By Ron Ceridono – Photography by Taylor Kempkes
When a diehard 1962 Chevy fan wanted someone to build an Impala convertible unlike anything seen before, Old Anvil Speed Shop got the call. The task was to build a car that could drop to the ground one minute and carve corners the next, house 21- and 24-inch wheels, and handle 1,200 hp. Obviously the first step in this process was going to be building a one-of-a-kind chassis.
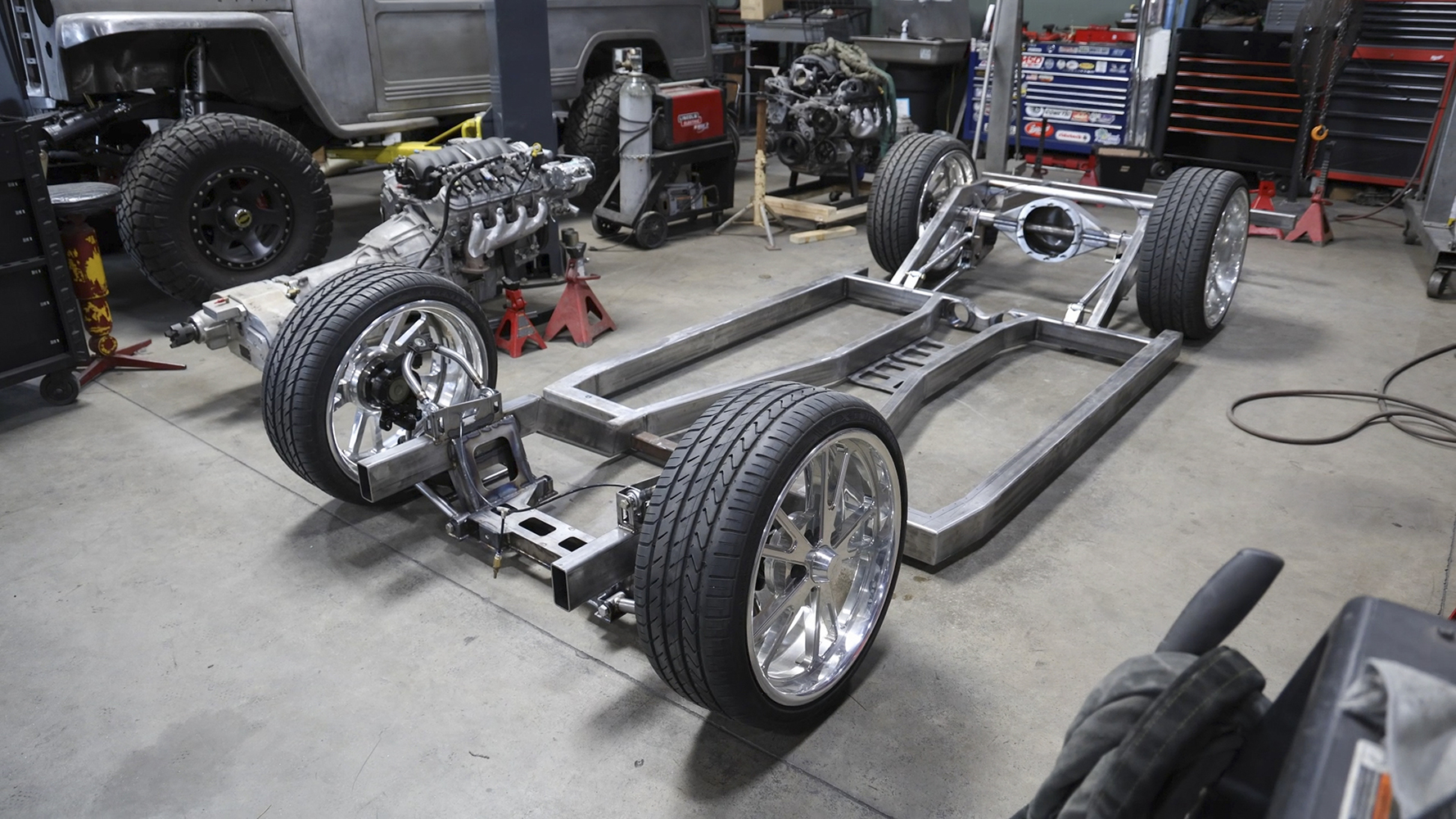
Paul and Jenna Bosserman started Old Anvil Speed Shop in Orange, California, in 2018, specializing in chassis engineering, fabrication, and sheetmetal work. Today, they manufacture their own CNC machined billet parts and custom wheels, and with their focus on complete custom builds, they’ve added facilities for bodywork, paint, and upholstery.
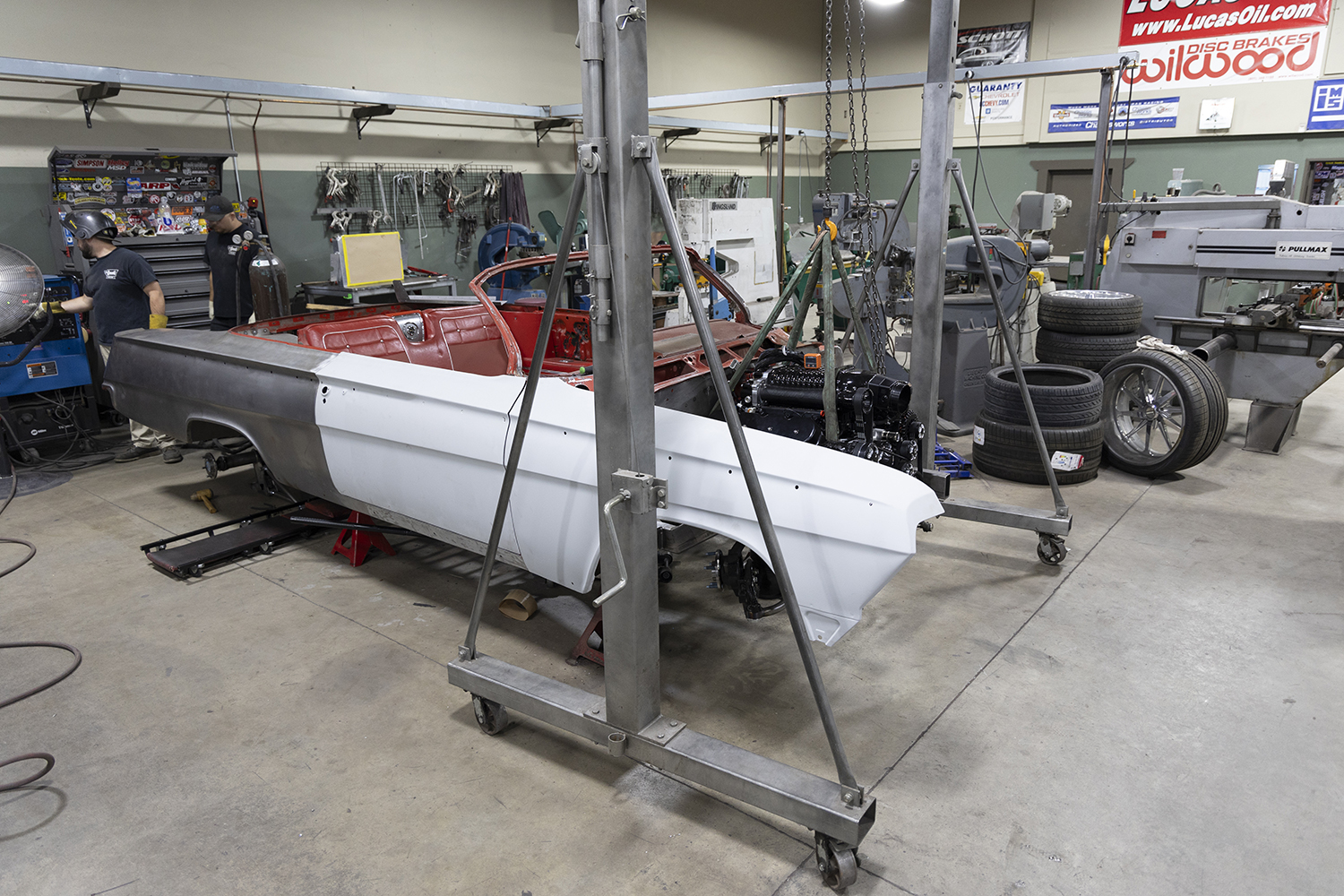
One of Old Anvil’s recent builds is based on a very original 1962 Impala SS convertible that had traveled a mere 42,000 miles in its lifetime. To meet the customer’s vision for the ragtop, it would have to be built from the bottom up, which meant an entirely new frame would be required.
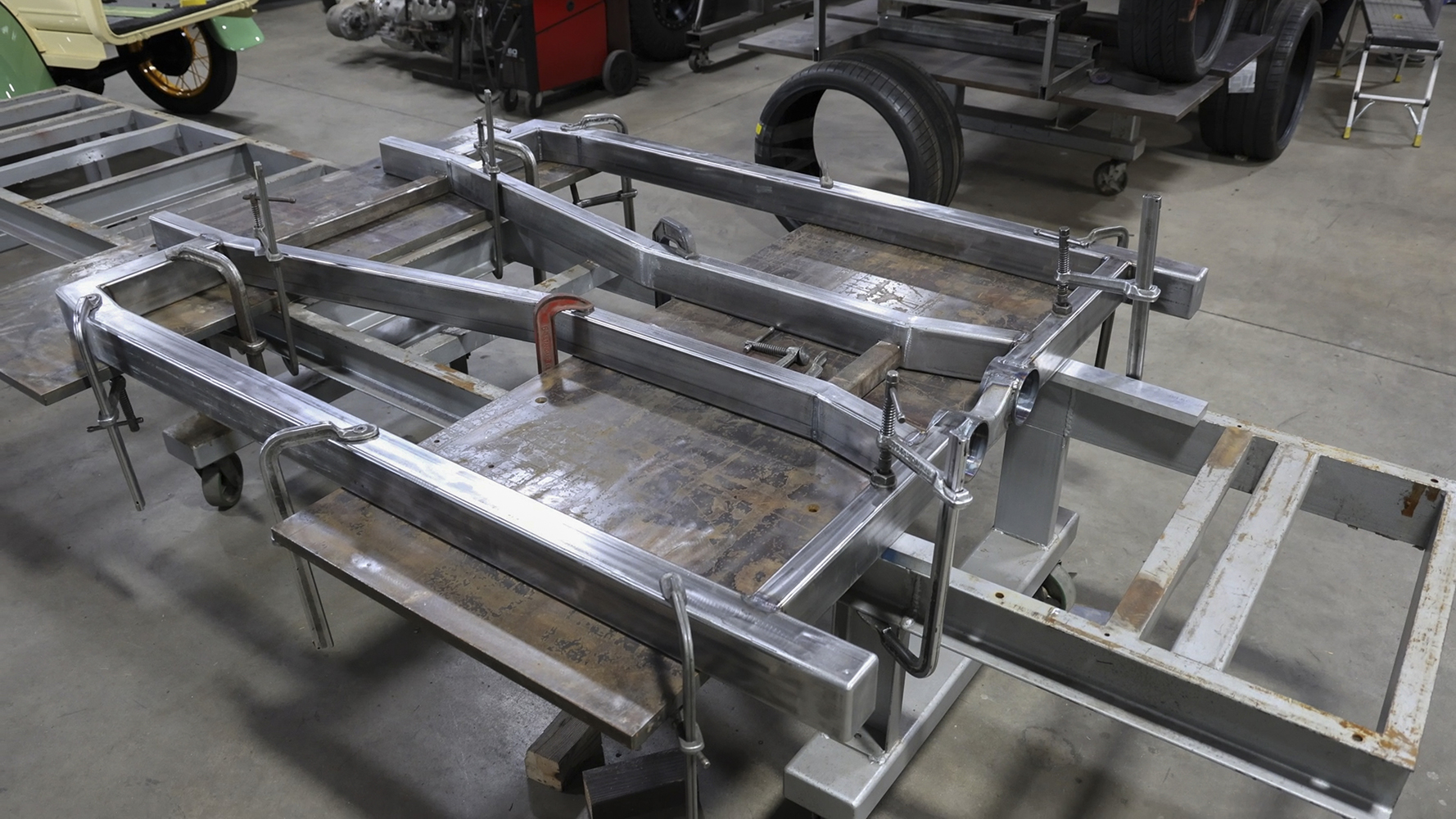
First introduced by Cadillac in 1957, 1958-1964 Chevys had what was called a cruciform, or hourglass-shaped, frame. GM touted the design allowed the seating areas to be lowered, making for a lower roofline. Of course, the bean counters loved these frames for their cost-effectiveness. The same basic frame could be used under a variety of GM cars by simply changing the length of its centersection to change the wheelbase. However, the problem with these frames was a lack of torsional rigidity, so they relied on the sills of the body to add strength. All things considered, these frames were not a great foundation for performance suspensions.
