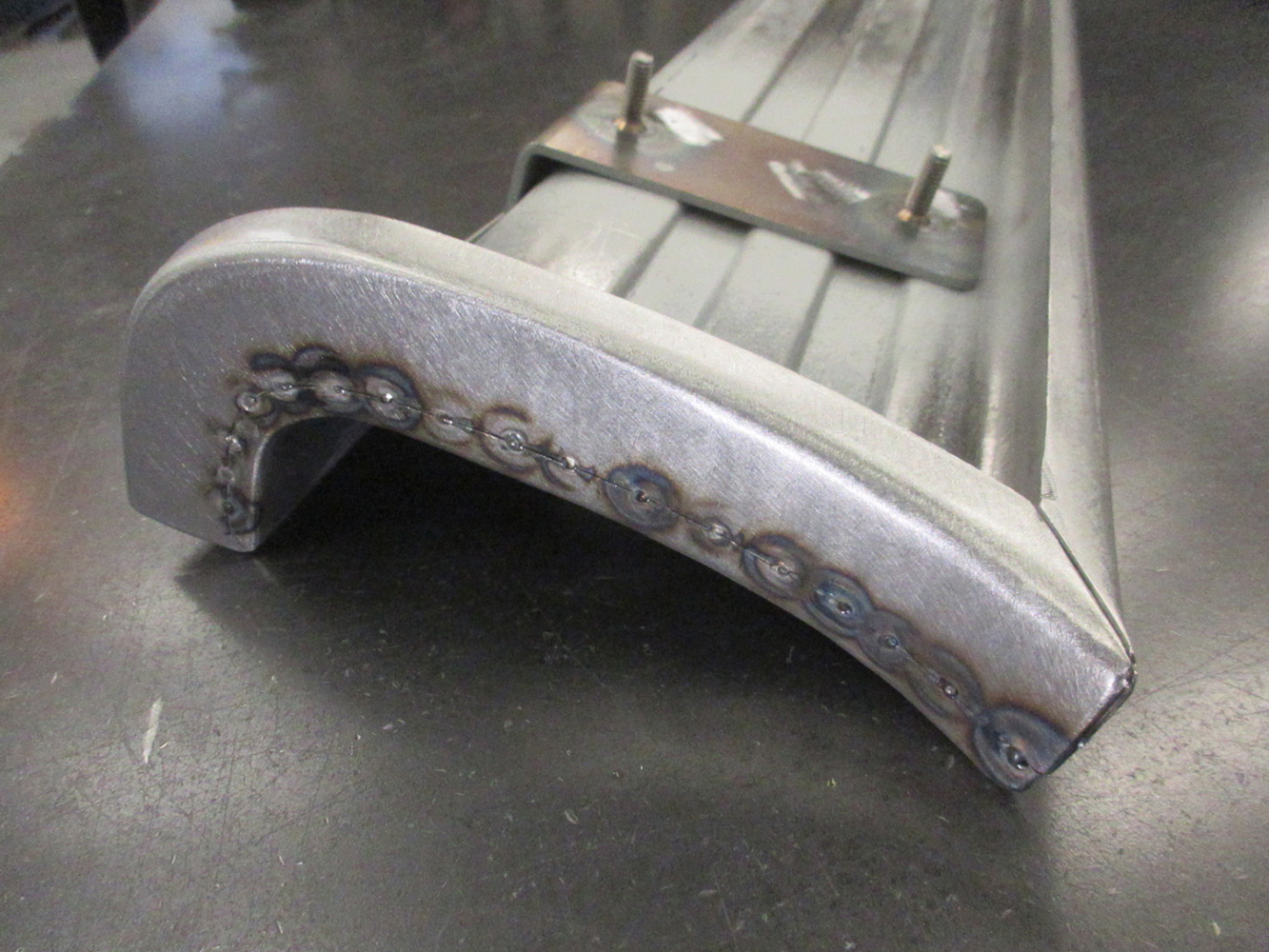
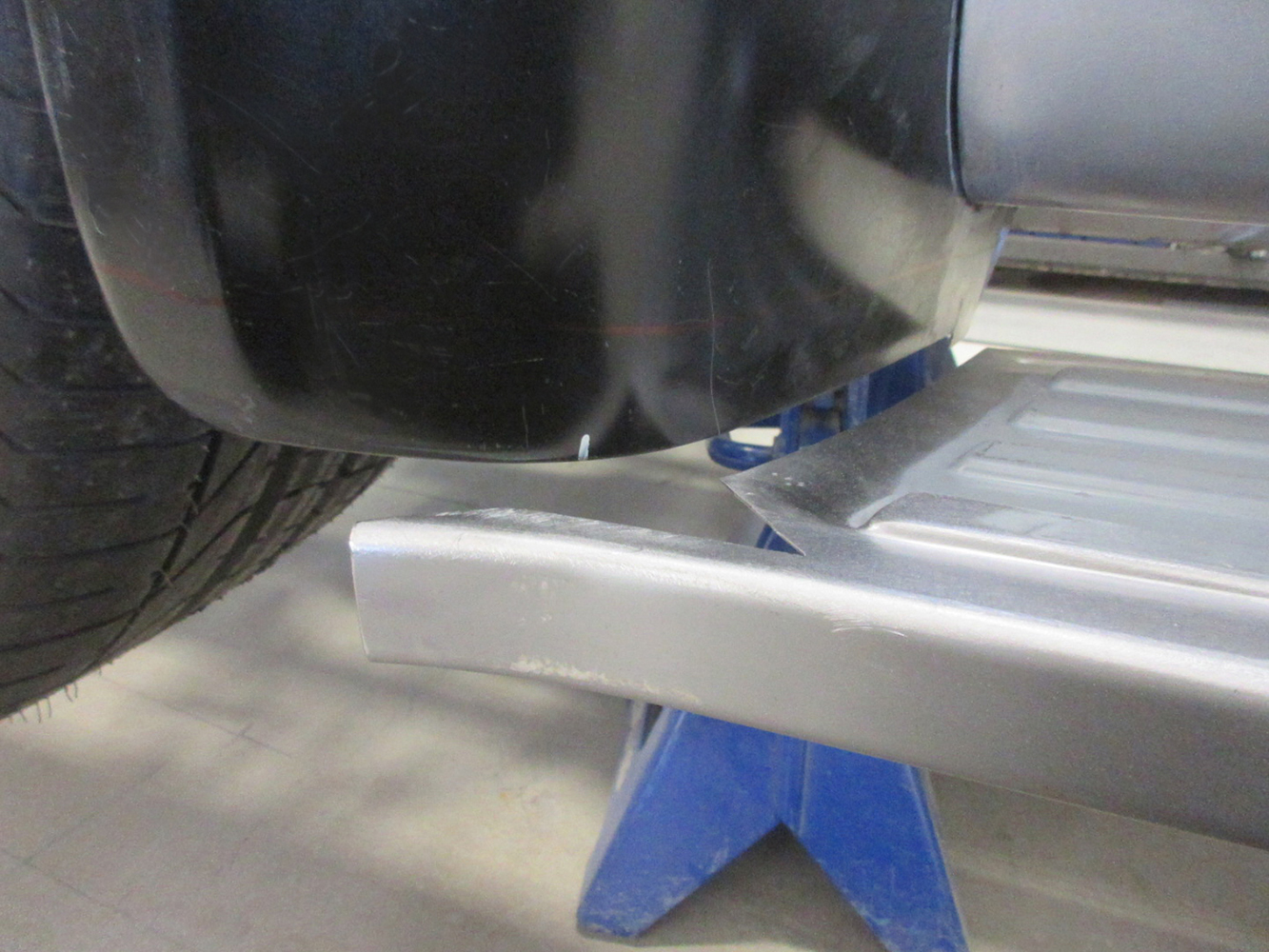
