If you’ve been around cars for any length of time, you’ve probably heard the well-worn aphorism “The camshaft is the brain of the engine,” or some version of it.
There is a bit of truth to that since the cam does determine when the valves in the cylinder heads open and close and how quickly, but unlike us smarter individuals—you know, those of us who prefer Chevrolet power over … well, let’s just say another brand—cams really can’t make decisions. Variable valve timing is helpful, but once the cam is stabbed in the engine, duration and valve lift really won’t change. So, the lesson here is not a matter of how advanced the technology may be in your engine, the cam still needs to be ground correctly for your application.
Of course that’s easier said than done. Even the very best engine builders test different cams occasionally just to make sure they are getting the best possible results. When you make changes to an engine package you may also need to update your cam specs.
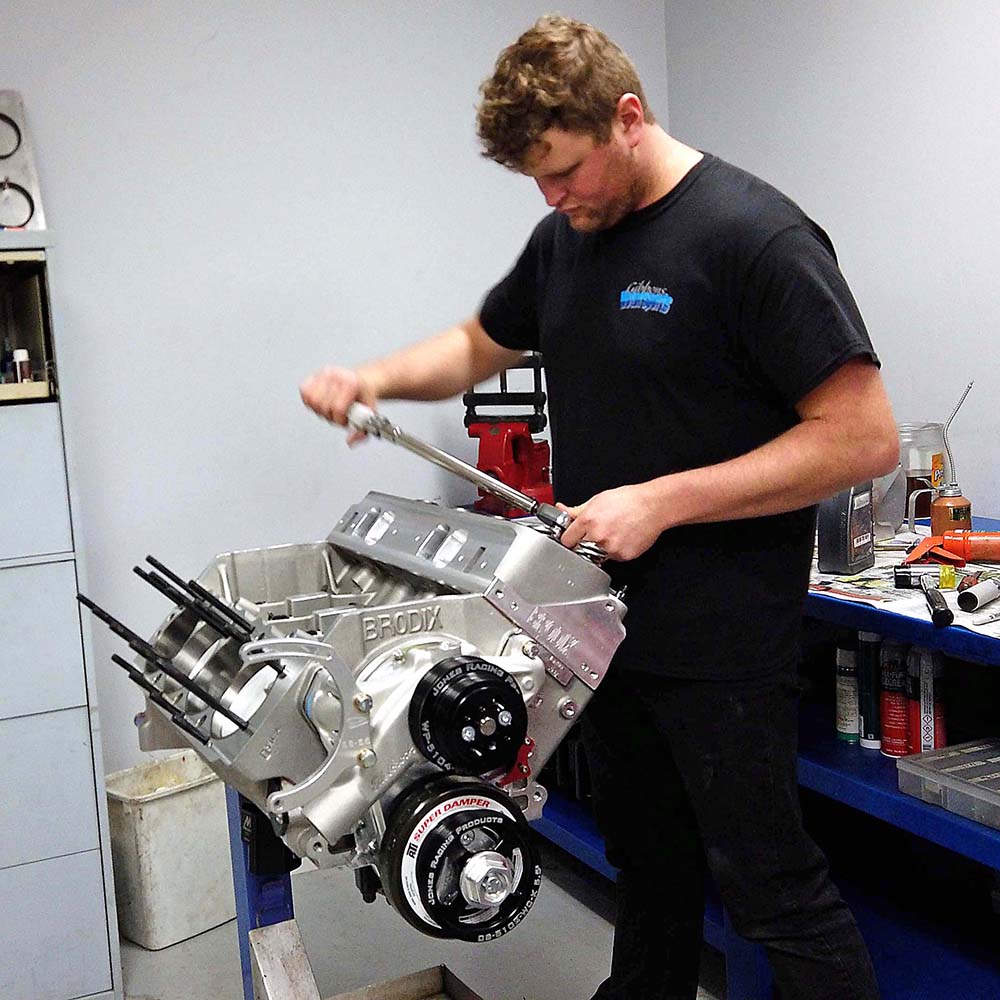
That brings us to the opportunity that allowed us to tell you this story. Gibbons Motorsports in Mooresville, North Carolina, specializes in high-performance engines. Located in the heart of NASCAR country, they do a lot of oval track racing engines, but their competition engine program includes drag racing, pulling, mud bogging, and just about everything else you can imagine. Of course, they also do high-performance street builds too, which is the engine you see here. Brothers Jake and Pete wanted to build a big-inch big-block for Jake’s personal C10 Chevy pickup they’re building in their spare time.
Originally, the plan was to build an all-aluminum big-block with relatively good power and adequate manners for an old truck. But as with most projects, plans changed and the horsepower potential grew quickly. It all started when the aluminum Brodix block showed up and the brothers found that the bores were larger than what they’d ordered. Of course, what horsepower fanatic is going to turn down the opportunity for more cubic inches? So, they kept the block and ordered up bigger pistons to match, and they ended up with a block sporting 4.600-inch cylinder bores. The crankshaft was already a forged stroker featuring 4.500 inches of movement for the pistons, which made the final displacement a healthy 598 ci.
