By “Rotten” Rodney Bauman – Photography by the Author
Final-primed and guidecoated, do these doors look pretty “straight”? As shapely as their designers intended for them to be, there ought to be a better word to describe them. Thinking back, we may’ve touched on that subject once before, but I don’t recall any mention of working with Charles and Dave.
Back in the boat shop, my friend Charles preferred the word “fair.” Back in the body shop, my friend Dave would say “uniform.” Now as it sort of seems to me, either of those words fit better than “straight,” so I’ve adopted those two bits of my coworkers/friends’ terminology.
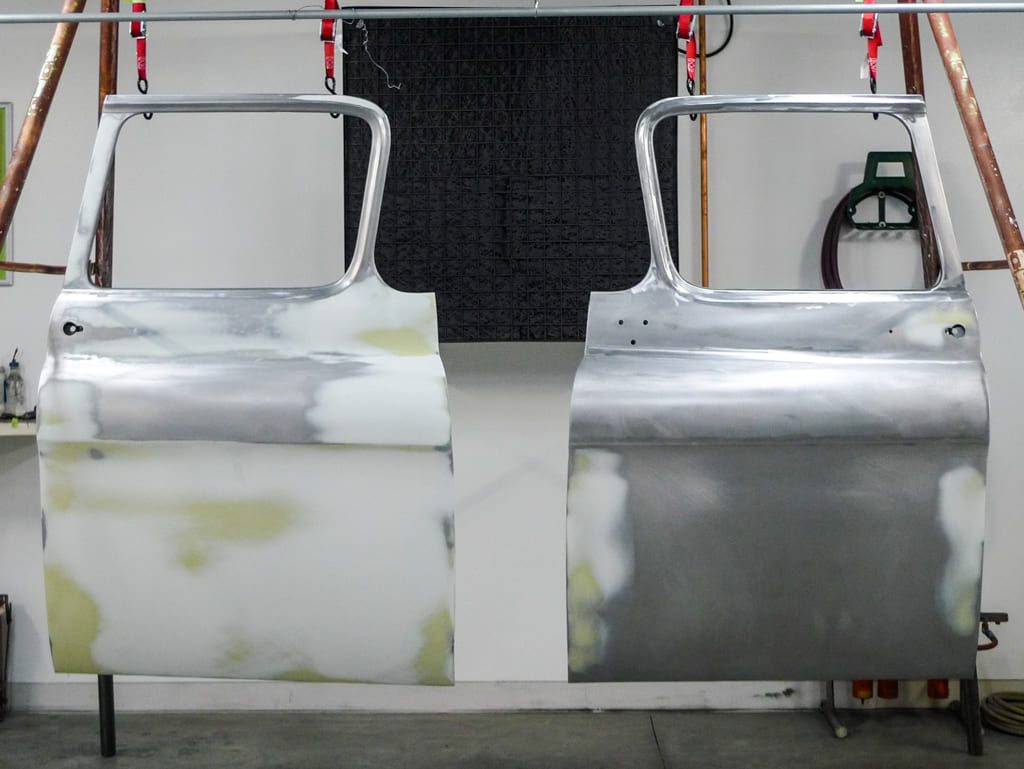
Read More: Complementing Body Lines With Custom Running Boards
In an earlier tech story we covered initial steps for achieving uniform fairness in the bodywork process. For our ’55 Chevy second-series build we’re using one original door and one reproduction from Brothers Trucks. Both doors had their own unique issues, but due to rust, dents, and extra holes, the original required a good deal more bodywork.
Our doors (along with other panels) are currently in first-round primer-surfacer. Let’s not go into which brand exactly. Primer-surfacer availability tends to depend on shop geography and we have choices wherever we might be.
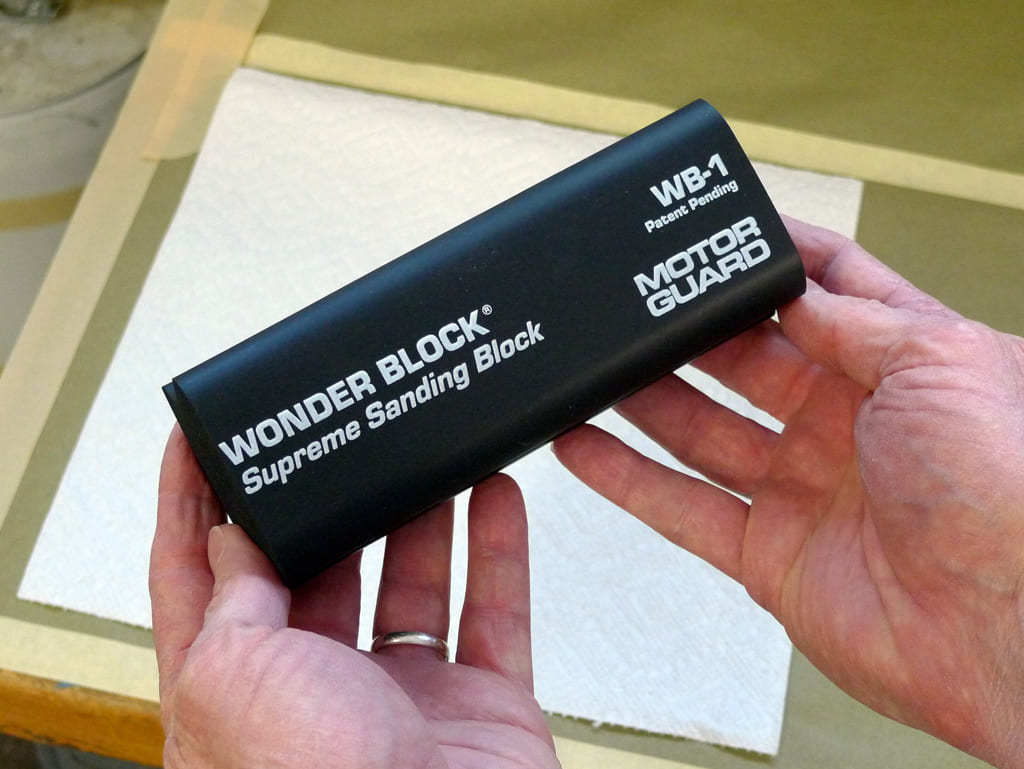
Here, our own favored primer-surfacer is “regular-build” urethane. Over steel, polyester filler, and epoxy primer we generally go with three wet coats of reduced primer-surfacer for the initial application.
Particularly prior to skim-coating, polyester filler applications tend to sand at varying rates, and areas where feathered edges meet steel (or epoxy if that’s your MO) require extra caution as undercutting can easily occur.
Now in first-round primer-surfacer we have for the first time a surface that’ll sand absolutely evenly. This is our chance to fine-tune our bodywork even further.
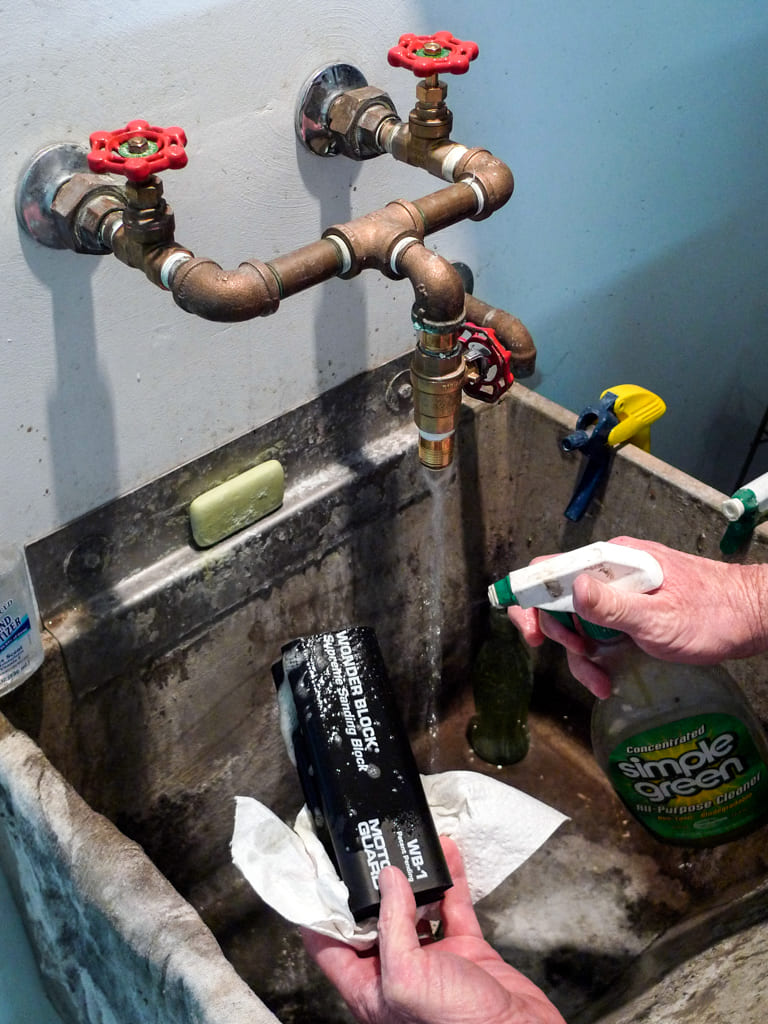
Read More: How To Restore A Delco-Remy Horn
Here at this shop we have a pretty-set routine. Our first-round primer-surfacer will be faired with 120-grit adhesive-backed longboard paper. Sanding blocks and fairing boards will be selected to match the varying shapes of our rather curvaceous Task Force doors.
