Roof Inserts: Natalie’s Distinctive Deuce Coupe
By Ron Covell – Photography By Not Stock Photos and Courtesy of Craftworks Fabrication
Ford Model A coupes have an iconic look that has been considered a cool hot rod since people started modifying them back in the ’40s. A lot of builders chop the tops on these cars, and the original fabric insert in the center of the roof is often replaced by welding in a metal insert.
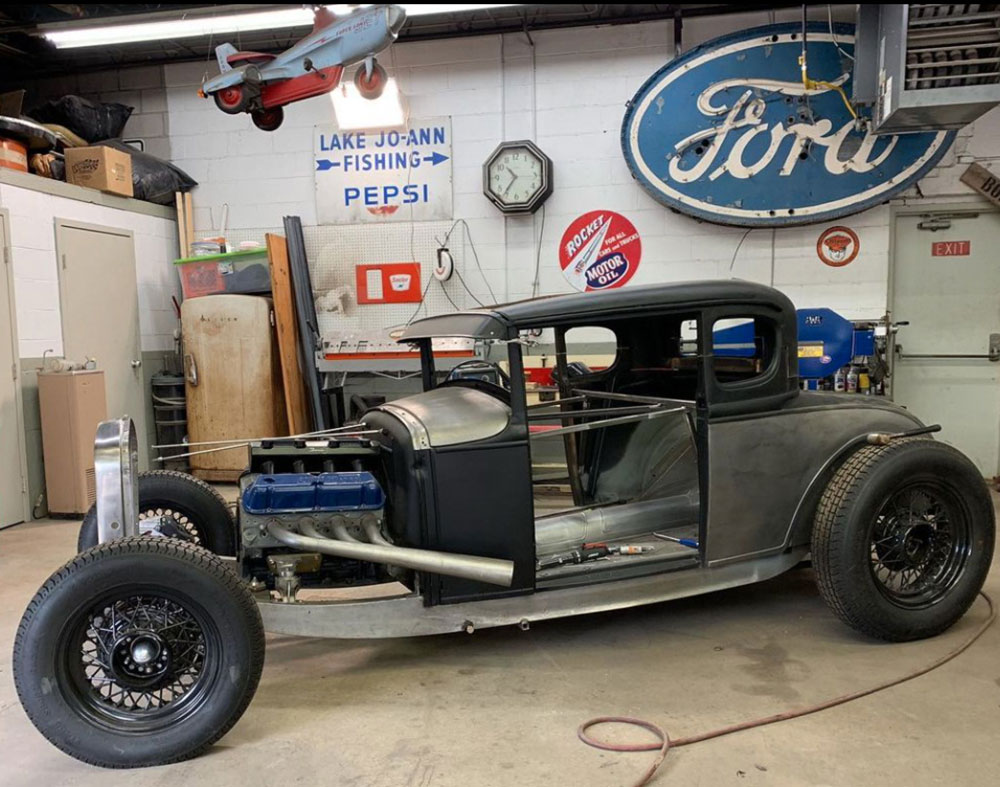
Natalie Bolea wanted a traditional model A coupe on a ’32 frame, but she wanted something that stood out from the crowd, so she contacted Craftworks Fabrication in Coraopolis, Pennsylvania, to get their take on it.
