New Life for an Old Rearend
By Ron Ceridono – Photography By Tim Foss
One of the common and most beneficial upgrades on ’63-70 Chevy C10 pickups is the addition of disc brakes (front disc brakes became standard equipment in 1971). The good news is, the increased stopping power converting to later model disc brakes allows the use of a variety of custom wheels with a 5-on-5 bolt circle as opposed to the original six-bolt pattern. The bad news is you’ll still be stuck with six-bolt wheels on the rear end. However, for every problem there is a solution, and in our case the solution came from Classic Performance Products and J&S Gear Company.
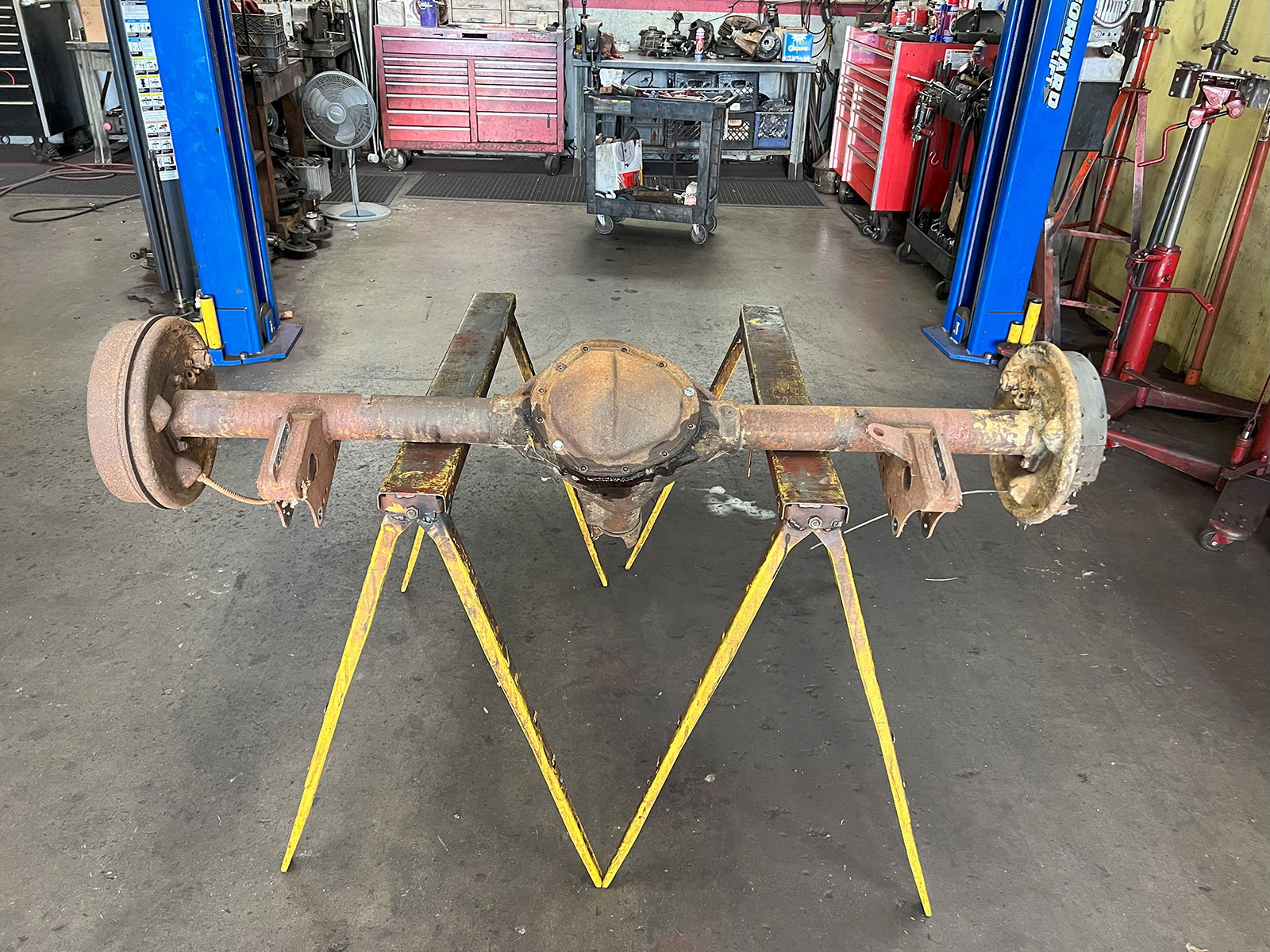
Read More: Affordable Independent Rear Suspension Upgrade For Your Classic Trucks