To ensure flexibility, elasticity, and durability down the road, we’ll keep on sanding till our first-round primer-surfacer is thin enough to just about see through. If we expose a little steel or polyester filler that’s usually OK at this stage. When the doors are hung on their fixtures, masked, and chemically cleaned as necessary, they’ll receive one coat of epoxy primer, followed by two coats of reduced urethane primer-surfacer, which we’ll call final-prime.
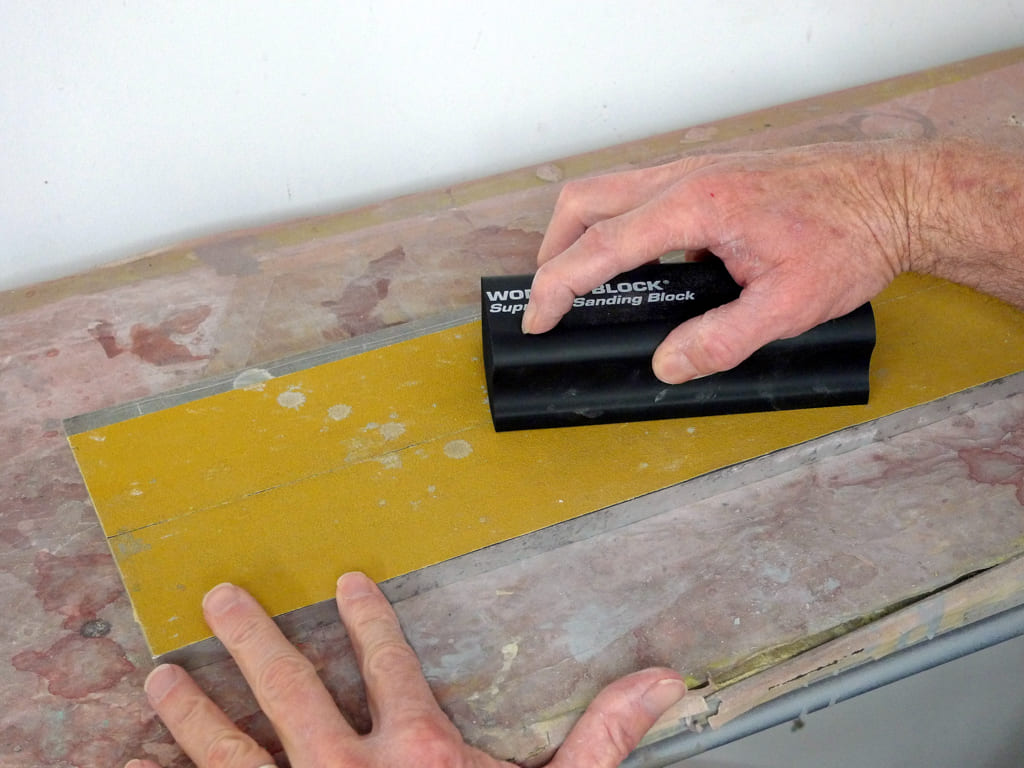
From final-prime on, paint prep can be done with small flexible blocks and scuff pads for the most part. There’ll be no further need for the longer fairing boards. With only a couple of homebrew exceptions, most of our blocks, boards, and abrasives are available through Summit Racing Equipment.
Of course there’s more to all of this than can be covered in a single printed tech story. Apart from a randomly pointed index finger, the following photos won’t clearly illustrate the direction of sanding strokes, so know that following each lap of diagonal panel passes, we’re switching up to counter in a crosshatch-type of pattern.
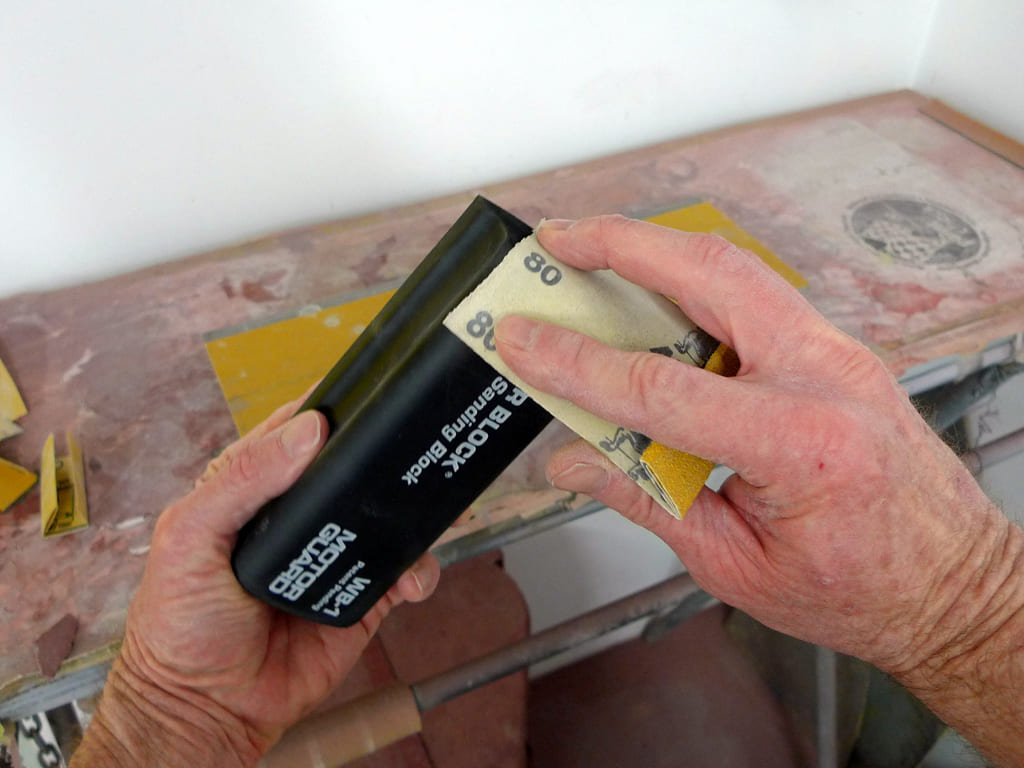
Read More: Modern Tech & Old School Hammerforming
If there’s room for just one more thing I’d stress the importance of light pressure and sharp abrasives. At this crucial final-fairing stage, downward pressure on these doors would push their skins out of their natural shapes. The skins won’t sand accurately that way, and if we don’t remain conscious of that, we’ll never achieve uniform fairness.
On those notes, let’s go on and do this job. It’s just another step along the way toward the type of finish our customers expect these days. Perhaps you’ve noticed, too—the bar only goes higher.
