How To Replace a Rusty Floor Pan on this 1964 Pontiac LeMans
By Barry Kluczyk – Photography By the Author
Whether it came from the bone-dry desert or the heart of the Rust Belt, corrosion is the bane of every piece of vintage car. Even if it’s not immediately visible in the quarter-panels or rockers, there’s a good chance water found its way to the crevices deep inside the body, in the toeboard panels at the front of the floor, in the plenum area in the cowl, and, very likely, beneath the trunk mat, turning the floor into sheet metal Swiss cheese.
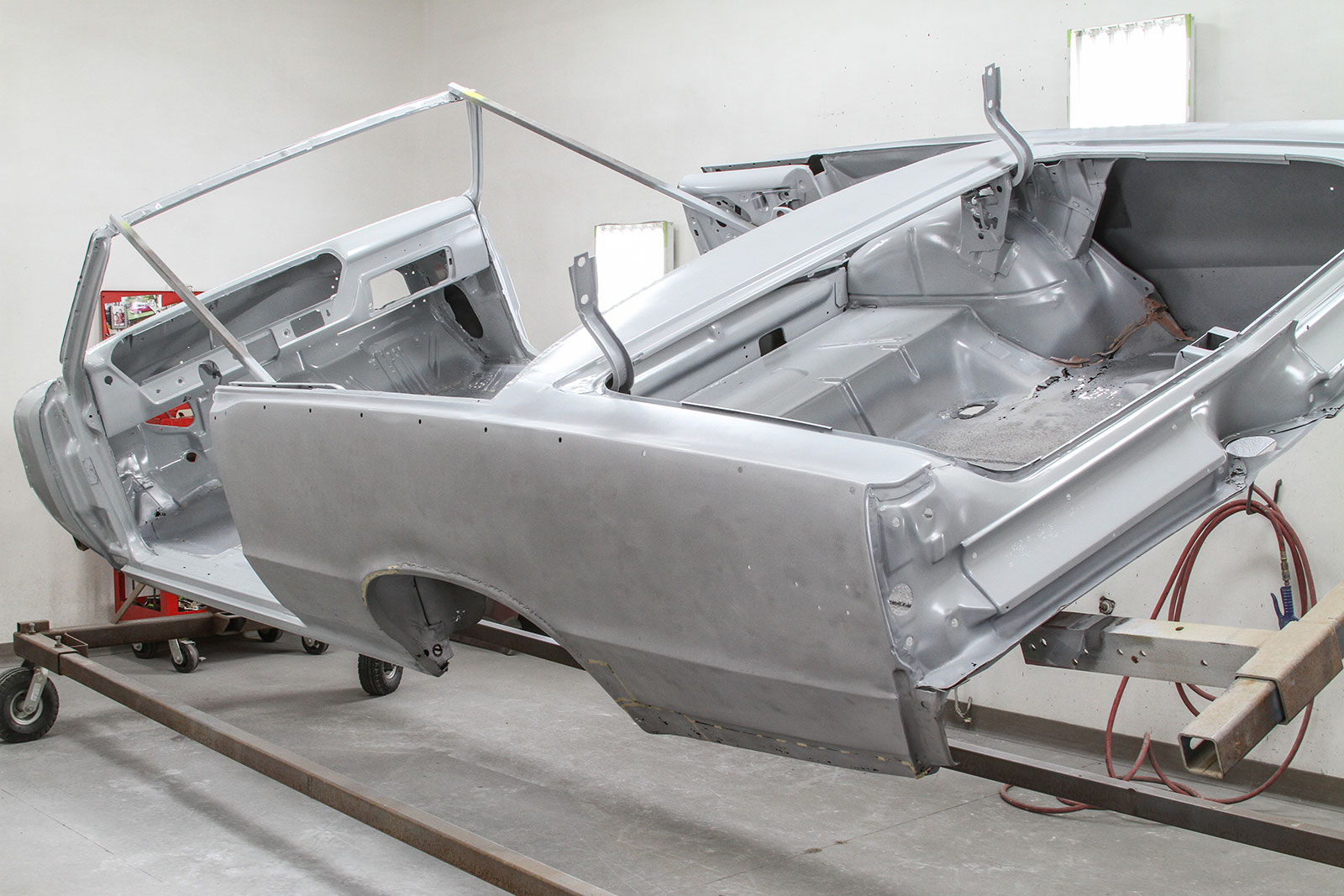
Sure, there are exceptions to the rule, and we’ve all been amazed to discover rot-free steel, but if you or your preferred resto shop is planning a thorough reconditioning of your favorite chunk of Detroit iron, a measure of rust repair will more than likely figure into the project.
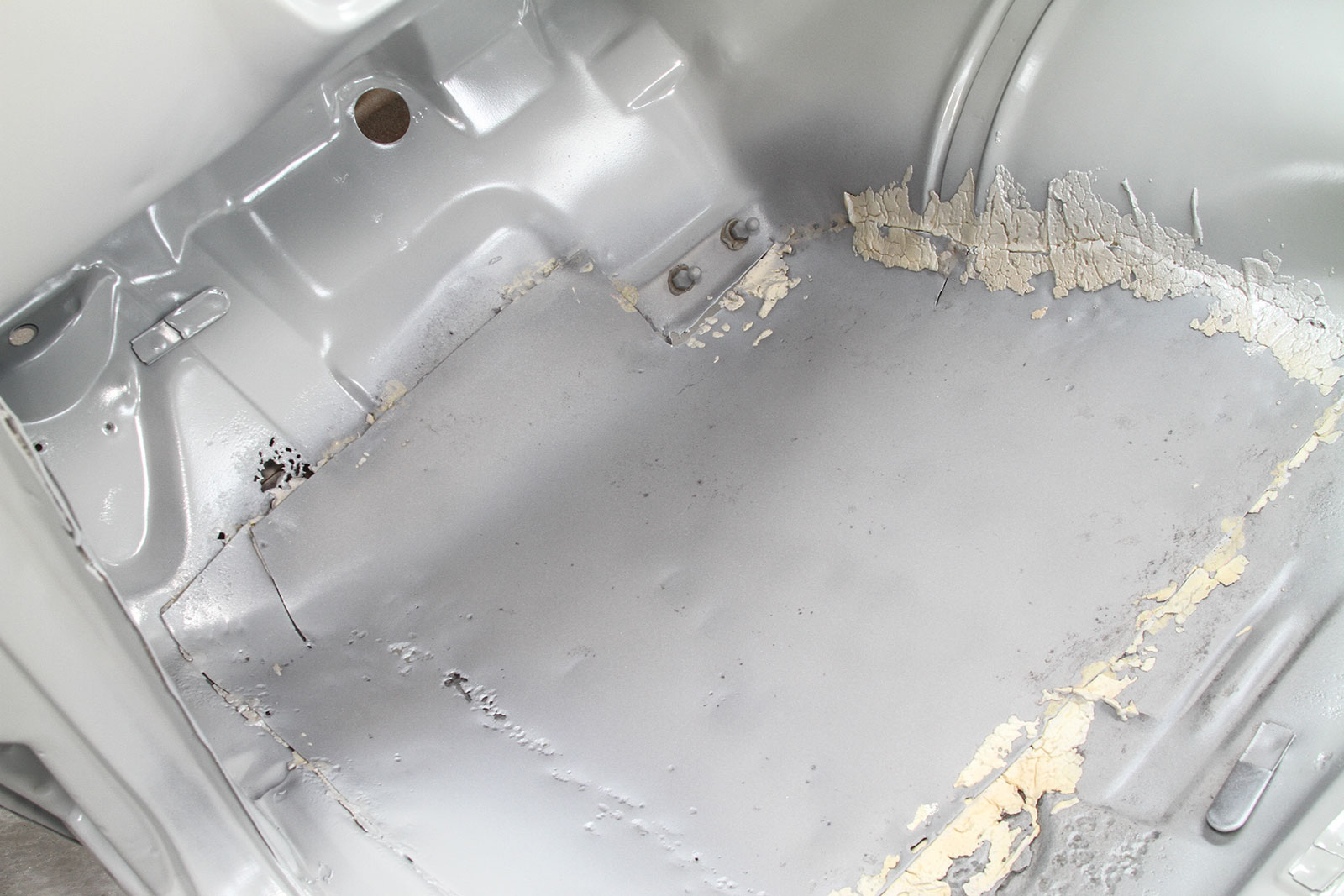
Read More: Timeless 1955 Ford Fairlane Victoria
There was no question the 1964 Pontiac LeMans convertible (GTO same floor pan) project car in our story would need a date with a sheet metal surgeon. A Midwesterner all its life, the A-body suffered from typical corrosion from stem to stern. Previous patches kept the car on the road longer but couldn’t stave off the inevitable.
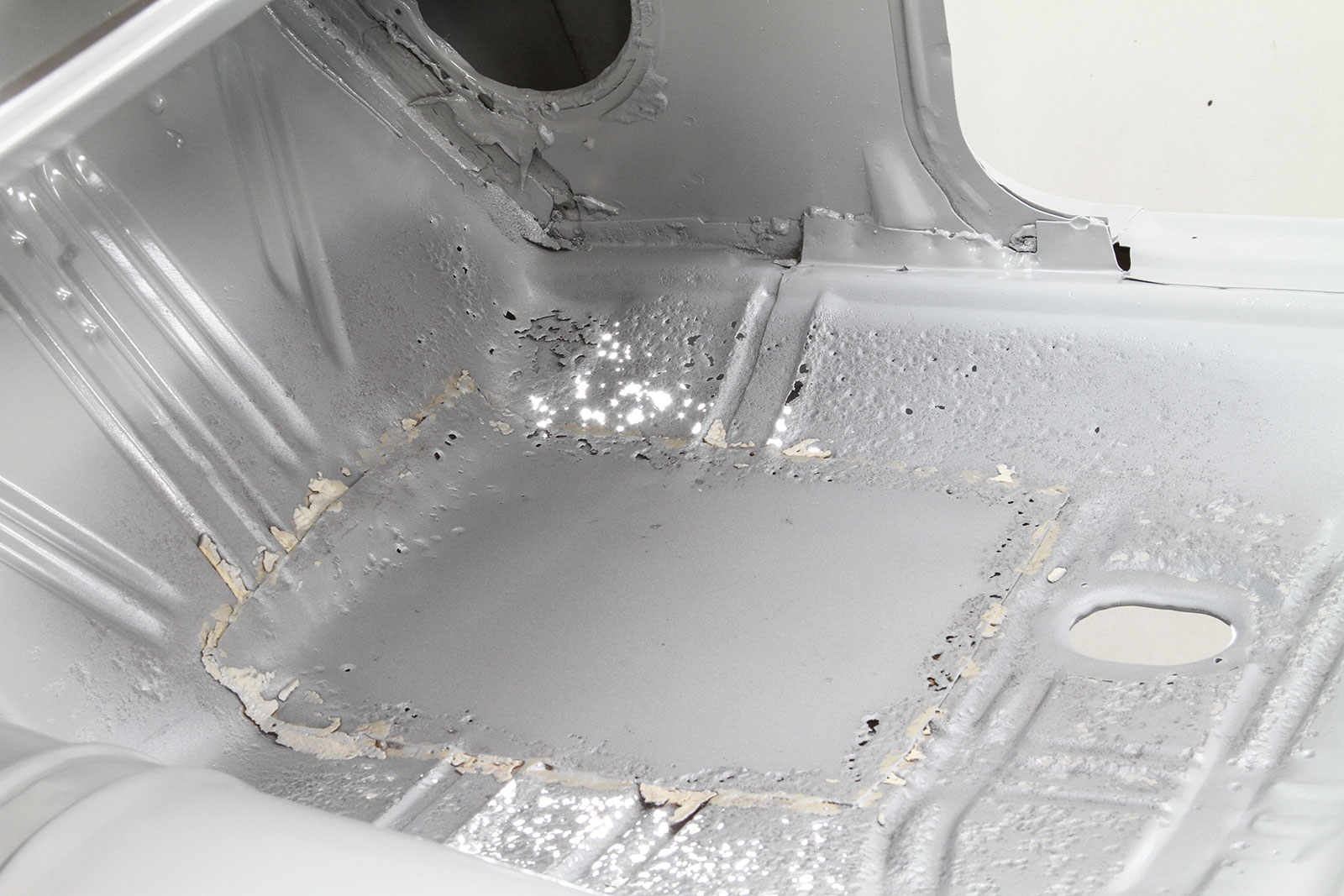
“You never know the full extent of the rust issue until you get the body stripped and media-blasted, but even before that we knew this one was going to need some serious attention,” says longtime and recently retired restorer Nyle Wing. “The car had been in the owner’s family for decades and he told us about some of the previous repairs, but even we were surprised to see rust holes literally from one end of the car to the other.”