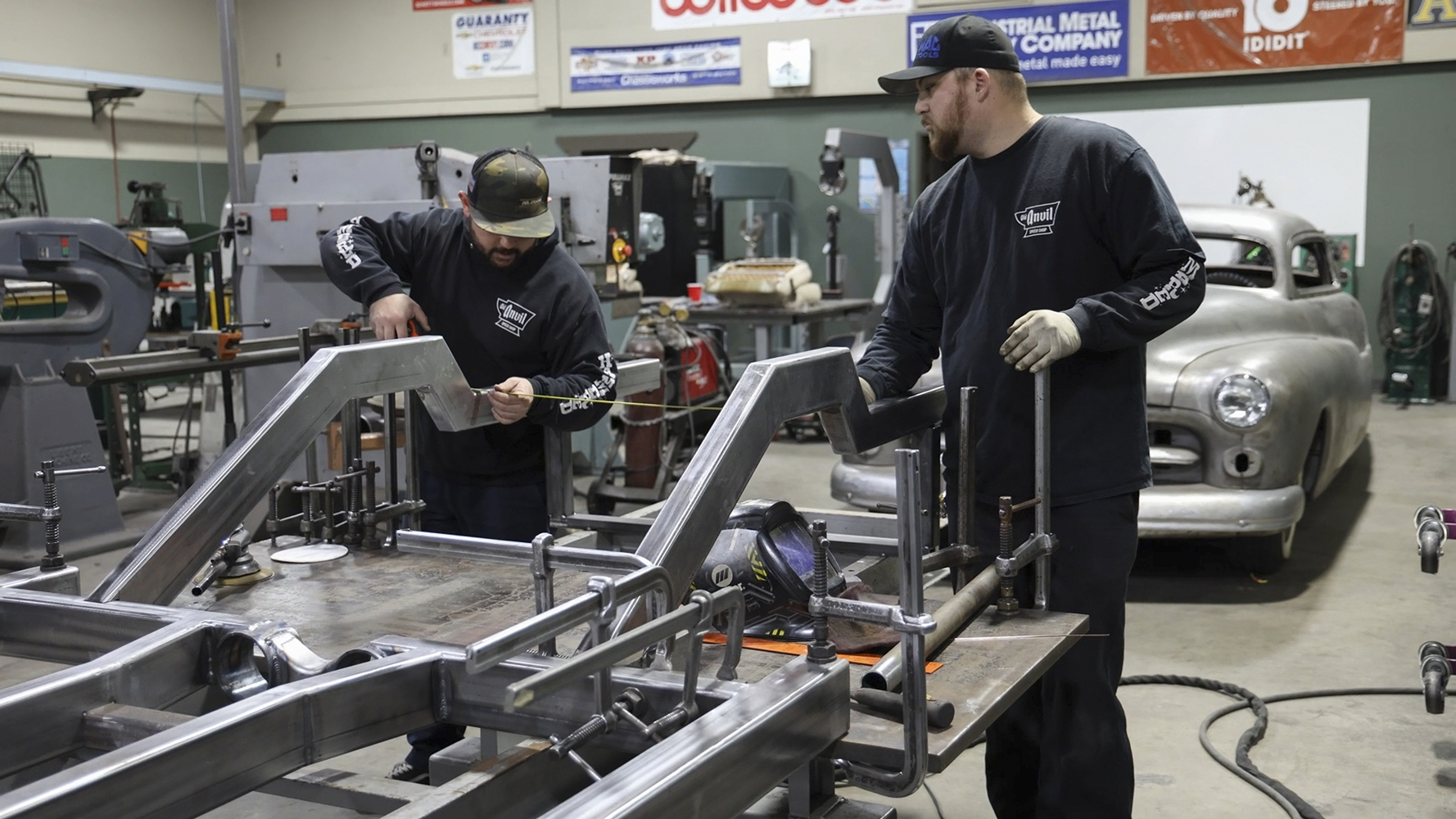
To provide the solid foundation needed for the Chevy modifications planned, Paul designed an entirely new perimeter frame, along with long-travel independent front and four-bar rear suspensions. Old Anvil’s Brandon Gerringer, Jake Caballero, and Phillip Avila handled fabrication.
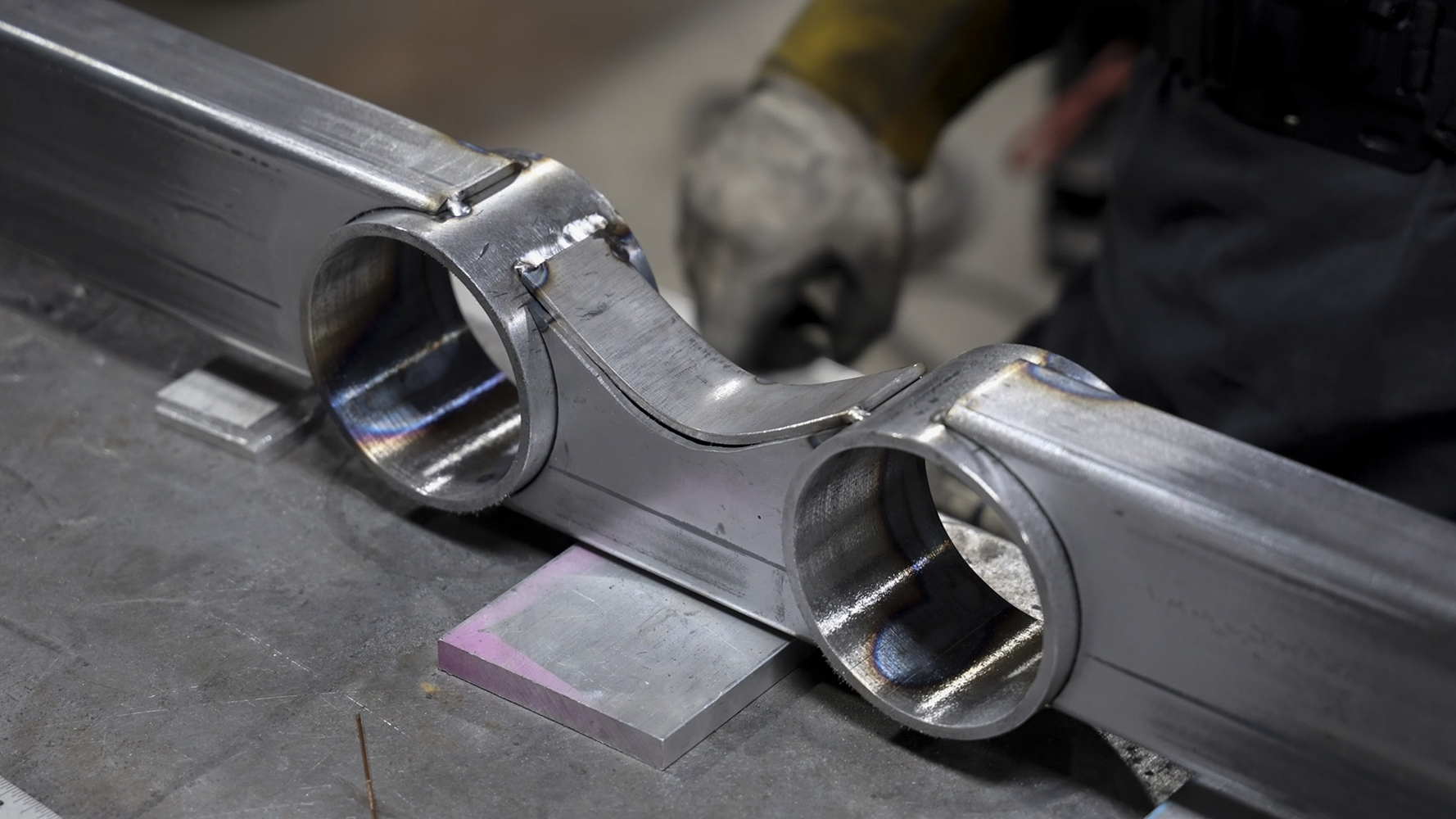
Both ends of the chassis are on airbags that allow for a total of 7 inches of suspension travel. Paul designed the suspension to enable the Chevy to come within inches of the ground and then rise to a reasonable ride height. The ride height and air pressure management system are from Air Lift Performance; ride quality will be assured by King Shocks, and sway bars on both ends from Old Anvil will keep the Chevy flat in the corners.
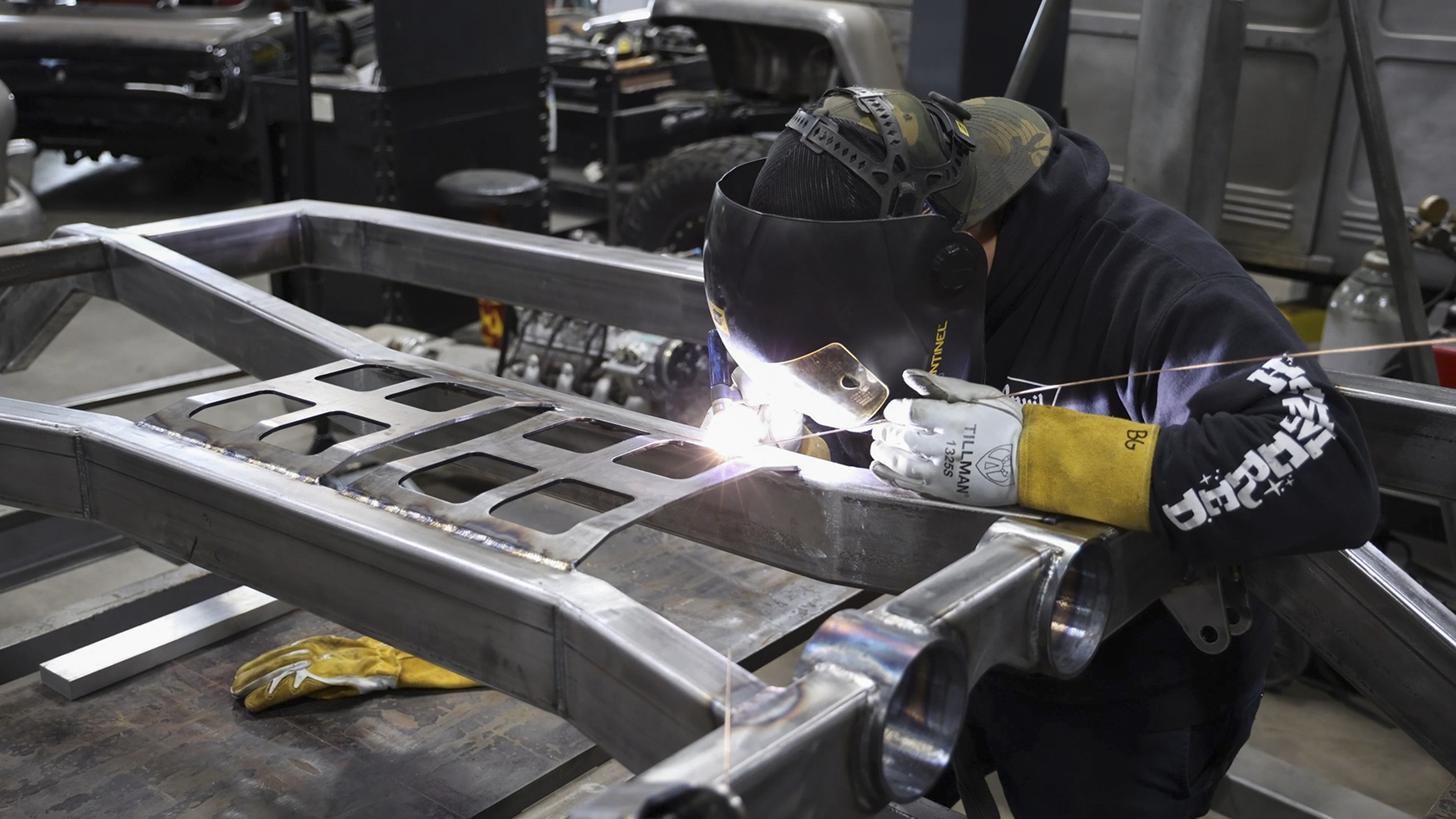
With the stock chassis out of the way, the new frame, replacement floor, and body joined. The rocker boxes were welded to the sides of the main ’rails, and the rest of the floor was welded to the top of the ’rails. In addition, the rear crossmember of the body is welded to the ends of the framerails. The result was a unitized shell, allowing the suspension to work as it should.