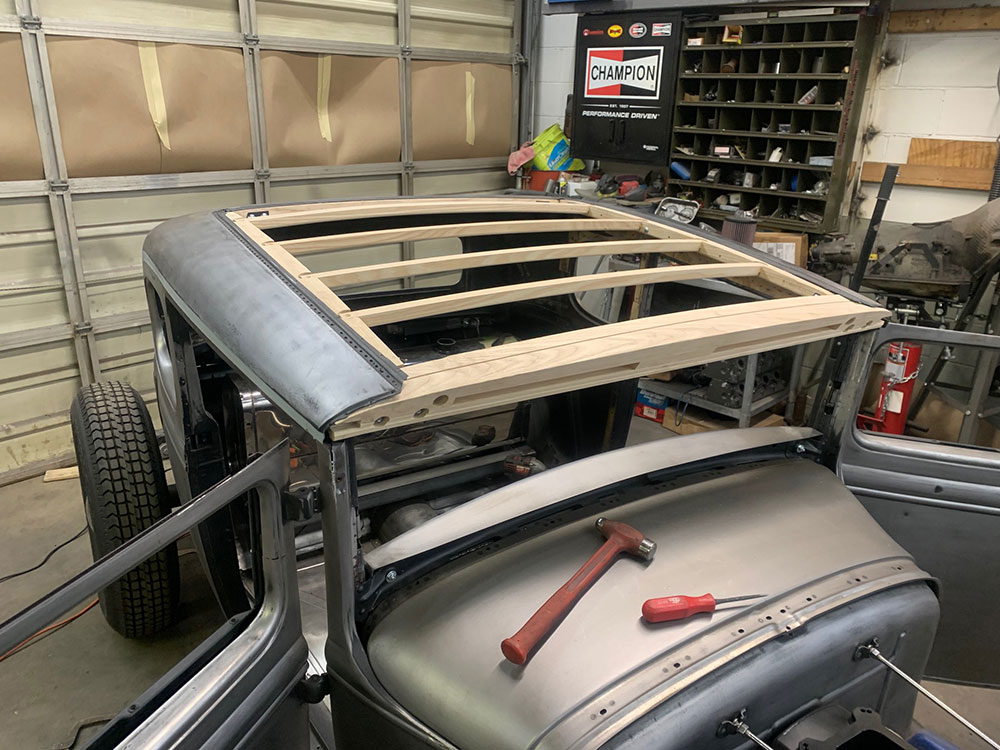
E.J. Talik, the proprietor, has a long history of doing finely crafted metalwork, and he loves to find unique ways to add style to his customer’s projects. The top would be chopped of course, but instead of welding in a metal roof insert, he thought it might add a point of interest to make the insert as a separate piece and give it a finish that contrasted with the paint scheme.
Read More: The Art of Channeling a Hot Rod
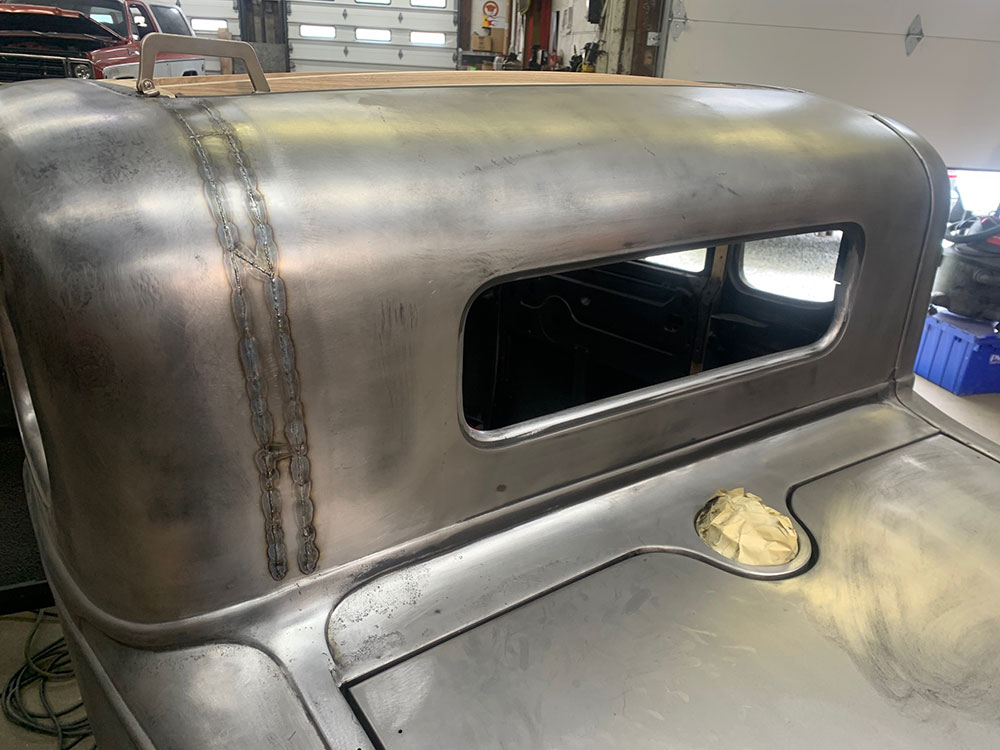
Taking the idea one step further, the fabric roof insert on the Ford Model A goes all the way to the windshield visor, but Talik hatched the idea of making the insert more like a ’32 Ford, which starts several inches back from the windshield.