Then they got a chance to get their hands on a pair of Brodix’s 24-degree fully ported cylinder heads and decided they wanted to give those a shot, too. Those heads move air and fuel like a firehose—we’re talking 365cc intake ports that flow over 460 cfm, so the intake manifold also needed to be upgraded in order to fully support it. And just like that the relatively mild build (their terms, most regular people would have called the original build plan a monster) turned into a high-rpm screamer capable of exceeding 800 hp on pump gas.
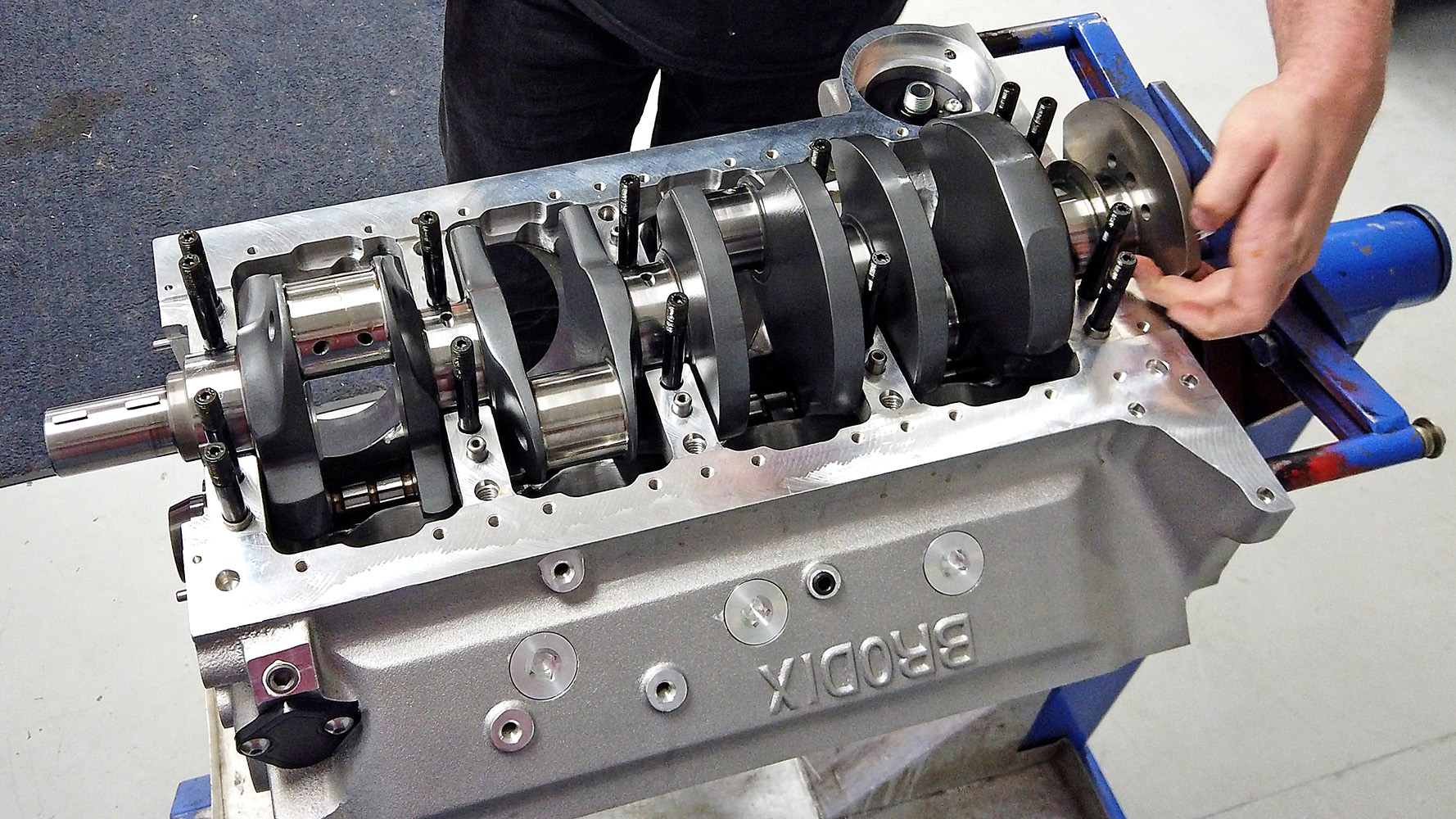
That all sounds awesome, and it is, but the problem was the camshaft had already been spec’ed out before all the unplanned upgrades were made. And it was also already sitting on the shelf. Pete and Jake knew the existing cam would be too small for maximum performance with all the revisions to the big-block, but they wanted to try it first and see how the engine responded before deciding just what changes needed to be made for an updated camshaft. And that’s how we were able to turn lemons into lemonade and make all of this into a very fun cam test.
Of course, the cam that they had isn’t small by any means. It is a 55mm core solid roller from Comp Cams. The cam is ground with 256 degrees of duration for the intake valves and 263 for the exhausts, measured at 0.050 inches of tappet lift. Lobe lift is 0.426 and 0.430 for the intakes and exhausts, respectively. That will make the gross valve lift 0.724 and 0.731 inches. The intake centerline is 110 degrees and lobe separation is 110. Also, the firing order is changed to an LS style, so it will be 1-8-7-2-6-5-4-3.
