Welding Up Unwanted Holes
By Ron Ceridono – Photography by THE AUTHOR & Tim Foss
Regardless of whether a classic truck is being modified or restored, chances are that during the bodywork phase of the project there will be holes in the sheetmetal that will have to be filled. As a general rule (keeping in mind there are extenuating circumstances), small holes less than a 1/4 inch in diameter can be filled by welding only; bigger than a 1/4 inch a copper backup plate should be used. Holes 3/8 inch and larger should have plugs welded in place.
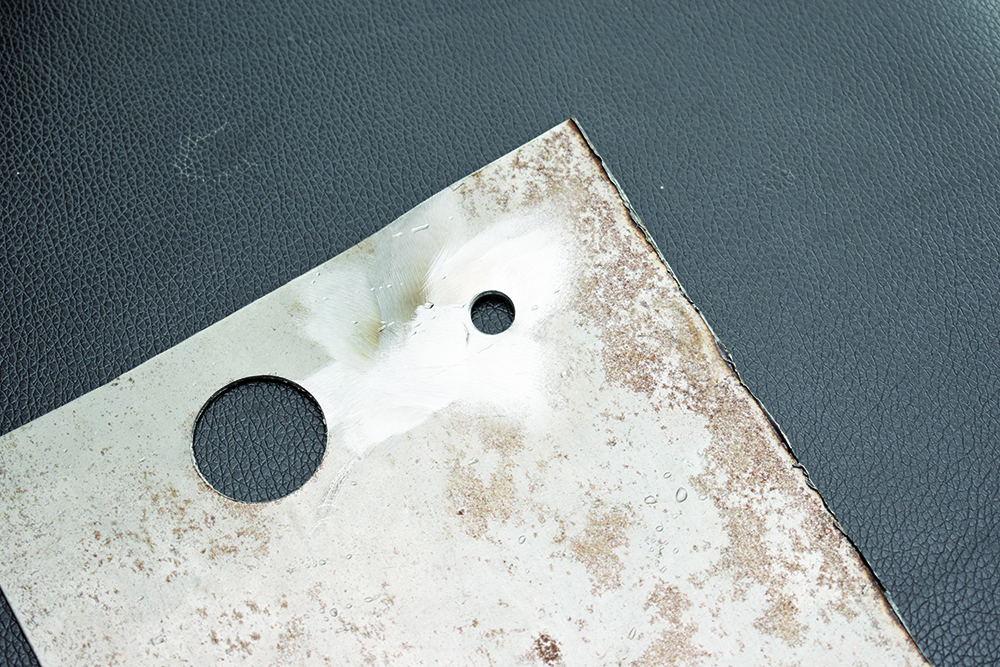
Now the extenuating circumstances. First is the type of welder being used. The key to success is to use as little heat as possible, so despite what you may see in some of the older magazines, oxyacetylene welding should normally not be considered. That leaves MIG and TIG welding, which both work well, but most hobbyists will rely on a MIG welder because wire welders are most commonly found in home shops. Another factor is ability; if you’re an experienced welder, filling holes shouldn’t be too difficult. If you’re new to welding, drill holes in some scrap sheet and practice filling them. You’ll soon discover that controlling the amount of heat that is put into the metal is one of the keys to success. Too much heat will cause the metal to warp; that has to be avoided because it can be very difficult to repair, particularly for a novice.
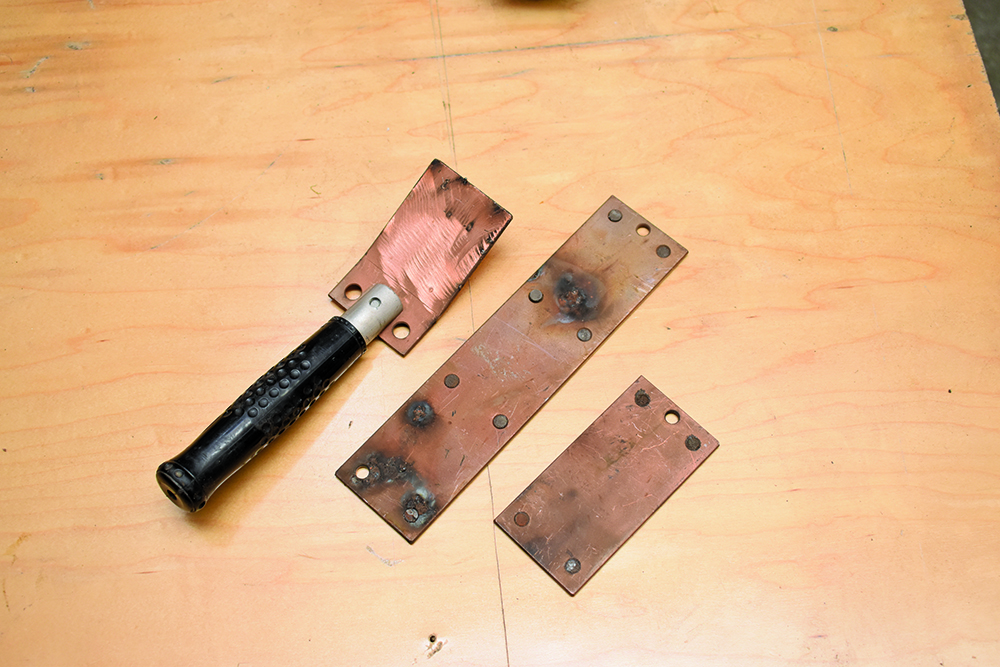
Another consideration when filling holes is not to stack up a huge bead that requires a great deal of grinding. Keep in mind grinding can also create heat that may cause the area to distort. Another common mistake is grinding too much, making the area surrounding the weld thinner than it should be. The idea is to level the weld bead to match the surrounding metal and no more.