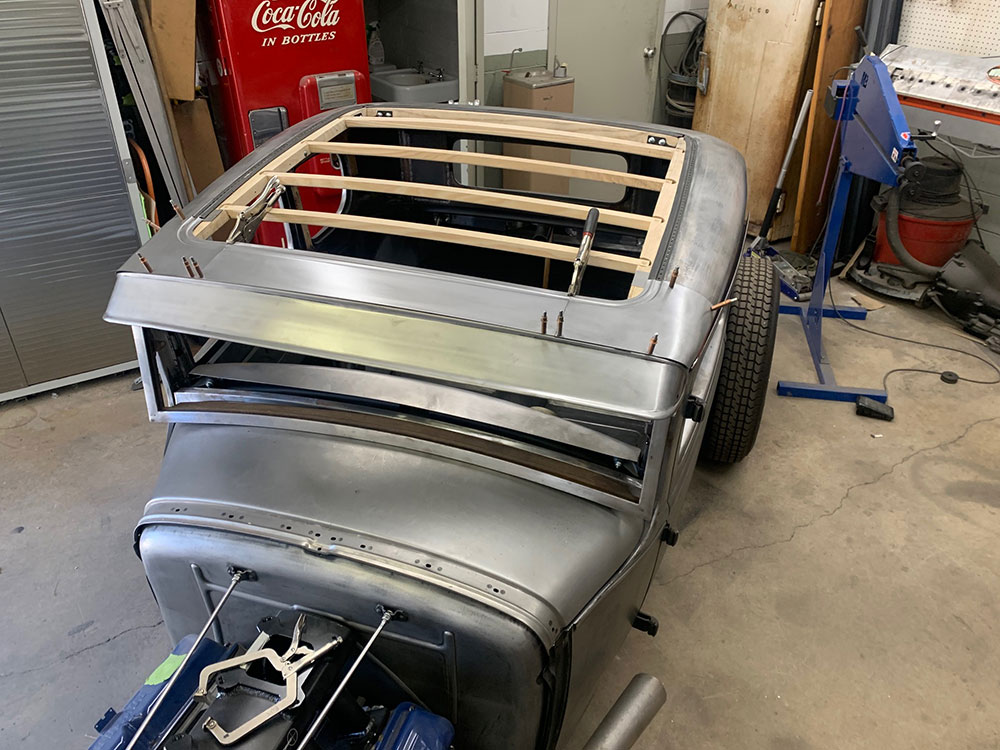
Bolea’s coupe has countless innovative details, which led to its being chosen by Goodguys as one of the Top 5 Hot Rods of the Year. We’ll focus on just the roof modifications in this article.