On the dyno the big-block performed well with the first cam, but we could tell there was more to be had. Jake and Pete ran the pull from 3,800 rpm to 6,600. We saw peak numbers of 742.6 lb-ft of torque at 5,200 rpm and 802.7 hp at 6,200. Averages across the pull were 680.2 torque and 676.3 hp. That sounds great, but the power drop-off after peak was a bit precipitous, which told us that the valves were closing too soon and not allowing the engine to breathe properly when it was starting to pick up steam in the upper-rpm range. Given the cubic inches, the flow capability of the cylinder heads and intake, along with the high-flowing Sniper Stealth 4500 throttle body capable of supporting 1,500 hp, this engine was capable of much more.
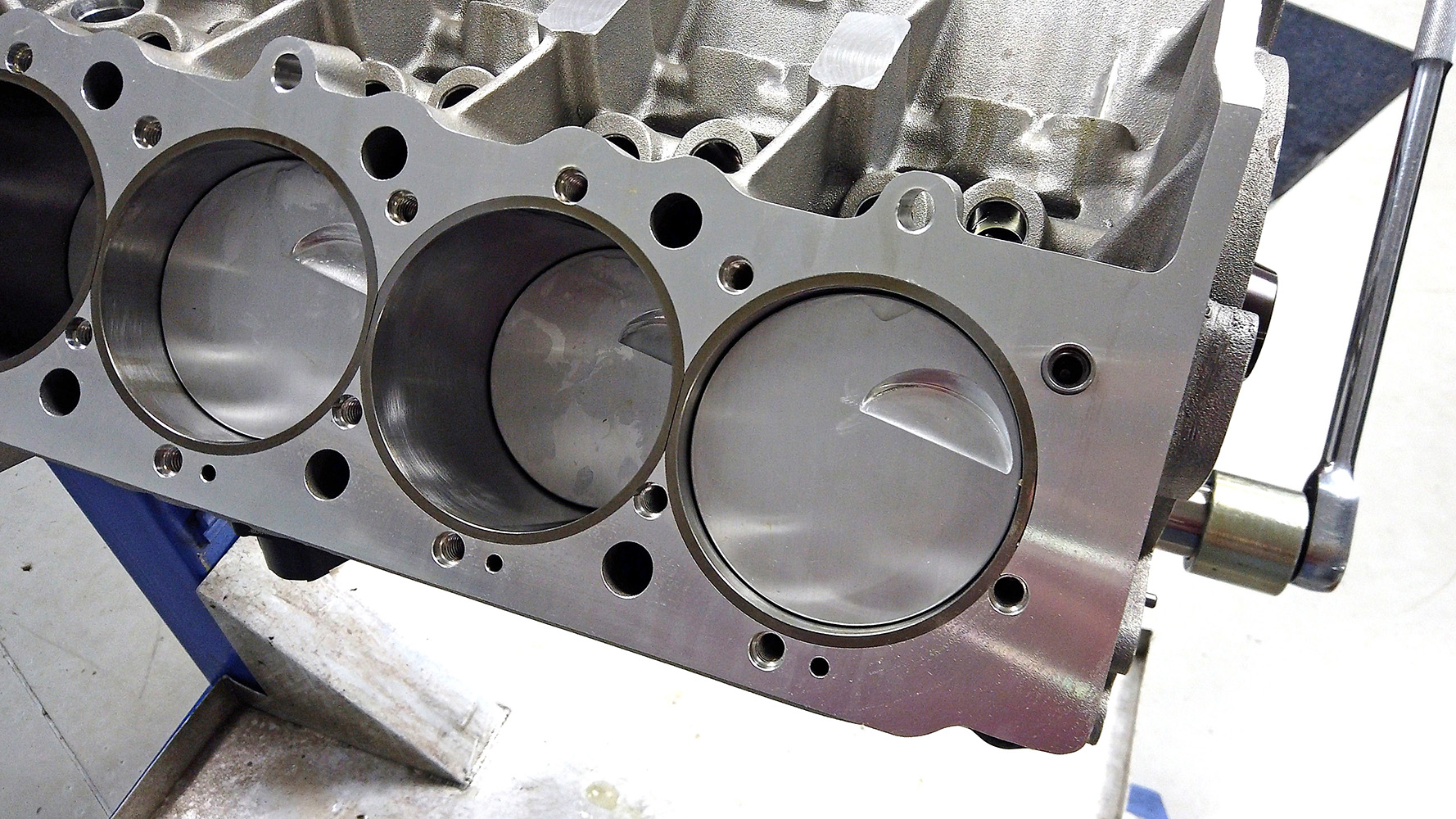
So, we went back to the drawing board. Pete and Jake worked with their contacts at Comp Cams and came up with an all-new grind. It is still a big 55mm-diameter core, still has the LS firing order, and still a solid roller. But now the duration at 0.050 inch of tappet lift is 271 and 284 (15 and 21 degrees bigger, respectively), lobe lift is increased 0.055 on both lobes to get to 0.481 and 0.485. So, with the same rocker arms, that will make gross valve lift 0.817 and 0.834 (recommended lash has been tightened up from 0.020 to 0.018). Finally, the intake centerline as well as the lobe separation has been moved to 114 degrees, which should help keep overlap manageable.