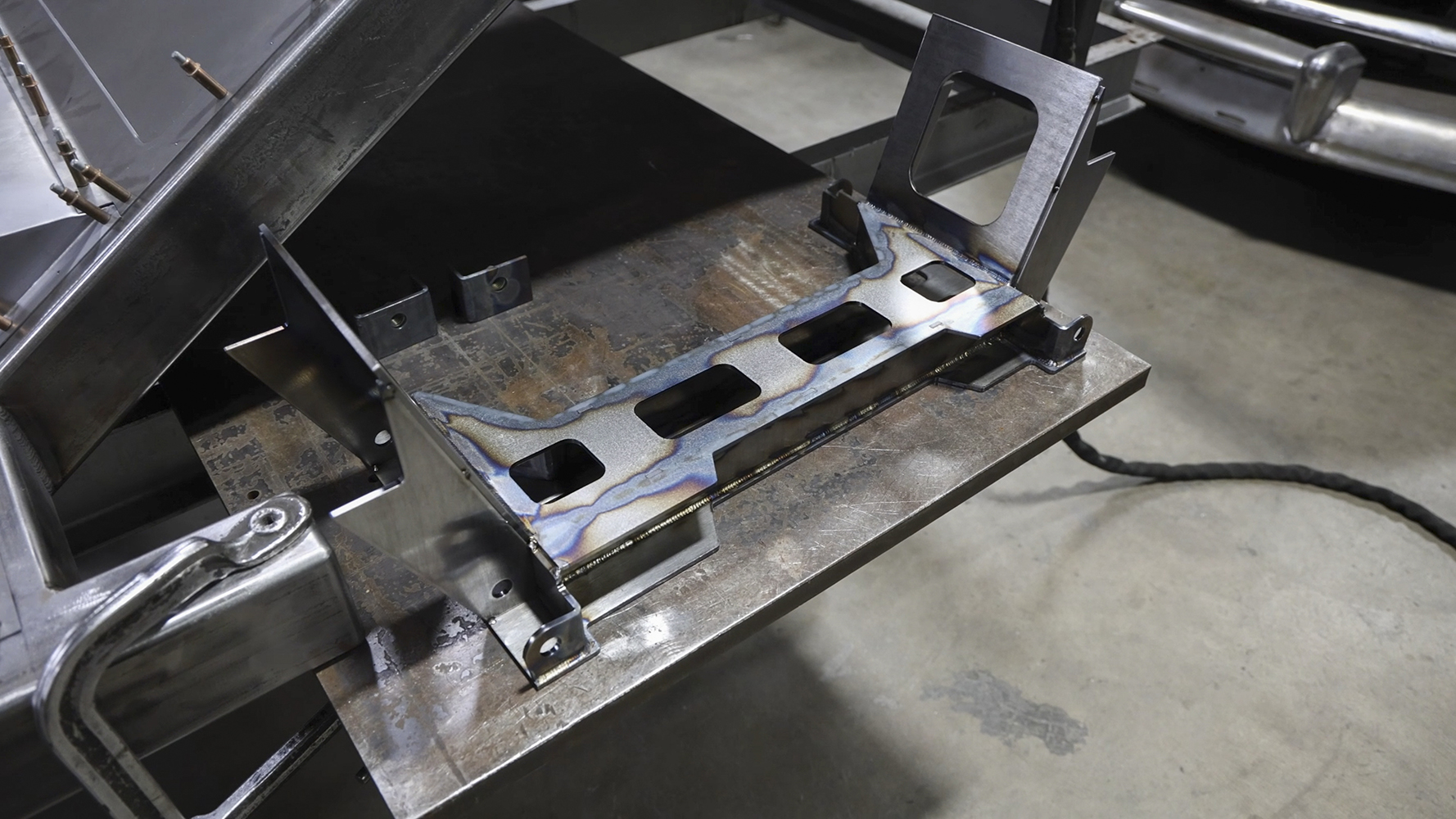
The engine and transmission would also be special along with the custom-built chassis. Underhood, the original small-block 327 and BorgWarner four-speed will be replaced by a Nelson Racing Engines