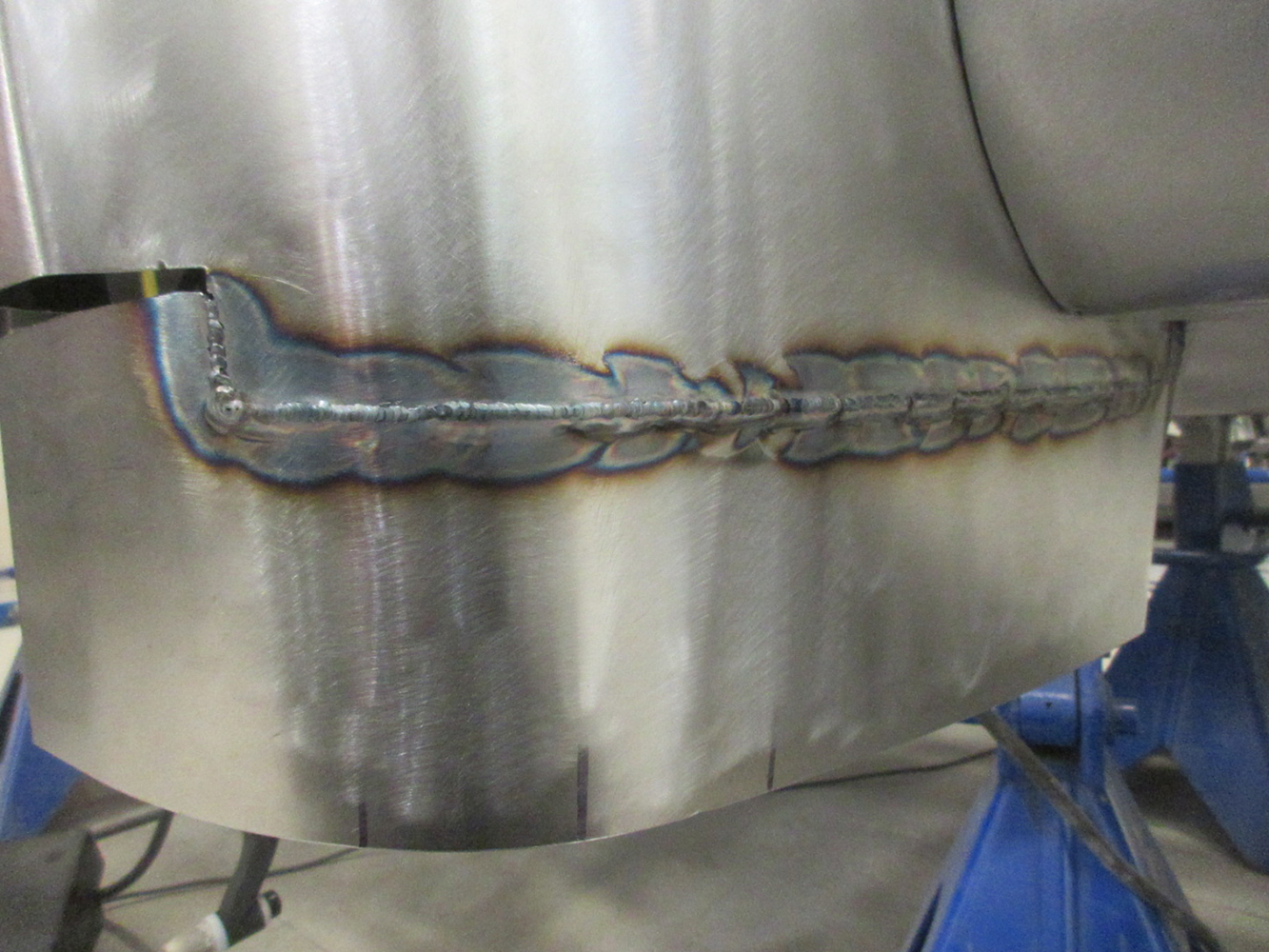
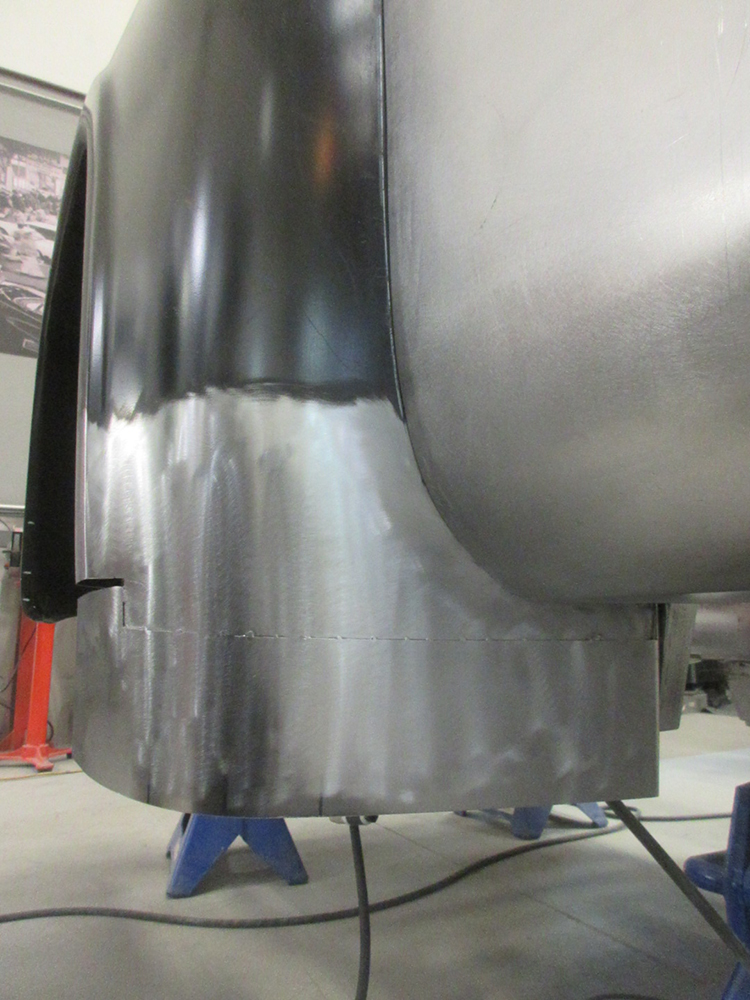