To convert to late-style wheels, Classic Performance Products offers new axles that come pre-drilled with the five-lug on 5-inch Chevy truck bolt circle that fit ’63-70 12-bolt rear ends (these axles won’t work on ’60-62 trucks or ’63-64 trucks with factory Positraction). These axles accept ’71-72 truck drums and use the existing brake hardware. While the necessary additional parts for the conversion are available separately, Classic Performance Products makes things simple by offering a complete kit (PN 6369RAC-5) that comes with axles, wheel studs, and new brake drums. For those with ’63-64 trucks it should be noted that due to the 17-spline axles these trucks were equipped with, the differential side gears have to be changed to 30-spline to match the new axles (CPP can supply these as well).
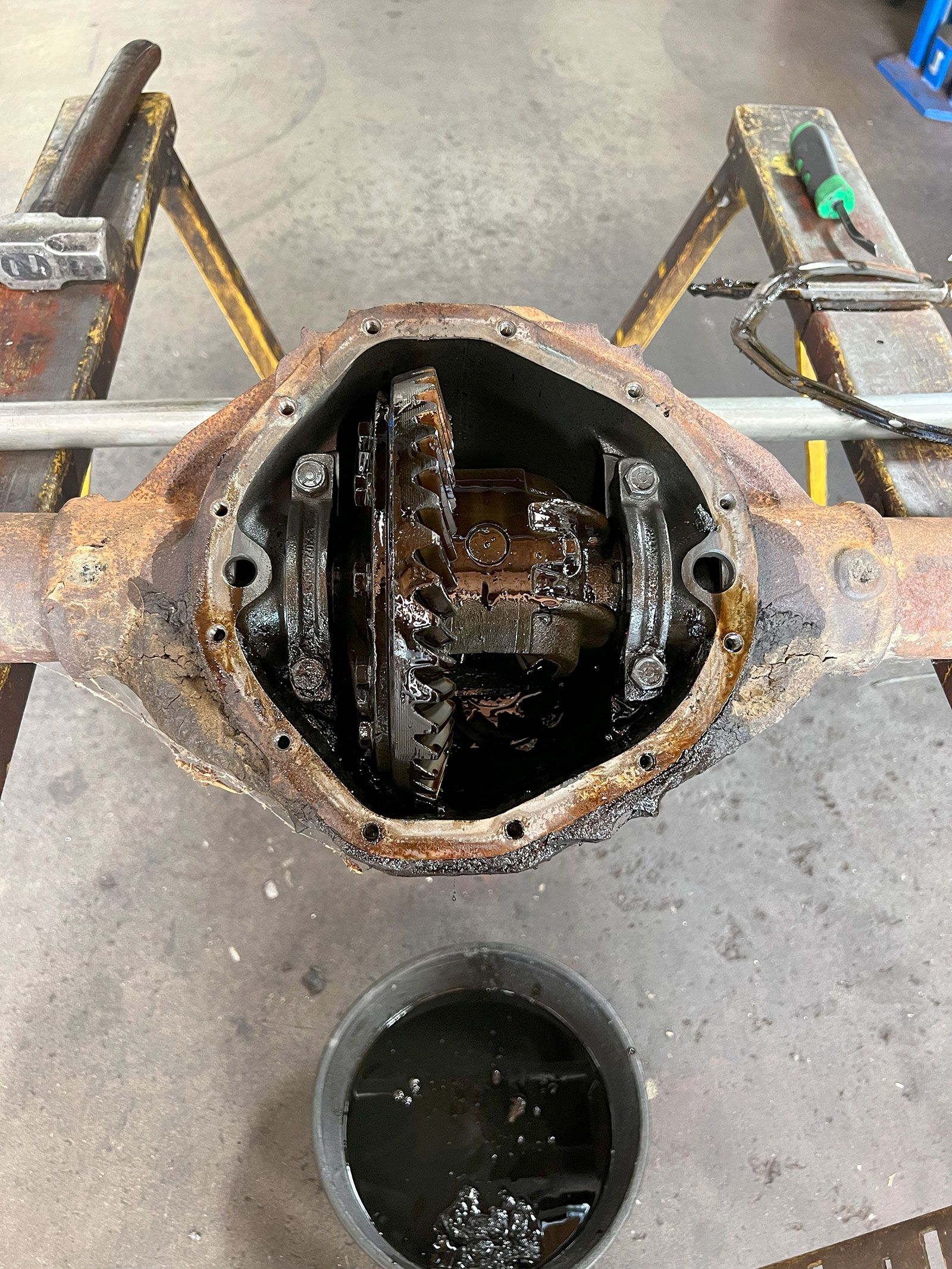