LS-based 427 backed by a 4L80E automatic transmission. Topped with a Kong intercooled supercharger, the engine is said to produce 1,200 hp.
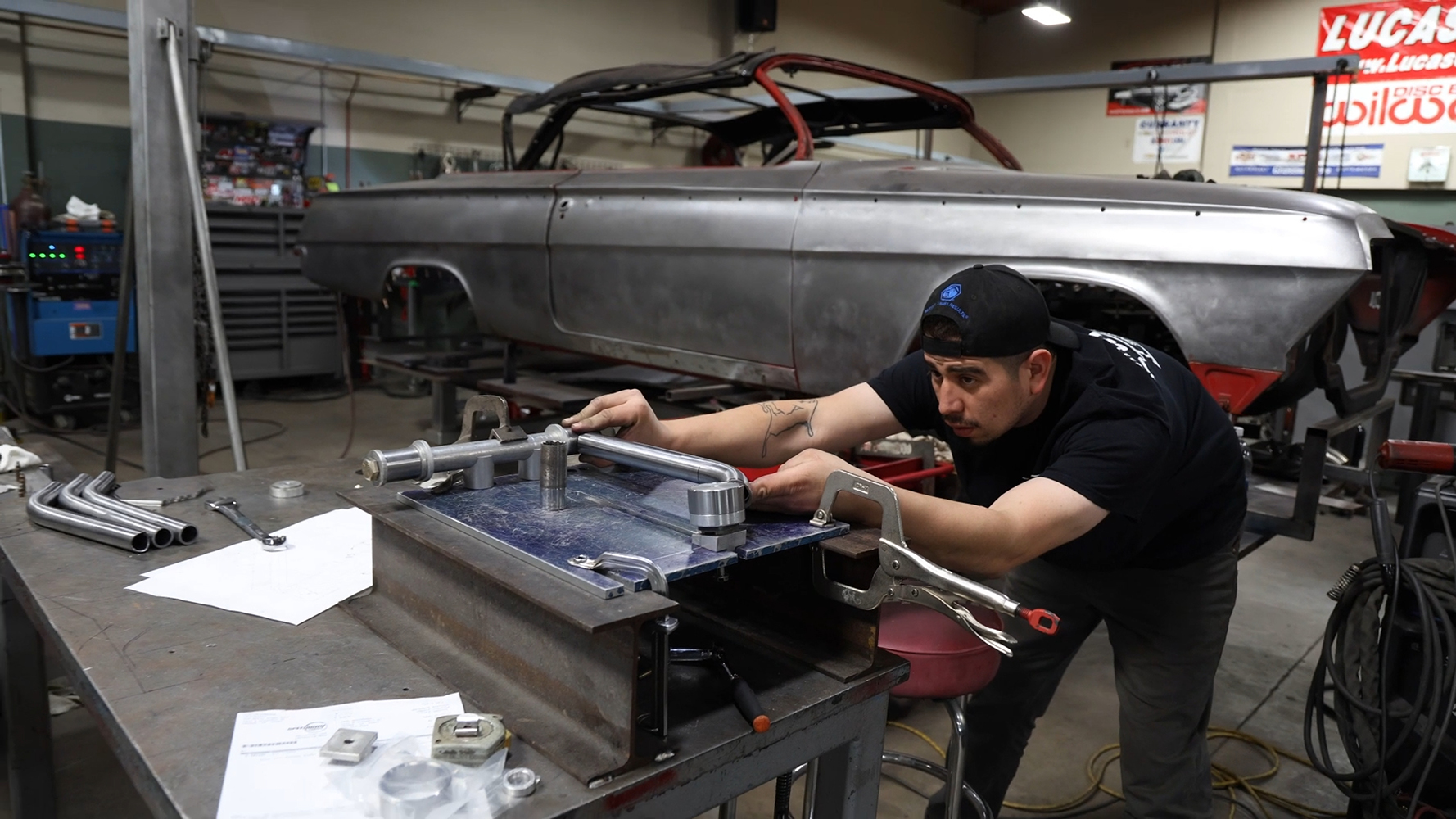
While relatively new on the scene, Old Anvil Speed Shop has already