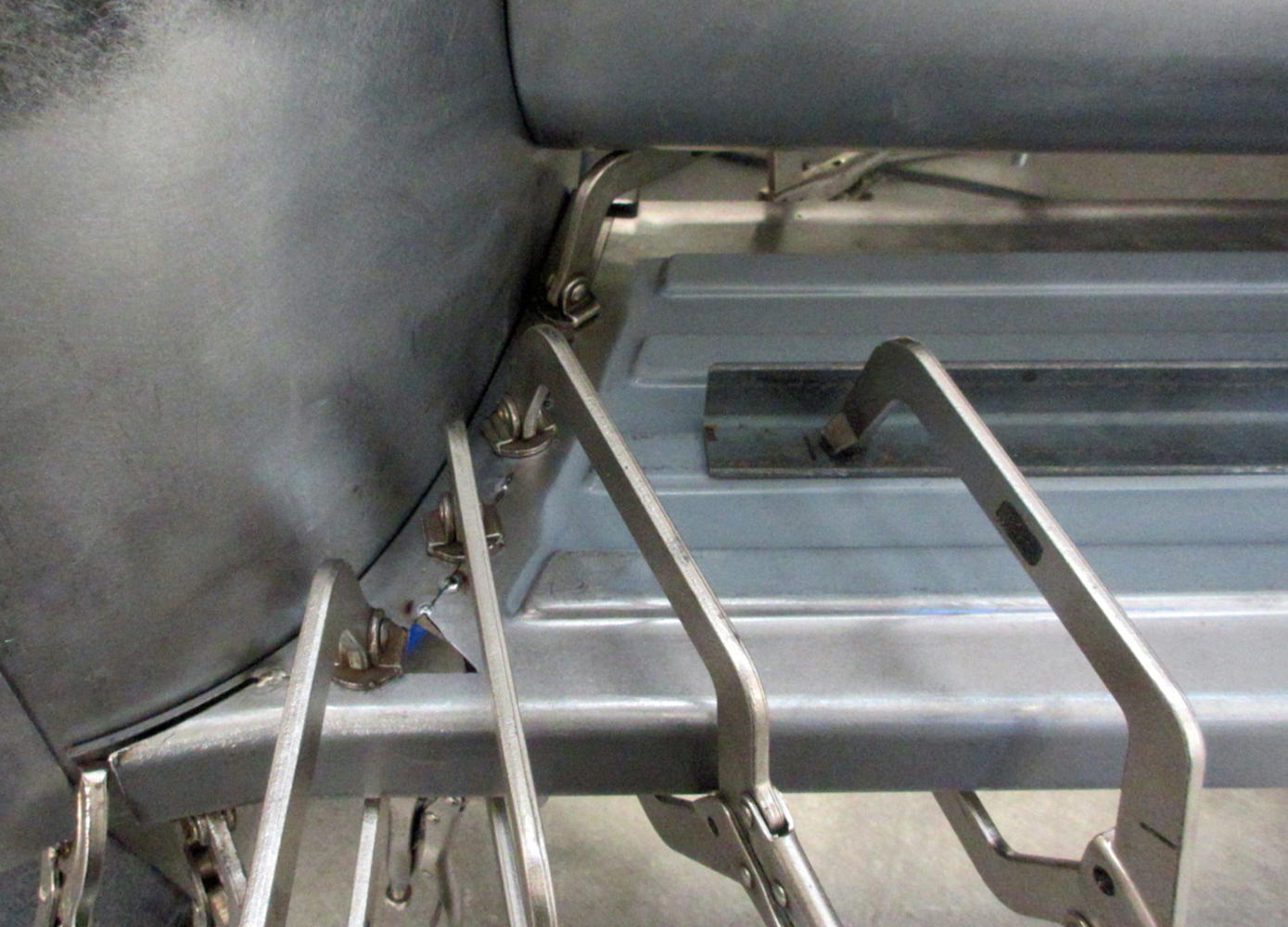
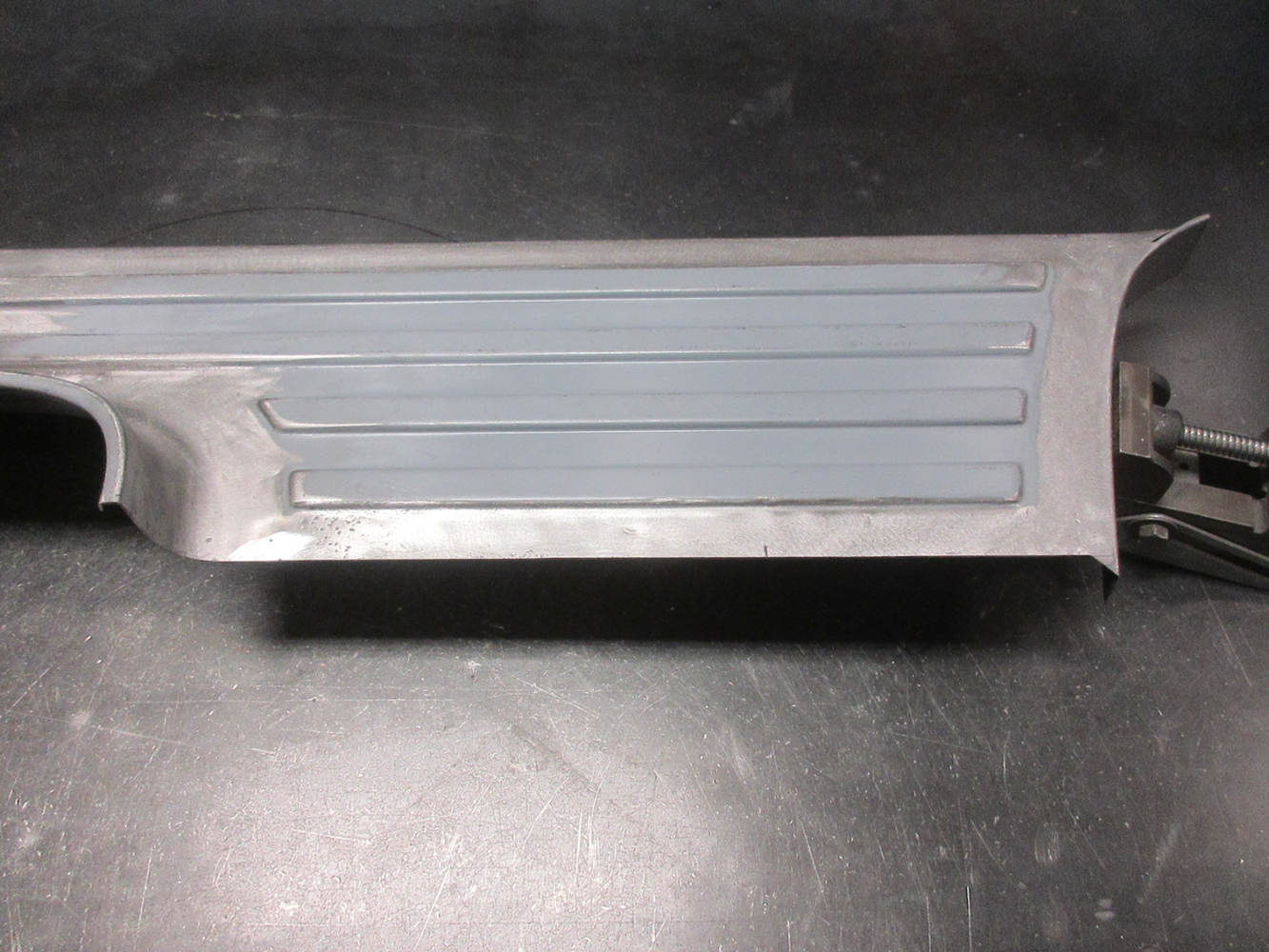