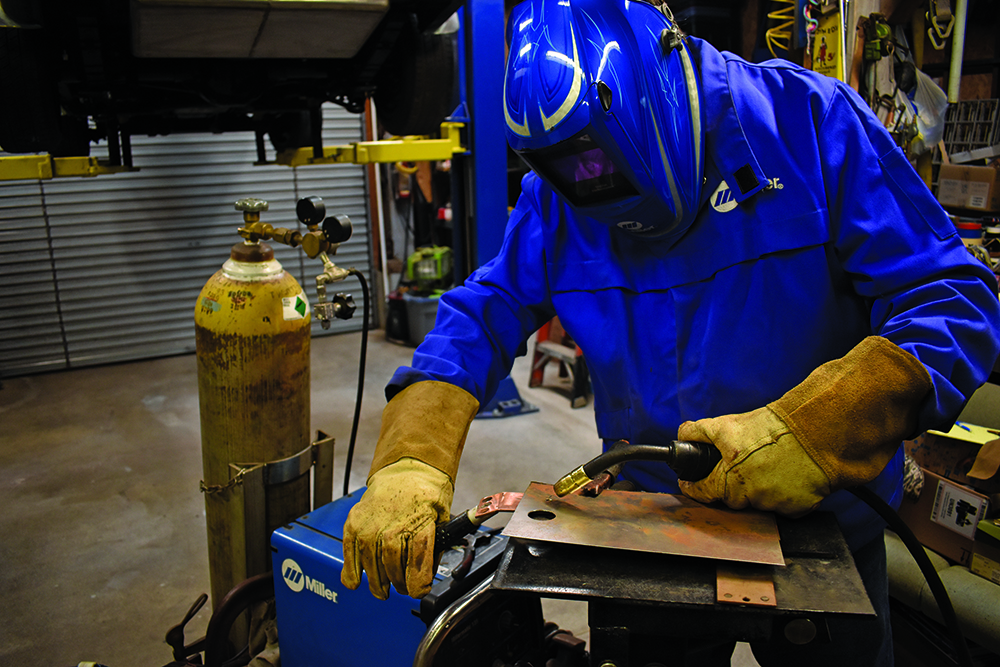
To demonstrate two different techniques we watched as Paul Wilson filled a hole in sheetmetal with a copper backup plate and his Miller MIG welder. Given the variations in welders and individual preference it’s impossible to recommend machine settings. The best advice we can offer is again to practice on scrap material that matches the thickness of the vehicle you’ll be working on.
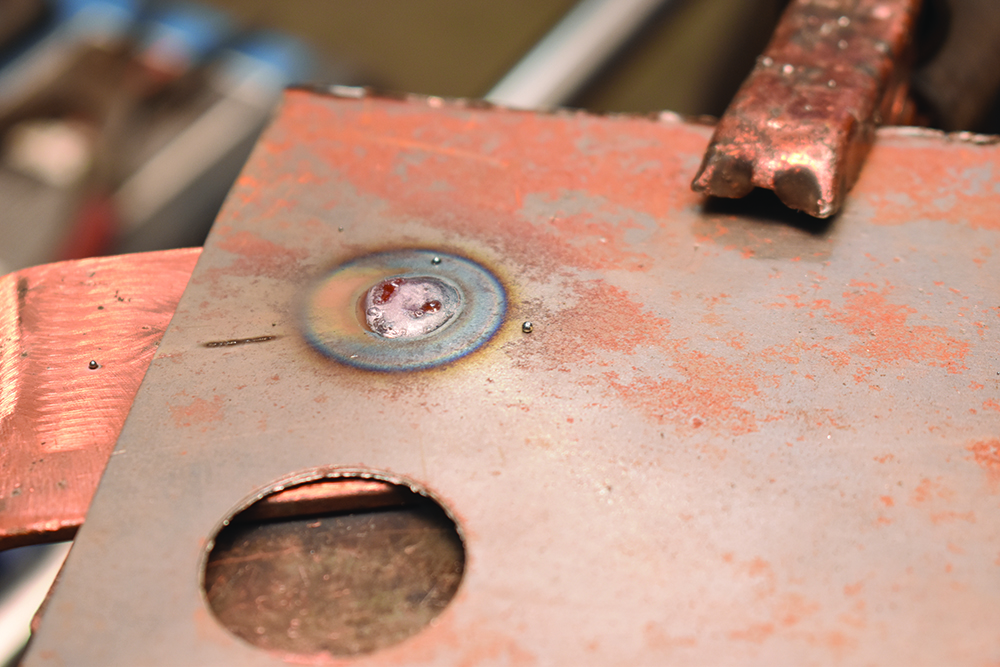
Filling small holes is usually done by making small tack-like welds around the edge of the hole, working your way to the center (it may help to slightly countersink the hole). Work slowly and try to keep the weld as flat as possible. If there is access to the backside of the hole being filled, copper backup plates, like those shown here, are particularly helpful.
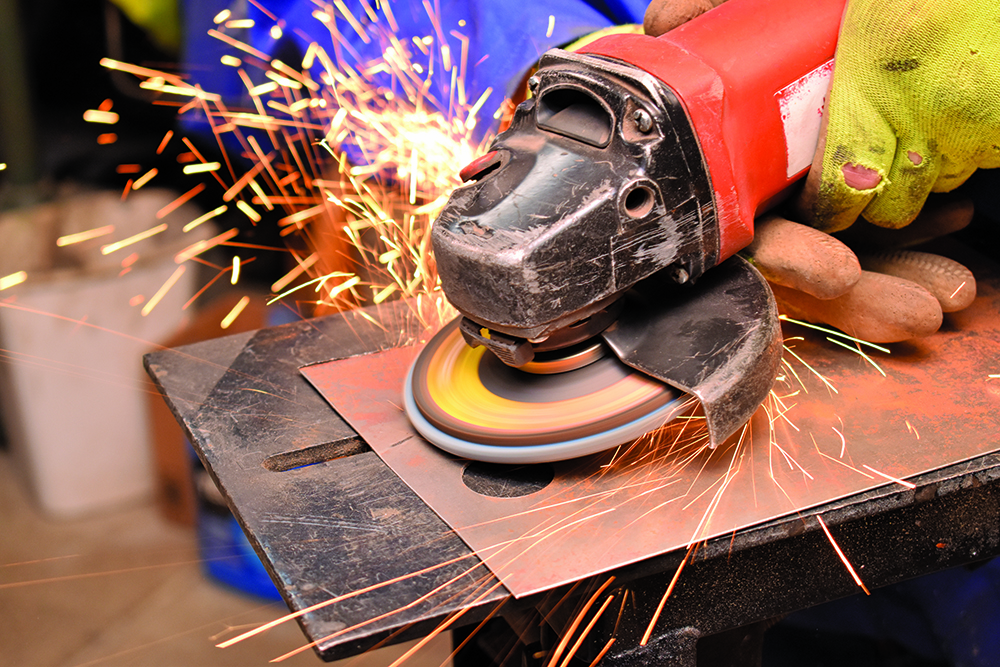
For larger holes, filler plates will be required. Tim Foss followed Kev Elliott, of Kev’s Rod & Custom, as he plugged the gas filler opening in a ’72 Ford pickup with a gas filler delete plate from LS Fabrication. Made from laser-cut, 16-gauge steel, the filler plate is contoured to match the contours of the cab.