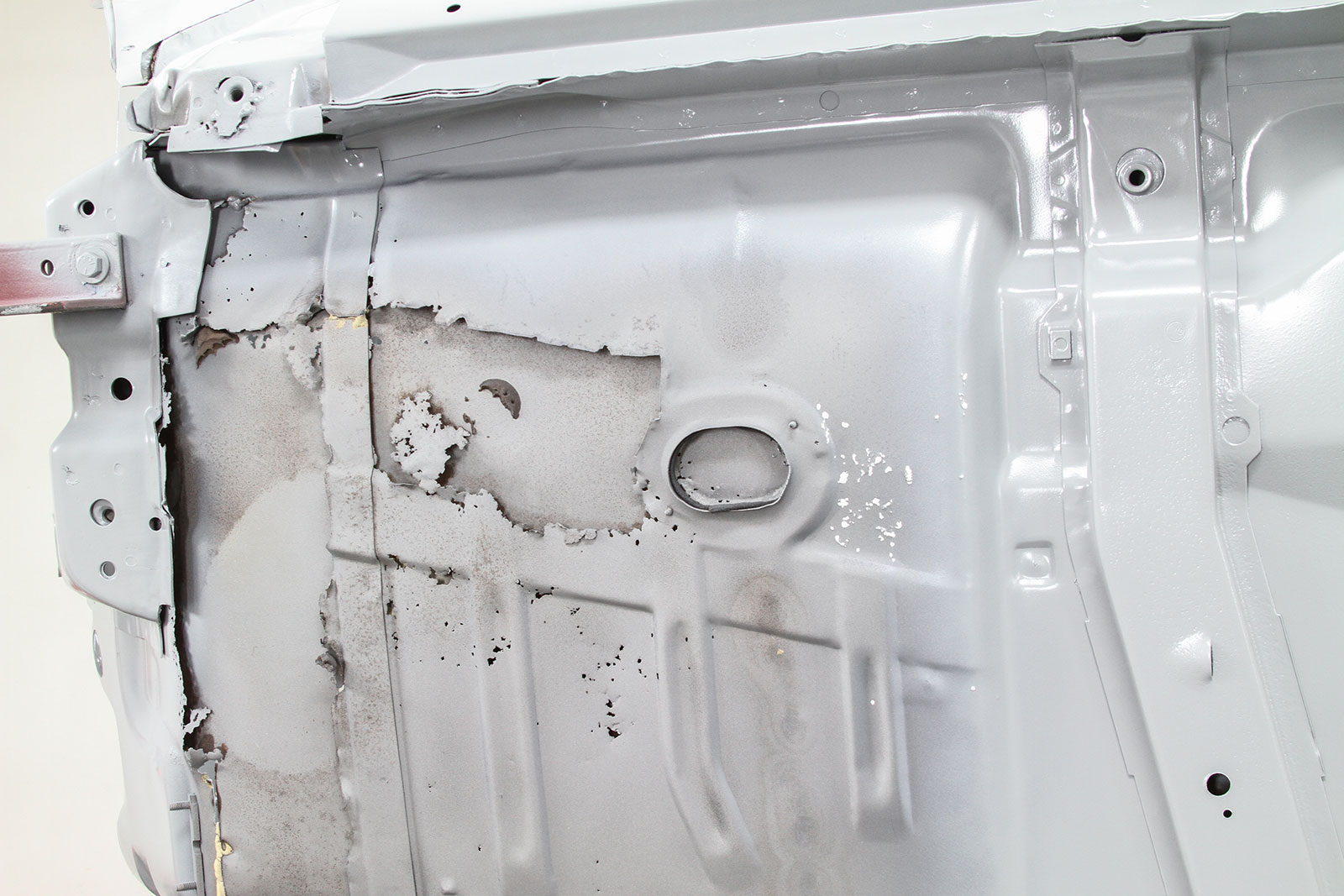
Read More: How To Retain Your Classic Car’s Original Frame
The extent of rot and patchwork throughout the Pontiac’s body was extensive and would ultimately take weeks of professional attention, but we caught up with the project to zero in on one of the more common repairs that DIY enthusiasts will attempt: floor pan replacement.
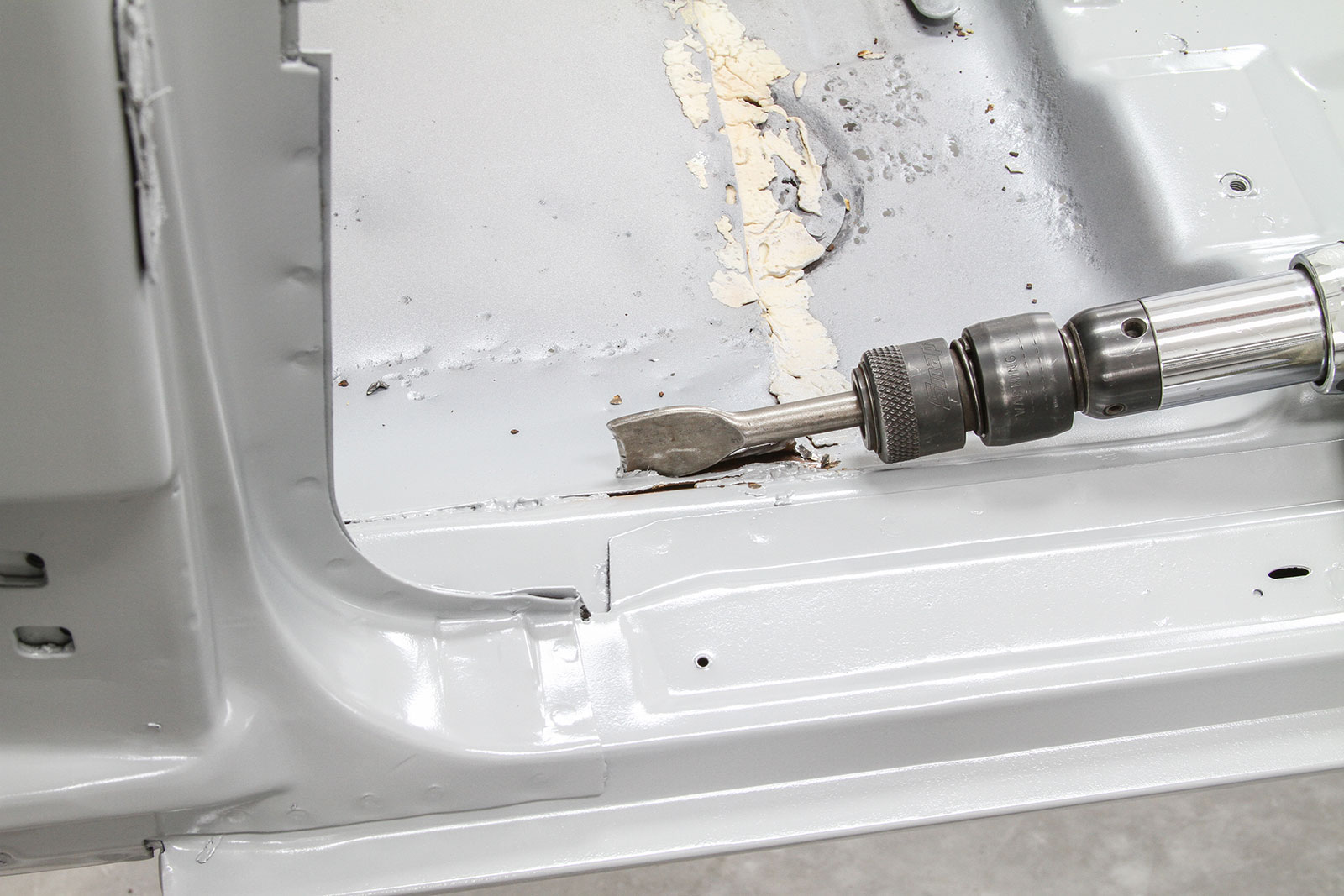
Floor Pan Replacement
It’s a project that must be performed accurately to ensure a strong, long-lasting repair. We followed along as the Pontiac’s cancerous steel was sliced out and the replacement metal grafted in with surgical precision. The project also demonstrated the more time-consuming butt-weld method rather than lap-welding, a technique that makes all the difference in a high-quality repair, especially when it comes to a show-quality final finish.
“The butt weld is the way to go for a strong, factory-type repair,” Wing says. “It takes a little more time, patience, and experience, but the end result is worth it.”
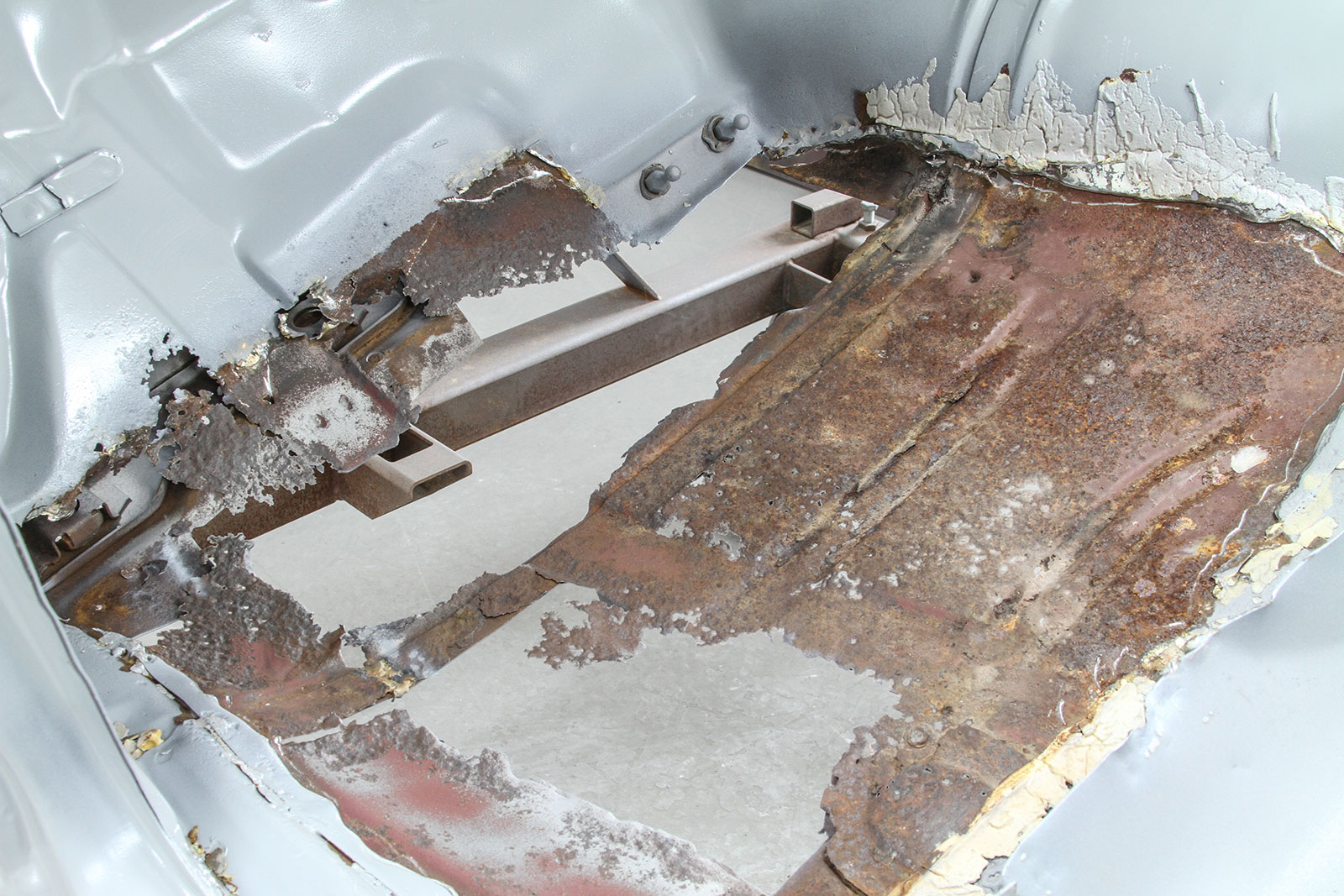
DIY Auto Rust Repair
It also begs an important question: Is a floor pan replacement a DIY project? Well, the welding isn’t particularly complicated, even for those with only moderate experience, but the job requires additional tools that might not be in everyone’s toolbox, including a spot weld cutter for a drill, long body panel vise clamps, and a body hammer. An air hammer or plasma cutter speeds things along, too, as seen in our story.