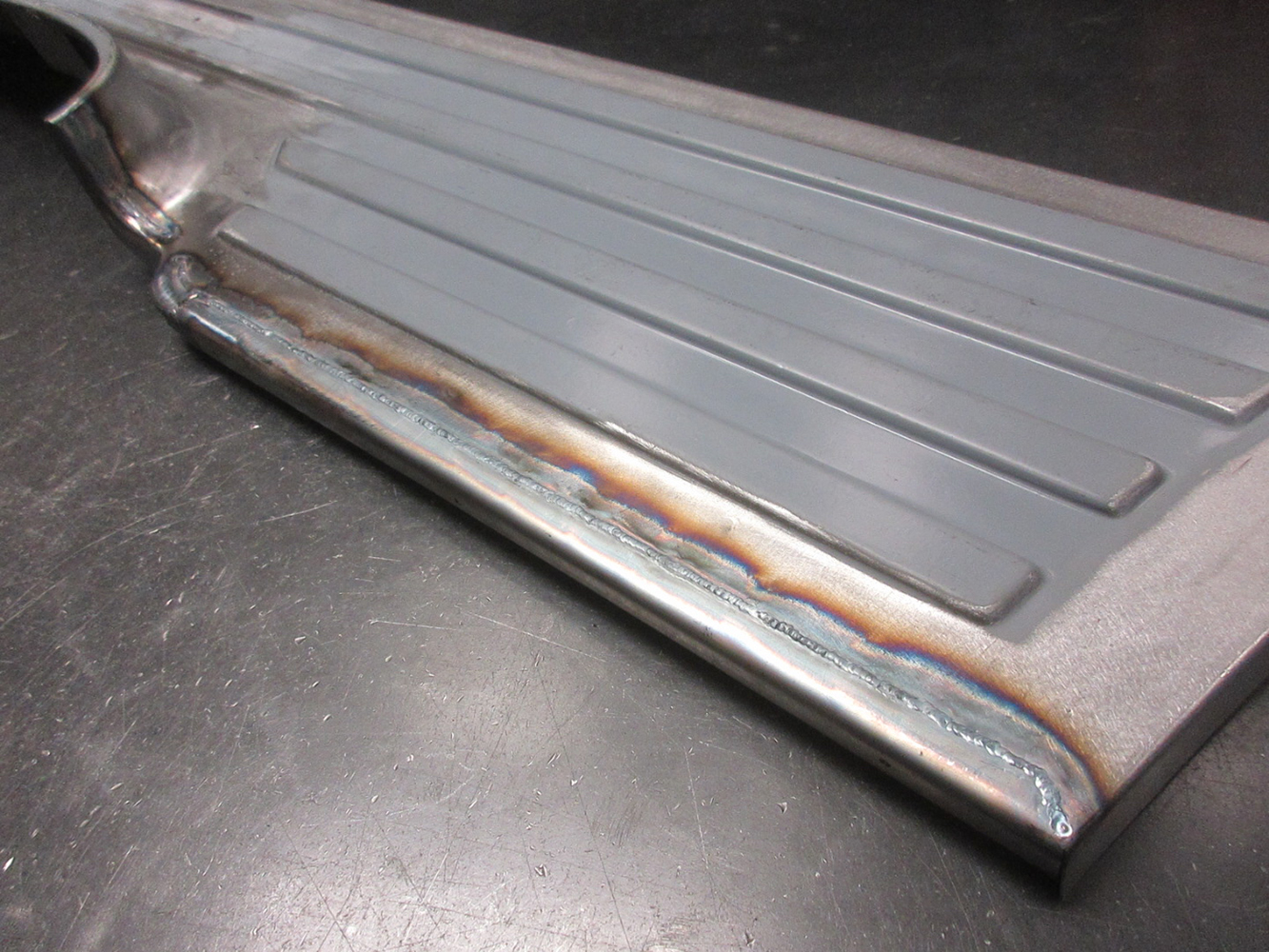