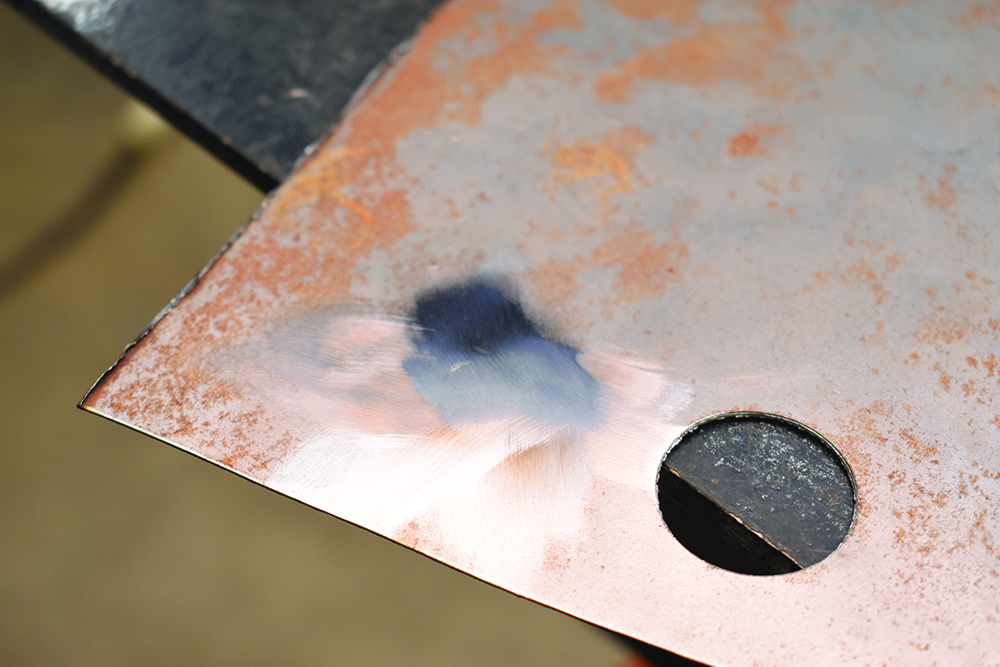
After preparing the area to be welded, Elliott went about tack welding the filler plate in place with his TIG welder. A few deft taps with a body hammer had the filler plate fitting perfectly—after that the welding was completed and then ground smooth.
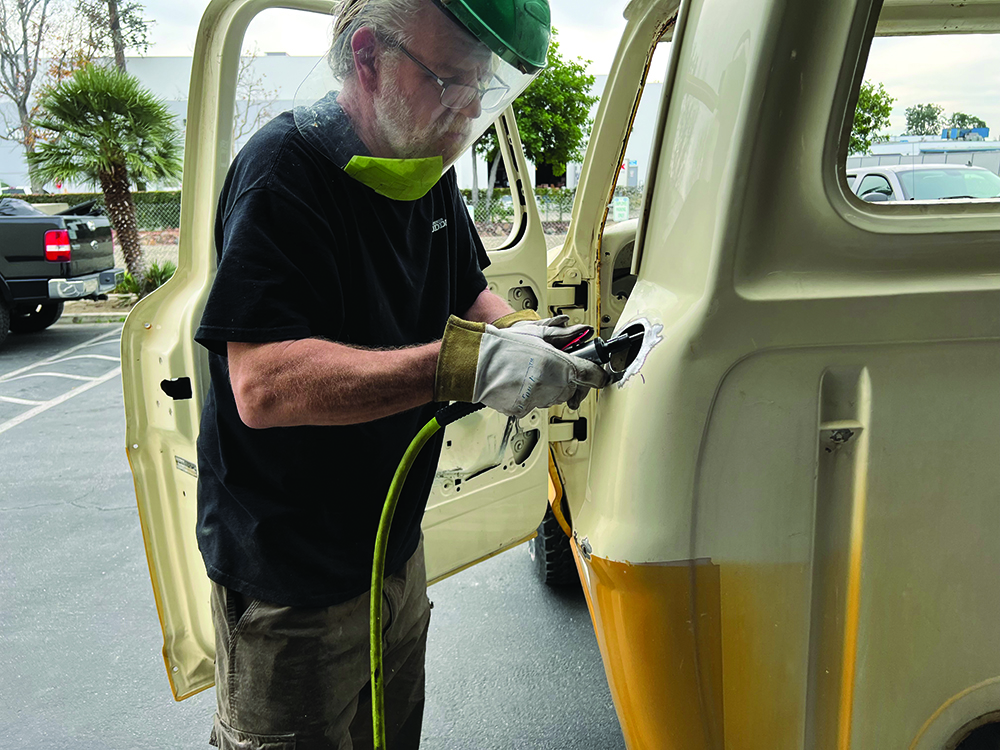
Remember when filling multiple holes move around to keep from concentrating too much heat in one area, try to keep the weld bead height to a minimum and use restraint when grinding. Filling holes in your hauler can be intimidating at first, but with patience and practice it is a skill that you can master.