So, the new cam was installed in our big 598ci big-block and it was put back on the engine dyno. The brothers did have to cut the valve pockets a few thousandths deeper to keep the pistons from crashing into the valves thanks to the extra lift, but otherwise everything was kept the same. By the way, we’re burning 93-octane pump gas thanks to the 10.1:1 compression ratio, and the same brand of 15-50 break-in oil was used just to help keep everything the same.
On the dyno the differences were readily apparent even before we were able to make a power pull. Previously, the Holley Sniper Stealth 4500 EFI system had the engine fire up and idle smoothly right from the jump with zero issues. This time around the ECU struggled to get the engine to idle well. That’s almost certainly because the bigger cam kept the vacuum levels lower than the threshold for the Sniper system. The Gibbons brothers weren’t bothered by this, however. They said it could be handled with a little tuning work. That will be done once the engine is in the truck, and we didn’t worry about it on the engine dyno.
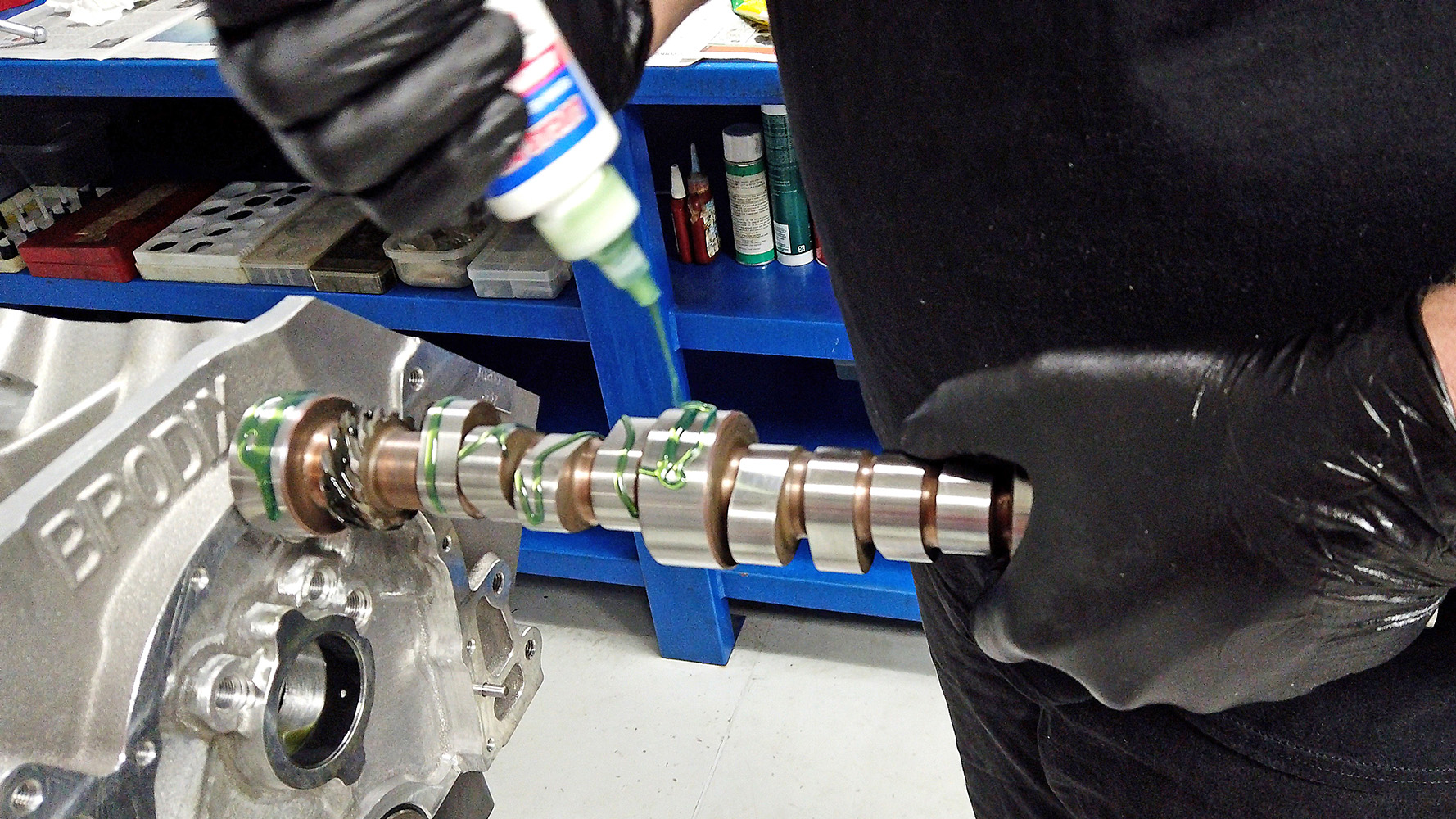
Then we were finally able to make some power pulls, and boy did things wake up! The big-block just continued to pull hard and make power well past the point it had given up previously. But the powerband shifted right on the dyno graph as well. This time around we saw peaks of 731.2 lb-ft of torque at 5,700 rpm (a loss of 11.4) and 863.8 hp at 6,600 rpm. That horsepower gain is an astounding 61.1, and although it isn’t exactly apples-to-apples because the rpm ranges are different, averages for both torque and horsepower improved to 688.5 (plus 8.3) and 787.5 (plus 111.2). That’s not a typo, the average horsepower improved by a hundo!