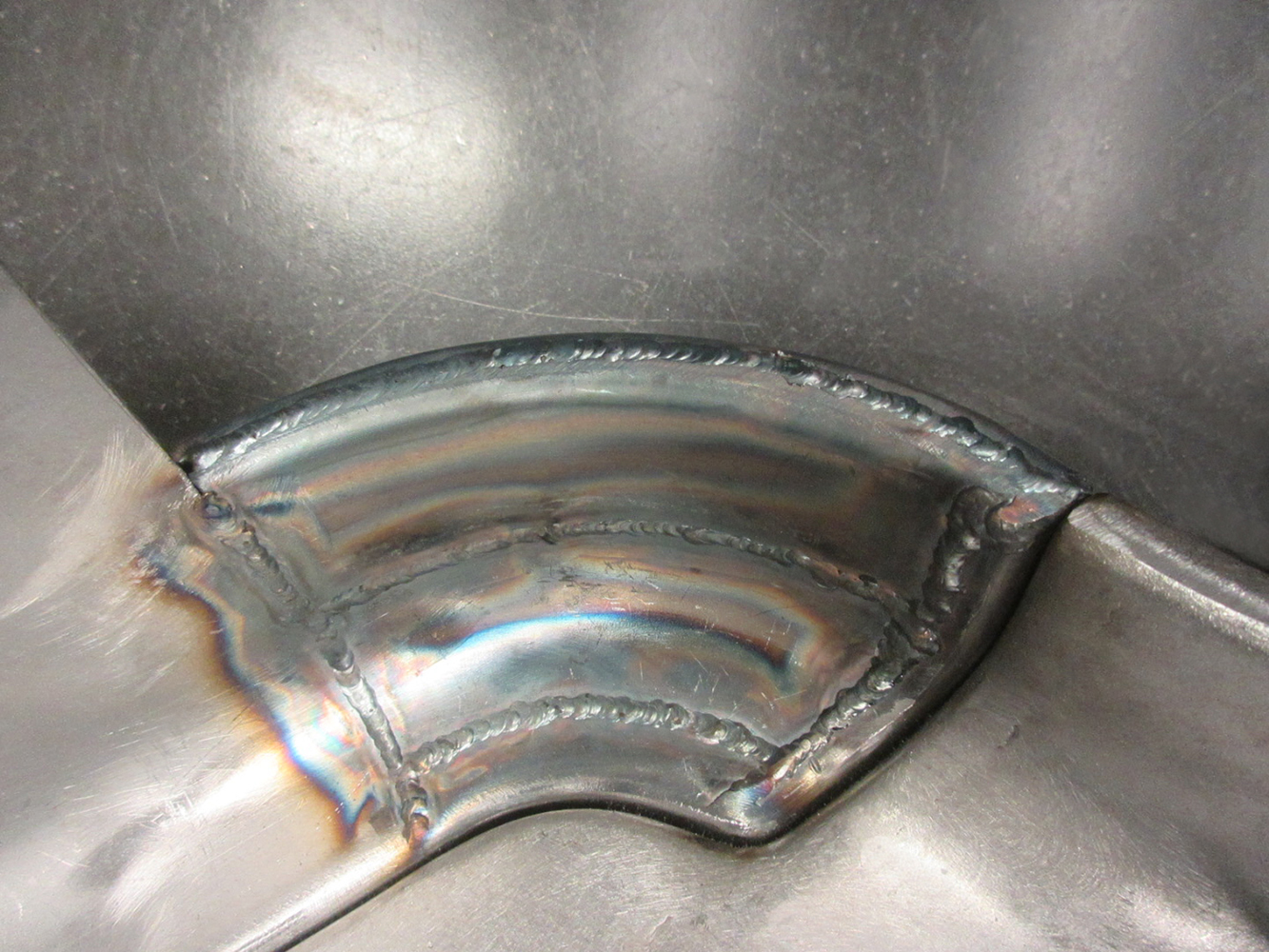
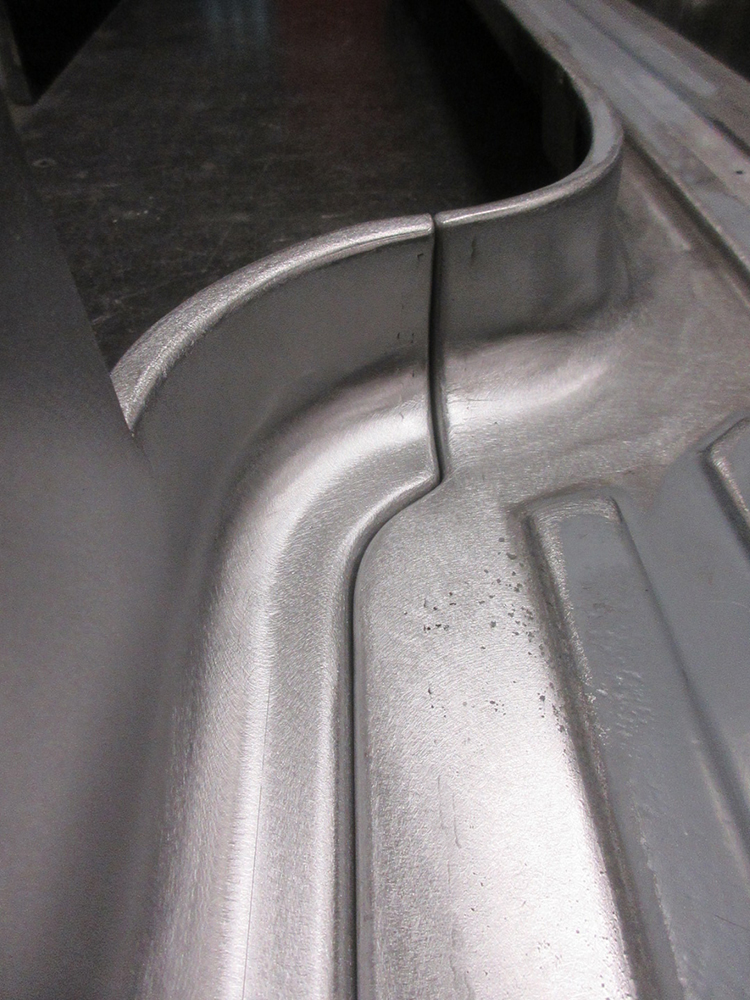