gained a reputation for creativity and craftsmanship—their work on this radical ragtop is just one reason why.
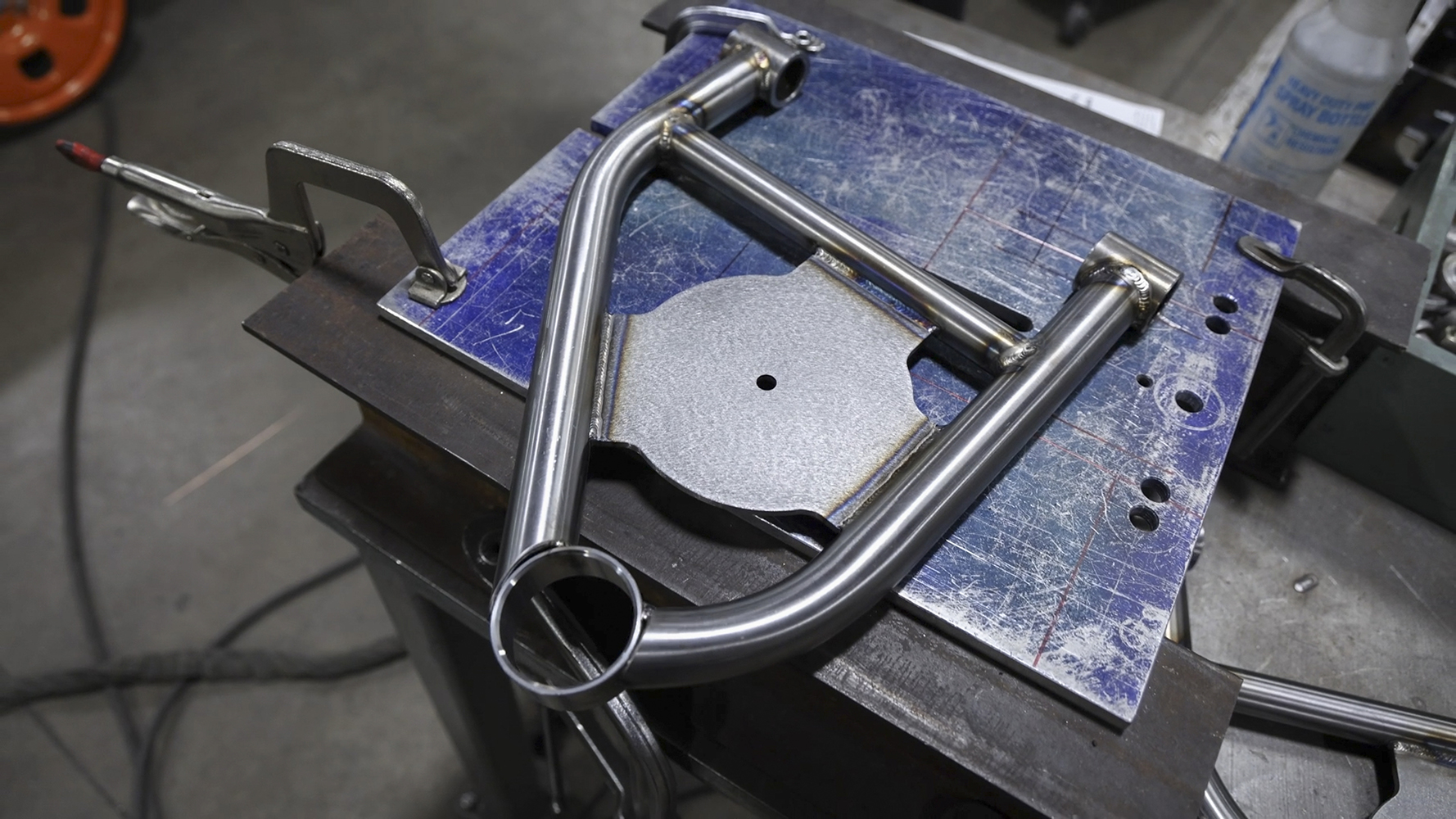
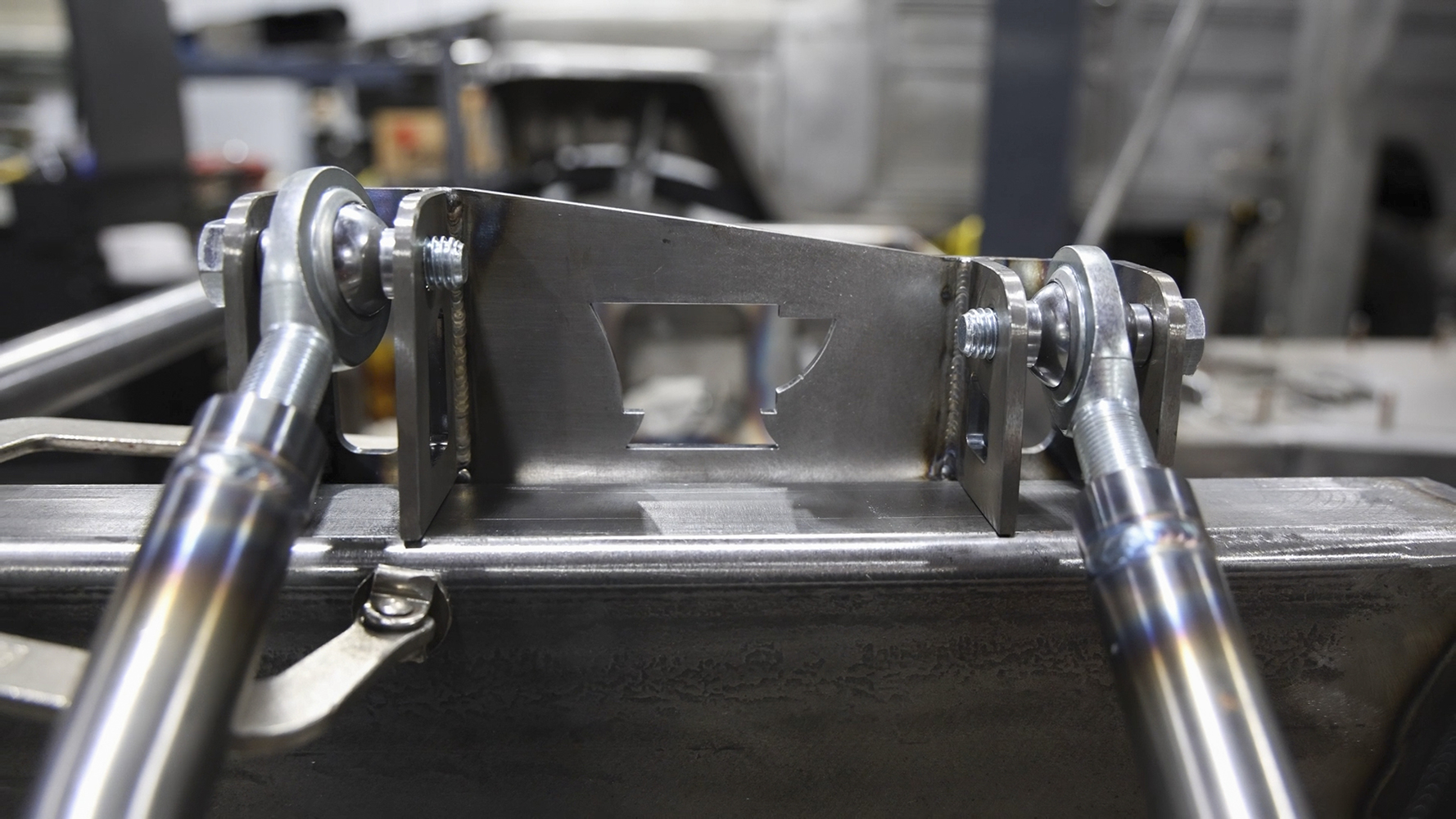
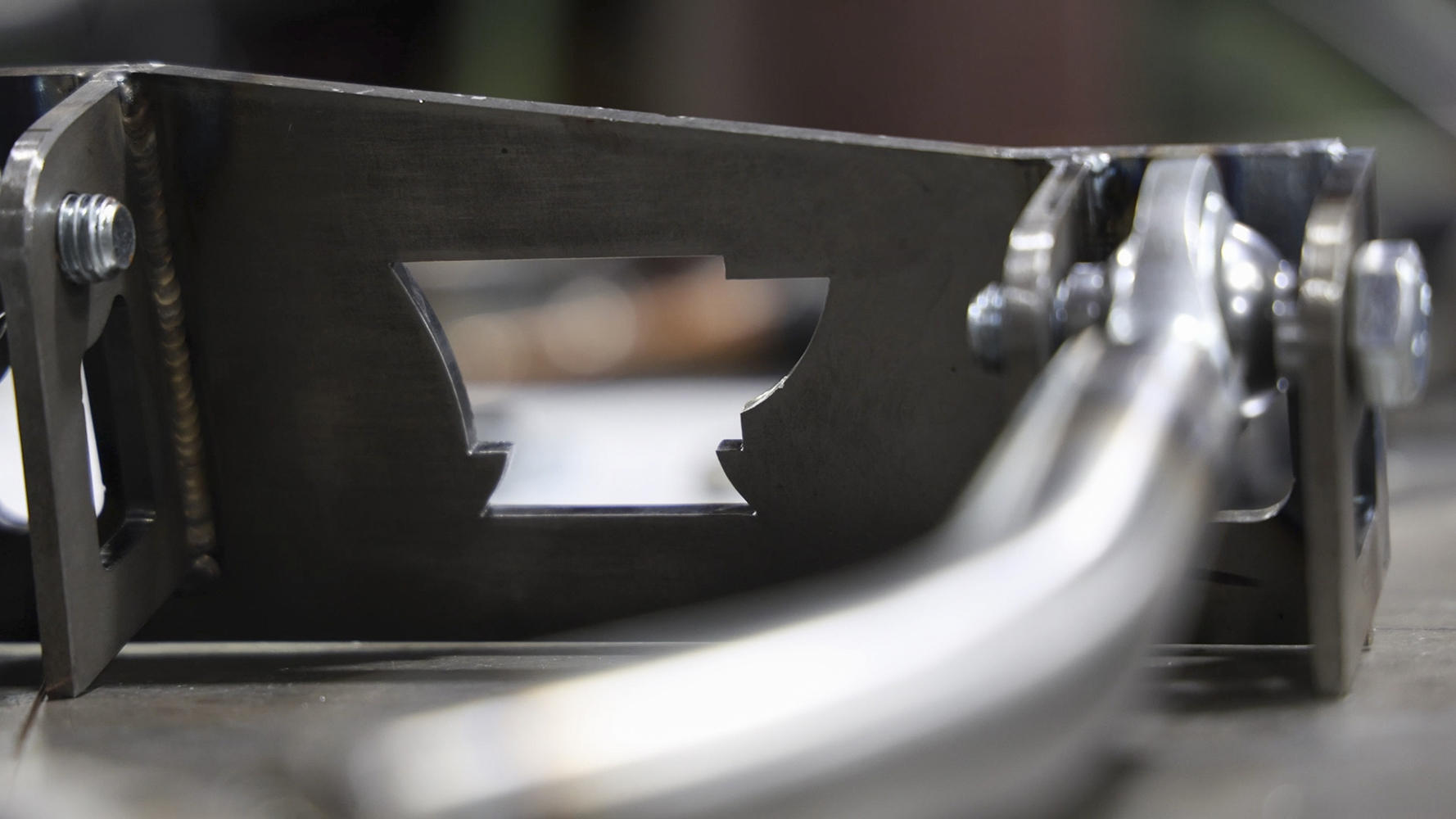