Read More: Hot to Replace a Ford Model A Rear Quarter Panel
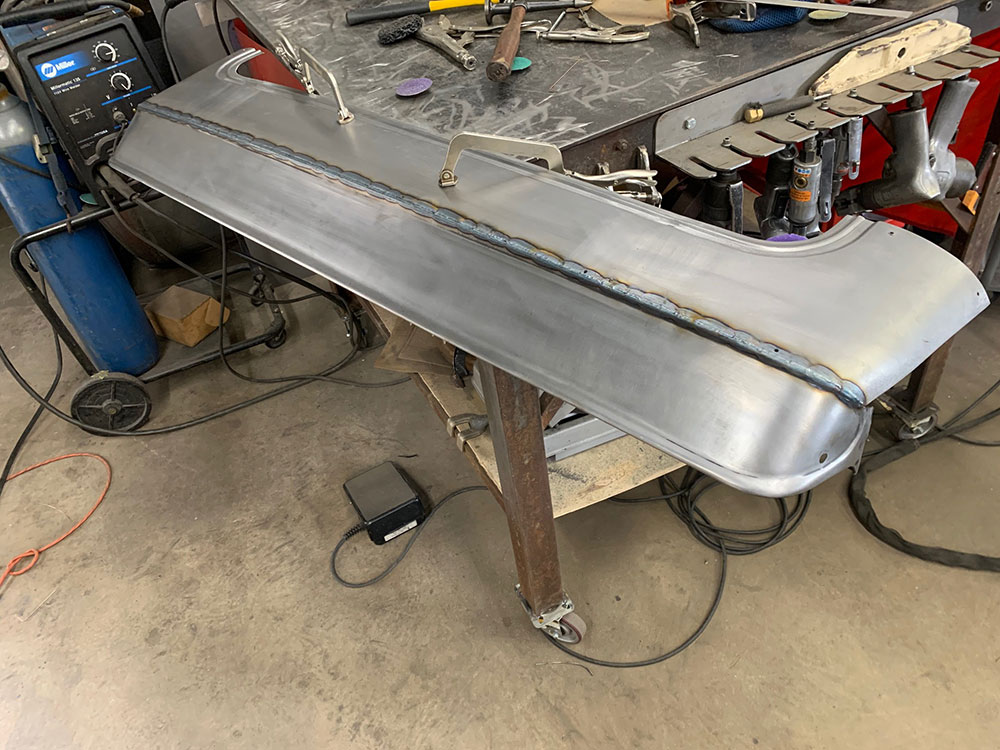
With a plan in place, the crew at Craftworks marked out the 4-inch top chop on the model A by laying down two stripes of 2-inch masking tape. The cuts were then made on the top tape line and the roof was removed. Next, the lower cuts were made, removing a section of the pillars and the rear roof panel.
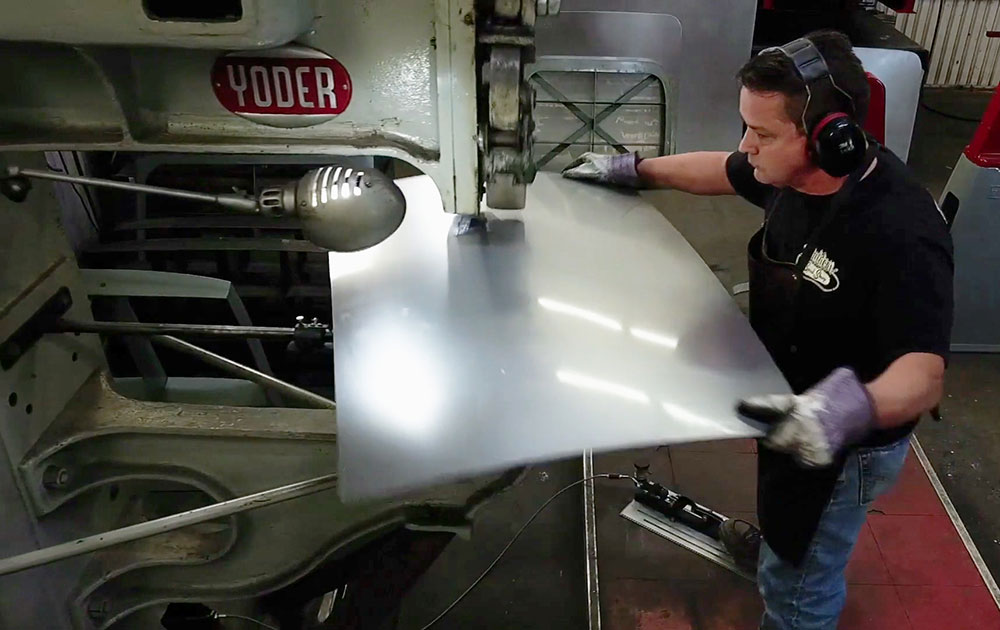
With the cutting completed, the roof was repositioned with its new, more aggressive stance and carefully welded back together. TIG welding was used exclusively for all the metalwork on this coupe.