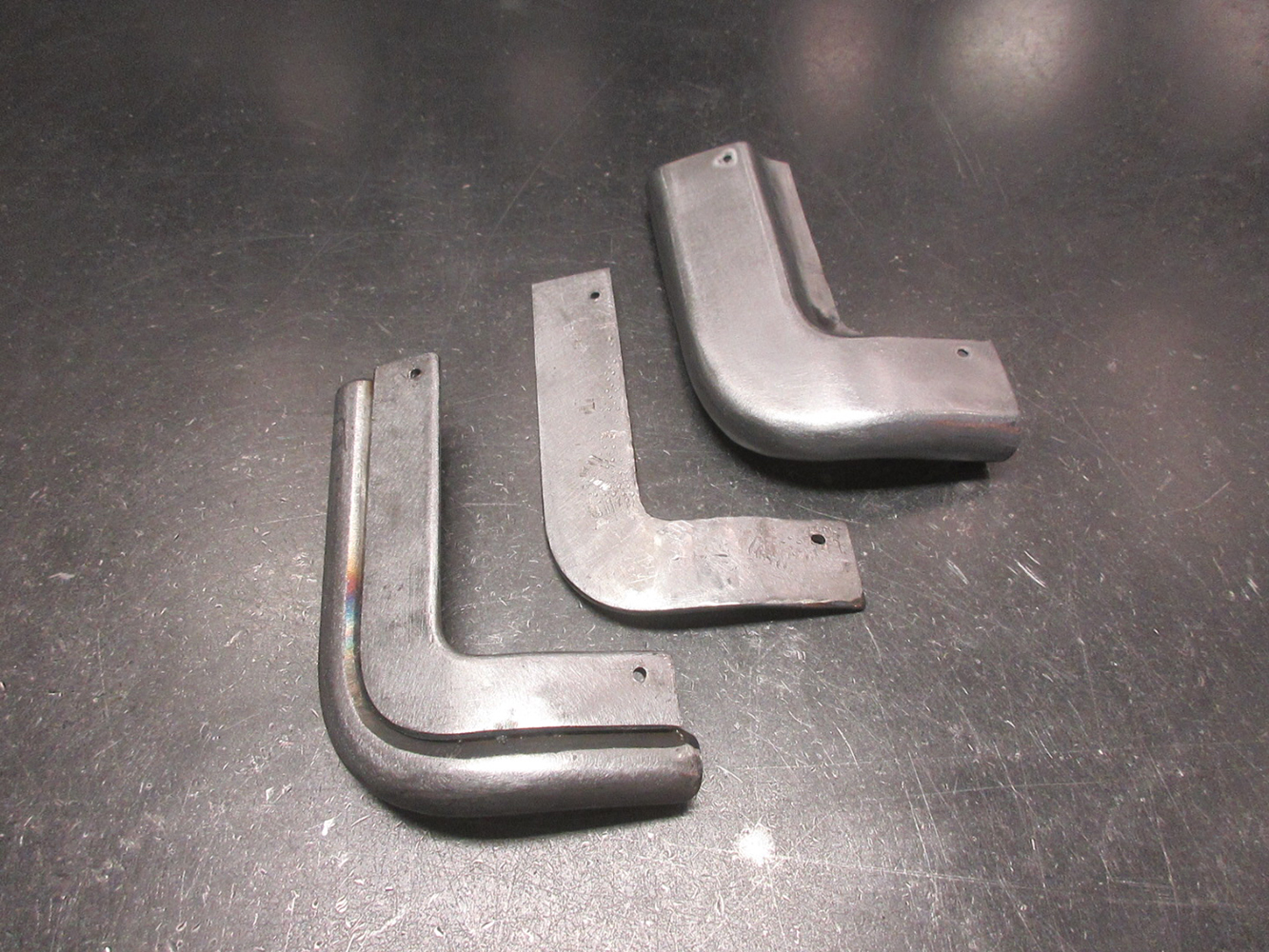
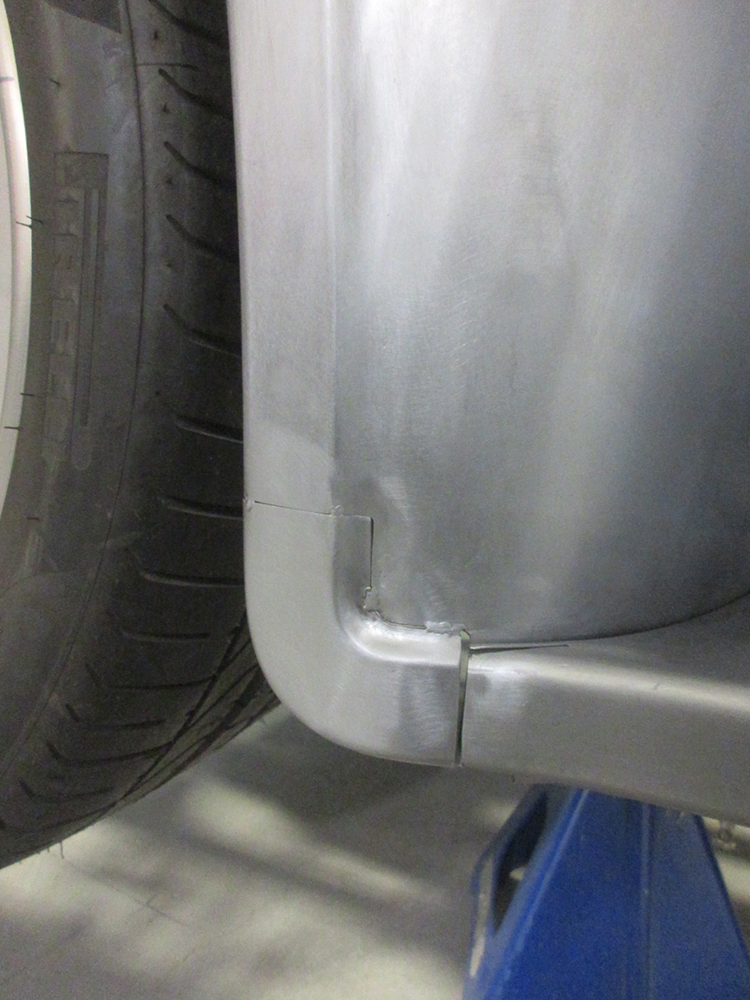