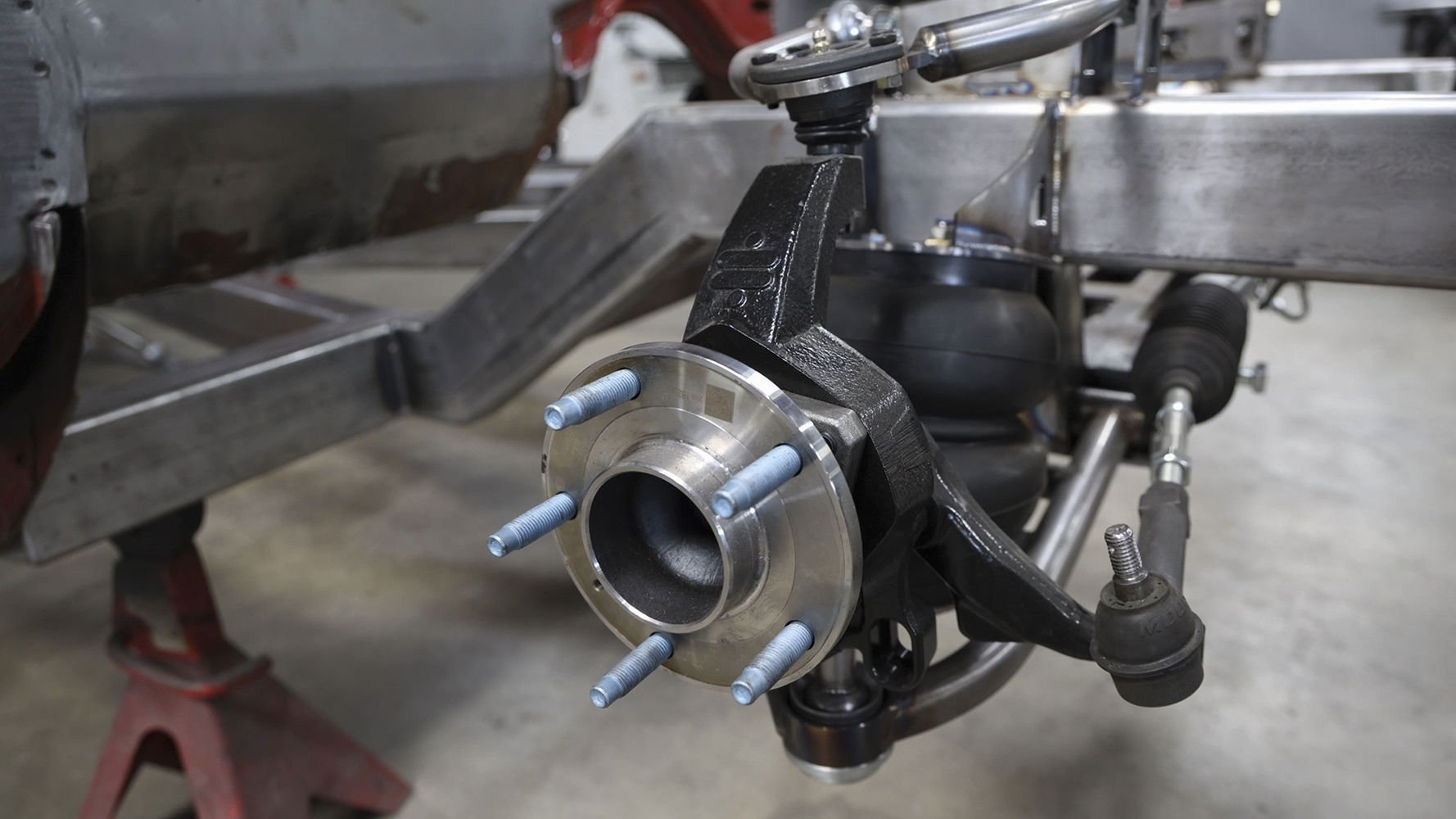
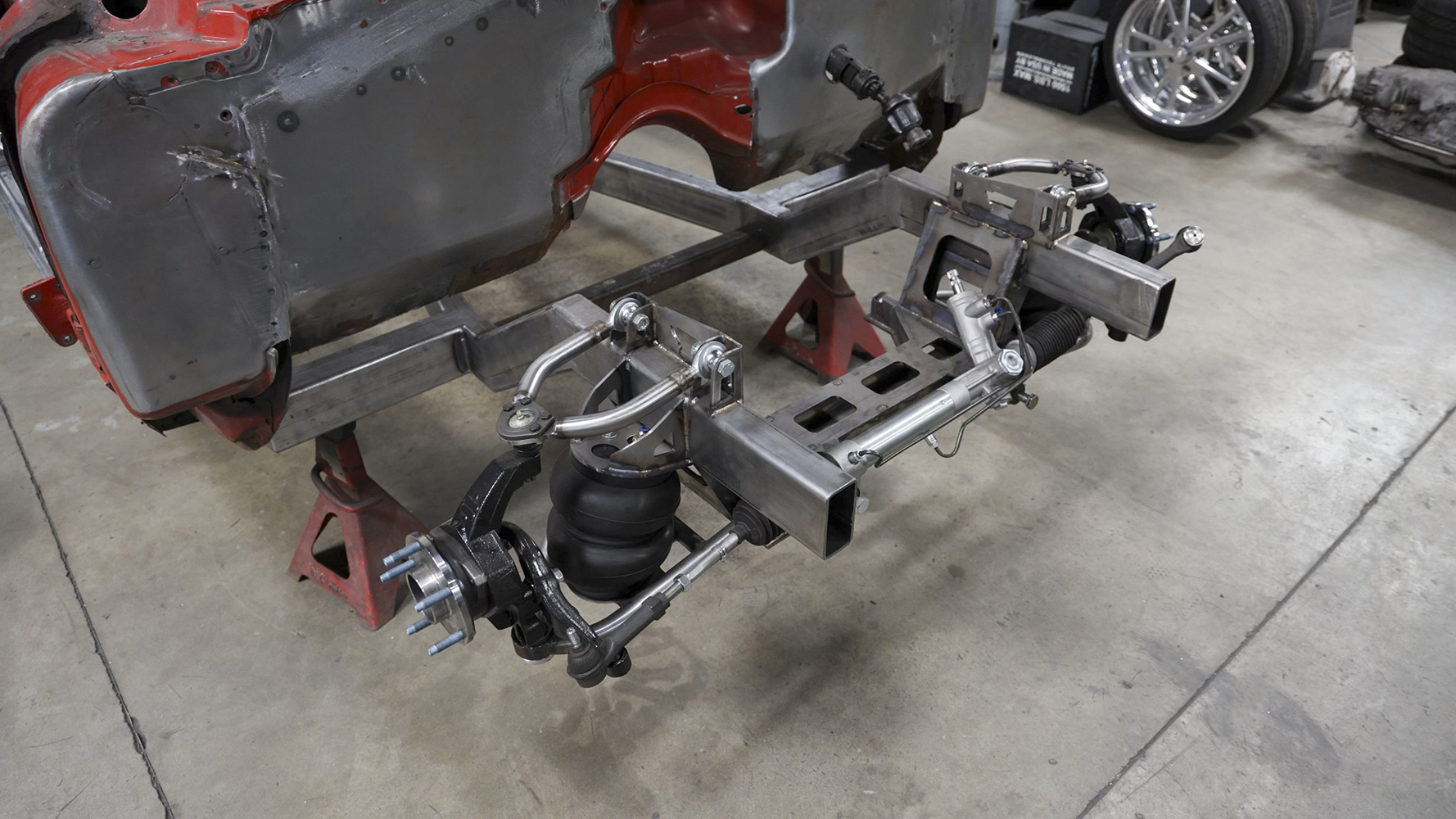
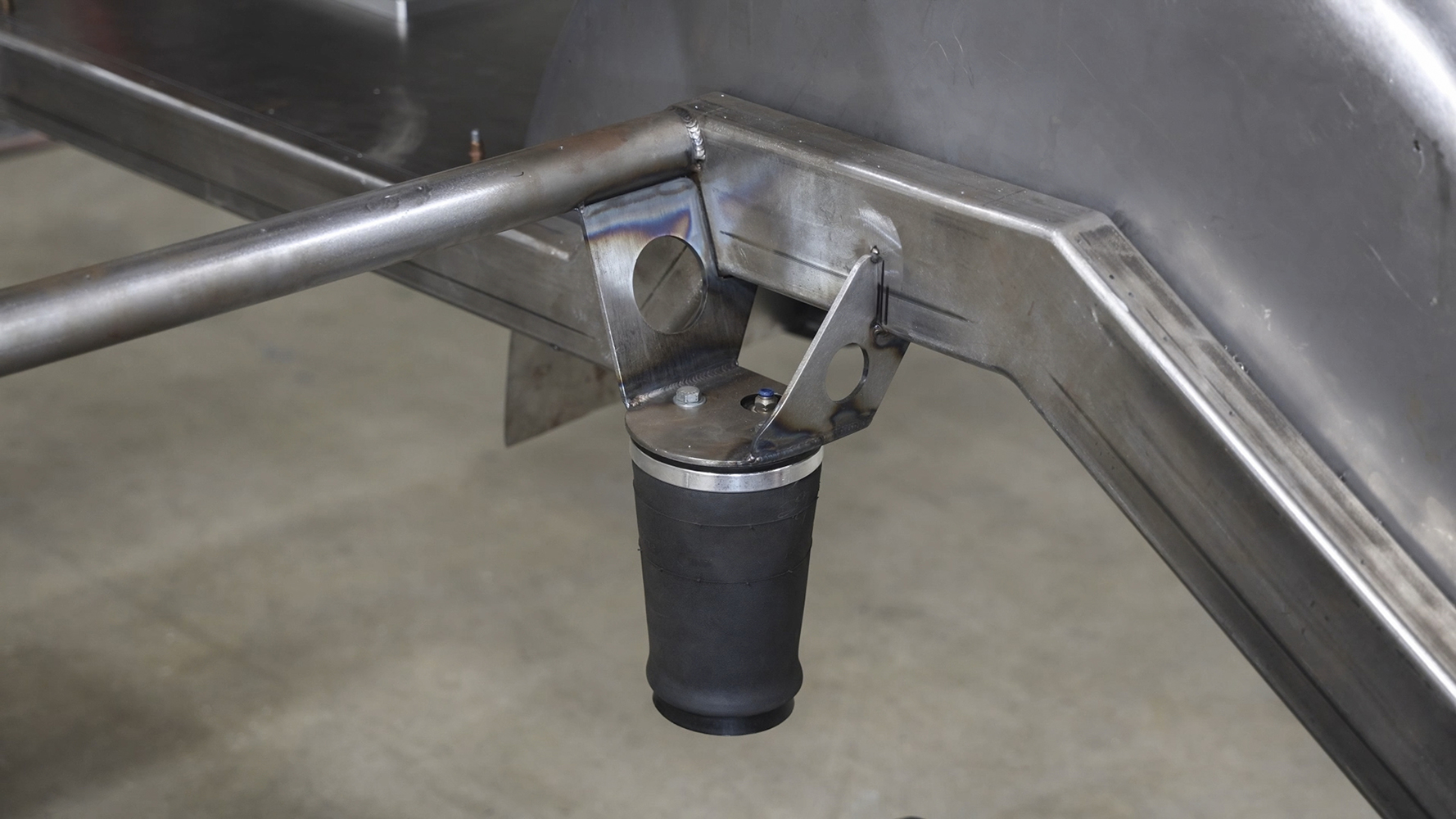
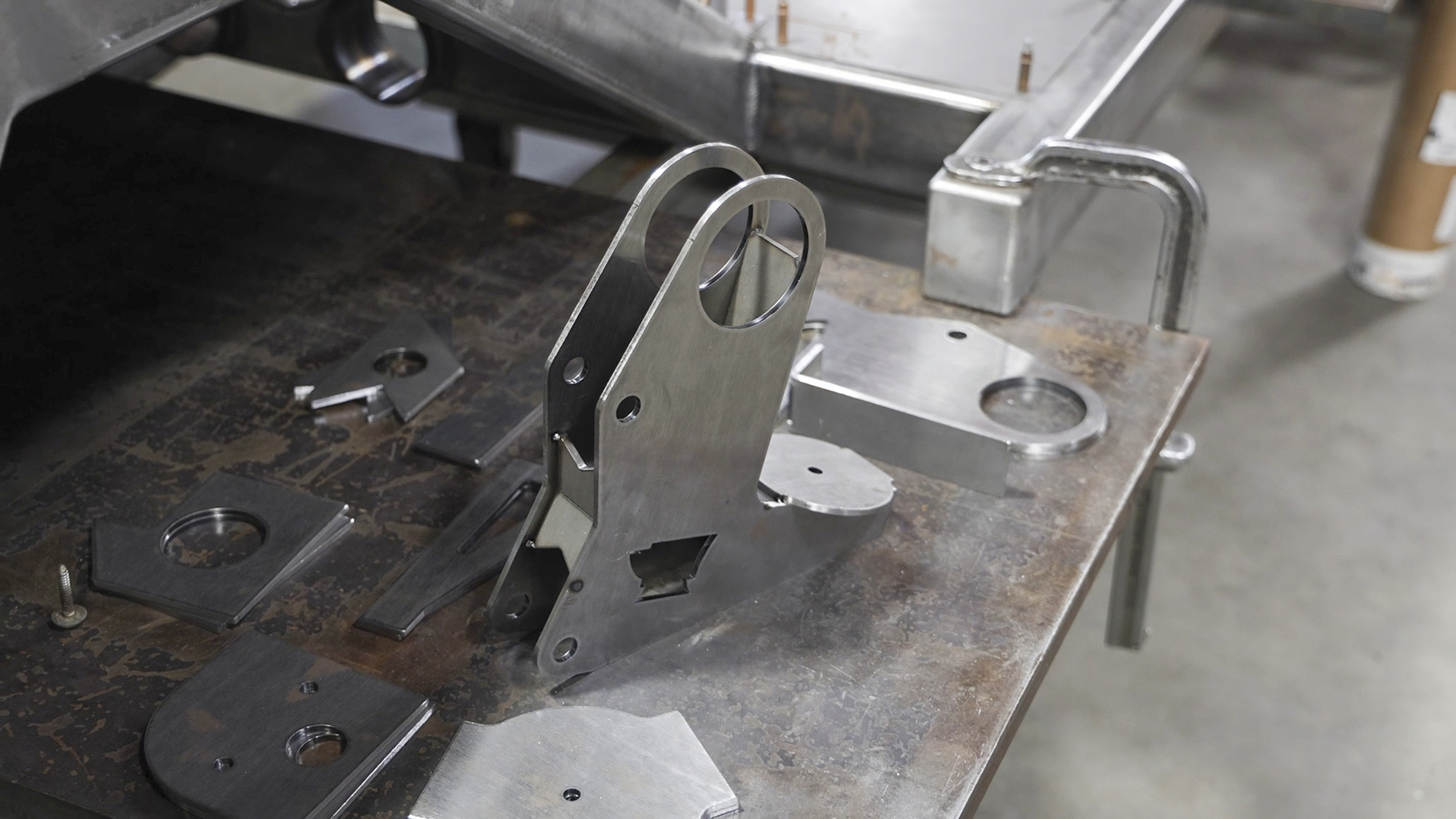
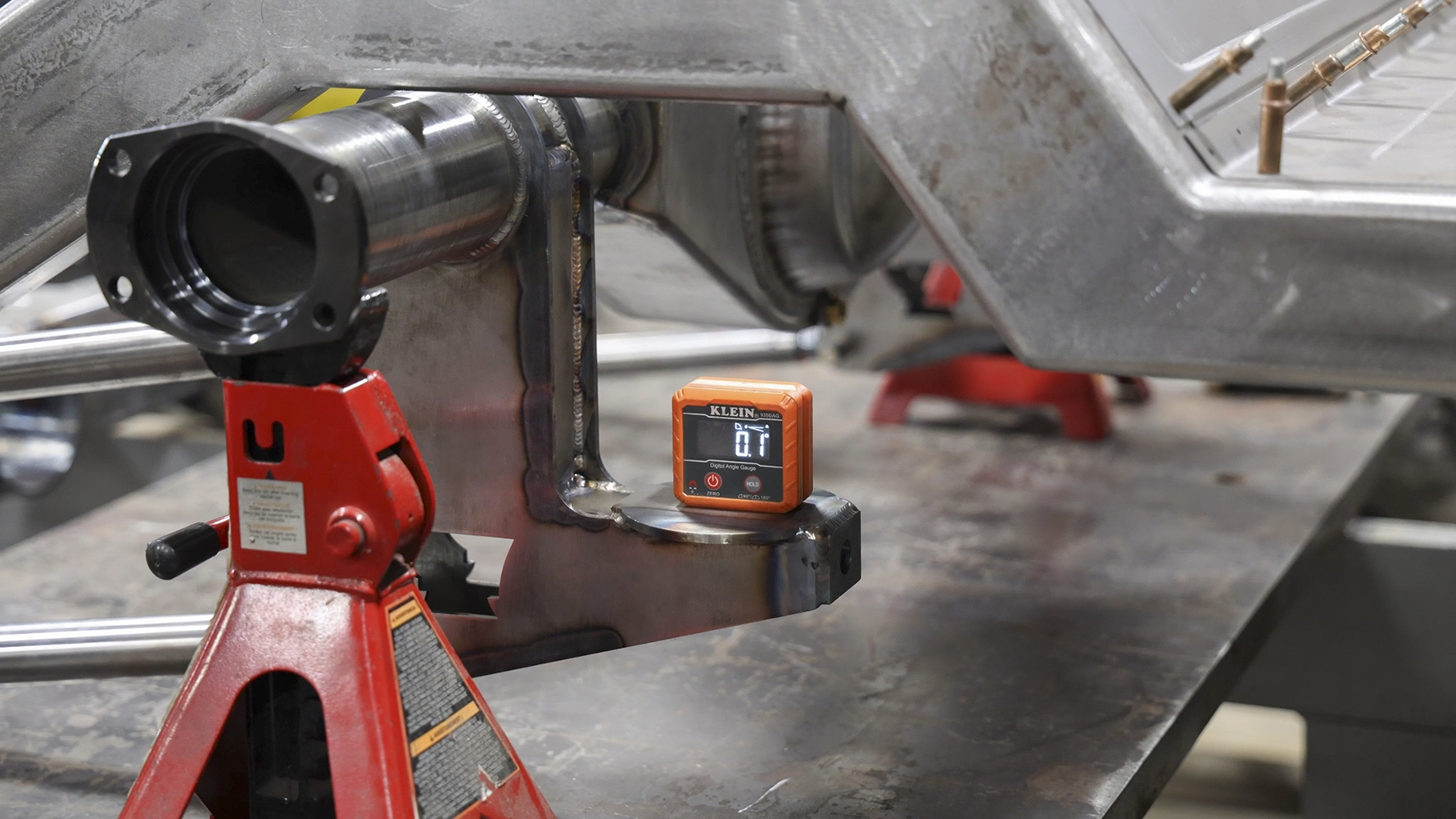
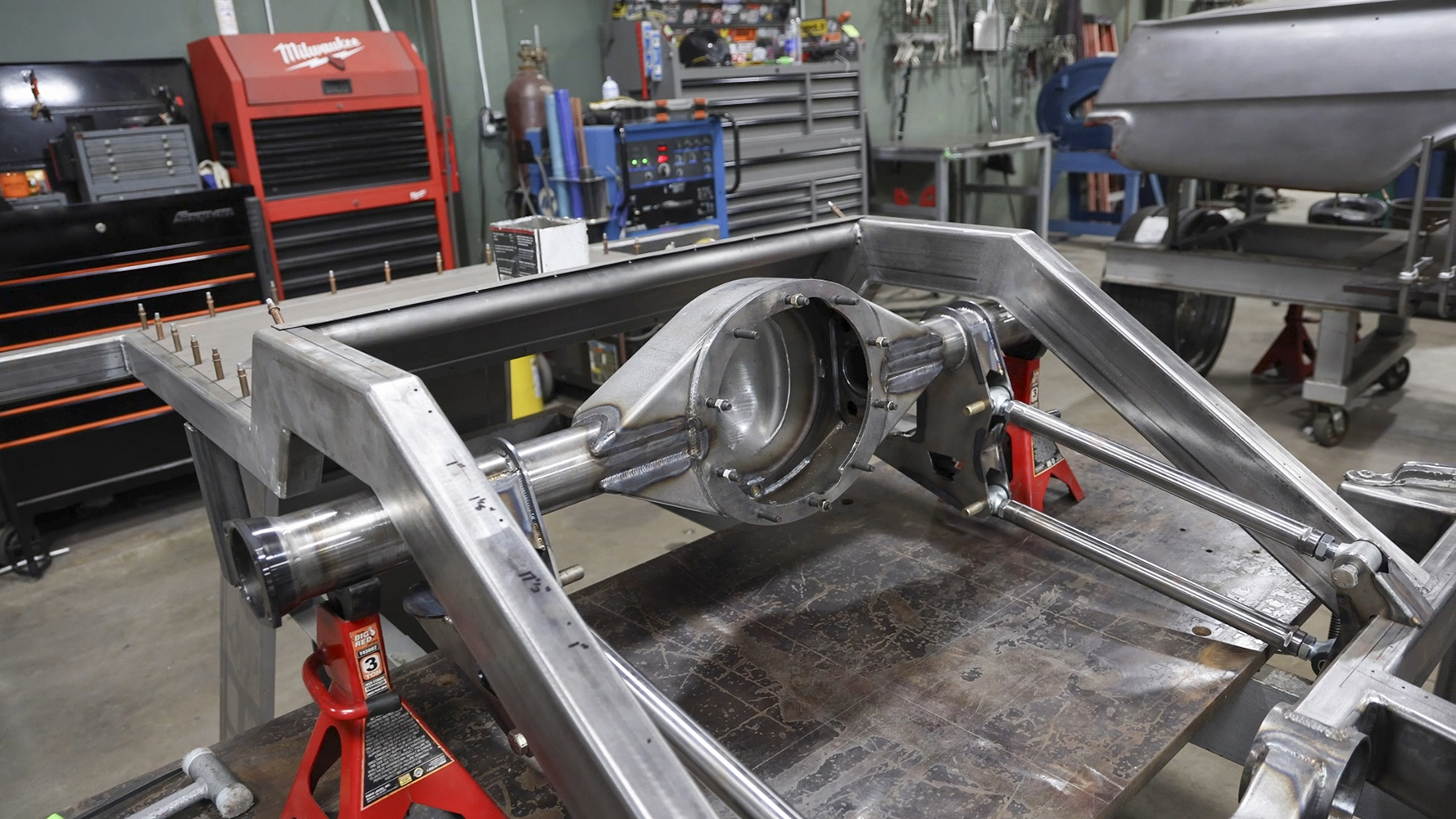