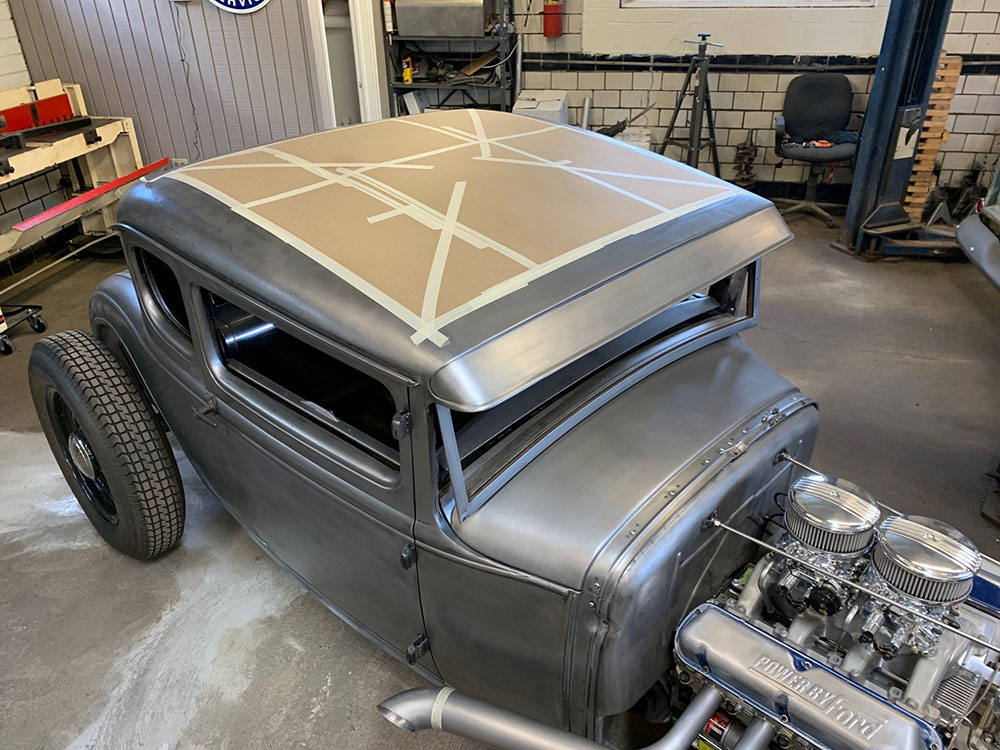
The visor was removed next. On the Model A, the visor is held to the inner wooden structure with nails that go into the wooden sub-structure. A new plan was needed to make the roof seamless, so new metal was formed to fill in the front corners of the roof, and a panel was fabricated that attached to the visor, bridging the gap between the corners. Each of these panels needed a step for the new roof insert to fit into, and it was demanding work forming these so they would tie in perfectly with the rear portion of the roof.