The well-used rear end that is the subject of our update was delivered to John’s J&S Gear Company in Huntington Beach, California, for a much-needed overhaul and update. The original 17-spline axles were unceremoniously tossed in the trash, followed shortly after by the mileage-weary differential assembly, ring gear, pinion, and all the bearings. A close inspection revealed that all eight of the spot-welds holding the axle tubes to the center section had been leaking gear oil, so all the factory welds were rewelded. To further secure the axle tubes they were welded all the way around where they were pressed into the center section. Once the welding was completed, the housing was thoroughly cleaned and then sent out to be sandblasted and powder coated.
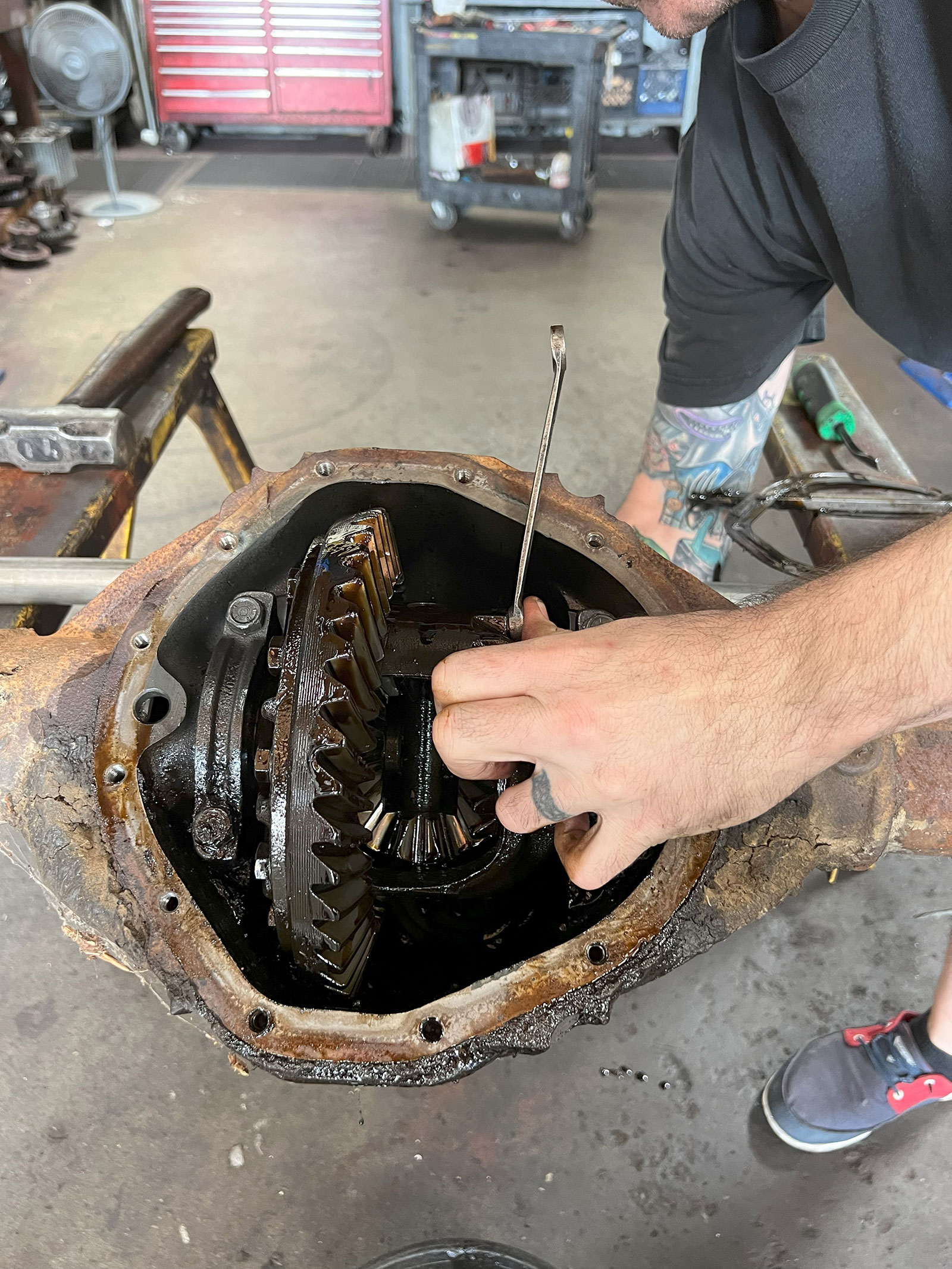
Read More: New 1967-72 Chevy C10 Art Morrison Chassis With IRS Upgrade
To replace the original open-drive differential, J&S ordered an Eaton Truetrac unit (PN DTL-913A315) from Summit Racing. The Truetrac accepts 30-spline axles and 3.73 and numerically higher ring gears. Truetrac differentials are unique in that they use what are described as parallel-axis planetary helix gears to provide seamless, automatic splitting of torque when the situation demands. What that means is that in normal driving conditions the Truetrac performs like a standard differential, but if one tire starts to spin torque is transferred to the tire with better traction. To complete the rejuvenation of the centersection, a new ring-and-pinion would be required so J&S again turned to Summit for a Richmond 3.73:1 gearset (PN RMG-4902801).