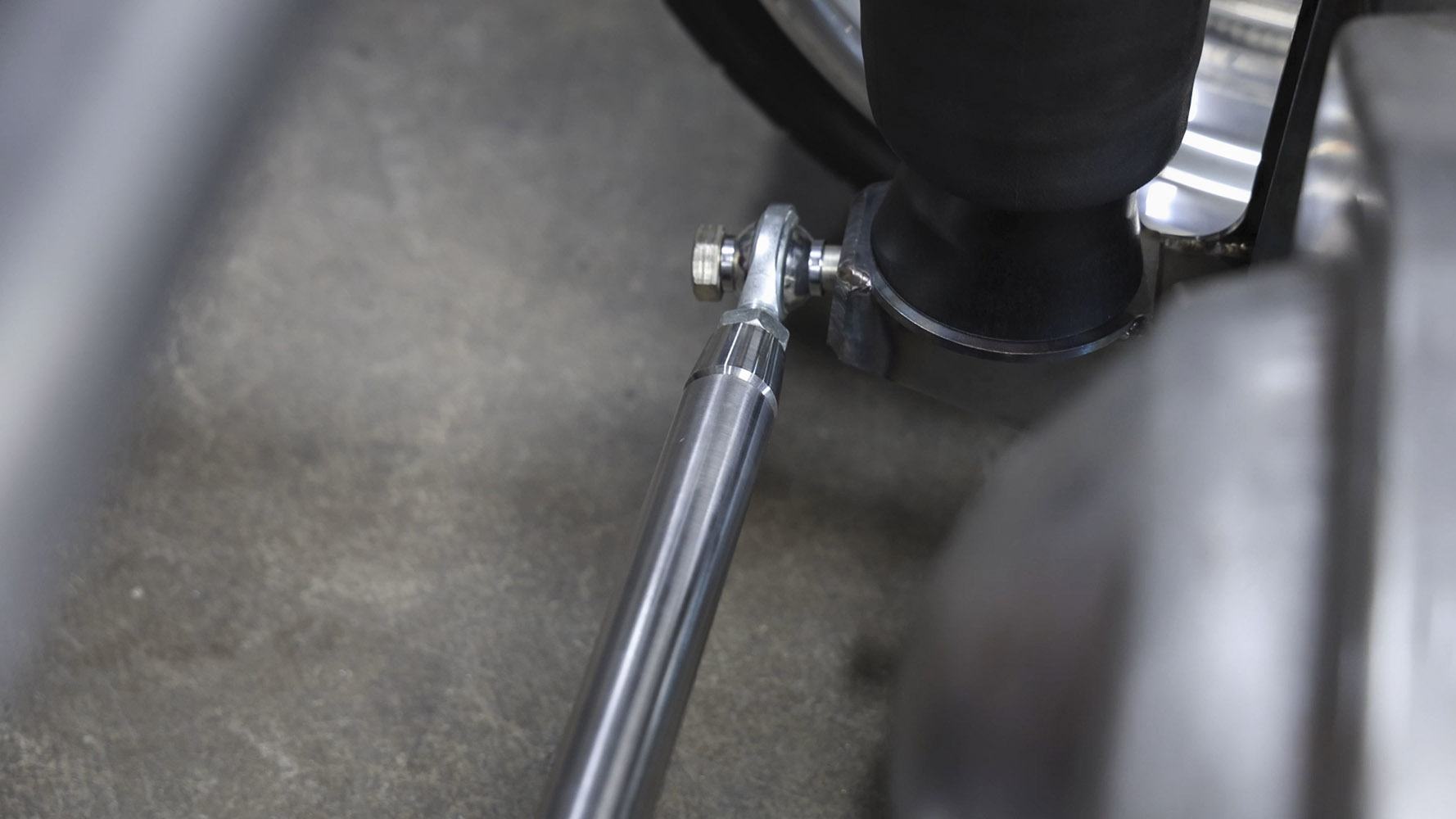
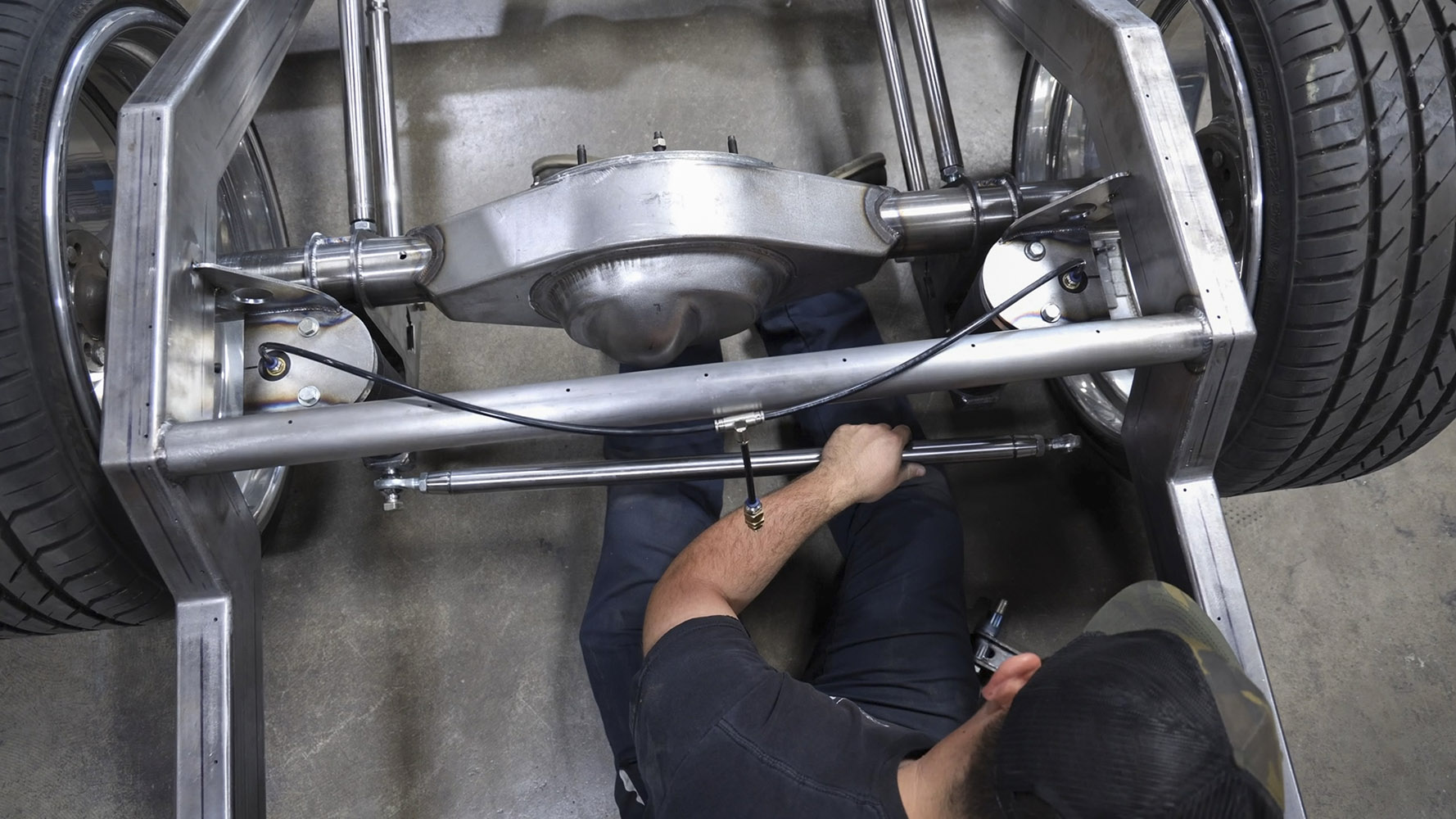
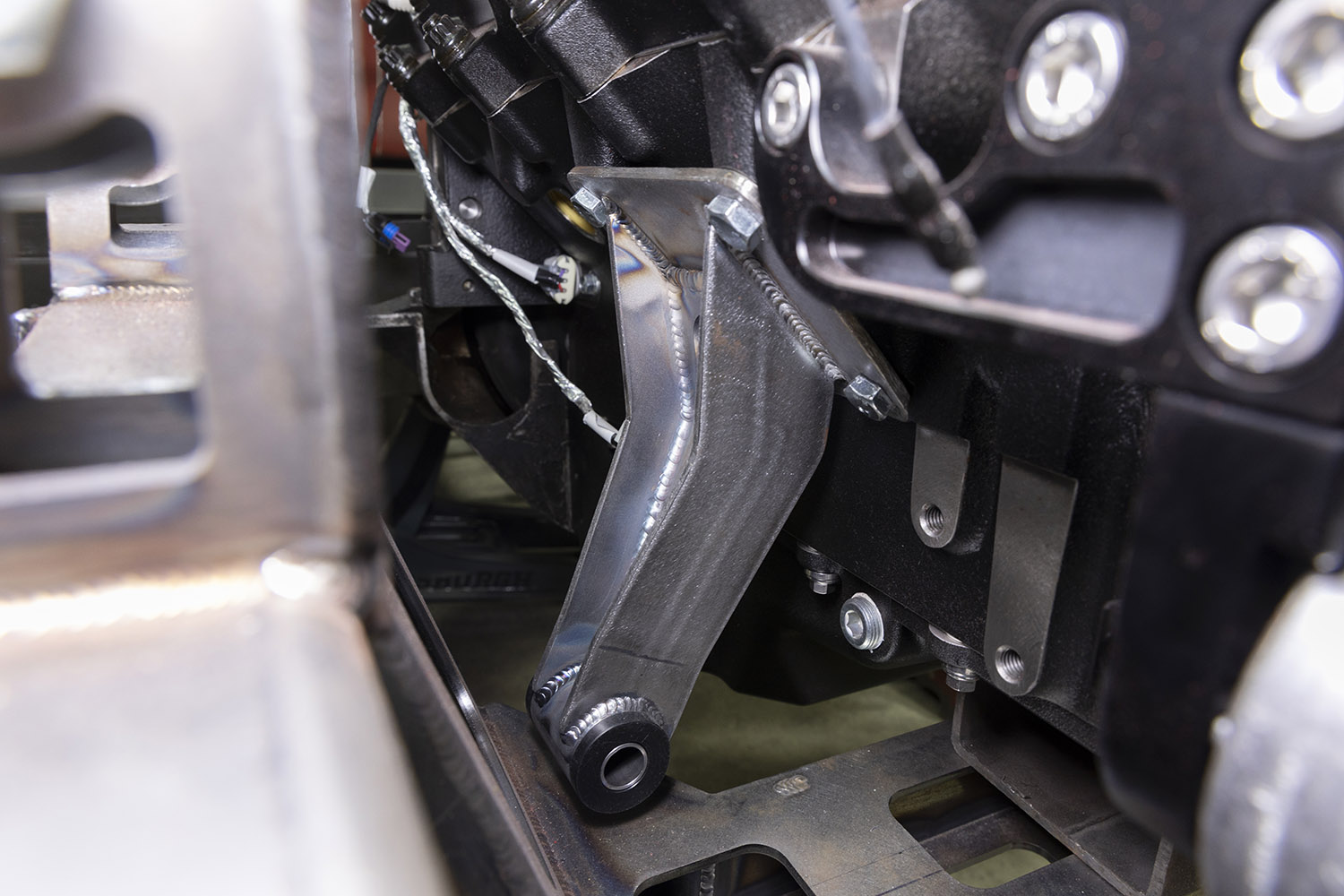
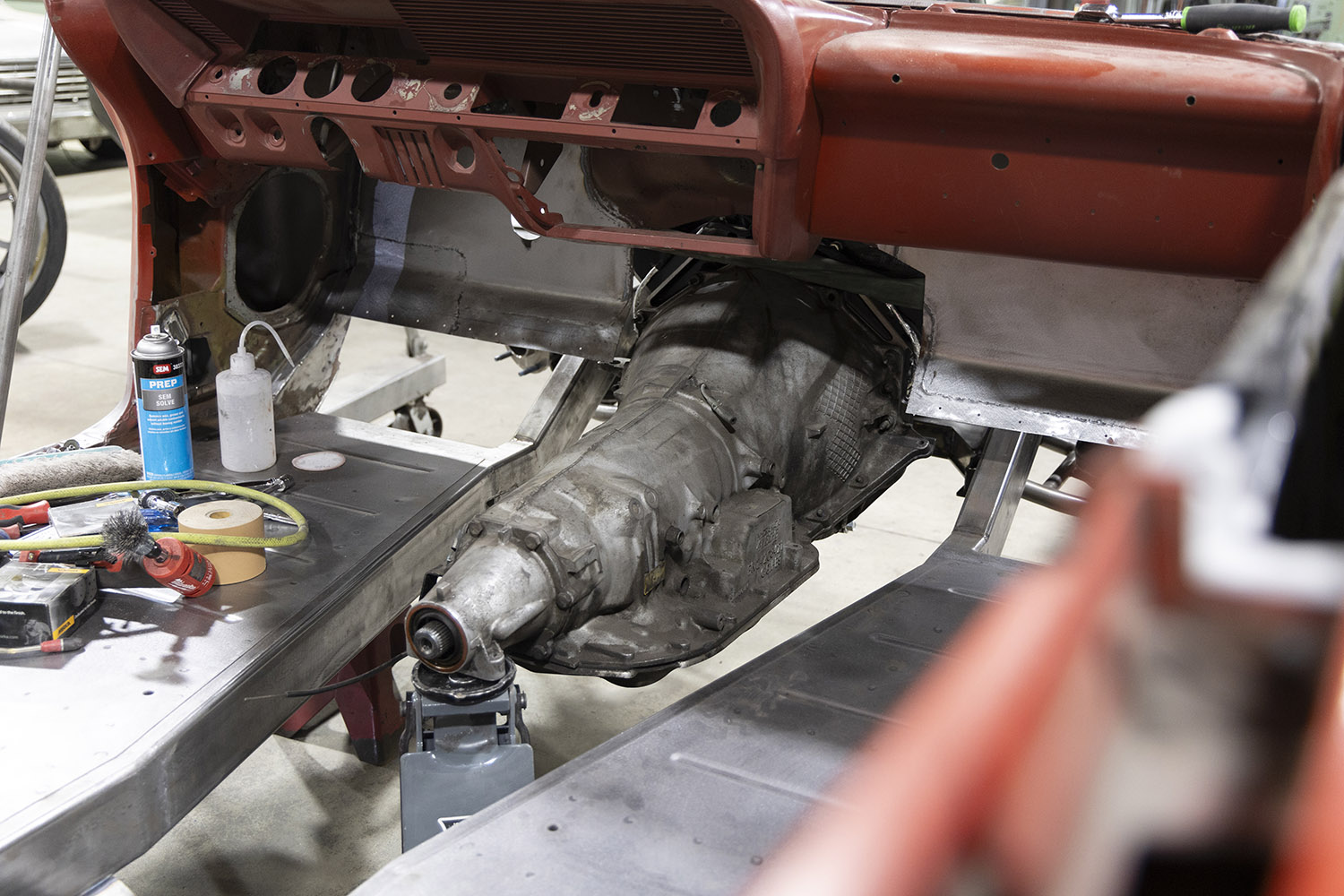
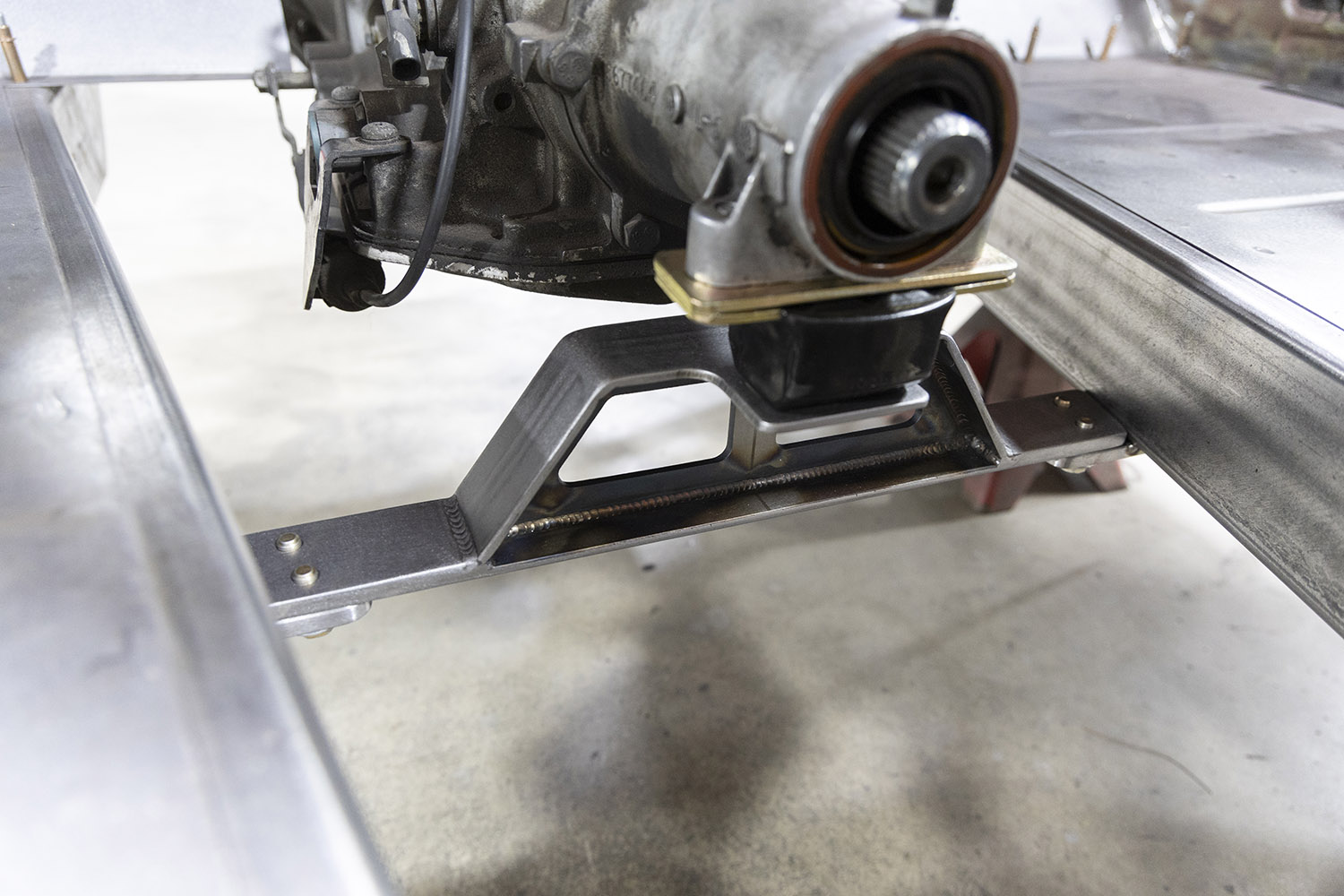
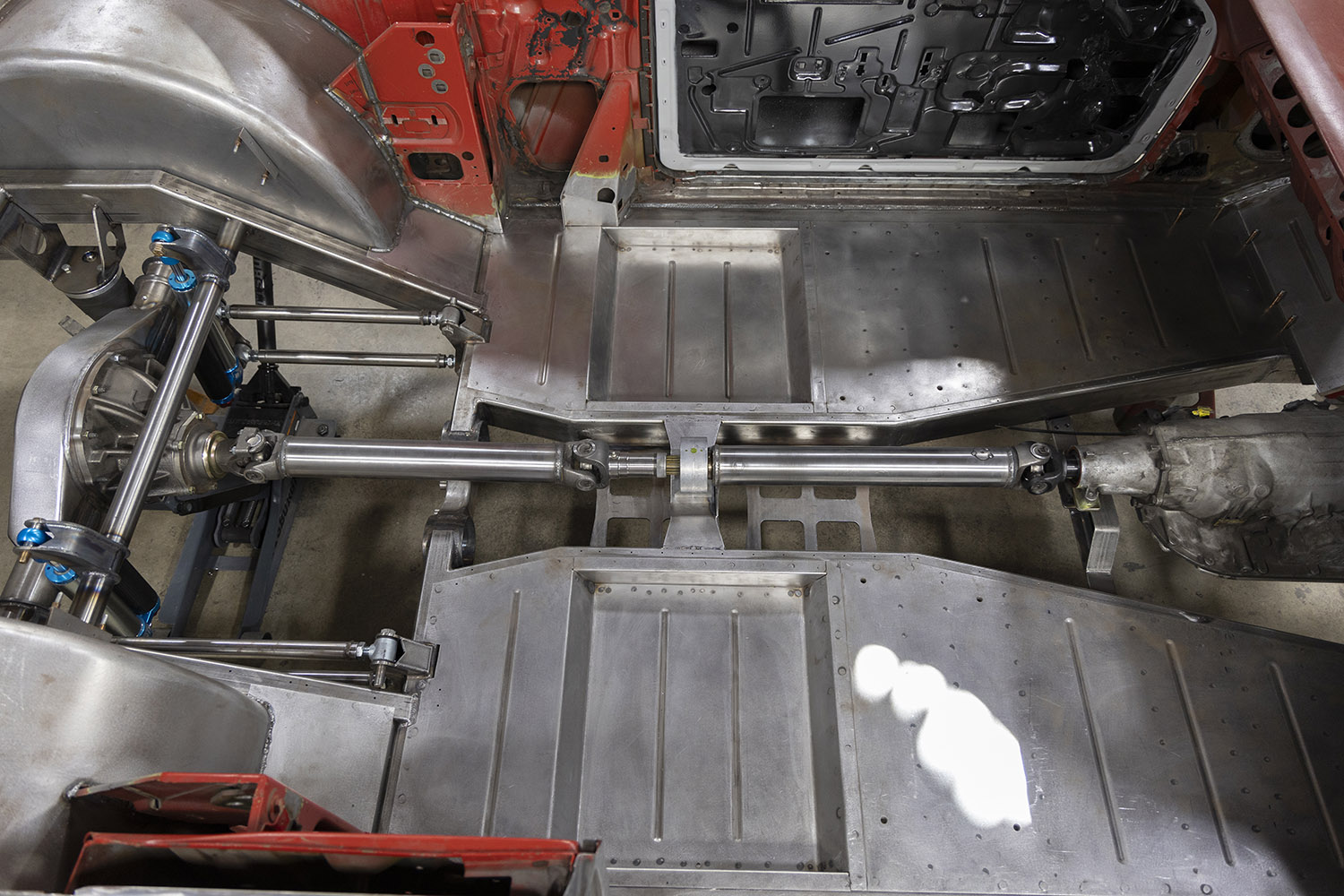