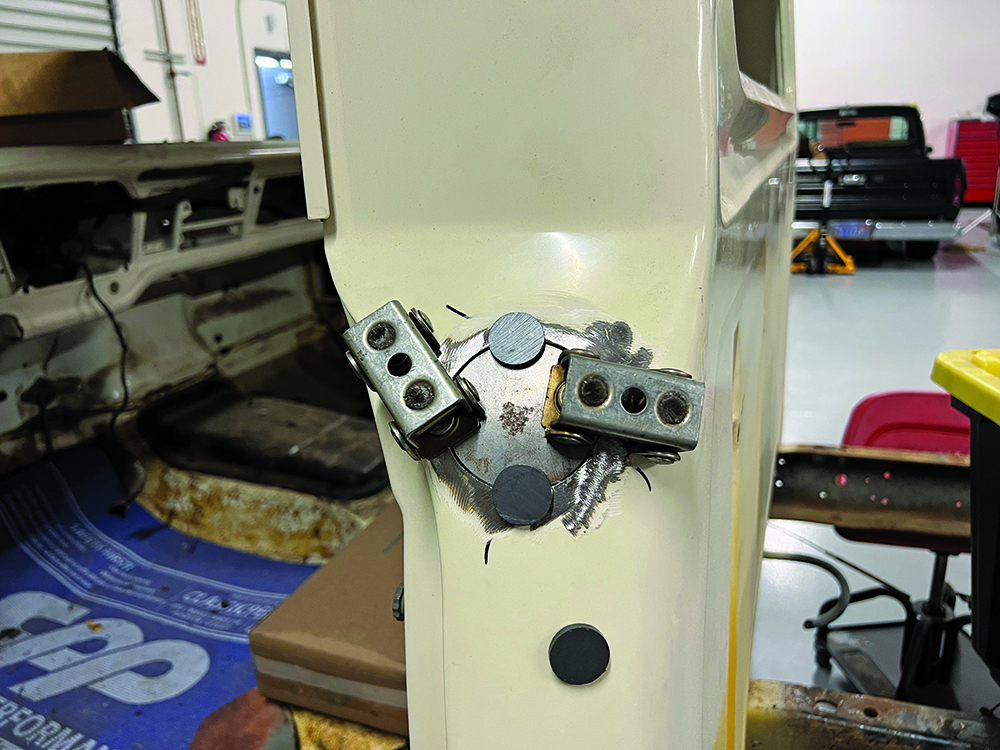
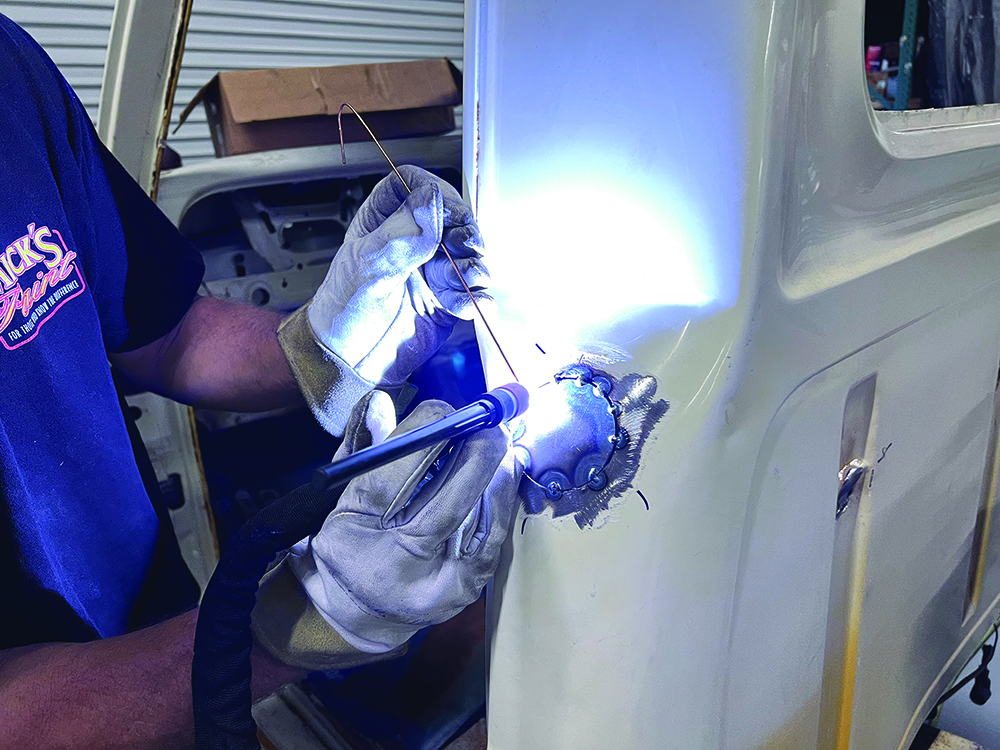
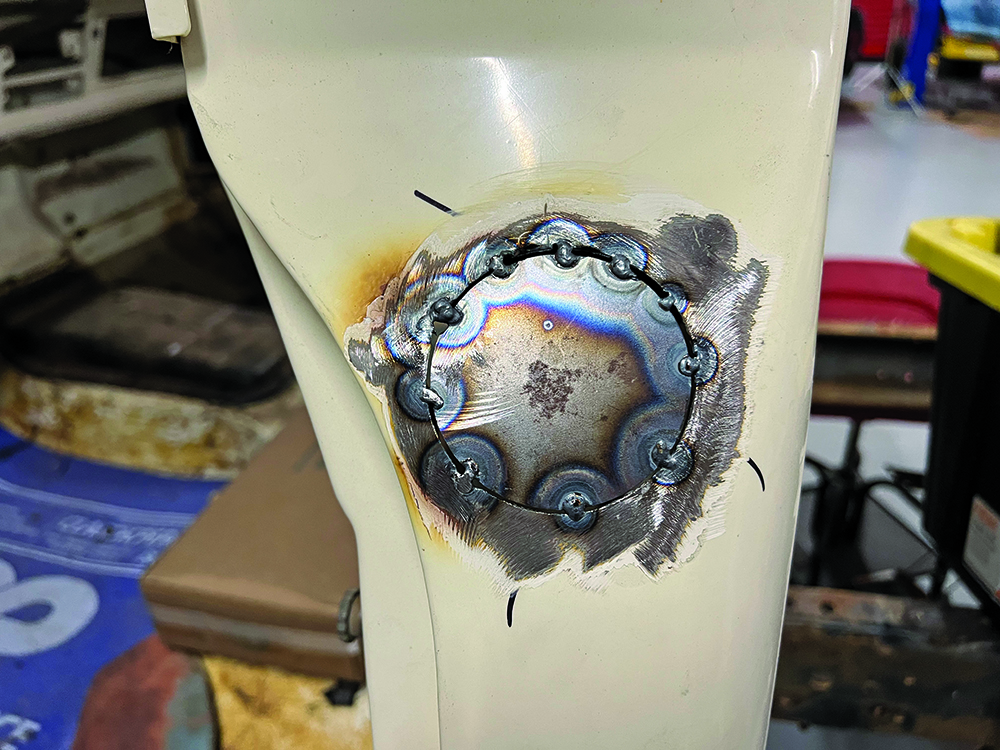
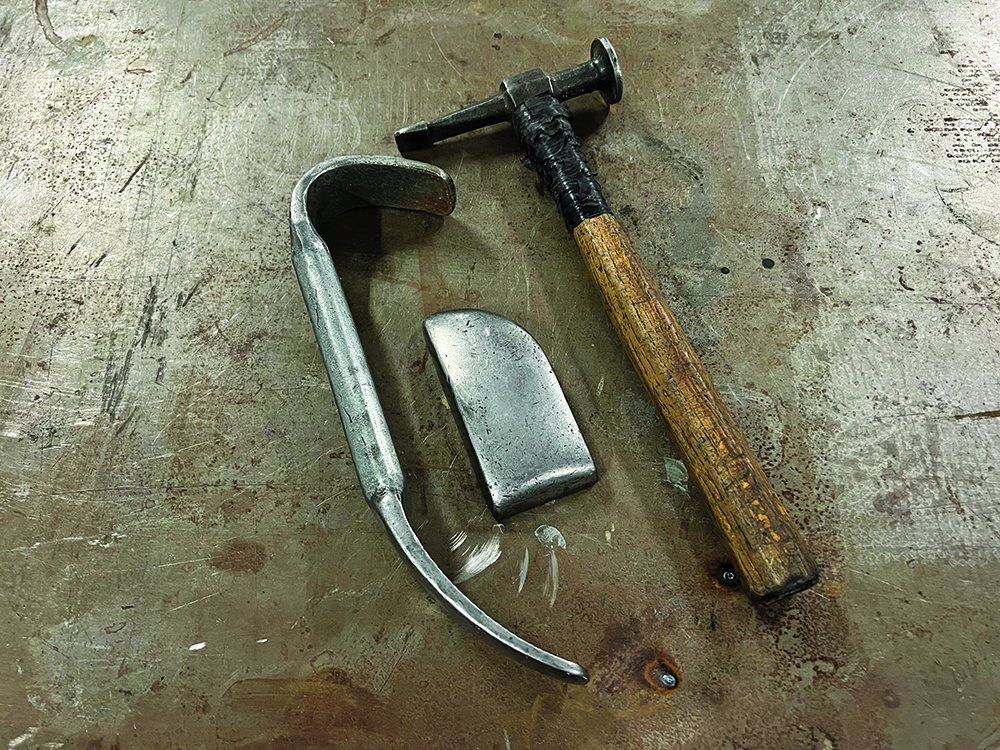
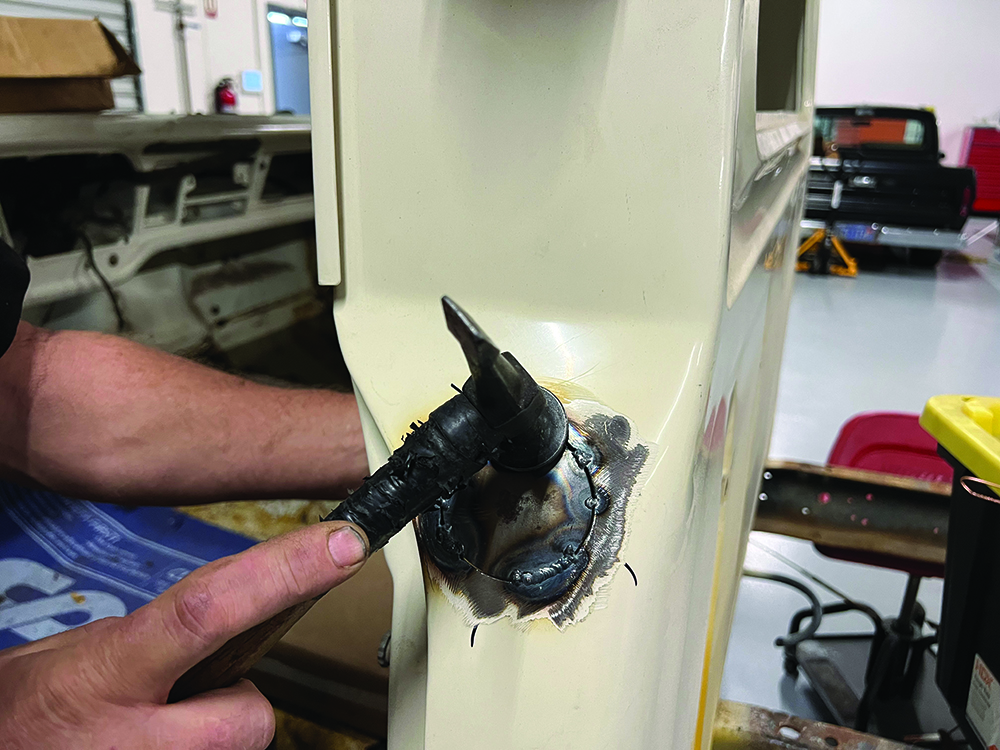