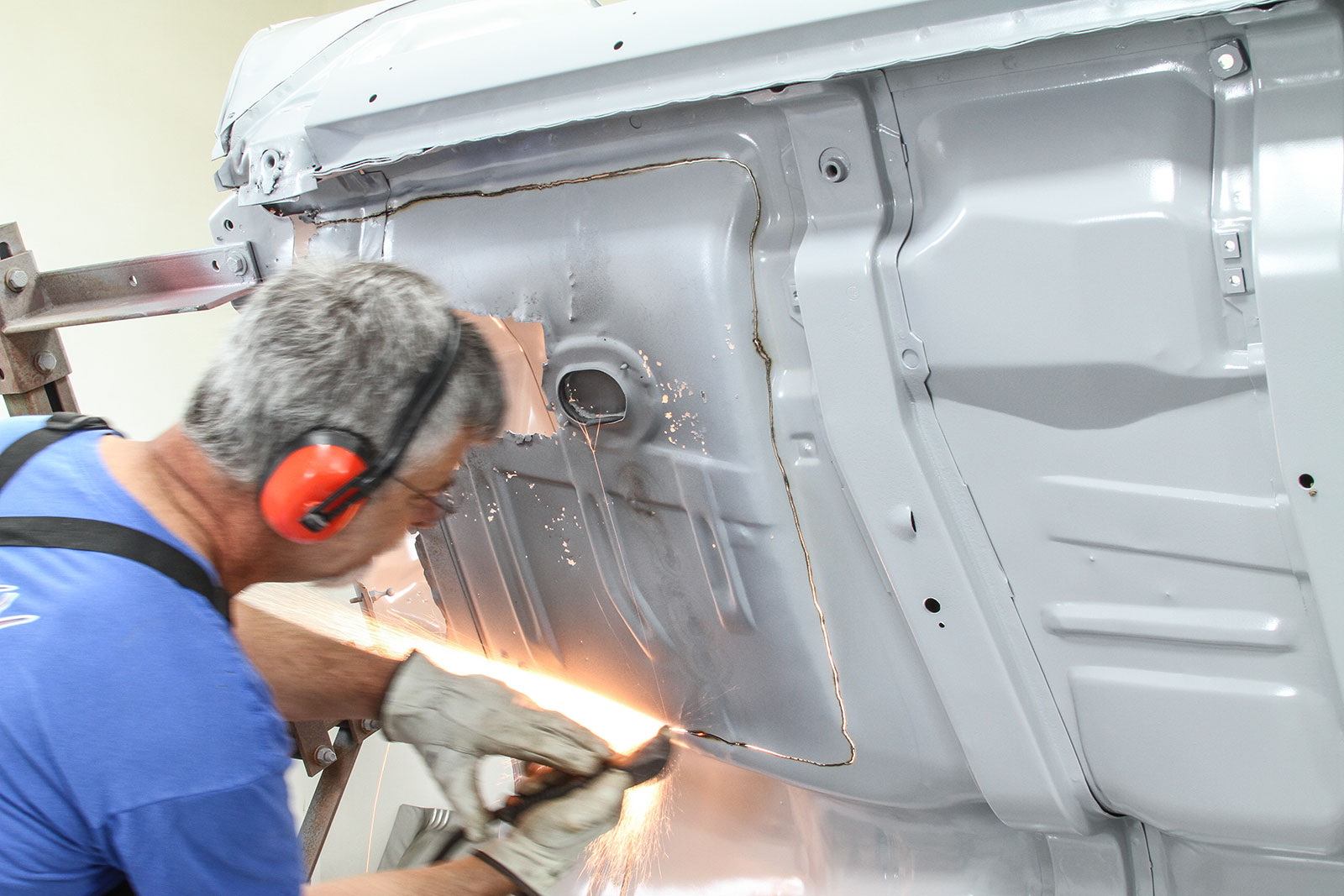
Read More: Myers’ Fenderless 1936 Ford Roadster
So, yes, it’s a project that could be tackled at home, but the chance for warping the comparatively thin sheet metal used in floor pans is high, particularly with butt-welding. With a professional repair, the bulk of the cost will be in the labor hours, as the cost of the replacement metal is comparatively inexpensive.
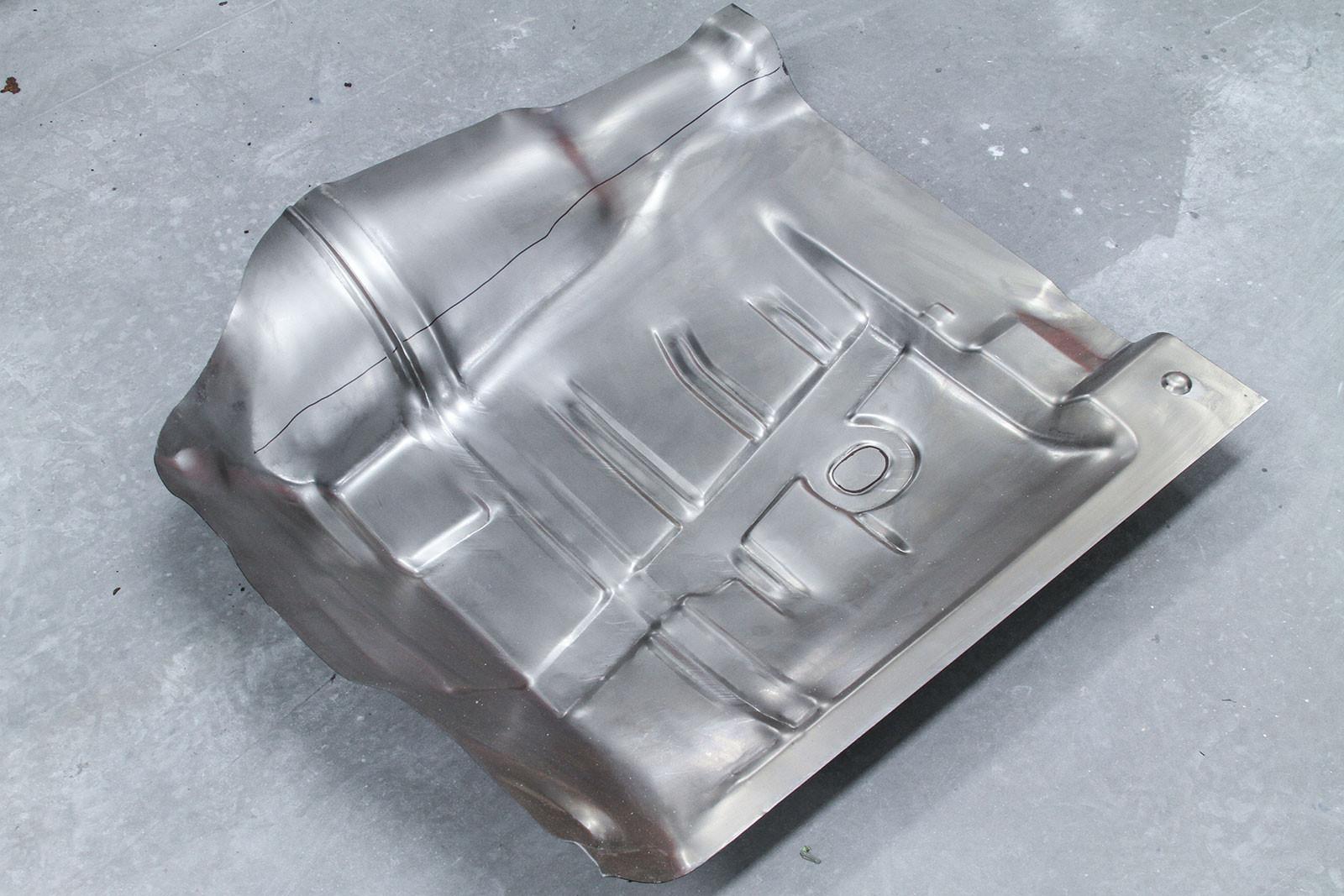
Patch Panel Procurement
For the project illustrated in our story, only a front floor patch panel was used, which can typically be found for less than $100 for GM A-bodies. In fact, we found the panel for only $84.95 at Golden Star Classic Auto Parts. Of course, this Pontiac project would go on to include several additional sheet metal parts, but as we mentioned, we’re focused only on the floorboard in this story.