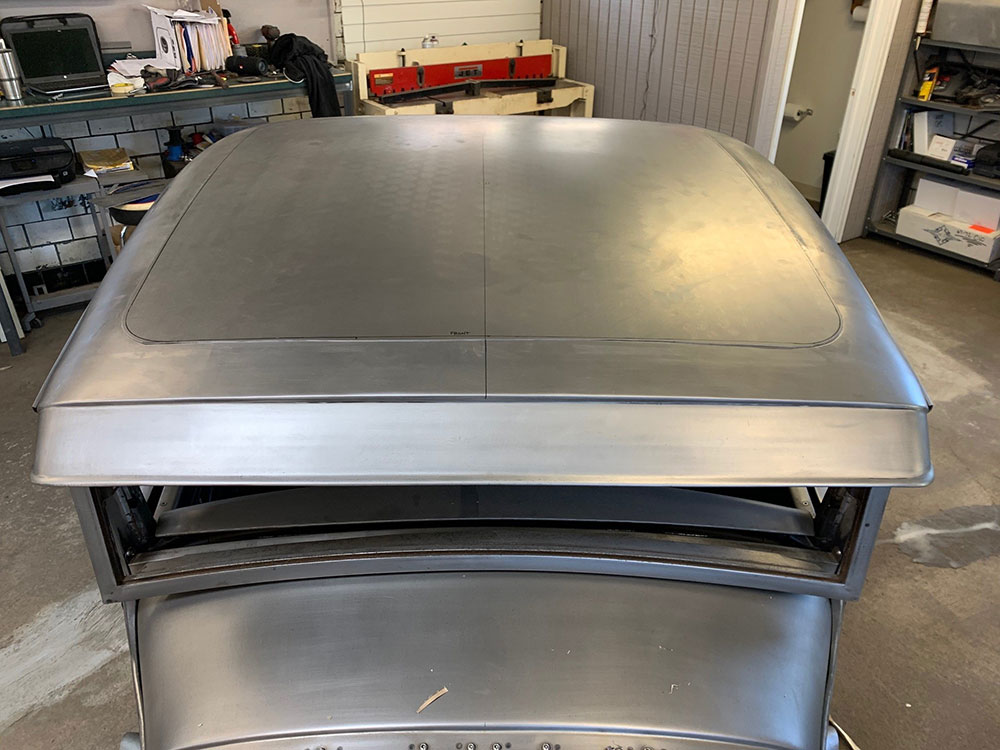
With the visor joined to the newly shaped metal, the assembly was fitted to the roof, welded into place, and metal finished. As you can see, the work is gorgeous and this detail really adds a unique look to the coupe.
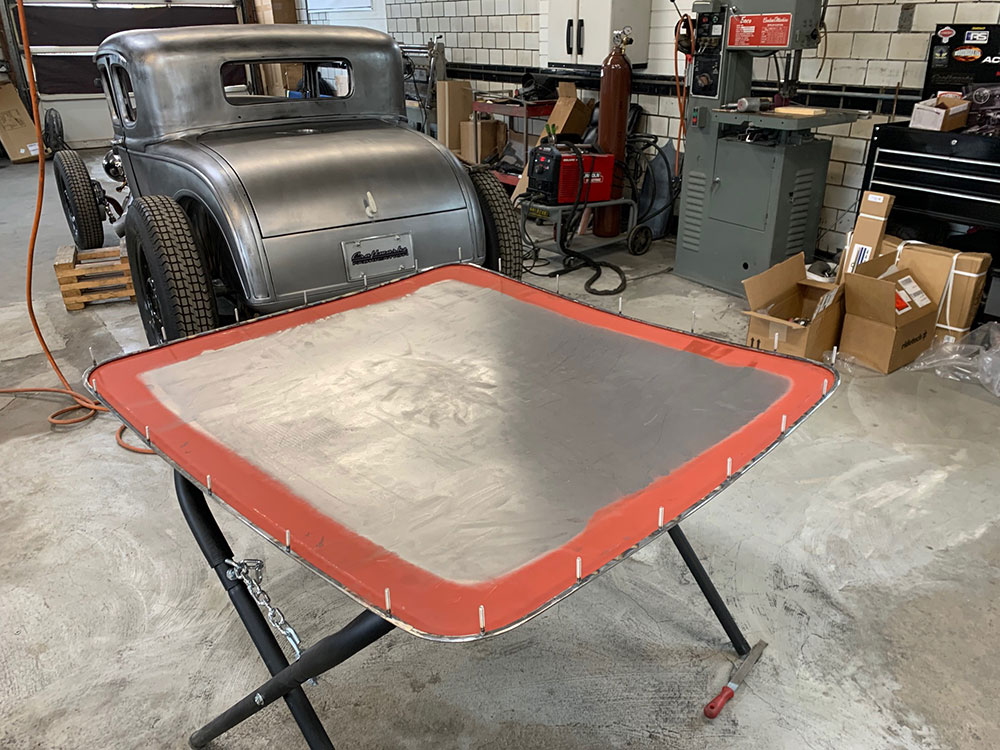
A shaped roof insert was purchased from Walden Speed Shop, and a paper pattern was made to fit the opening in the roof, so the insert could be trimmed to fit perfectly. A Mittler Bros. bead roller was used to make a bead around the perimeter of the insert, giving it some style.