This is an astounding improvement, considering the only change was the camshaft. We even kept the same valvesprings for this run, although the increased lift did create greater open pressure and at peak lift the springs were closer to coil bind to help improve damping.
Some might complain that the test of our second cam doesn’t match the same rpm range as the test for the first cam. They do have a point, but the Gibbons brothers were more concerned with gaining real-world knowledge that they can use for future builds. They wanted to see the power curve around the peaks. Plus, the more power an engine makes the more damaging it can be to begin the pull too low in the rpm range. That’s why you’ll never see a dyno pull right from idle. It’s because an engine dyno limits the engine’s acceleration rate in order to accurately measure torque. In the lower rpm ranges, holding back acceleration at wide-open throttle creates tremendous cylinder pressure that can potentially bend rods and break pistons.
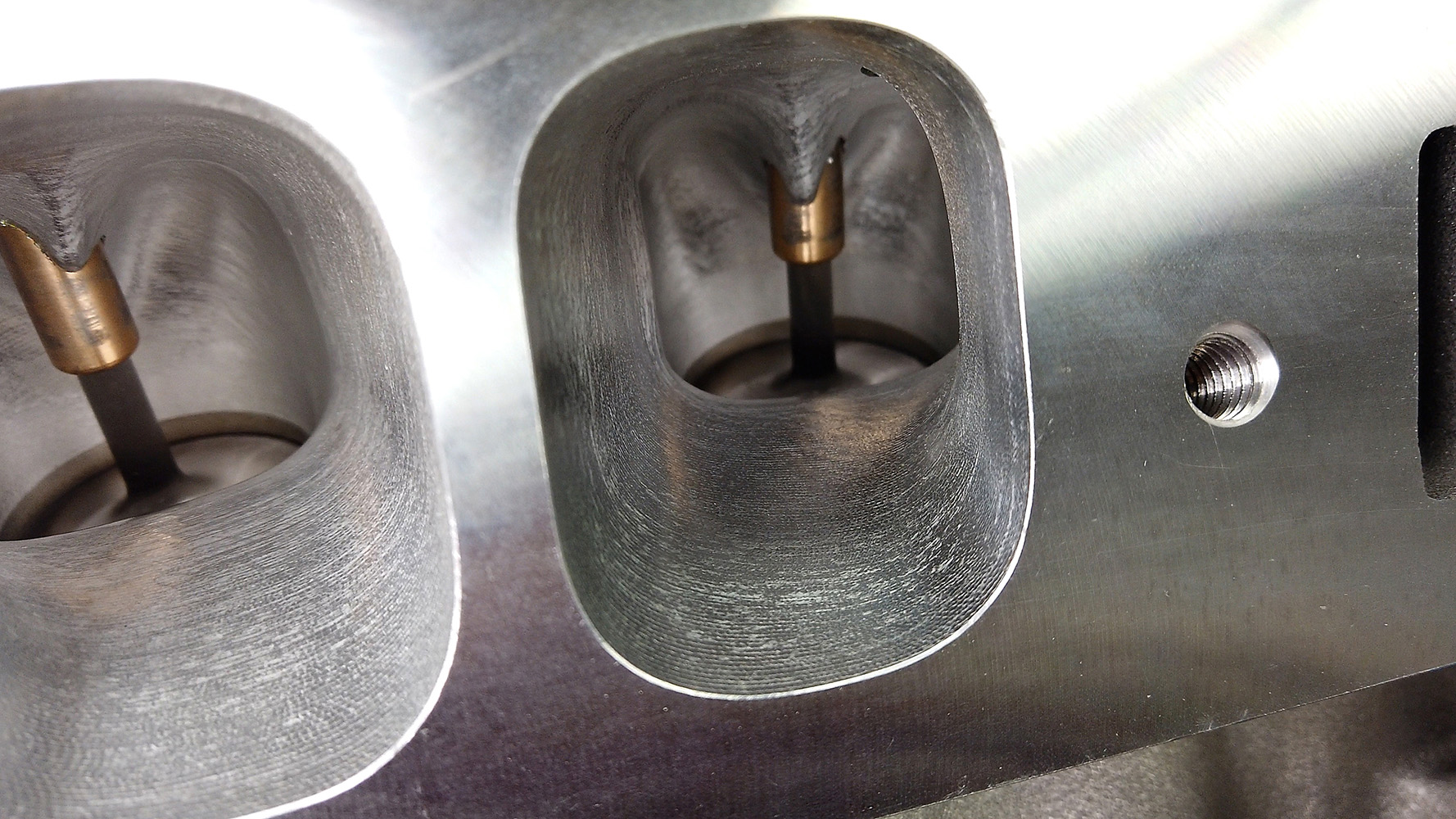
Still, by following the curve of the torque line, you can see that the engine almost certainly still produces torque in the mid 400s at 3,800 rpm—more than enough to spin the tires with a careless stab of the throttle pedal. By 5,500 rpm the second cam had surpassed the first in both power and torque, and it only increased from there. This engine is built for high-rpm performance, so it’s obvious that the second cam is the proper choice.