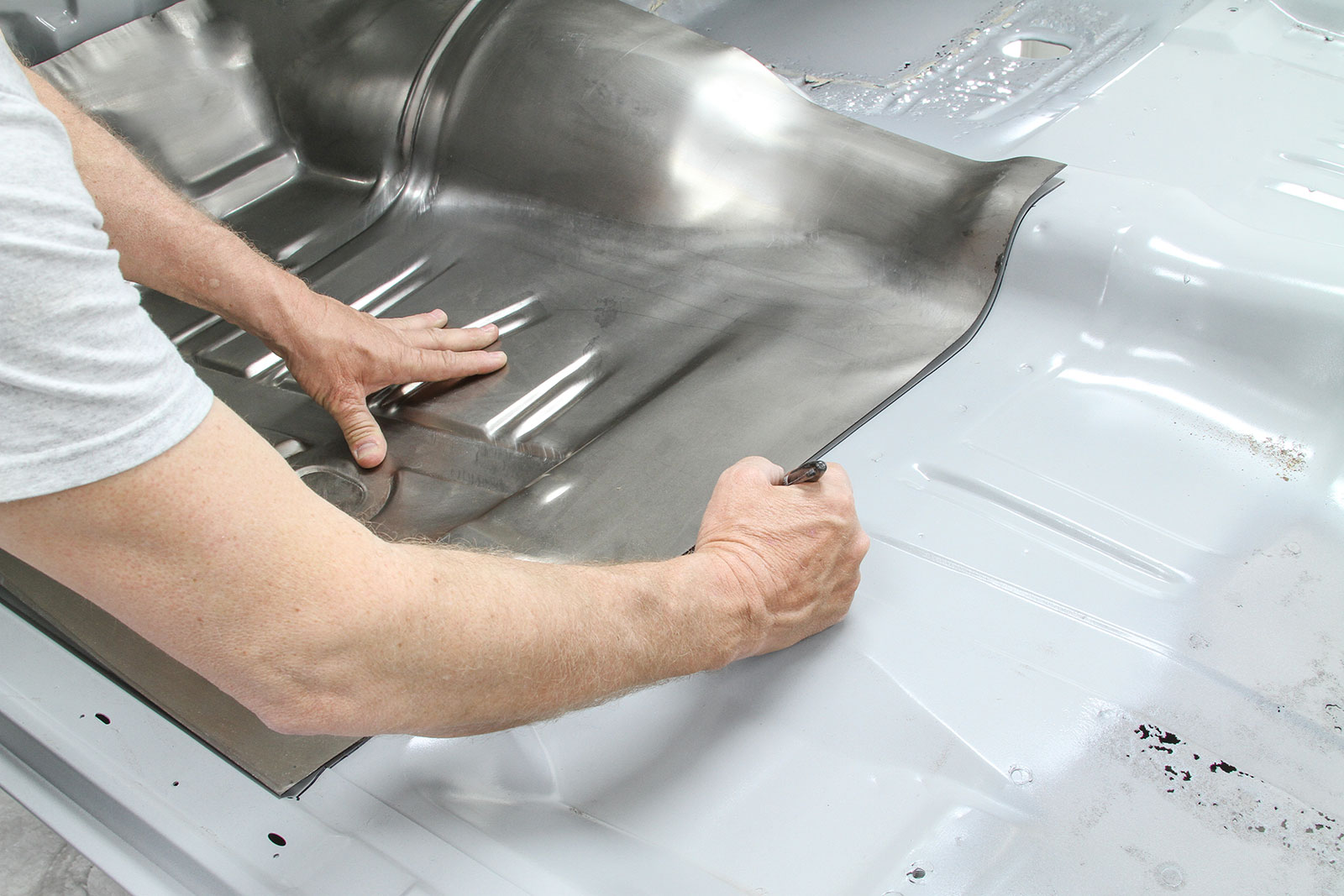
No matter which path you choose, DIY or a professional repair, the bottom line is you can’t ignore your project car’s corrosion indefinitely.
Rust, as they say, never sleeps. MR
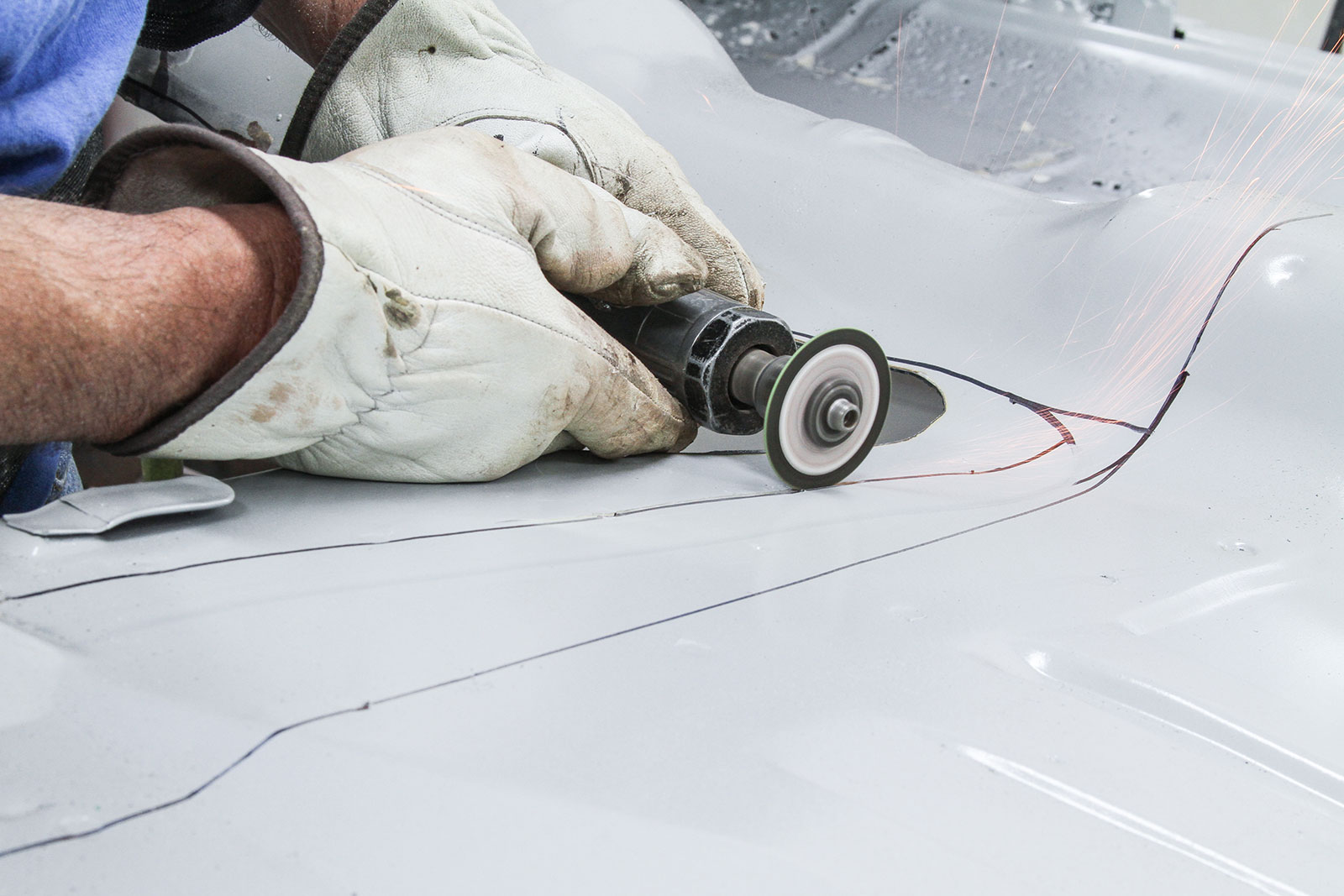

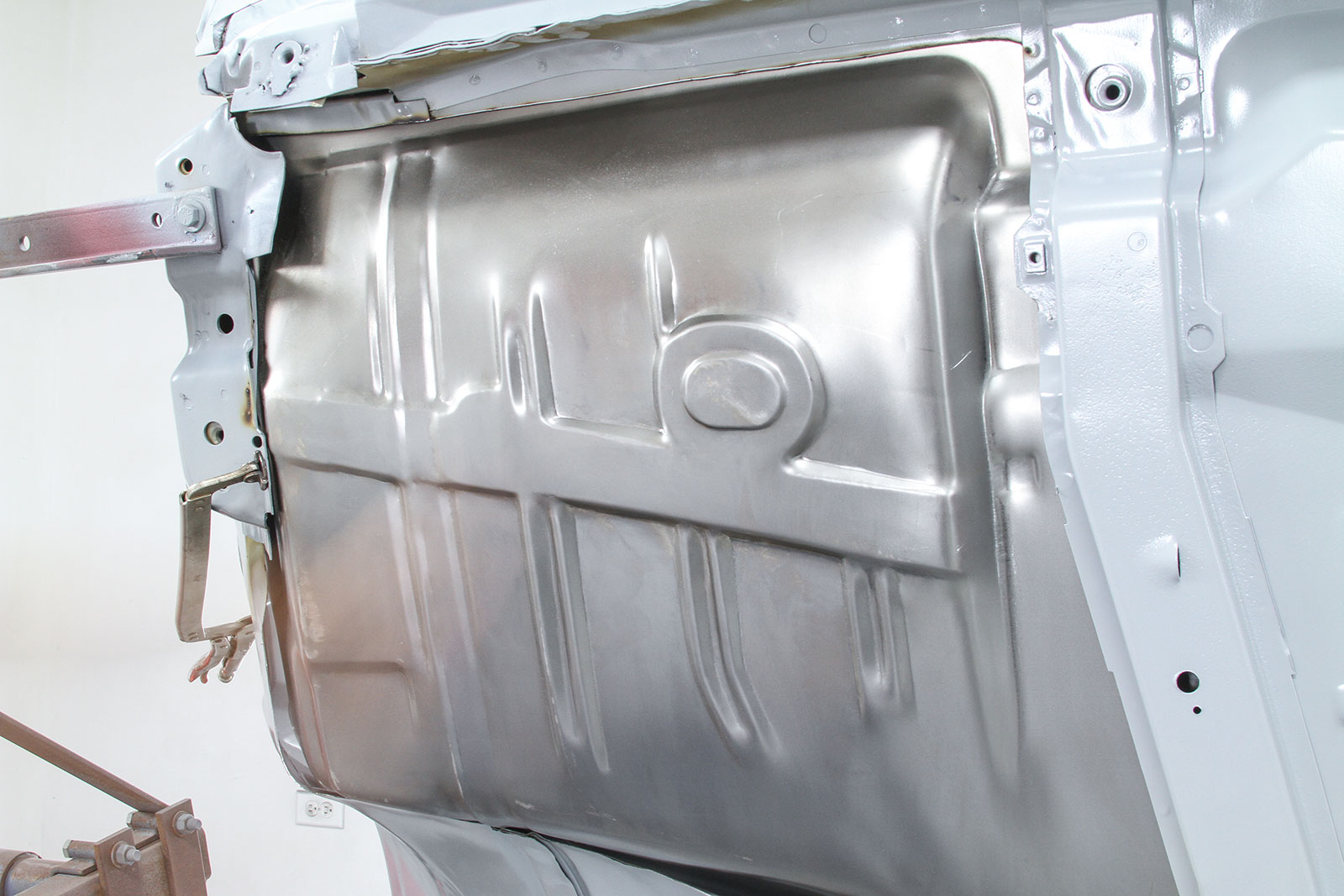
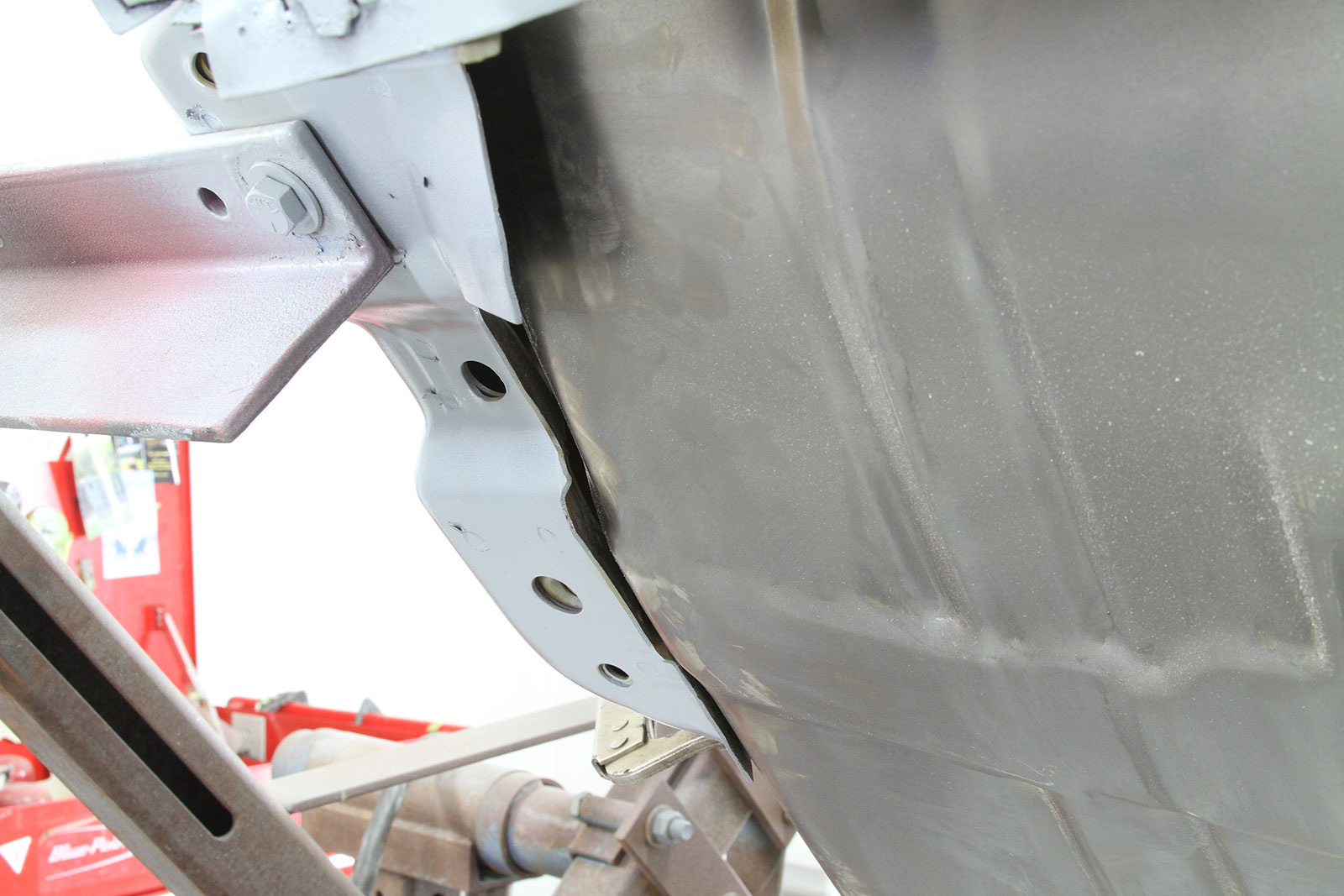
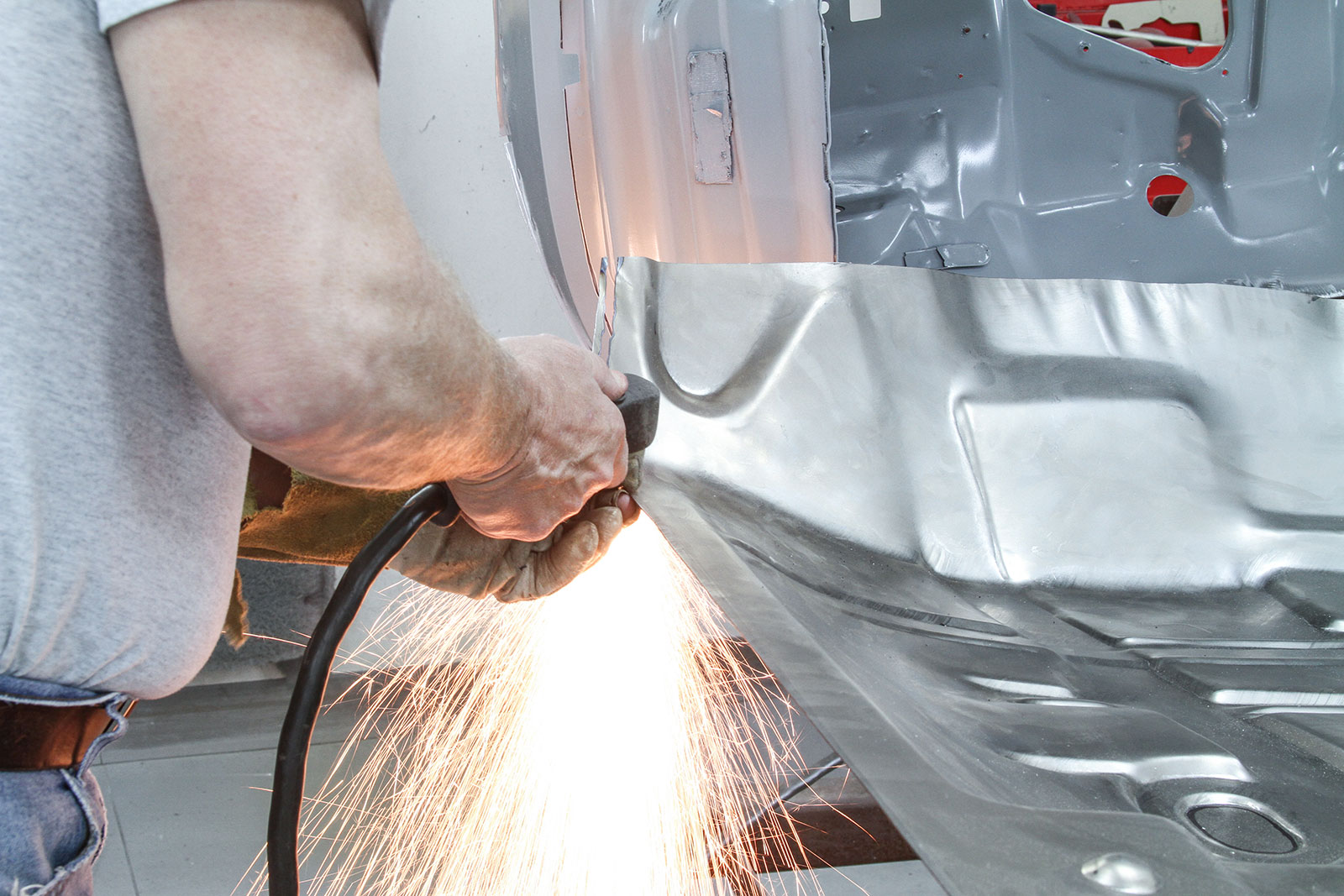
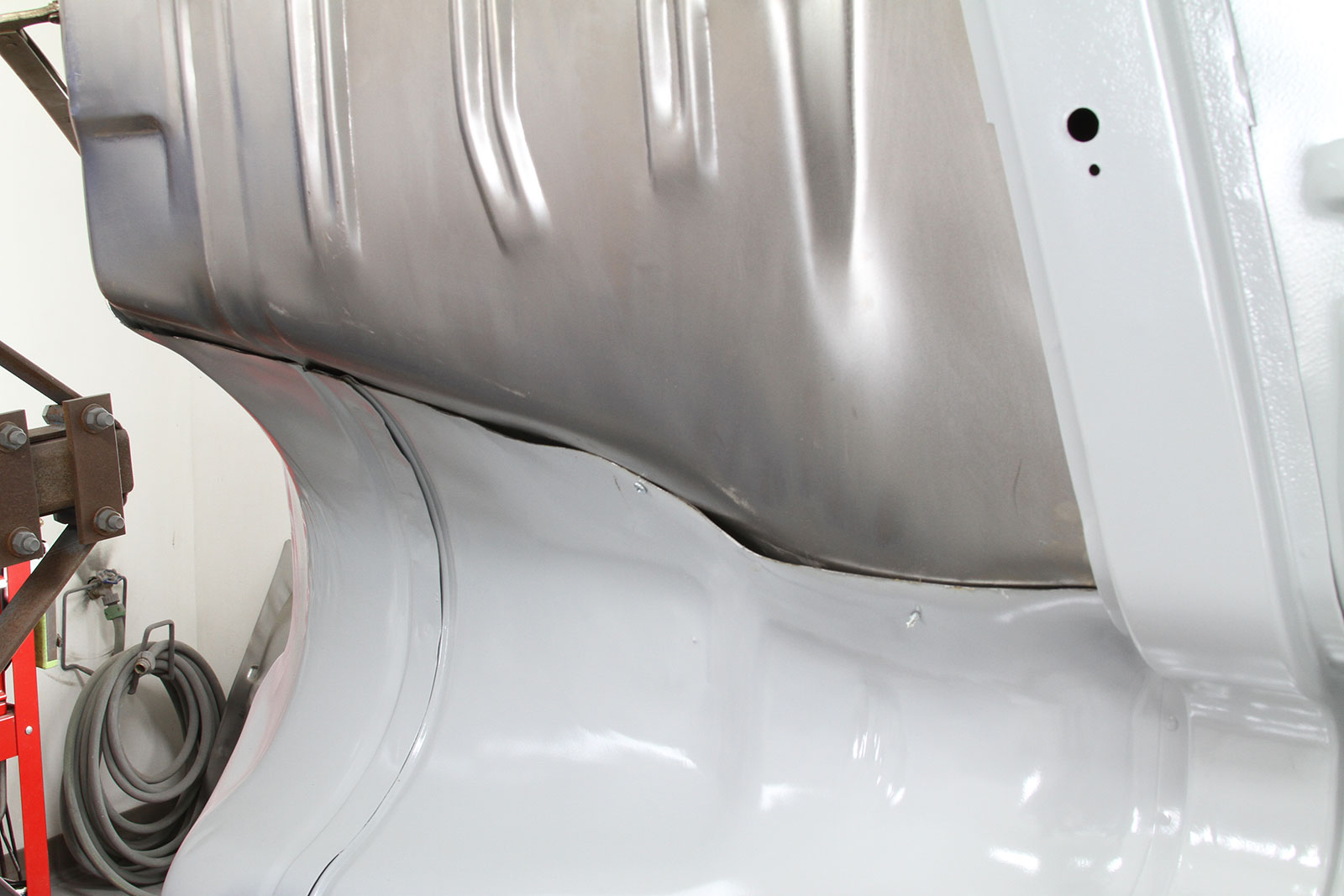
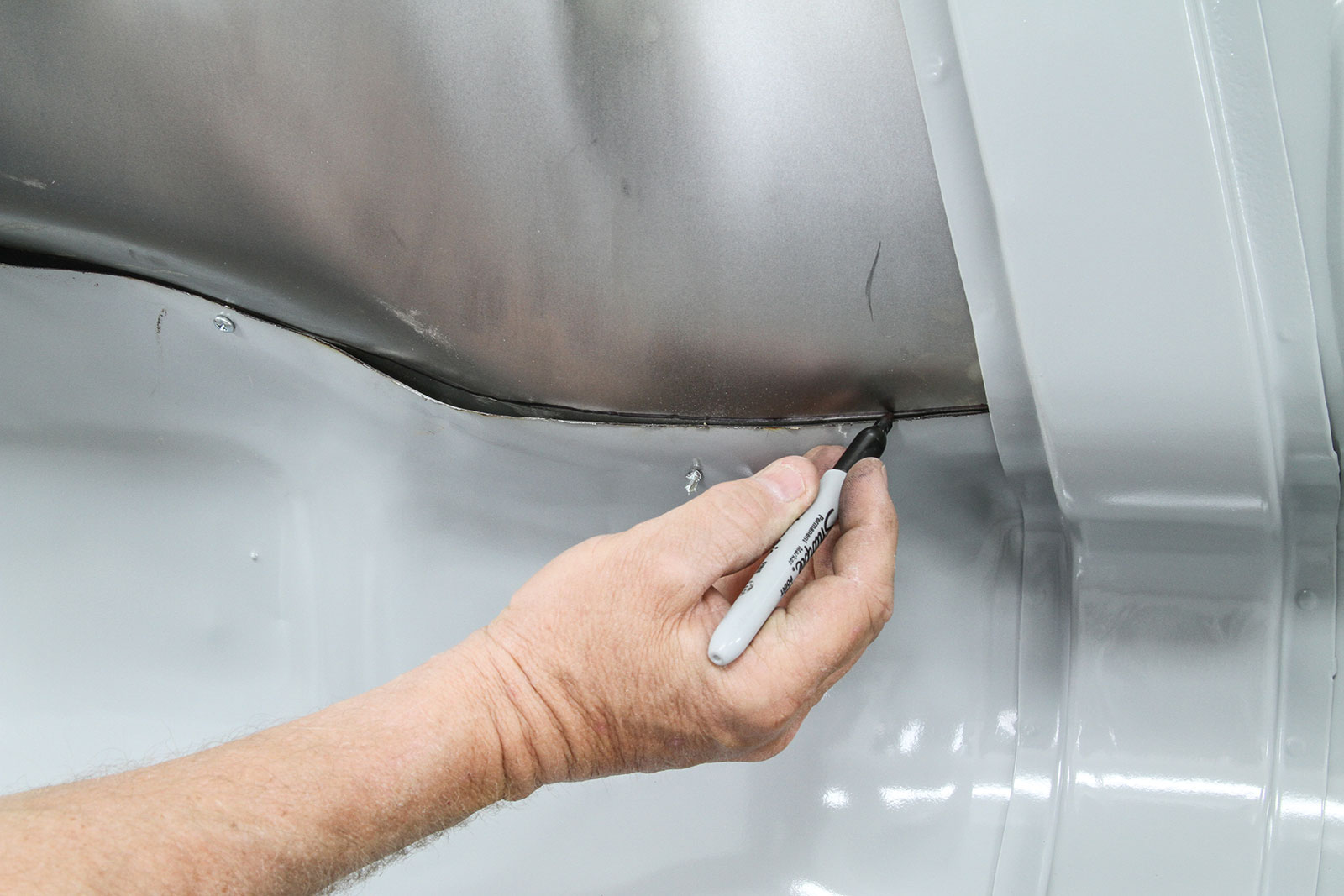
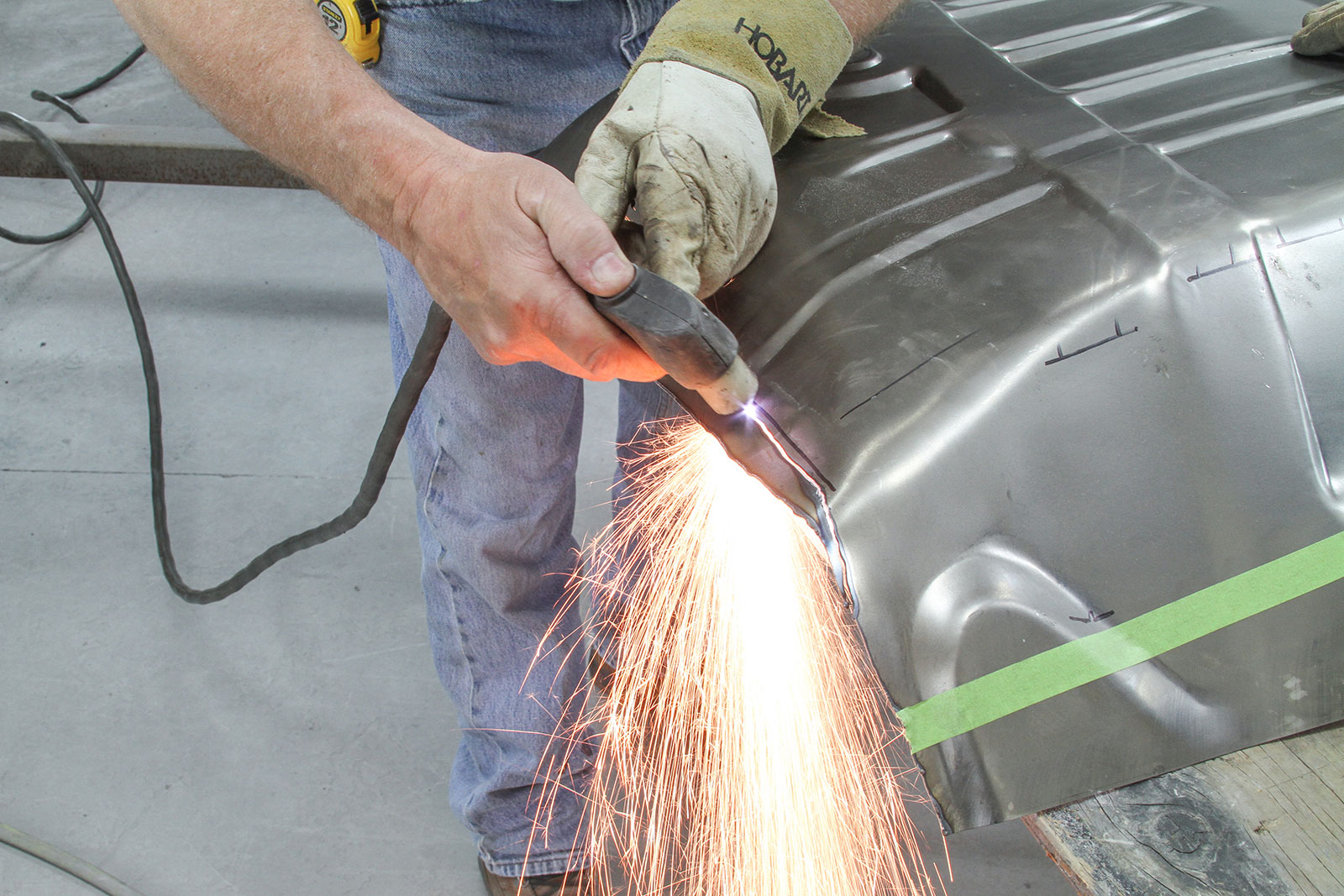
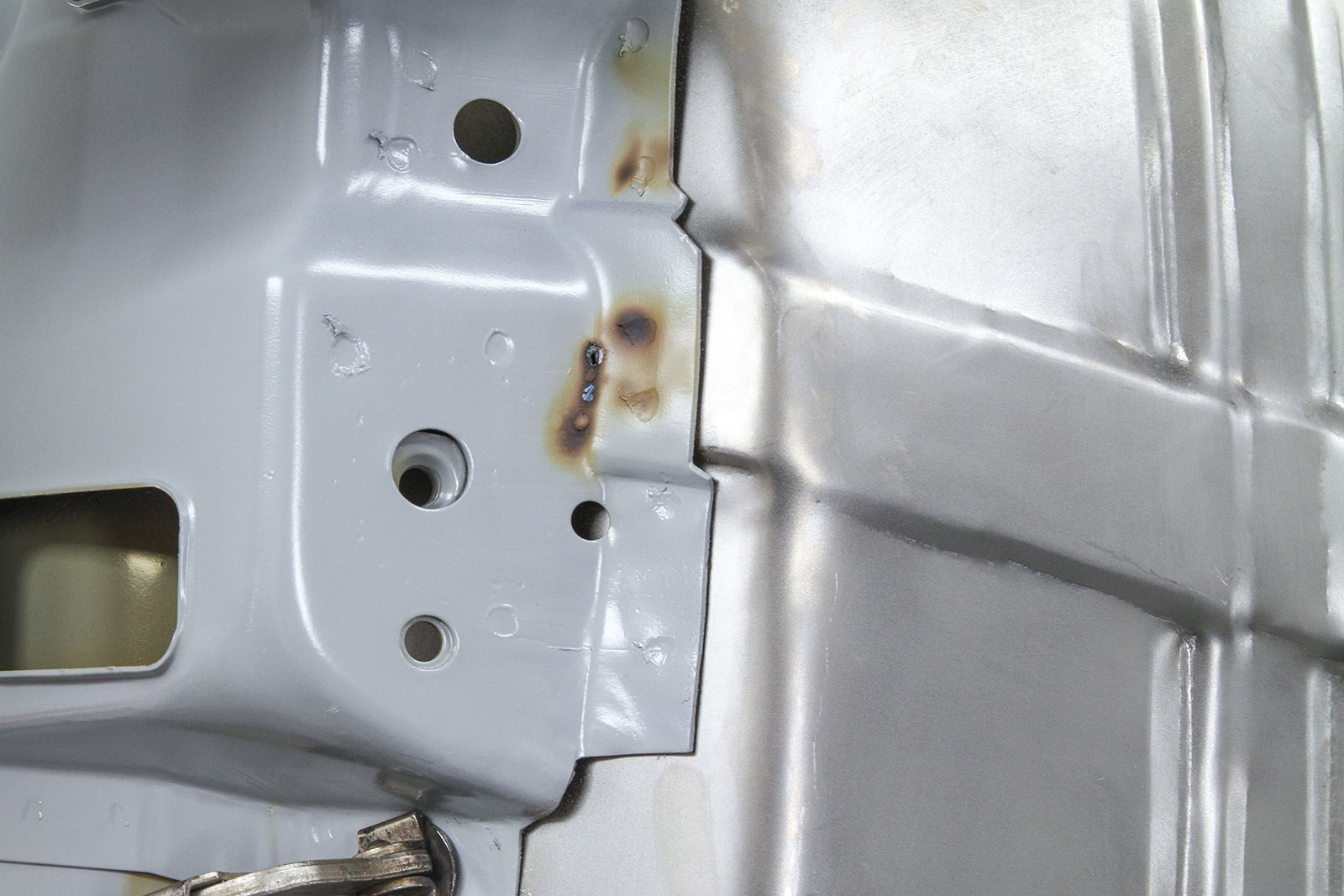
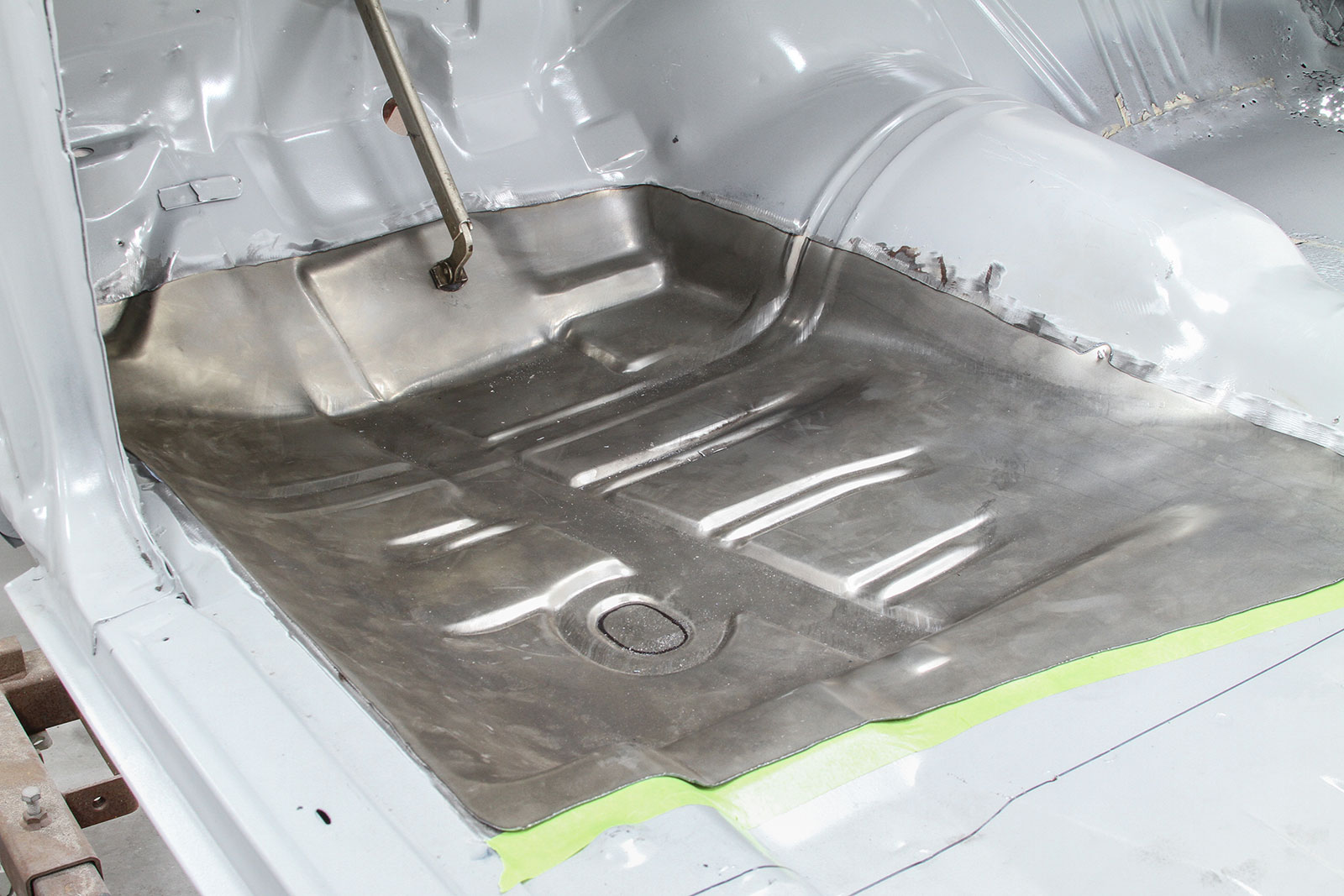
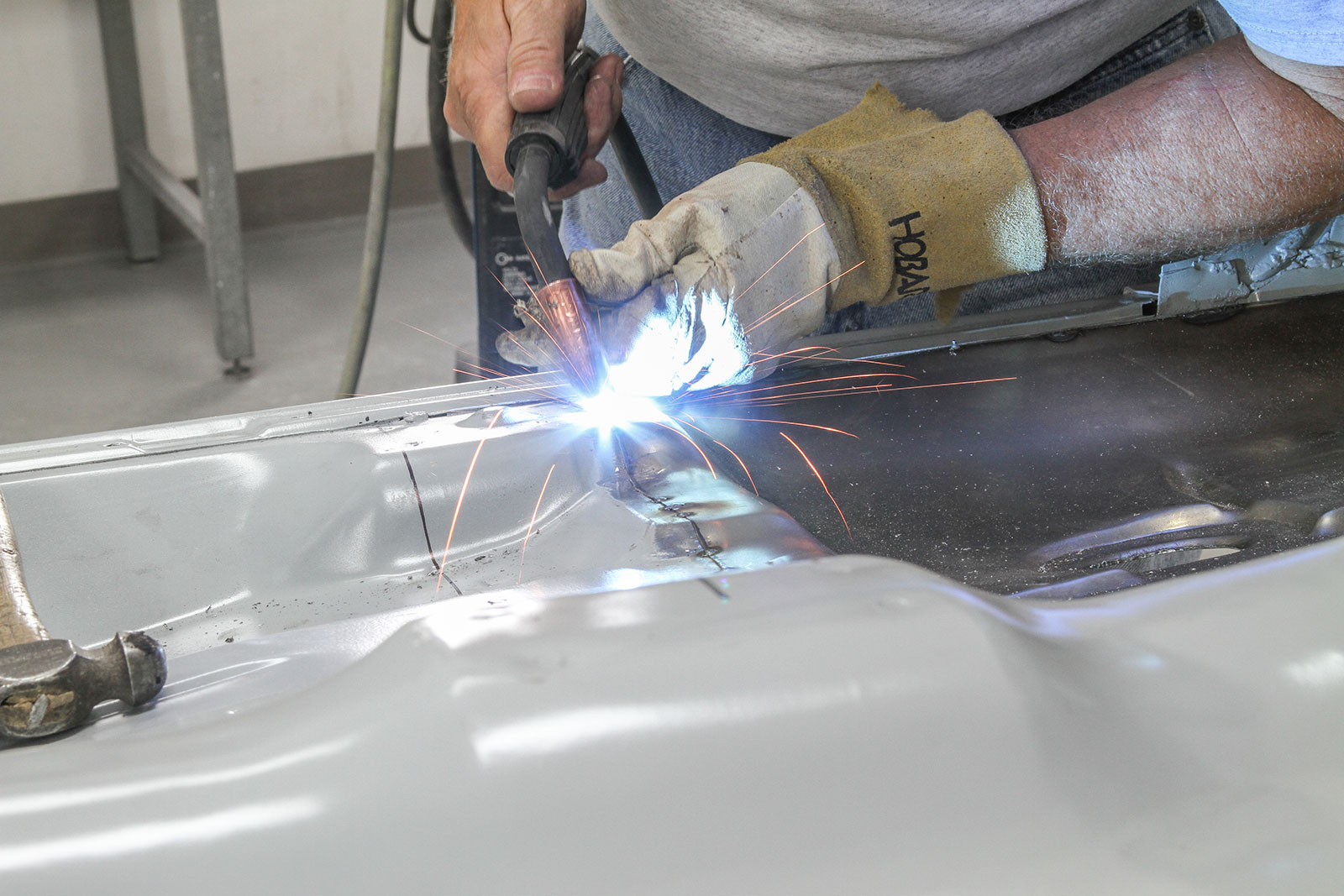
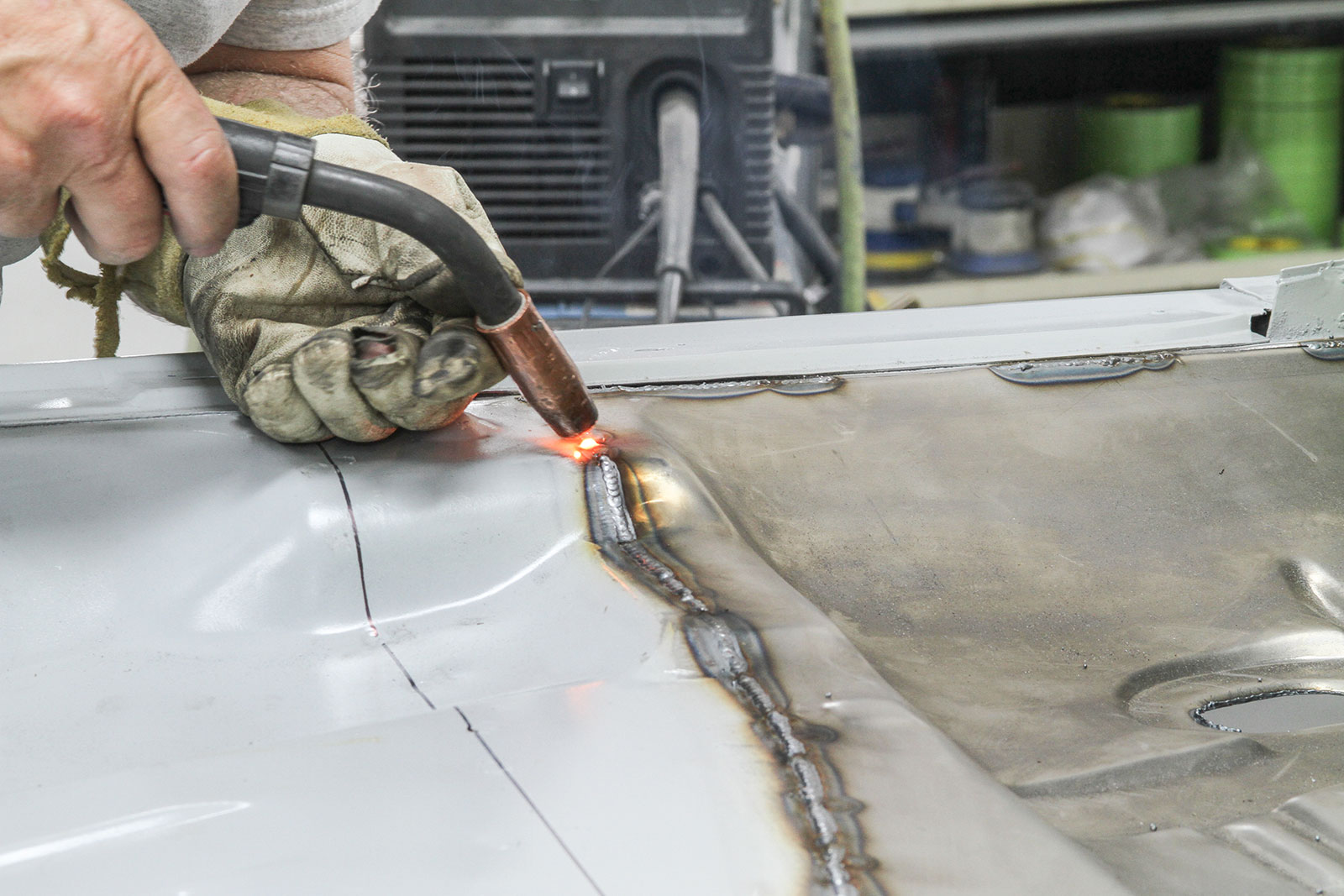
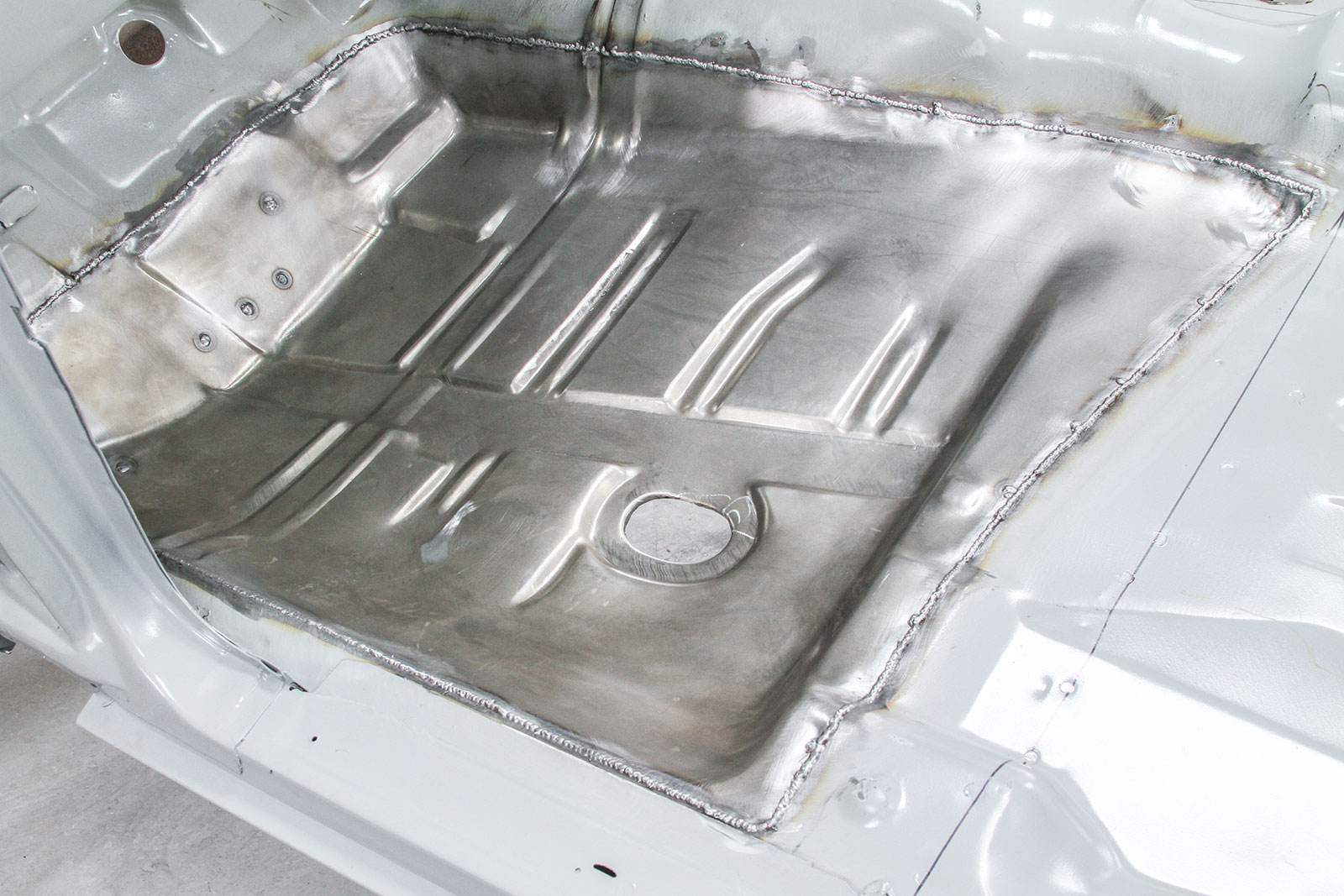
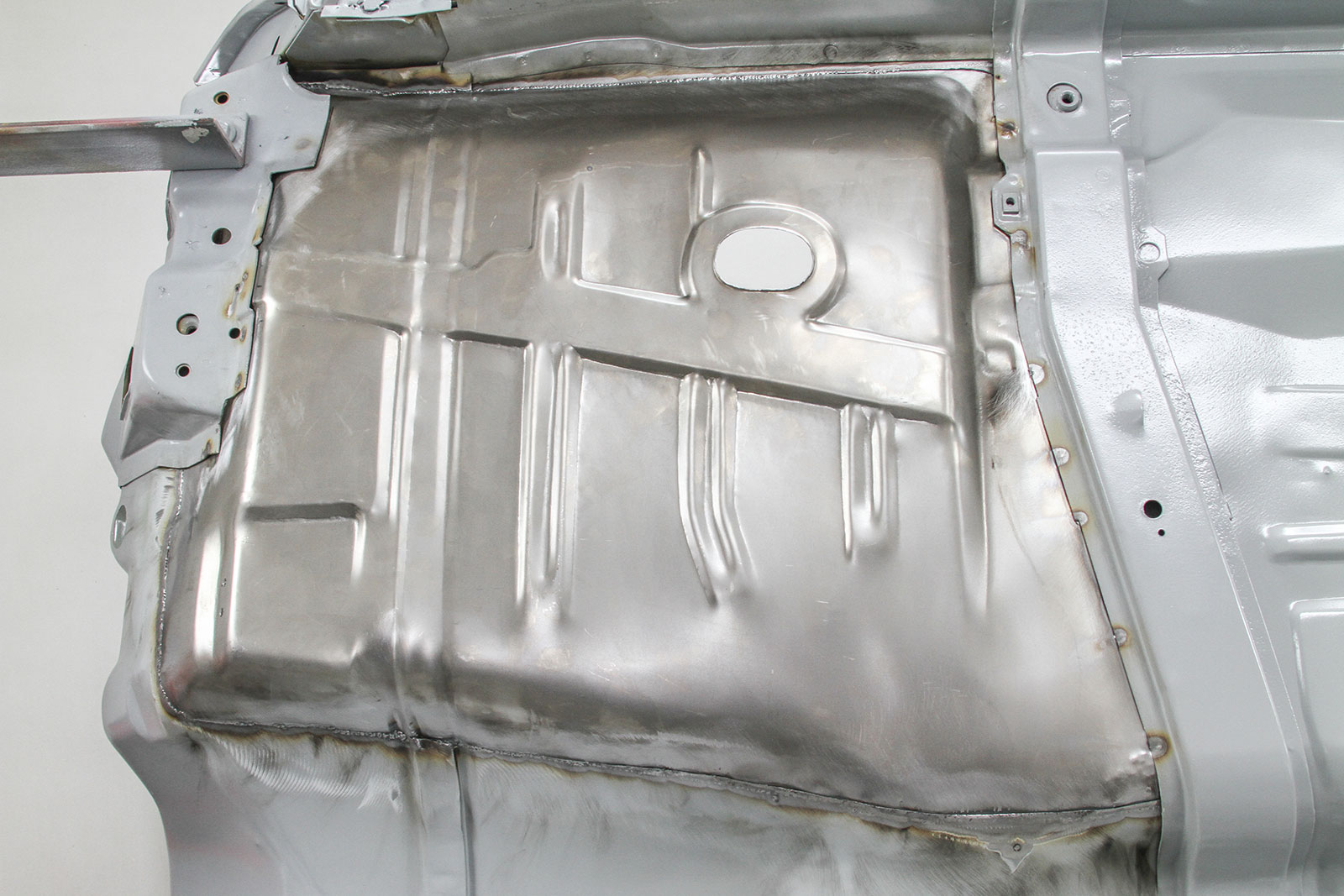