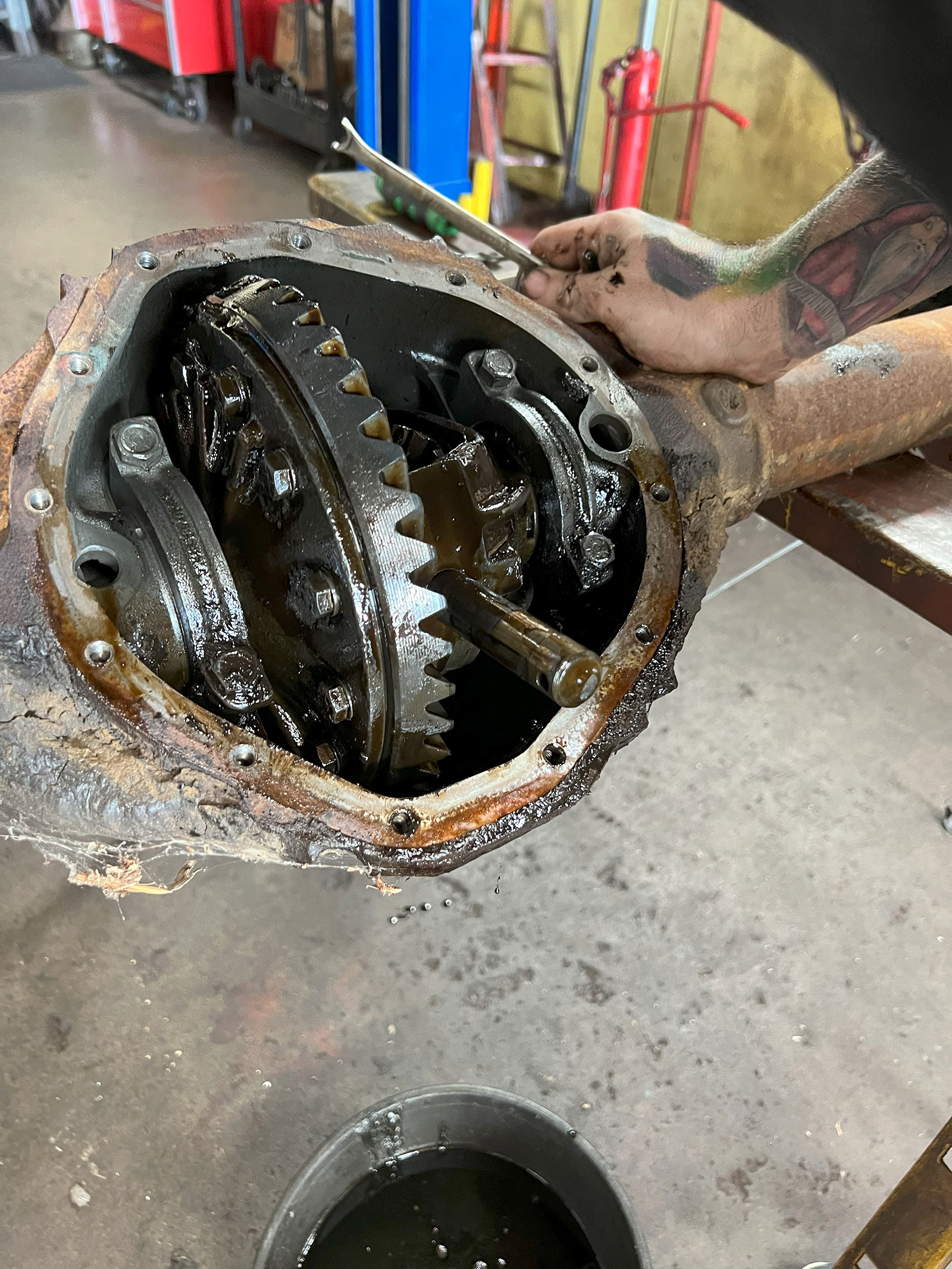
When the housing came back from sandblasting and powdercoating it was time to clean it once with a brush attached to a drill. Gary, who was responsible for assembling the rear end, points out the quickest way to destroy a new gearset is to powdercoat the housing with sand stuck to the internal surfaces. Due to the heat generated in the housing during operation it will cause the sand and debris to come loose, which will quickly wear out the gears.