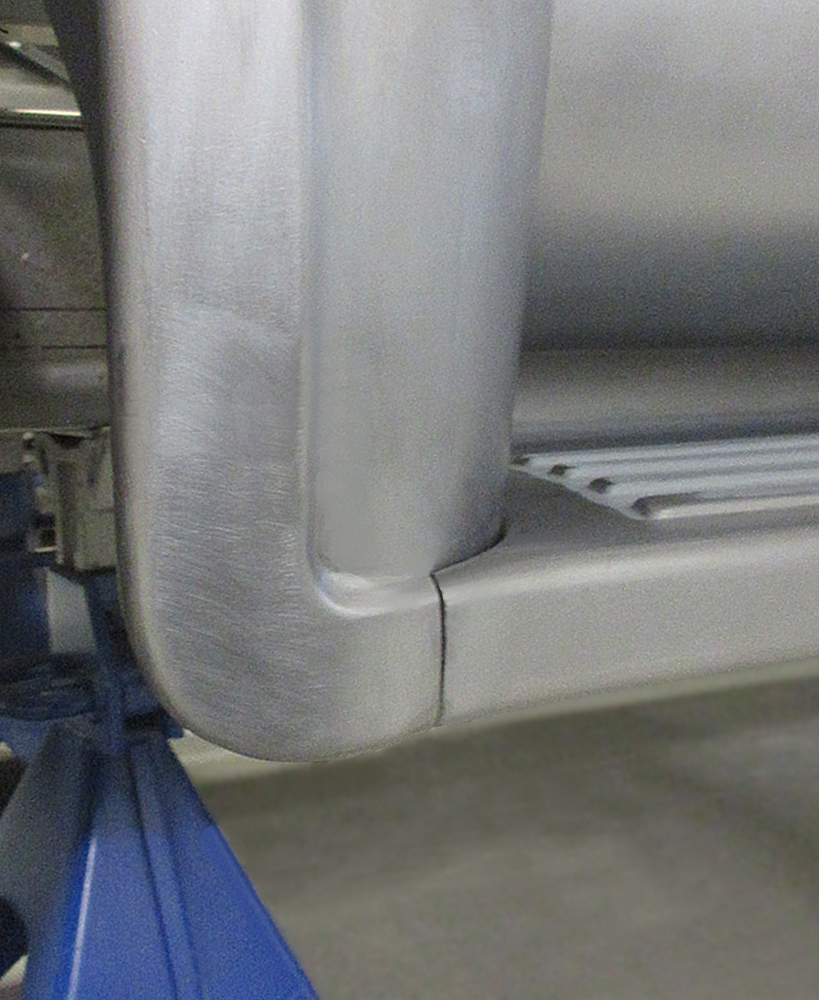
Check out this story in our digital edition here.
Source
Gary’s Rods & Restorations
(831) 728-7025
garysrods.com