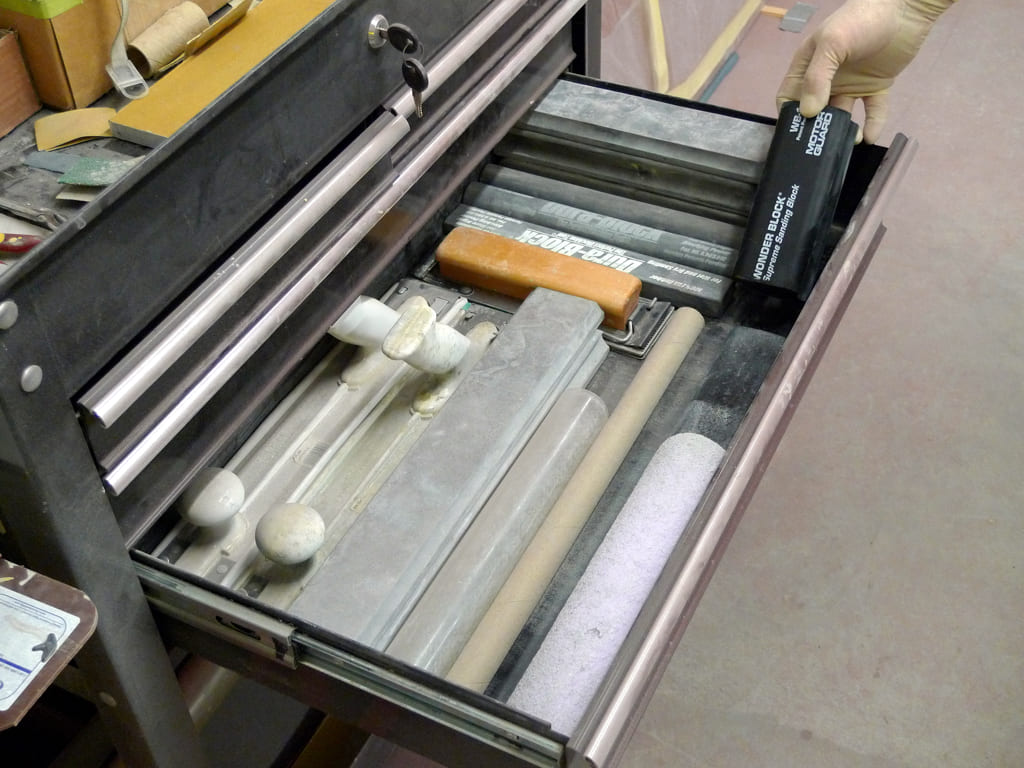
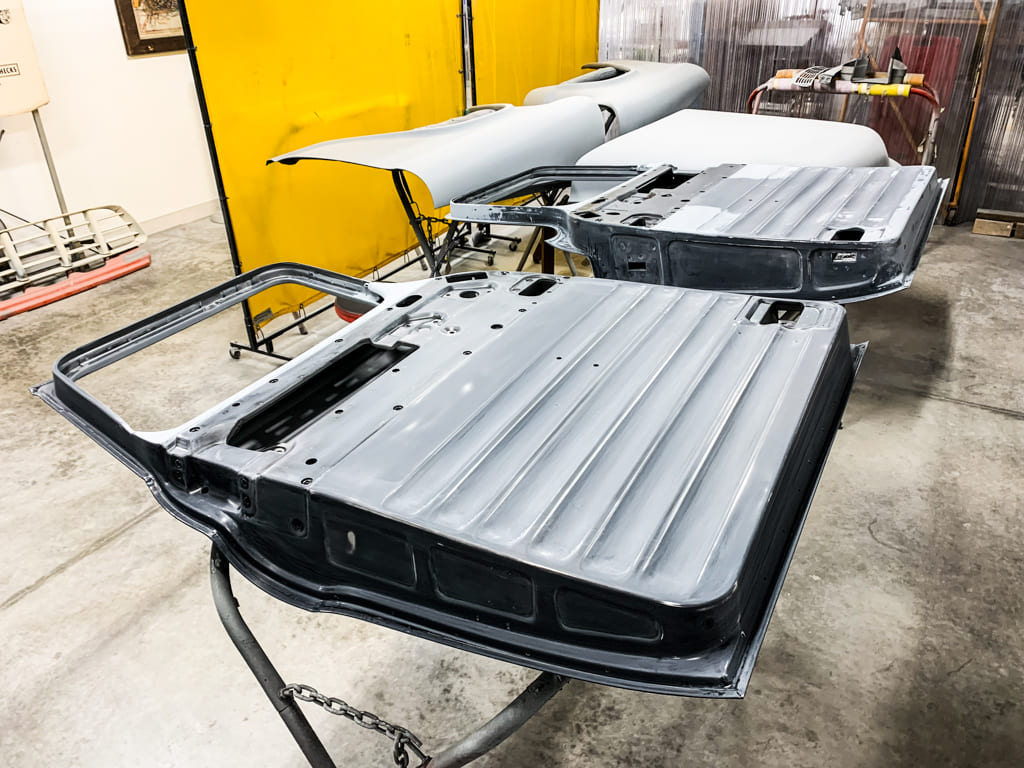
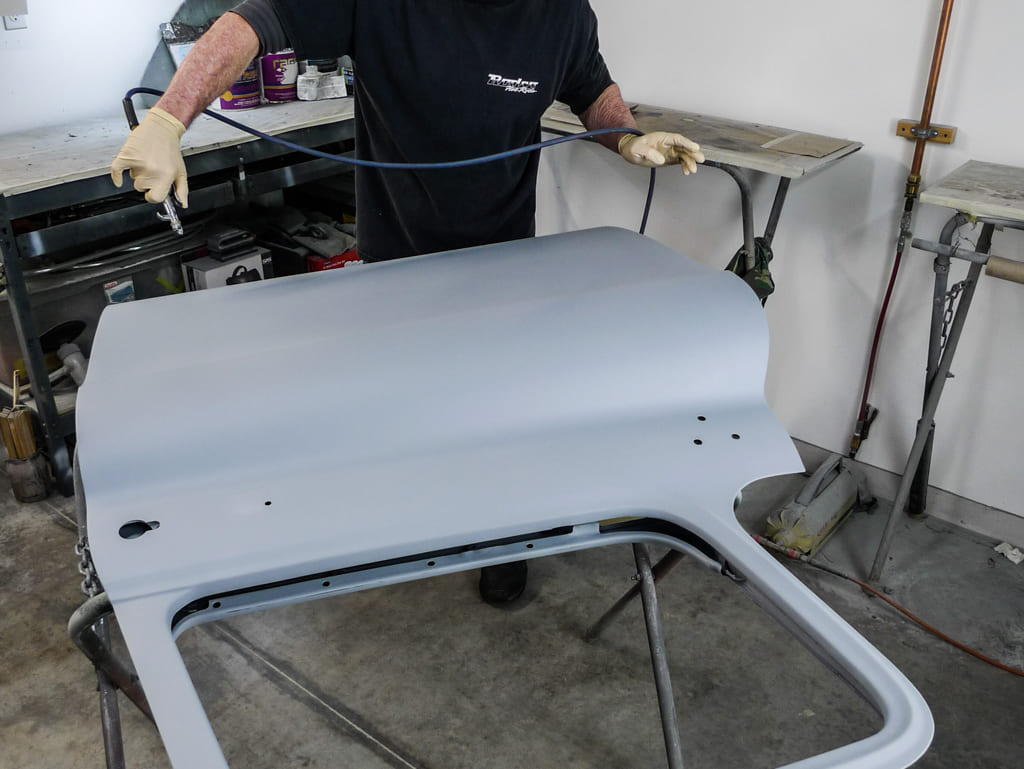
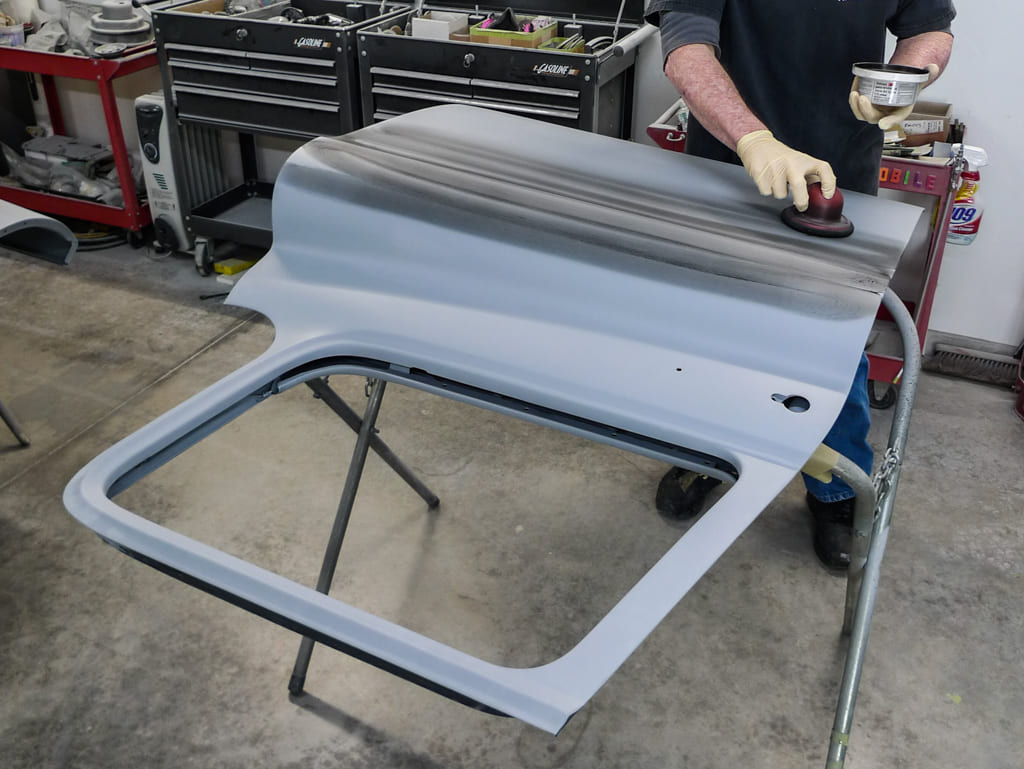