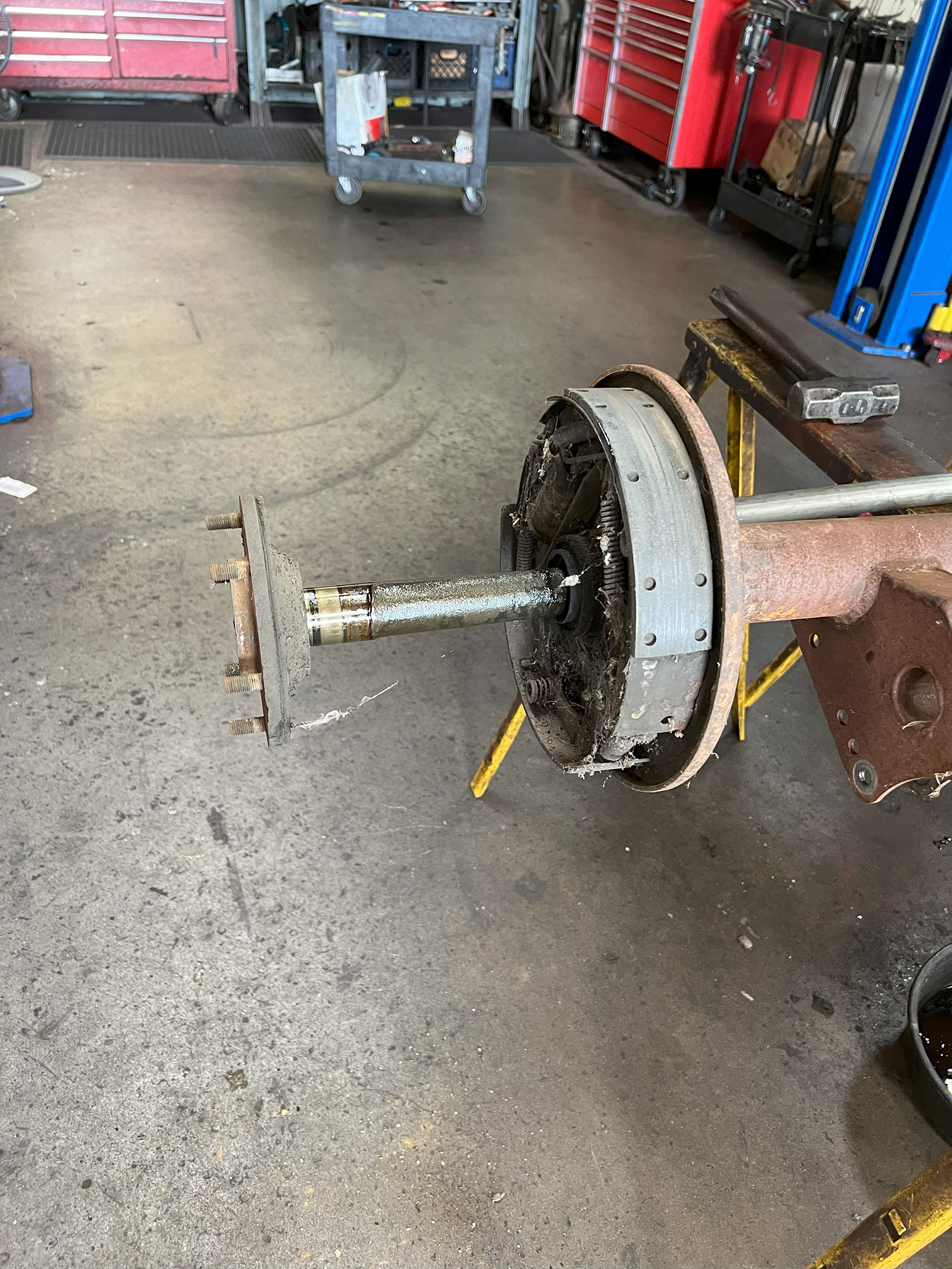
Read More: Keeping Your Classic Truck Cool
With the new Richmond gears and Eaton Truetrac in place, Gary went about adjusting the preload on the pinion and side bearing and then checked the gear pattern and backlash. Satisfied that all was as it should be, new wheel bearings, seals, and 5-on-5 bolt circle axles from CPP were slipped in place. When all was said and done our Chevy’s 12-bolt rear end was as good as new—in fact it was even better.