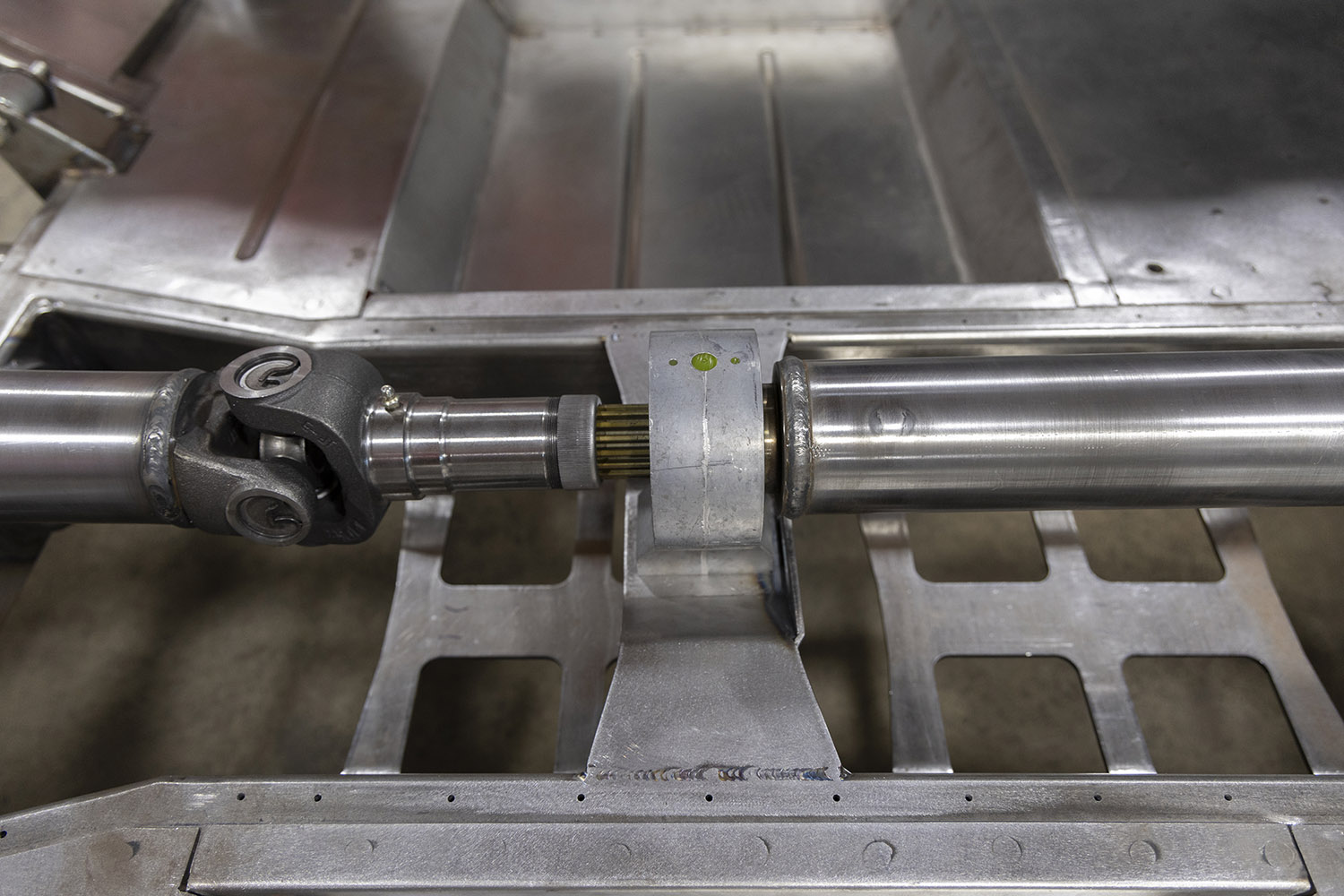
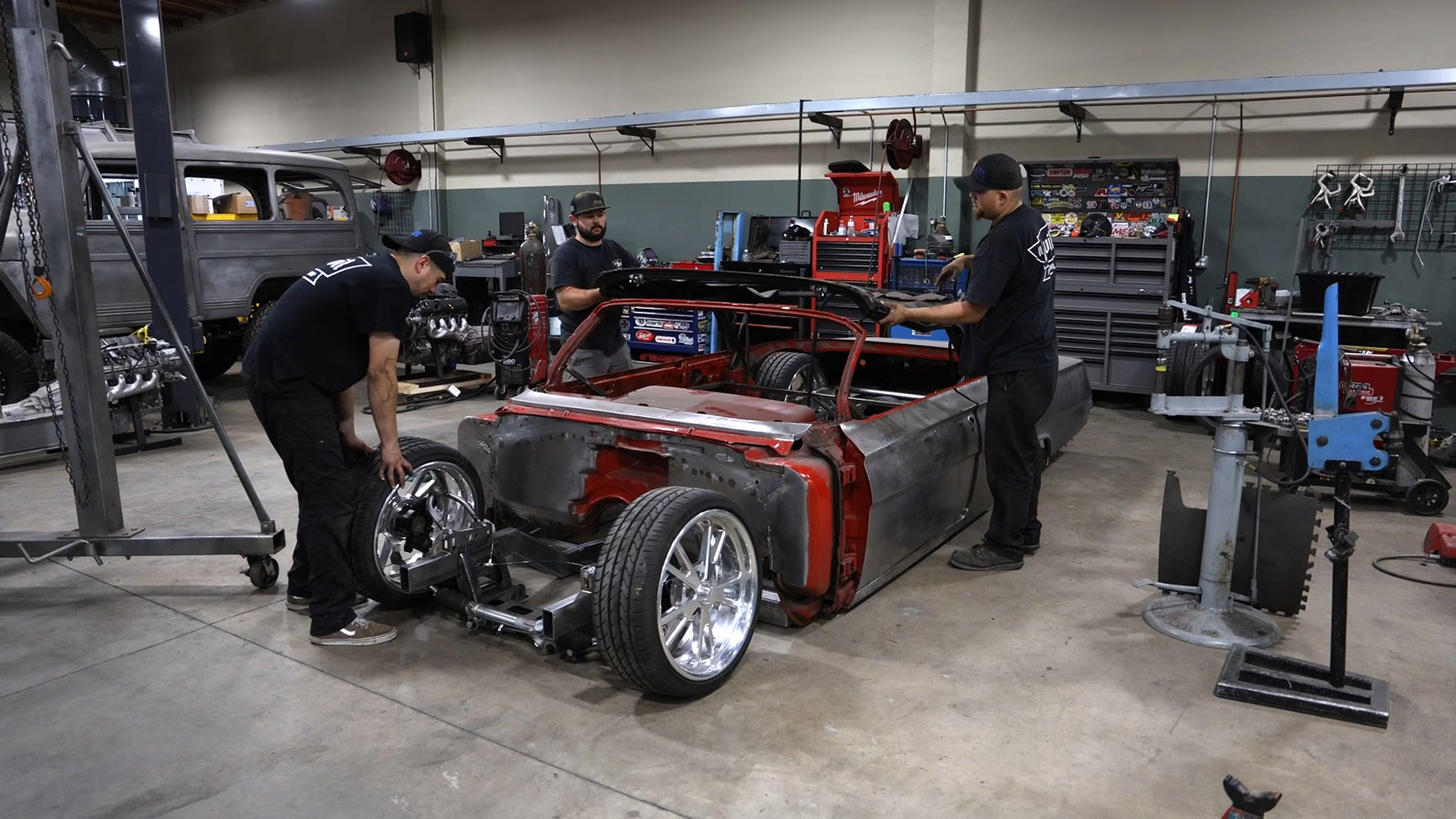
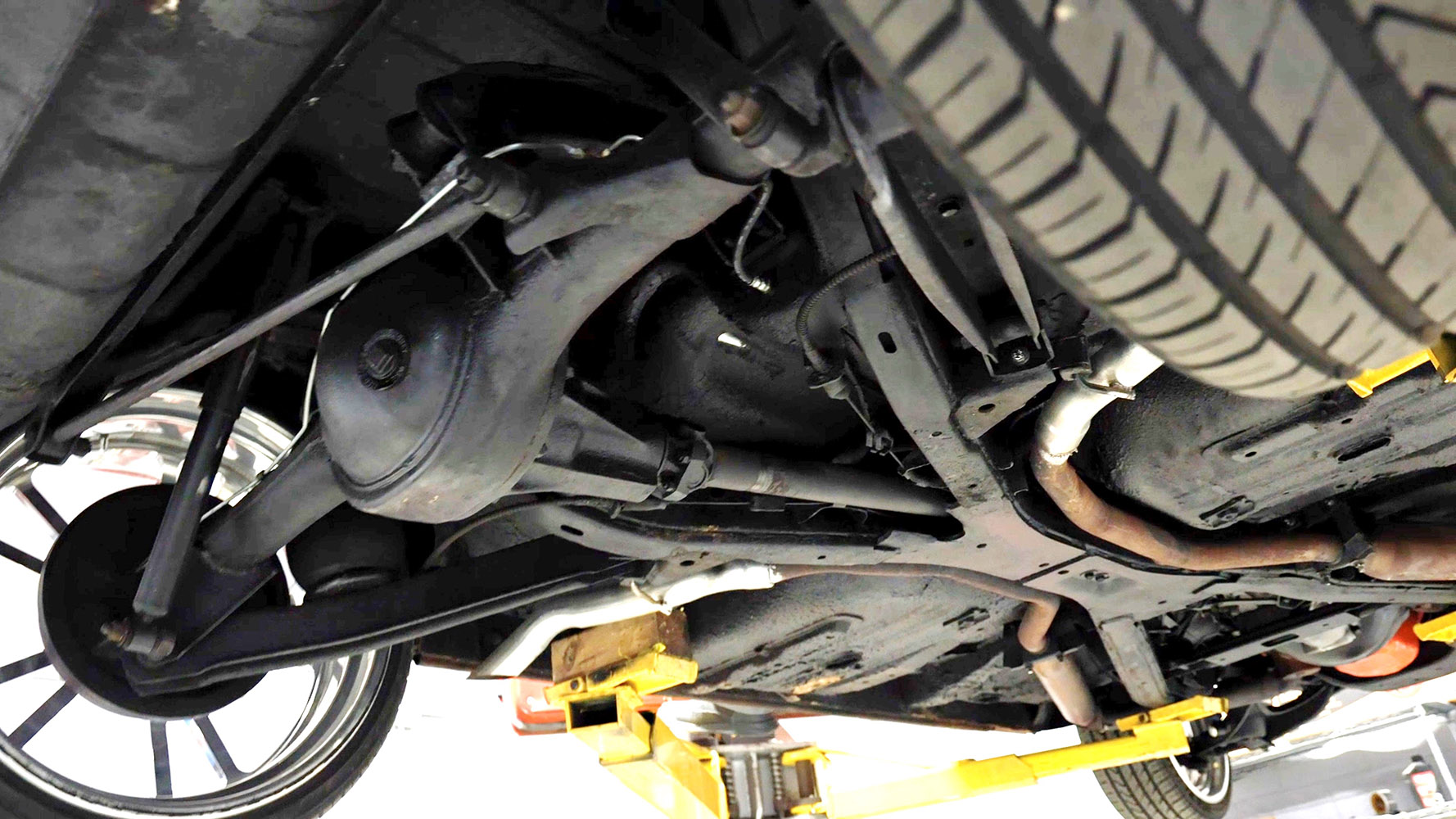
Check out this story in our digital edition here.
MR
Source
Old Anvil Speed Shop
(657) 223-9889
oldanvilspeedshop.com