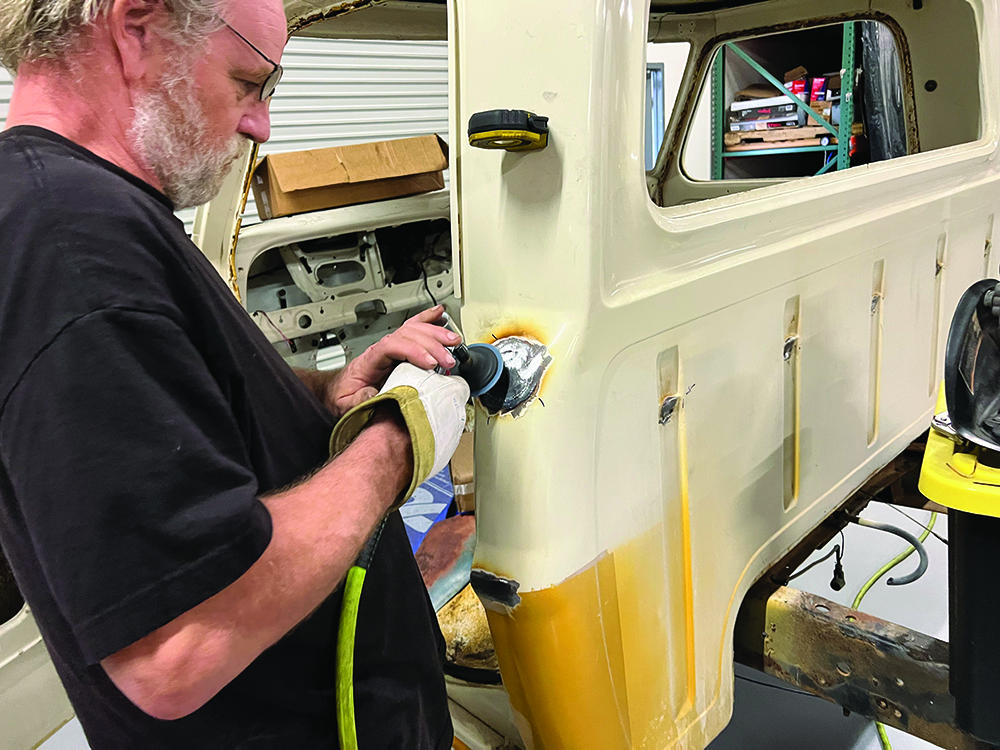
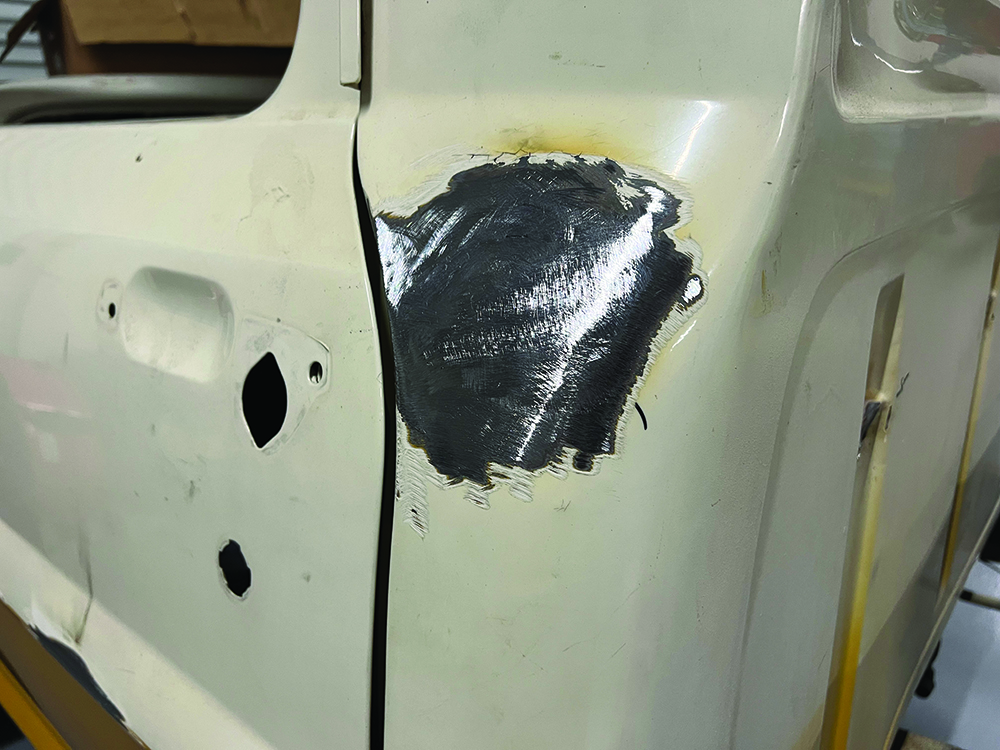
Things You Should Have in Your Toolbox
Here are three examples of sheetmetal tools you should have in your garage. We dug these out