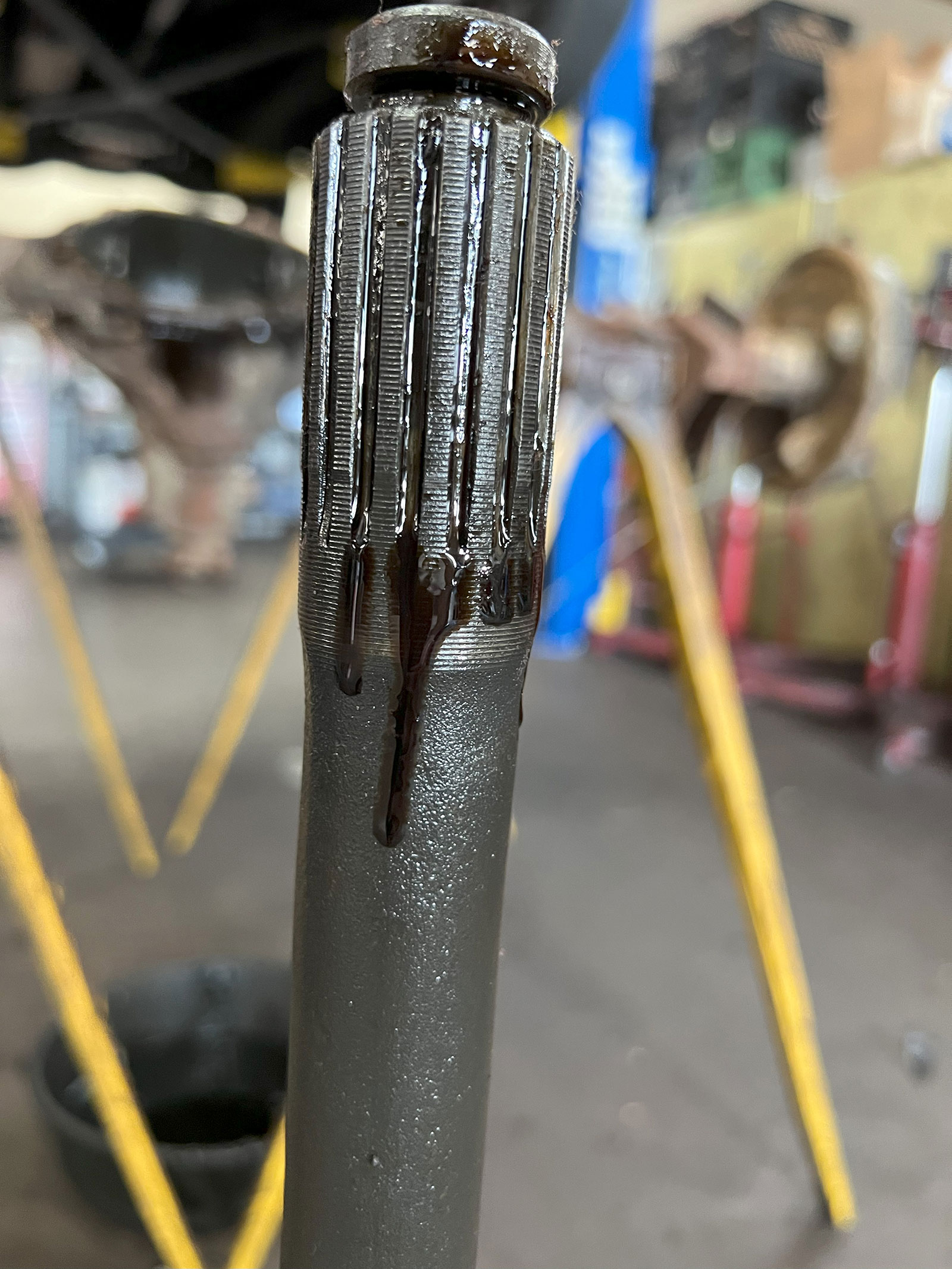