But this is only a single engine build for a specific purpose. What if you are building a big-block but want massive torque at low rpm for towing? Or a small-block with a turbo? Or any other number of builds. Honestly, besides professional engine builders, who can afford to buy a range of camshafts to dyno test which is best? Thankfully, the best cam companies have a wealth of experience on hand to help you determine what cam will work best for you. A high-revving, de-stroked LS6 with ported heads and a fabricated intake may be new to you, but they’ve probably seen something similar from their many customers a thousand times already.
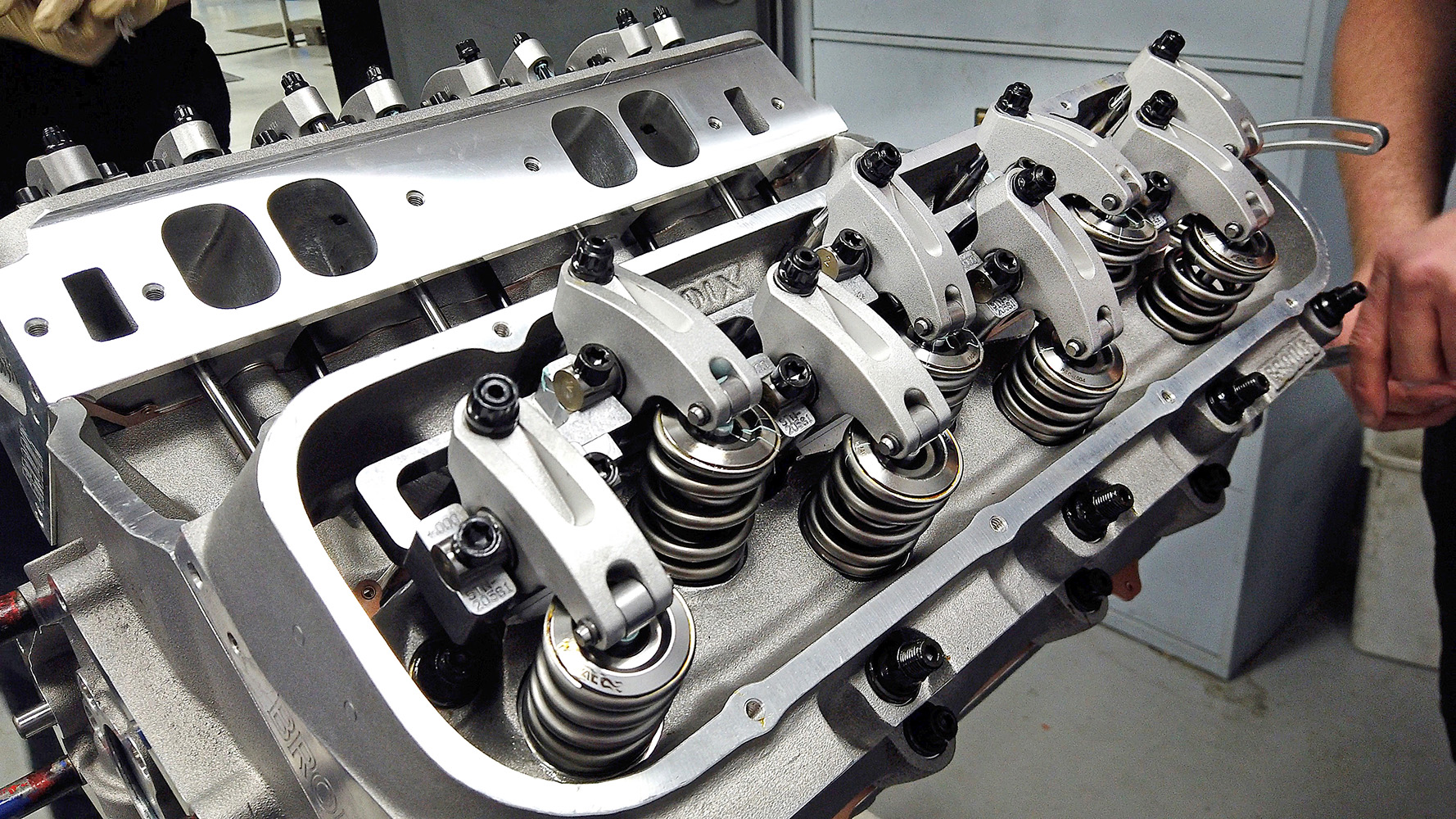
“The more information you can give us about your car and what you are trying to do, the better,” Chris Mays of Comp Cams explains. “We’ll start with the big stuff. Are you working on a race car or a street car? Is it naturally aspirated, supercharged, or maybe nitrous assisted?