of our toolbox and grabbed some random scrap metal pieces to show how they are used.
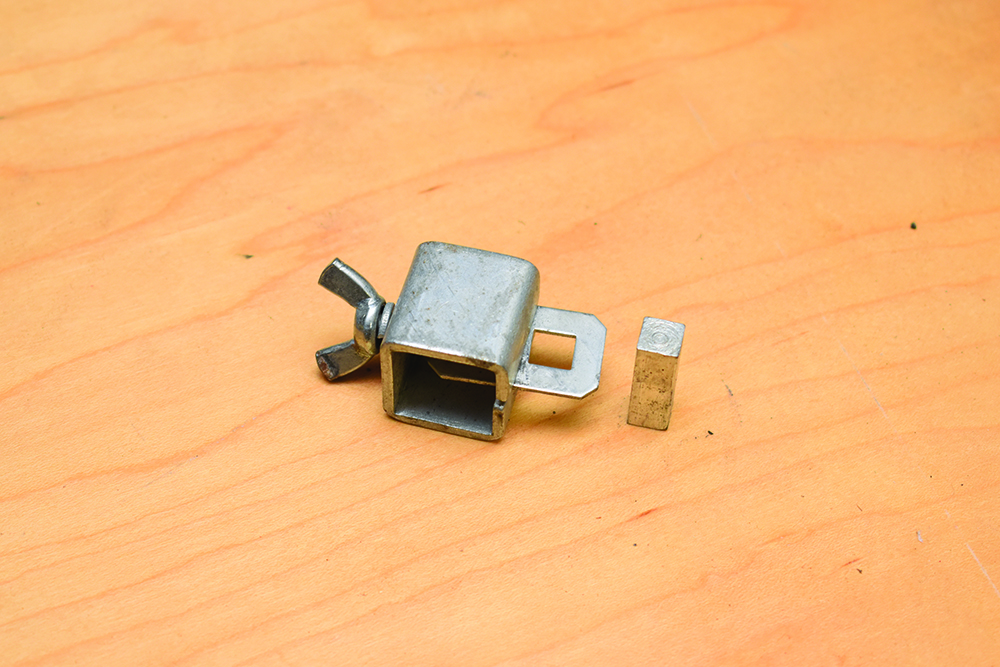
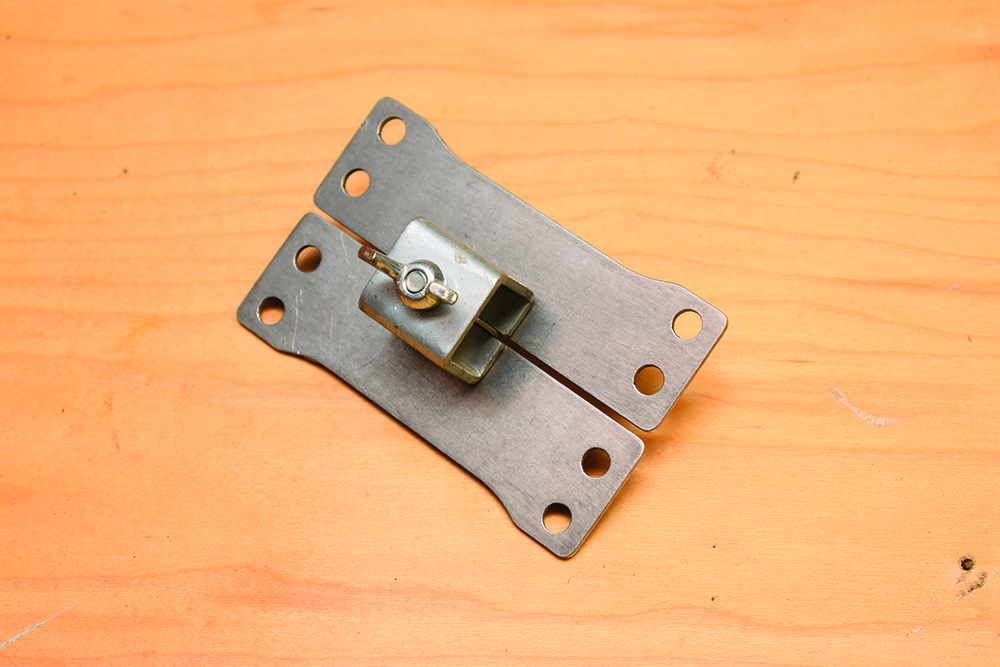
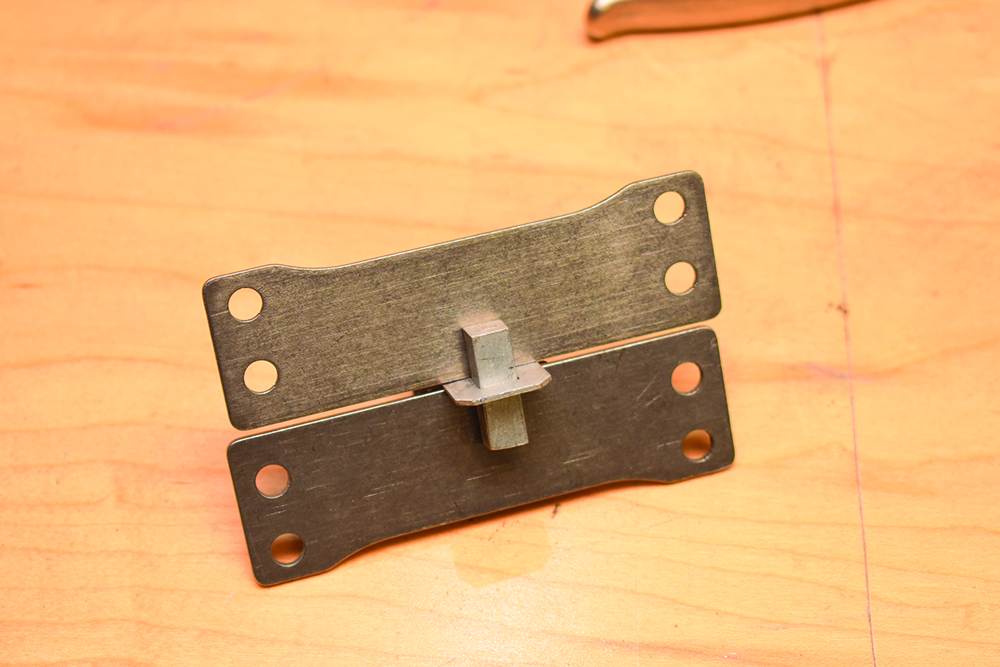