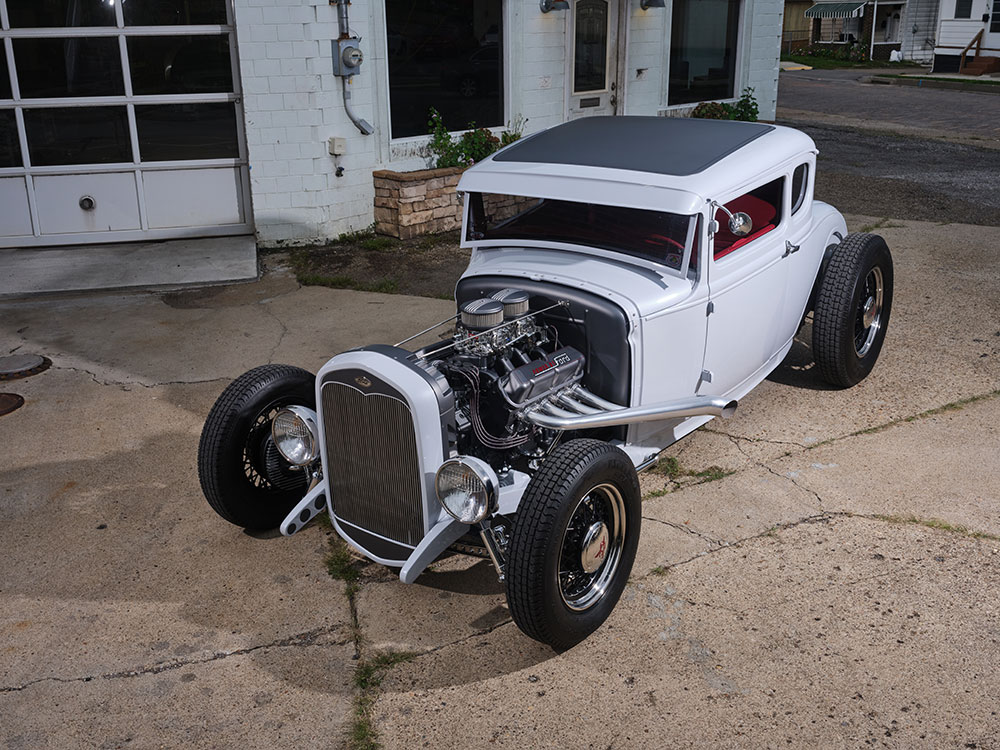
Once the insert was perfectly fitted to the opening, a ½-inch strip of steel was fabricated to fit around the perimeter and numerous studs were welded to it, which allows the insert to be pulled down securely into the recess. This strip was edge-welded to the bead on the outer border of the insert.
Read More About: 1930 Ford Highboy
There are lots of other details that help make the roof of this deuce coupe special, which you’ll see in the accompanying photos. MR
Source
Craftworks Fabrication
(412) 922-7062
craftworksfab.com