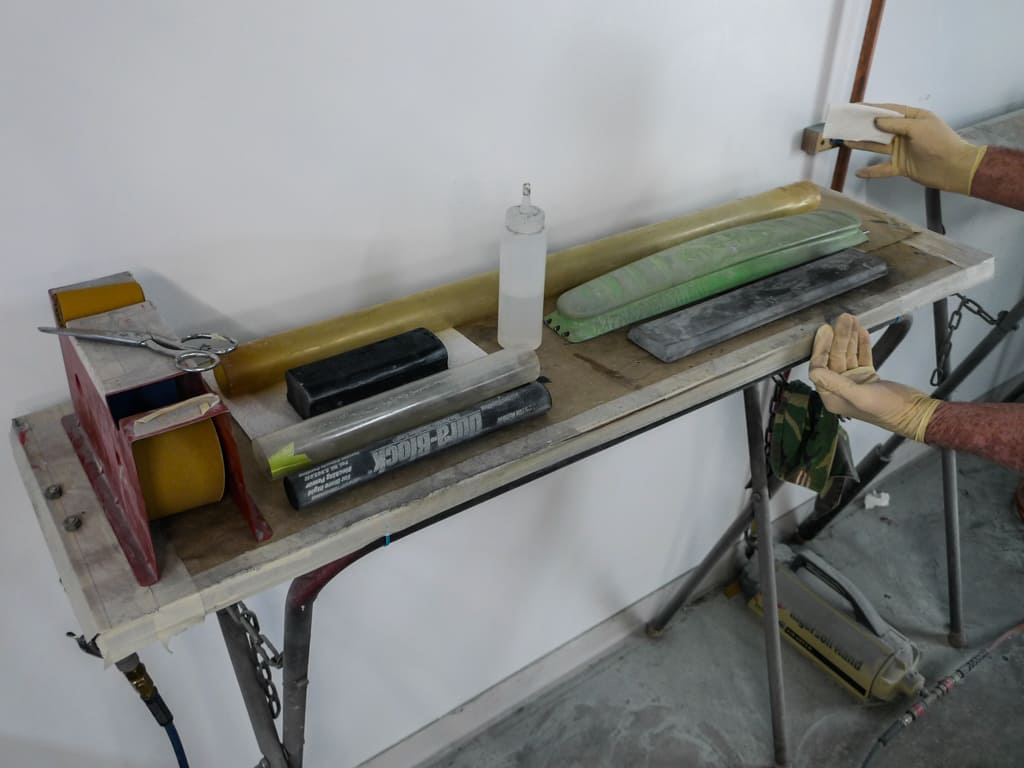
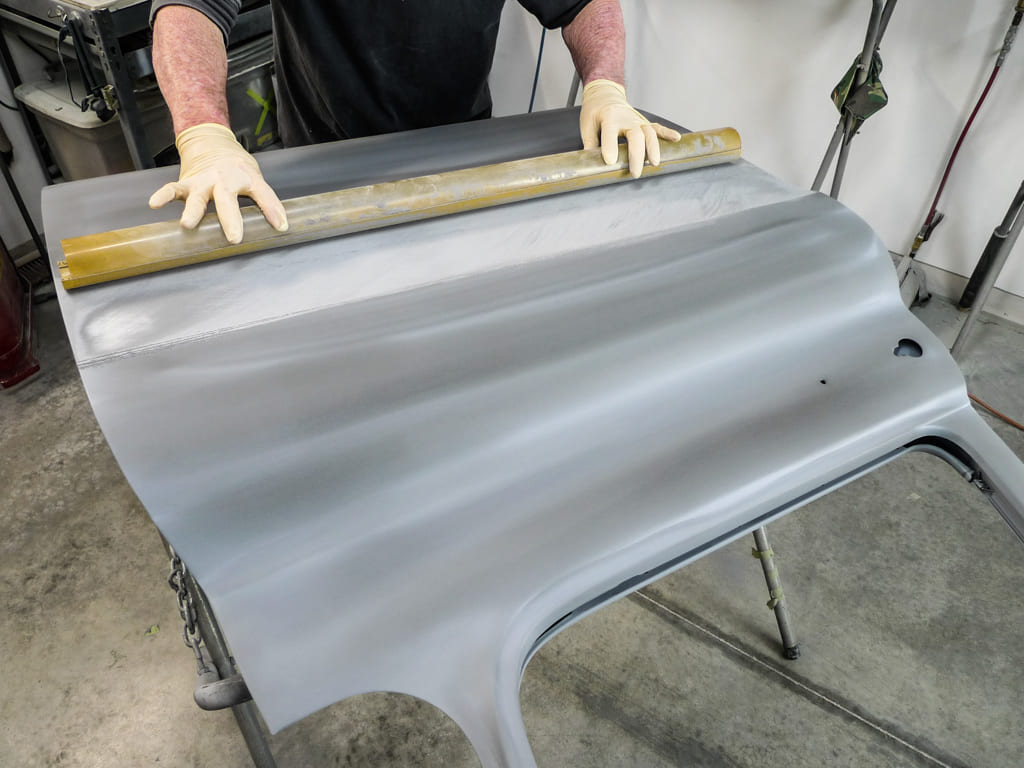
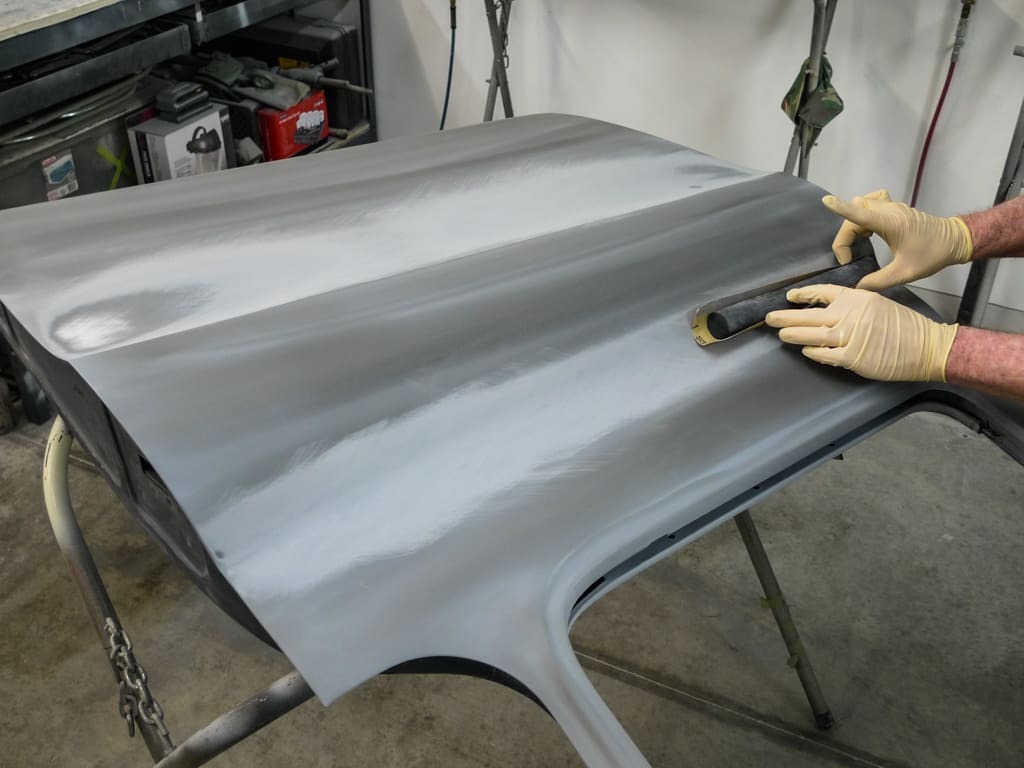
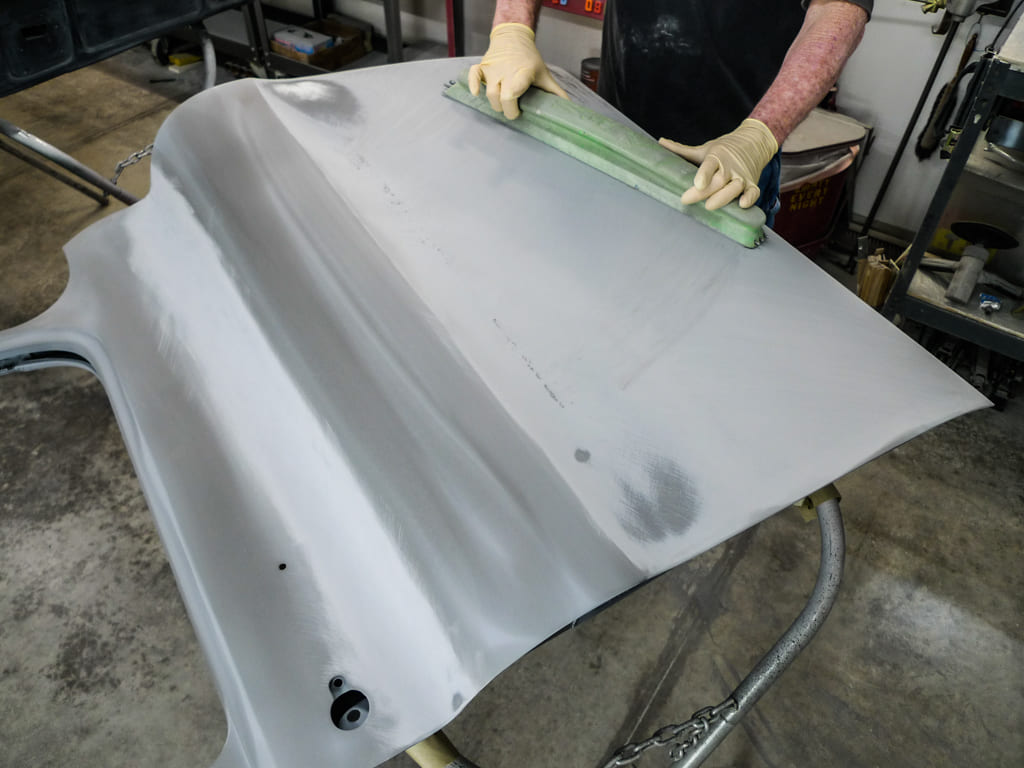