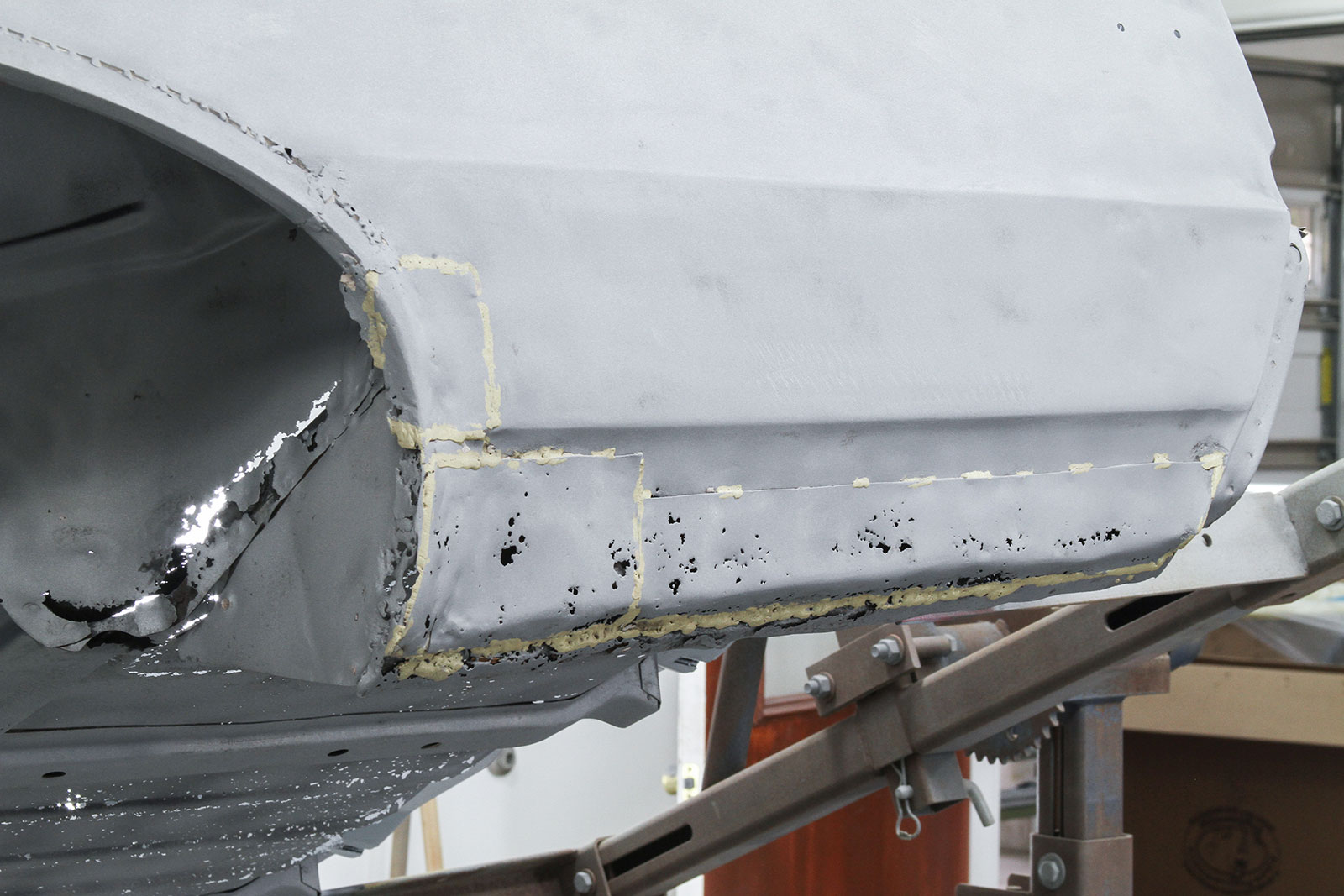
Welding is as much an artform as it is a skill; no matter how you approach, practice and experience are the only ways to become proficient at it. Not surprisingly, many enthusiasts are reluctant to make the investment in a welder for fear that their trepidation in learning the skill will relegate the unused machine to the corner of the garage, like a 220-amp treadmill.
There isn’t a single welding process to cover every task, but certain types are more likely to be encountered in the types of projects associated with working on cars. Here’s a quick rundown
Stick Welding
It’s the most basic of welding types and is typically what many people use as their first foray into welding. Also known as arc welding, it simply used