“Then we’ll drill down from there. What size is the engine? What cylinder heads are you using and how much do they flow? If the car is already built, we’ll want to know about that. What rear gear ratio? How heavy is it? If you are running an automatic transmission, what torque converter stall are you running? The more you can tell us the better, then we can take all that information to help you make the best decision on cam choice.”
Mays says it is also quite common for him to spend time with a customer trying to improve on a cam choice that was maybe a little bit off. And, by the way, he can’t share names, but these are racers on every level. “We have had a lot of success helping customers get the engine response they need by dialing in the cam. Maybe they will say ‘It’s nosing over on the big end.’
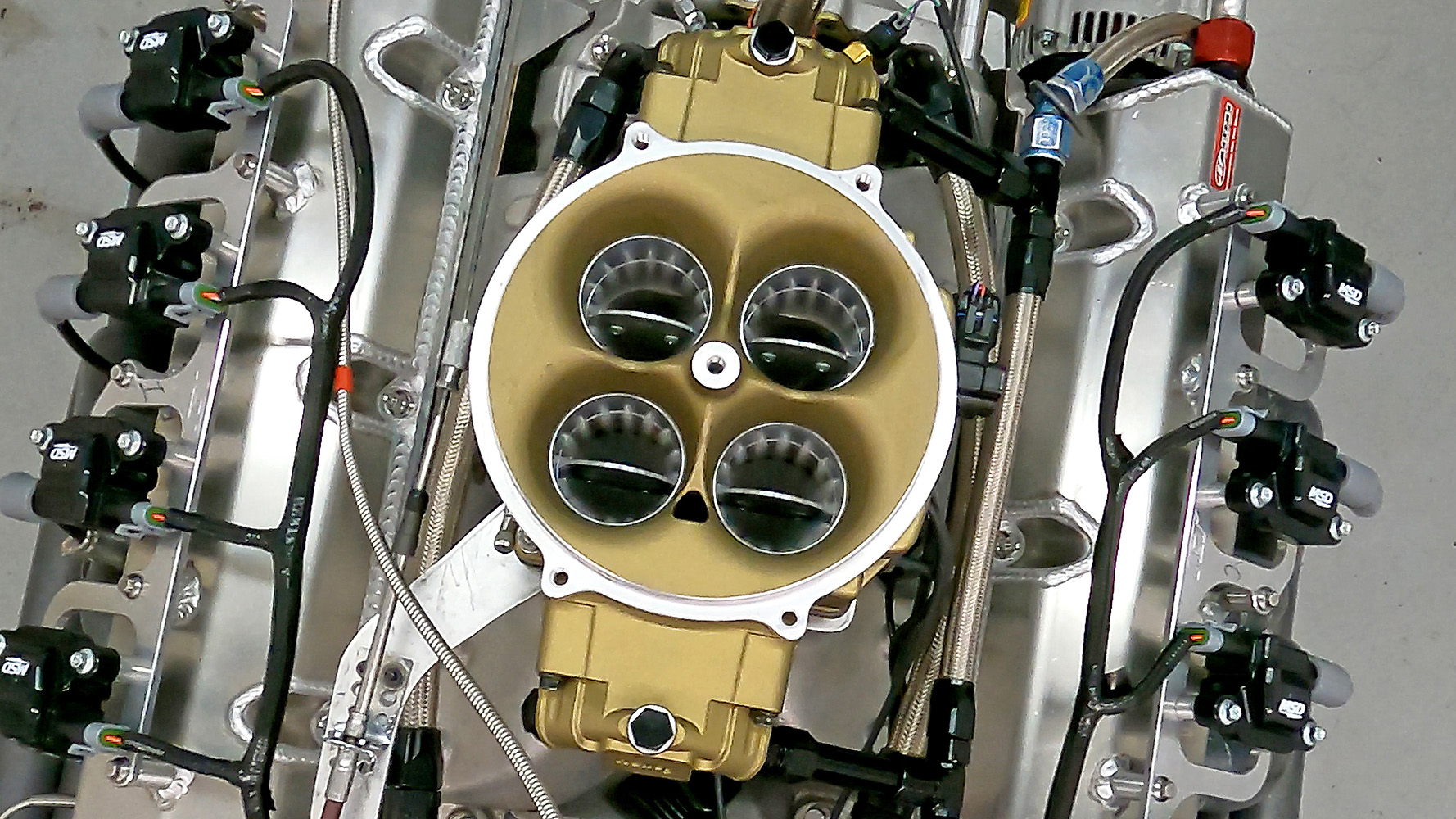
“Well, then we’ll look at maybe the lobe separation, is too tight and that’s making the torque curve too narrow? Or maybe the exhaust flow is too limited by the port and we can improve it by increasing the duration there?”