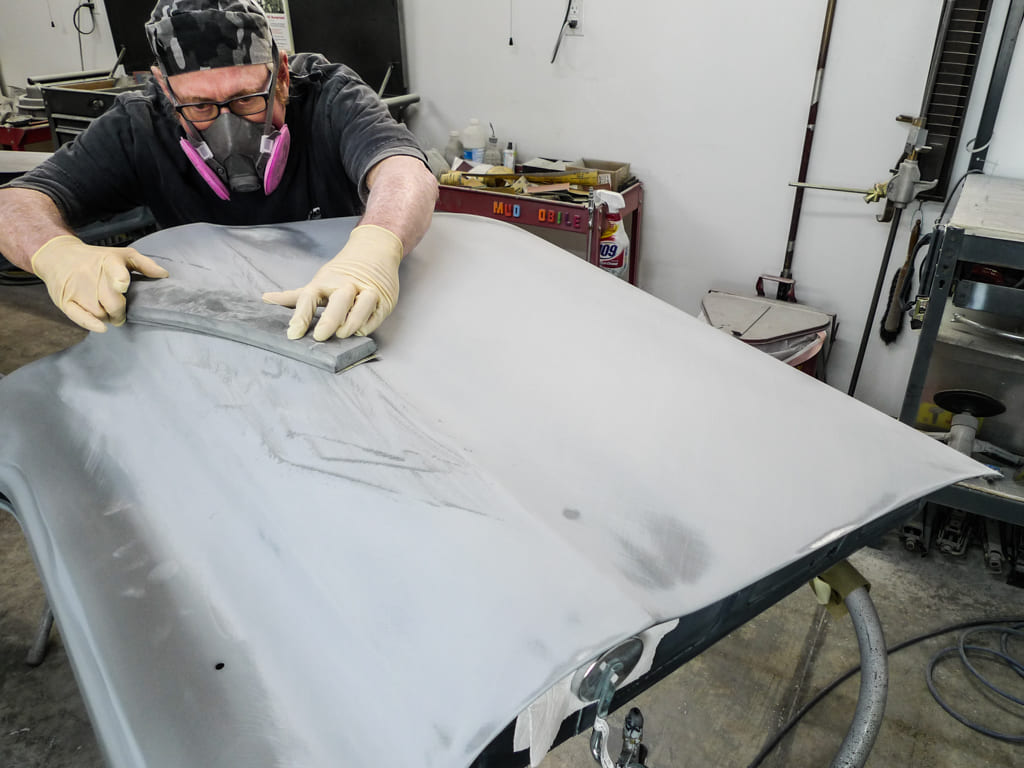
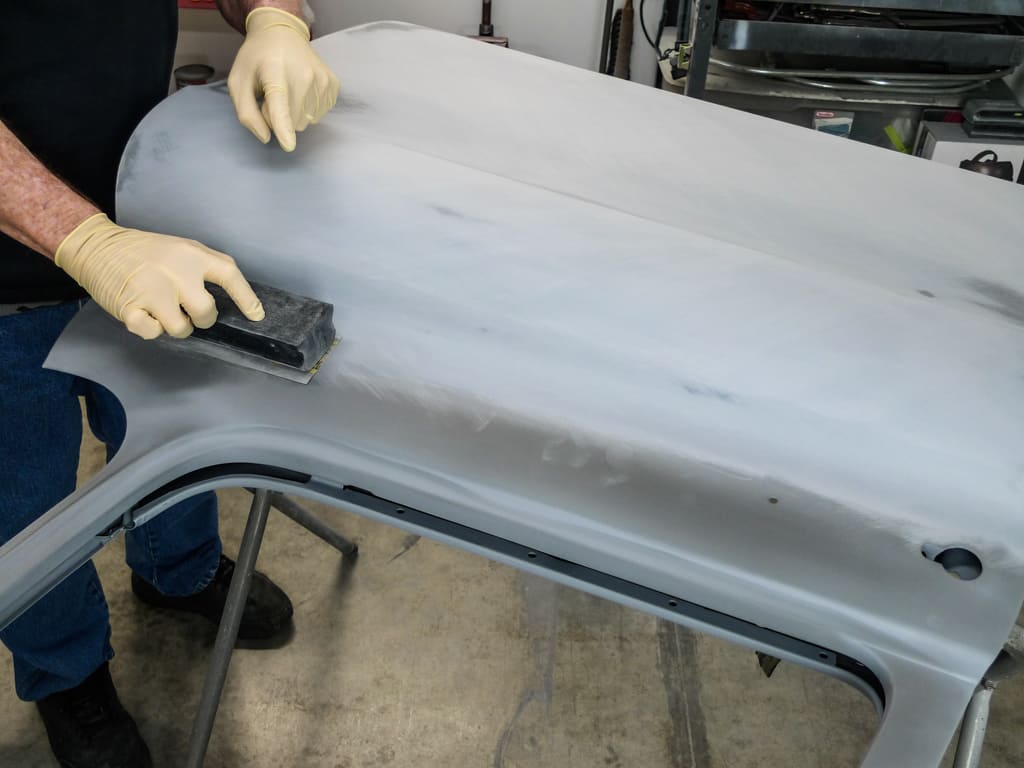
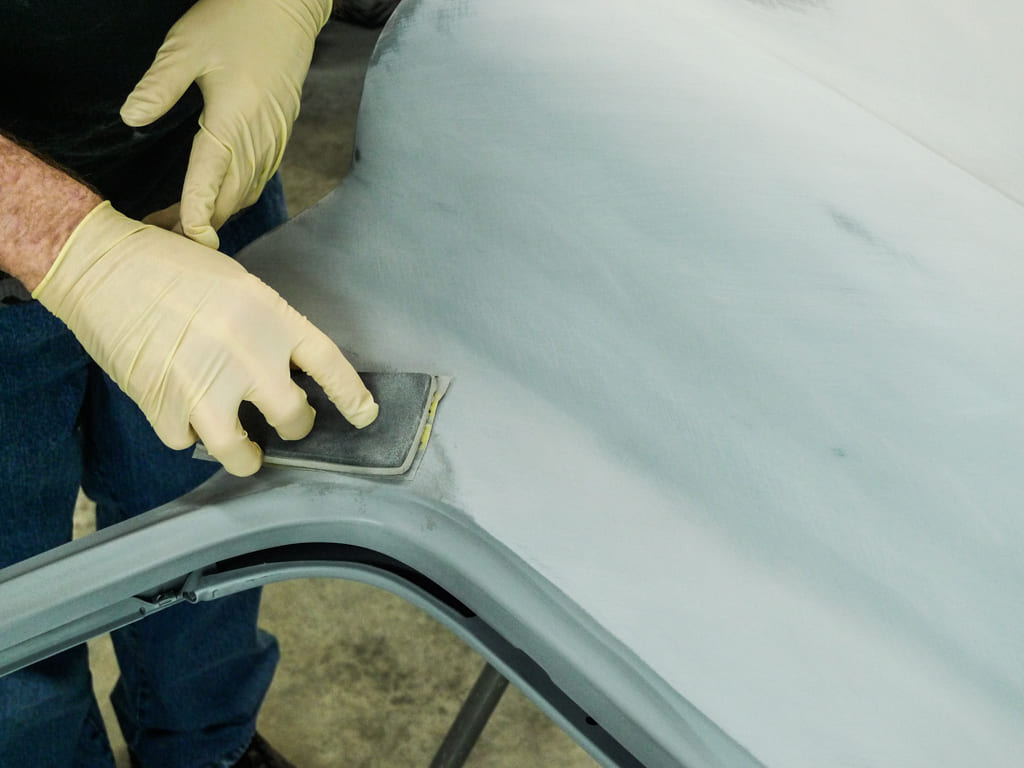
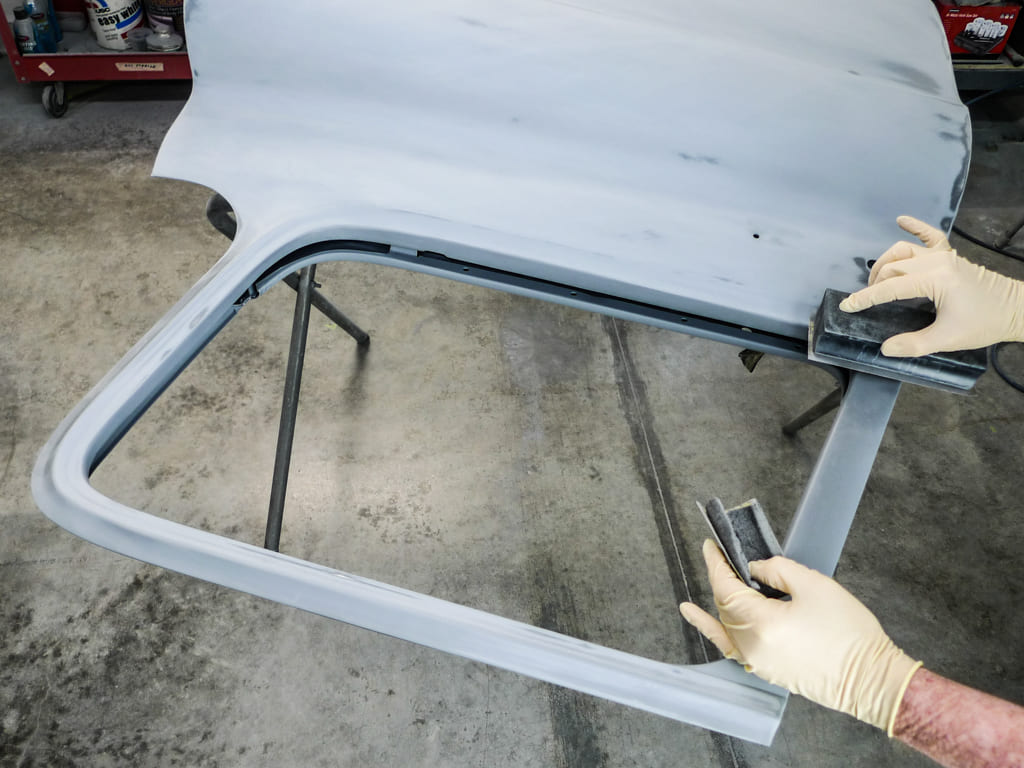
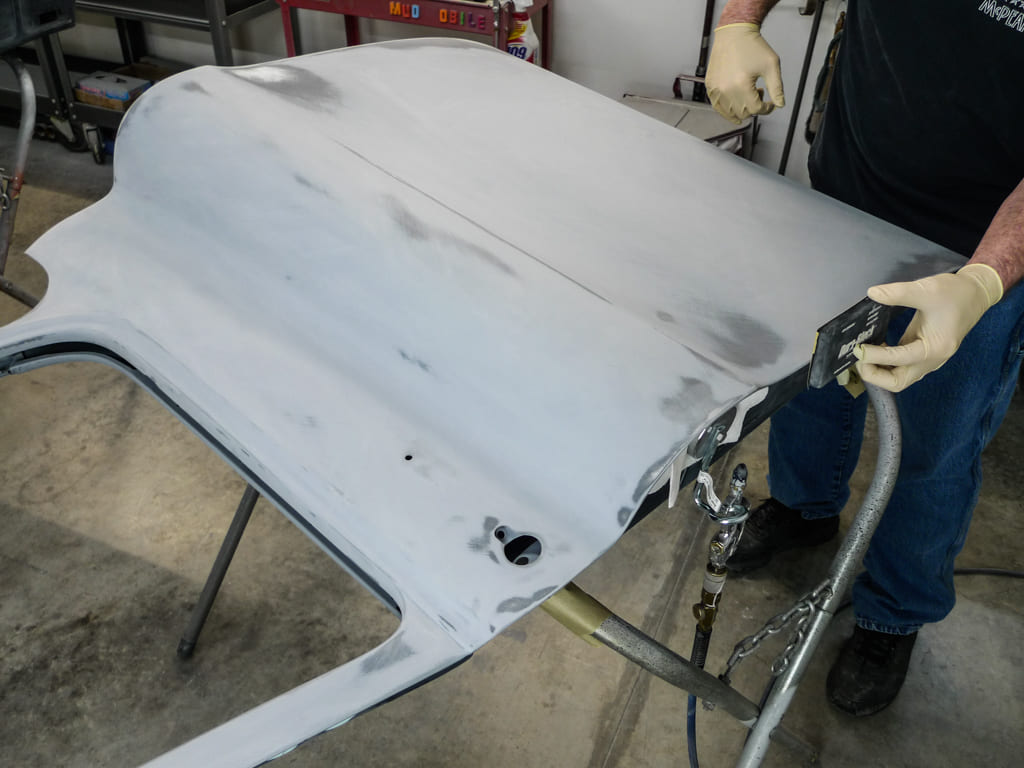