an electric current flowing from a gap between the metal and the welding stick. It’s good for basic work, like welding a hitch receiver to the bumper frame of your truck but tends to throw off a lot of spatter and can’t be used with anything thinner than 18-gauge sheetmetal.
MIG Welding
MIG stands for metal inert gas and the process involves a wire-welding electrode on a spool. An arc created by the electrical current between the metal and the wire melts the wire to join the metals. It’s a relatively easy process to learn, although it takes experience to learn optimal temperatures and stitching procedures. It’s also a clean process, with little or no spatter, and it can be used on thin or thick metals.
TIG Welding
TIG stands for tungsten inert gas and is an arc welding process that uses a tungsten electrode to produce the weld. The tungsten does not create the filler, like the wire in MIG welding and with some processes, one isn’t needed. TIG welding is generally the best for joining thin sections of metal and non-ferrous materials, such as aluminum and magnesium. It is more complex than MIG welding and more difficult to master.
Bottom line
A MIG welder will handle just about all the automotive hobby projects you’ll encounter. It’s the just-right tool between a basic stick welder and the more-complex TIG welder.
New Striker Door Shims for Mopars
When it comes to reversing the rust on a muscle car–era Mopar, most enthusiasts are stuck with the often-corroded original striker door shims or take-offs from a parts car—and that’s only if better ones can be found.
It’s a compromise that can be avoided with JF Restoration Parts’ new laser-cut shims. Like the factory shims, they install behind the striker on the door post to optimize the door latch catch and door alignment. The shims come in a kit with four sizes that match the thickness of the originals: 0.032, 0.048, 0.060, and 0.077 inch and each kit includes two of each, which is enough for a two-door car.
The shim kit is available on eBay, under item number 222204828682, or by searching “jfshims;” or call (204) 822-0745 for more information.
Source:
Golden Star Classic Auto Parts
(972) 315-3758
goldenstarauto.com
Click on this issue’s cover to see the enhanced digital version of Sheetmetal Surgery.