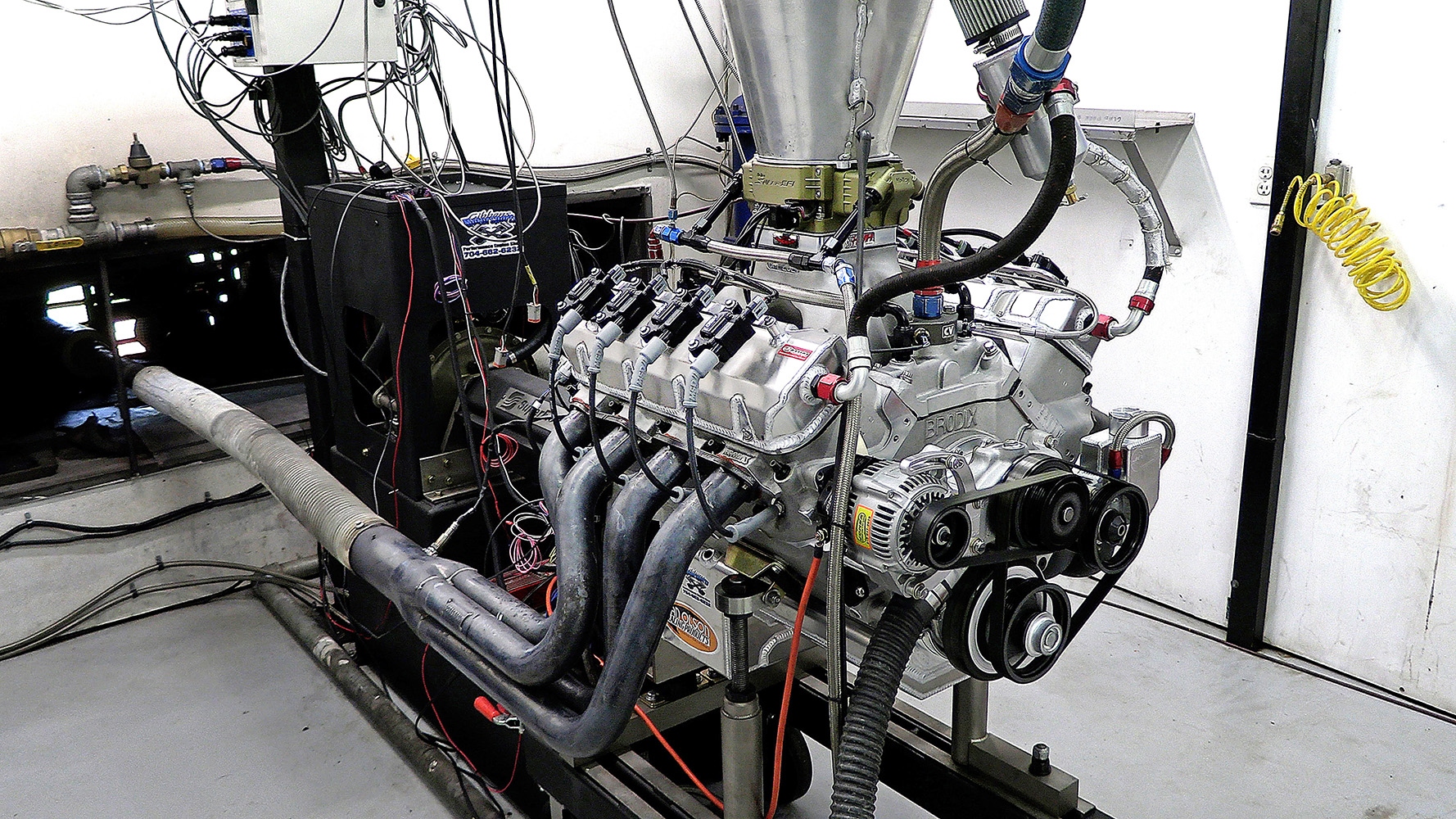
Mays points out that cam choice can also help improve mistakes in other areas. As an example, let’s say you’ve rebuilt your engine with a stroker crank and bored out the cylinders to get more cubic inches, but now dollars are tight and you’re forced to use the stock heads, which can’t flow enough air for the extra cubic inches. You can help that by swapping in a camshaft, which is much cheaper than new heads, with a bit more duration to help get more air and fuel into the combustion chambers.
Tale of the Tape | ||||
Cam #1 | Cam #2 | |||
Intake | Exhaust | Intake | Exhaust | |
Lash | 0.02 | 0.02 | 0.018 | 0.018 |
Duration at 0.020 Tappet Lift | 284 | 293 | 304 | 319 |
Duration at 0.050 Tappet Lift | 256 | 263 | 271 | 284 |
Centerline | 110 | 114 | ||
Lobe Separation | 110 | 114 | ||
Lobe Lift | 0.426 | 0.43 | 0.481 | 0.485 |
Gross Valve Lift | 0.724 | 0.731 | 0.817 | 0.824 |
On the other hand, if your engine is annoyingly weak off the line, you may be able to see improvements by going with a cam that has a shorter duration. That can improve the dynamic compression in the lower-rpm range and help improve the torque right off idle. It’s all a game of mixing and matching the many components in an engine to get them all working in harmony. It may be a bit overwhelming at first, but don’t worry, you can get there. And don’t be afraid to look to the experts for a little help.
“Just tell ’em to give us a call,” Mays says. “We’ll be happy to help.”
Check out this story in our digital edition here.
Sources
Comp Cams
(800) 999-0853
compcams.com
Gibbons Motorsports
(704) 662-6232
gibbonsmotorsports.com