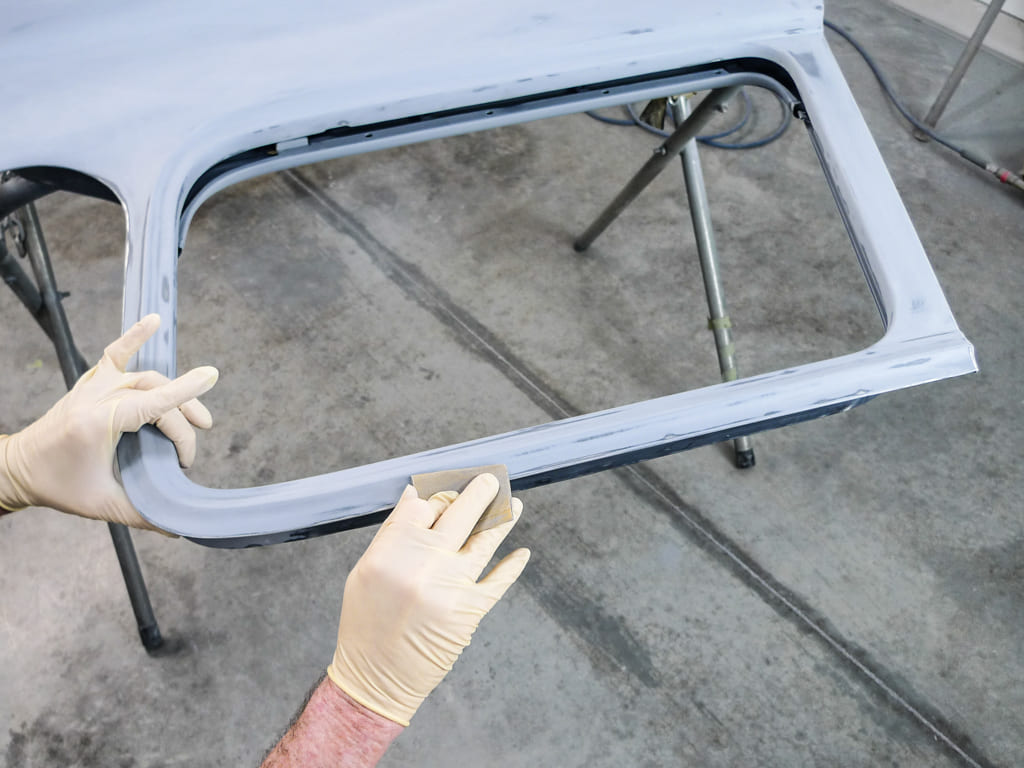
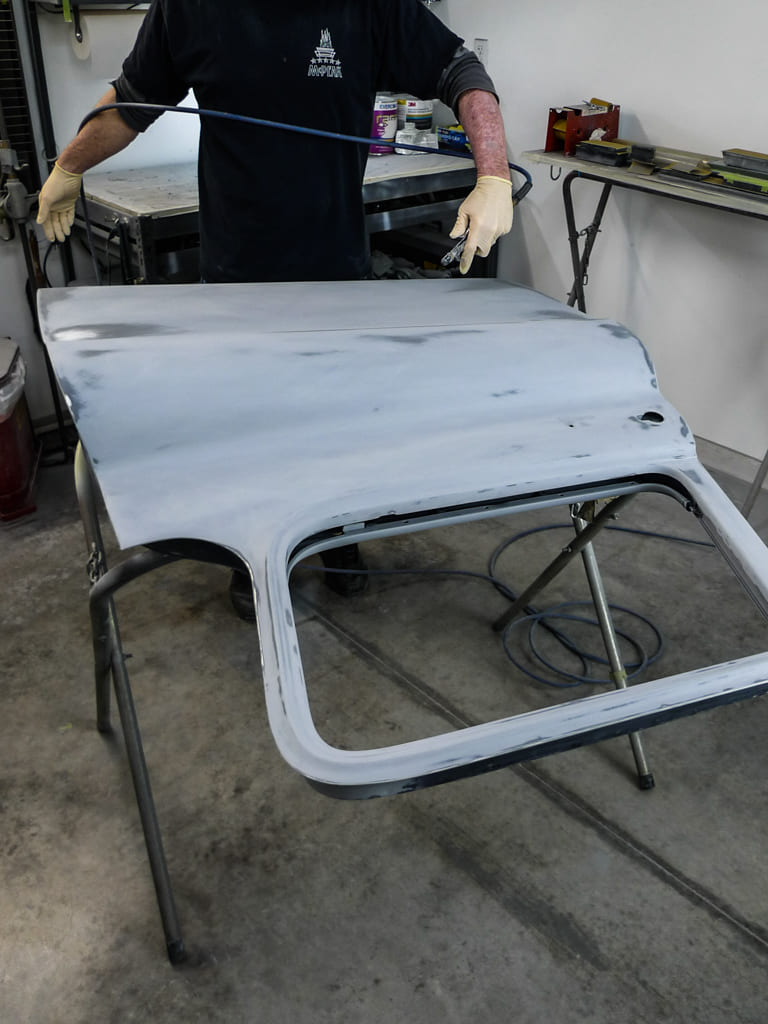
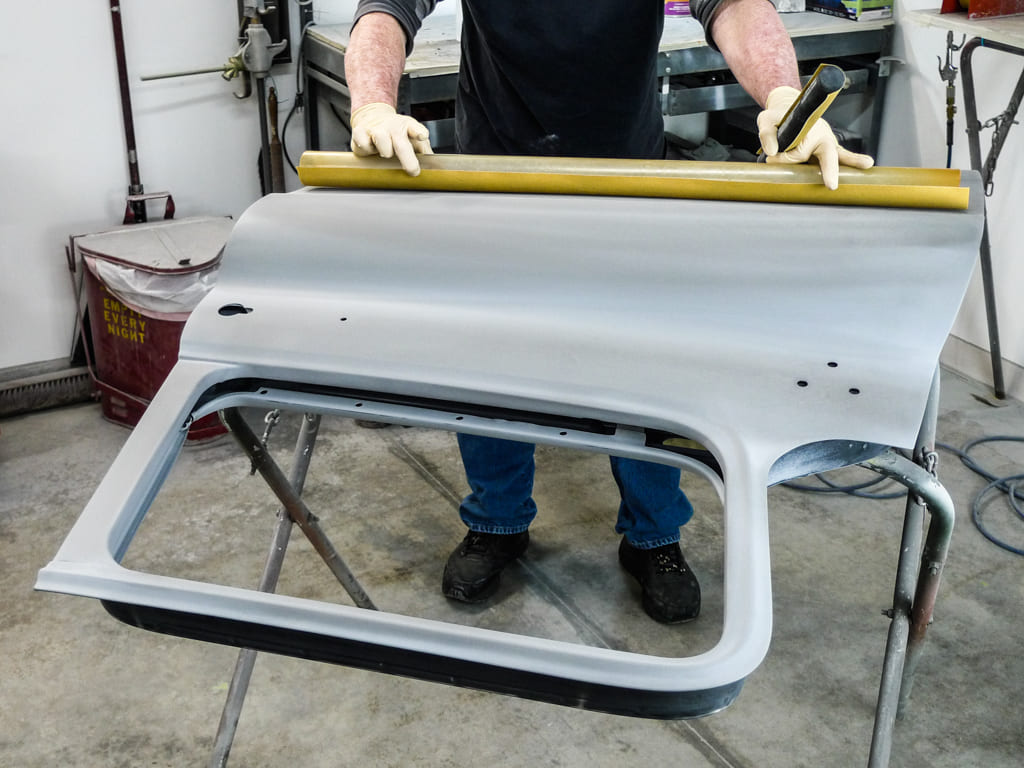
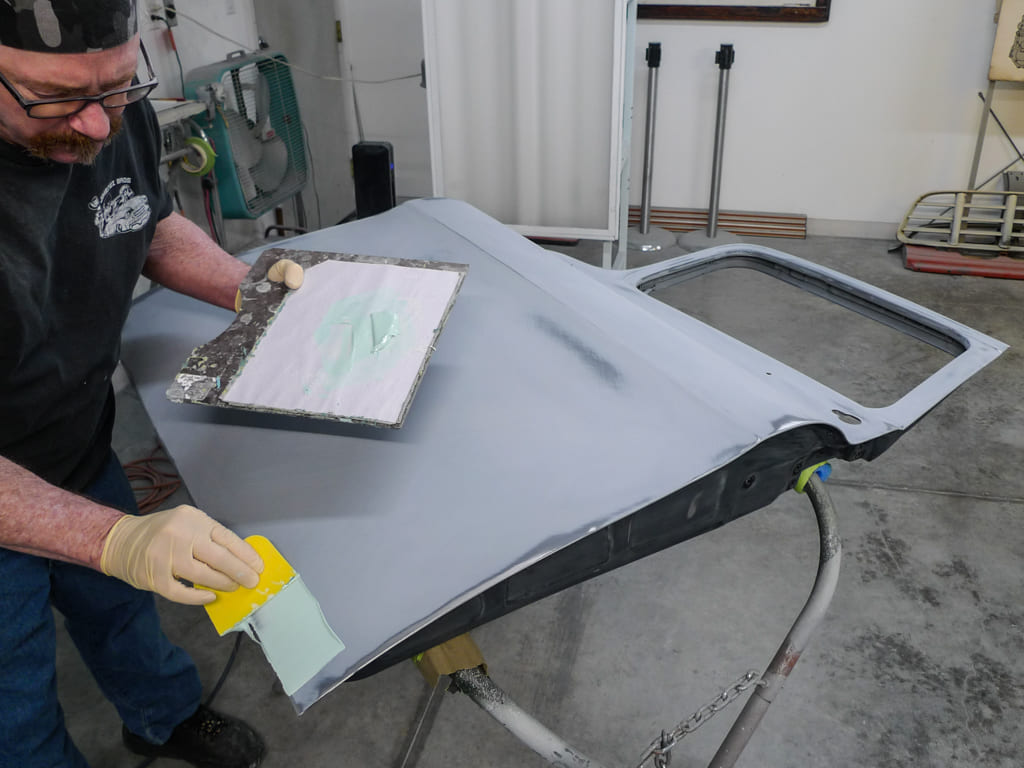