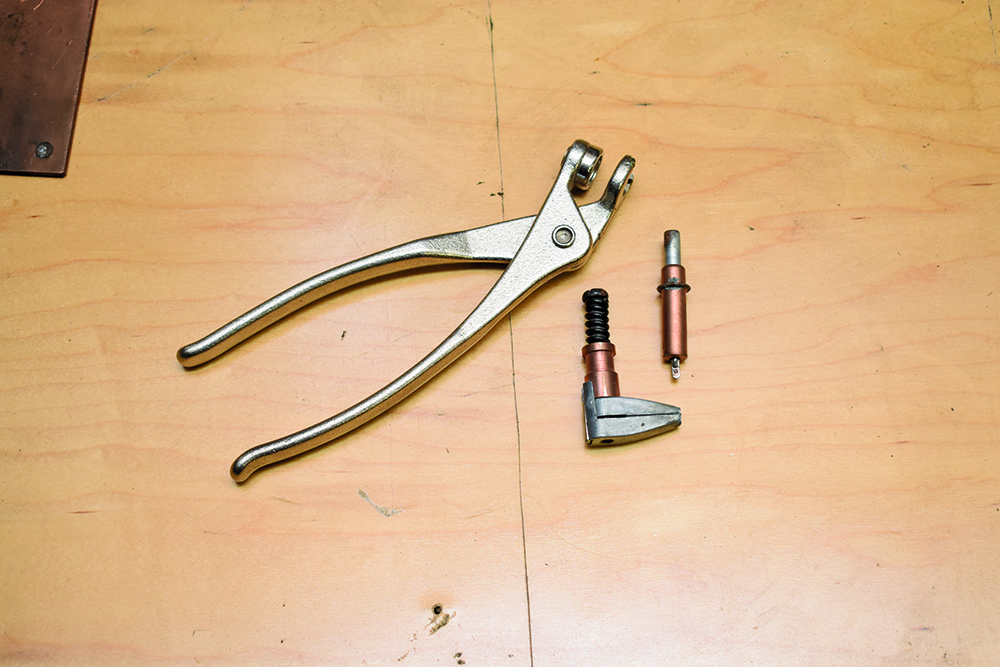
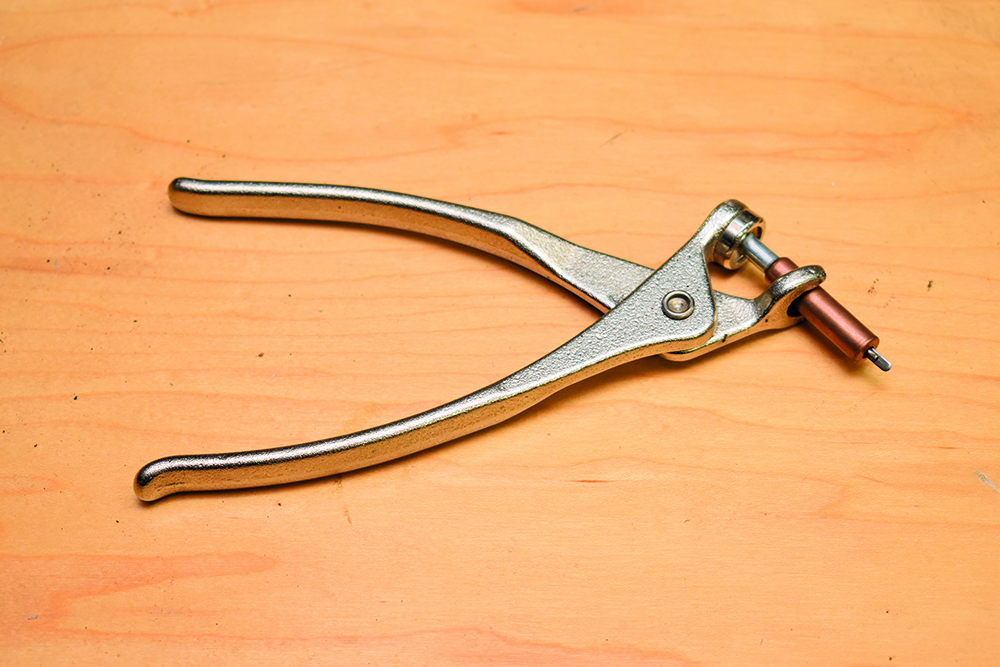
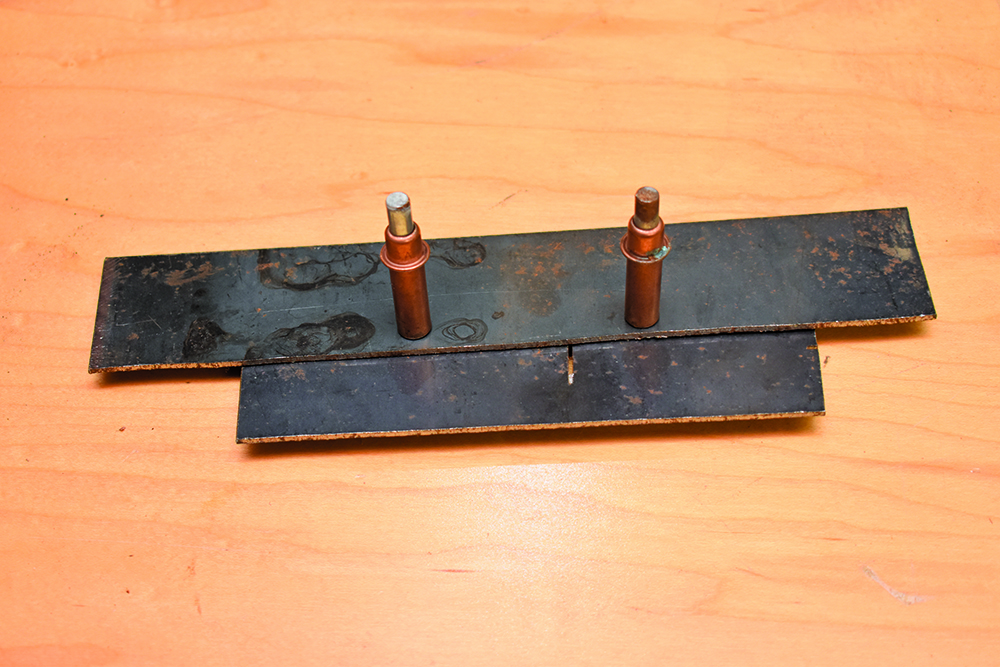
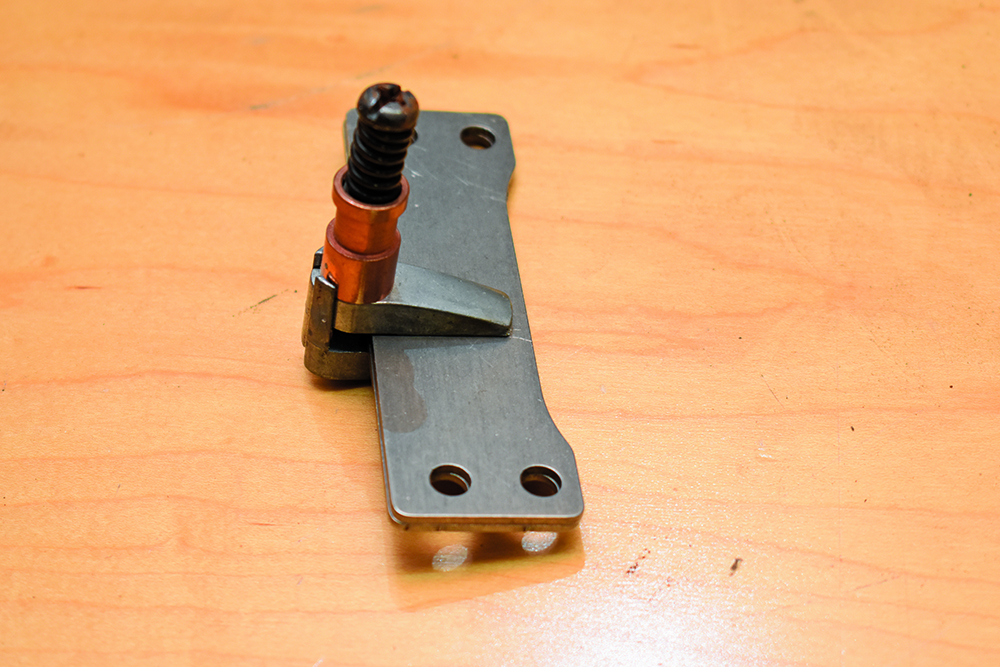
SOURCES
Eastwood
(800) 343-9353
eastwood.com
Kev’s Rod & Custom
(714) 686-8982
facebook.com/kevsrodandcustom
LS Fabrication
(780) 678-946
ls-fab.com
Miller Electric
Manufacturing Company
millerwelds.com
Summit Racing Equipment
(800) 230-3030
summitracing.com