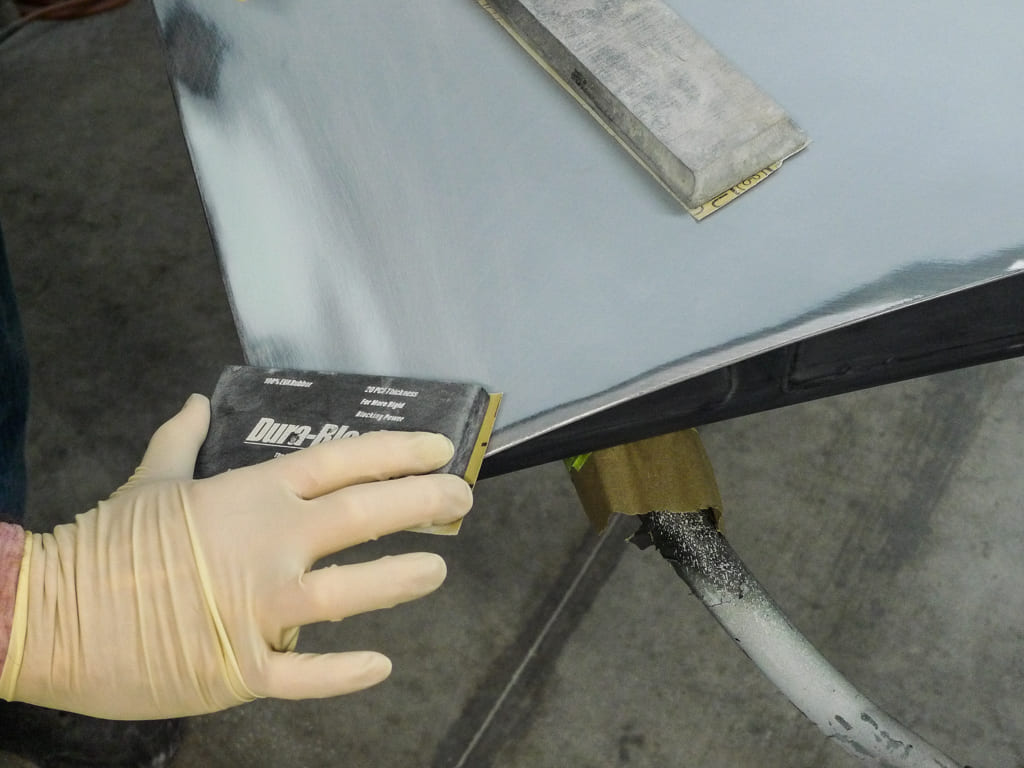
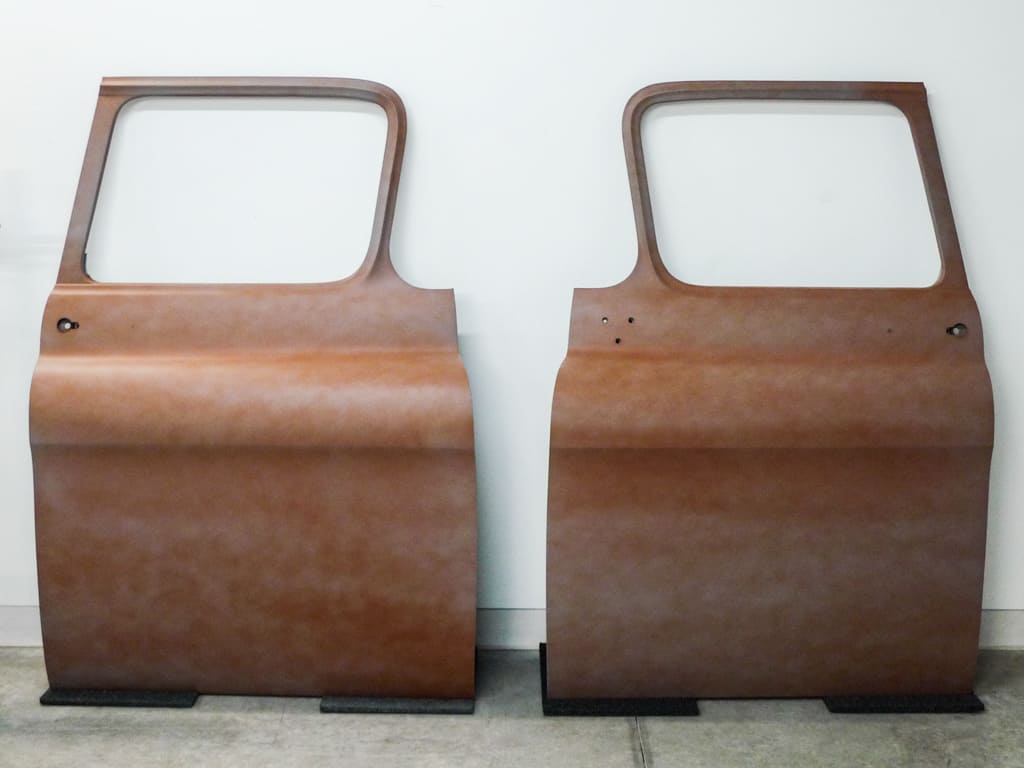
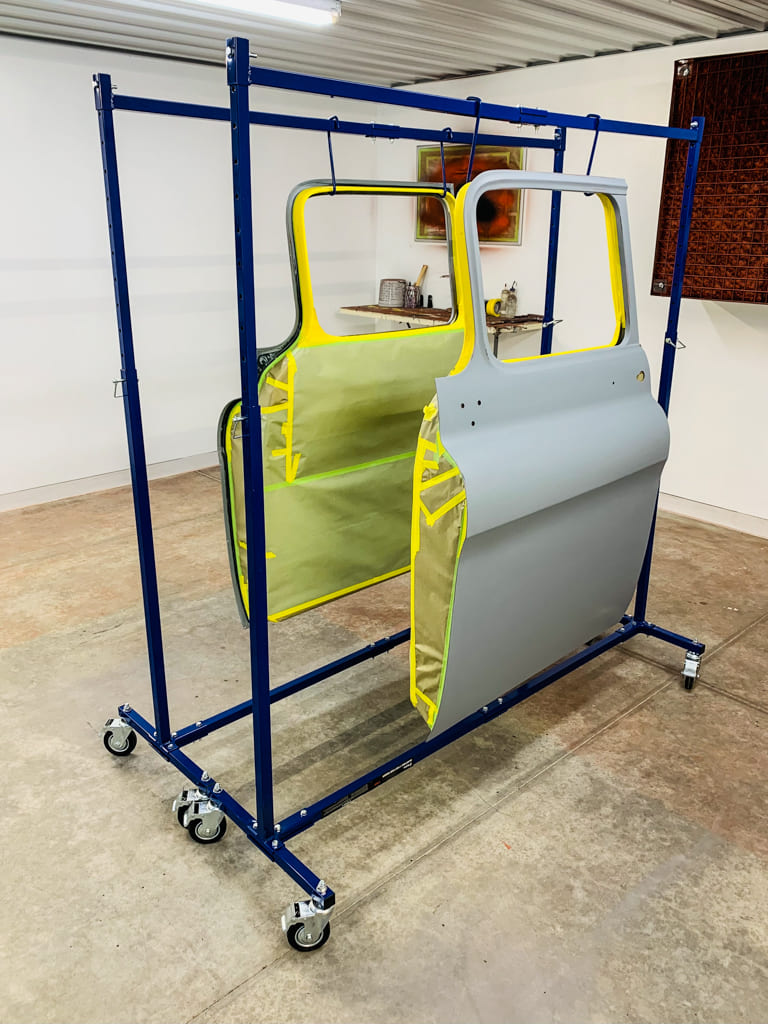
Sources:
Brothers Trucks/Holley
(800) 977-BROS
holley.com/brands/brothers_trucks/
Summit Racing Equipment
(800) 230-3030
summitracing.com
Click on this issue’s cover to see the enhanced digital version of In Uniform Fairness.