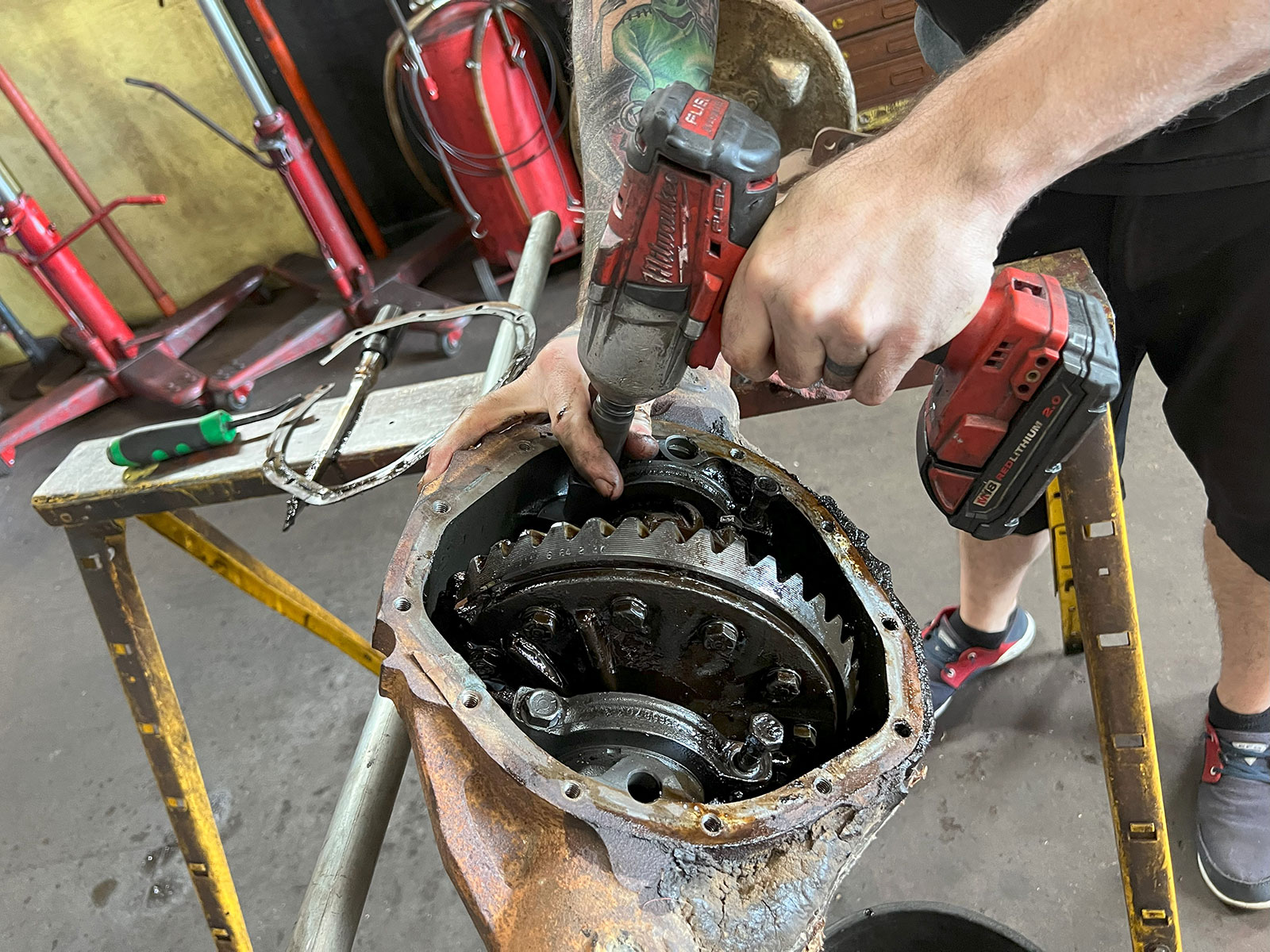
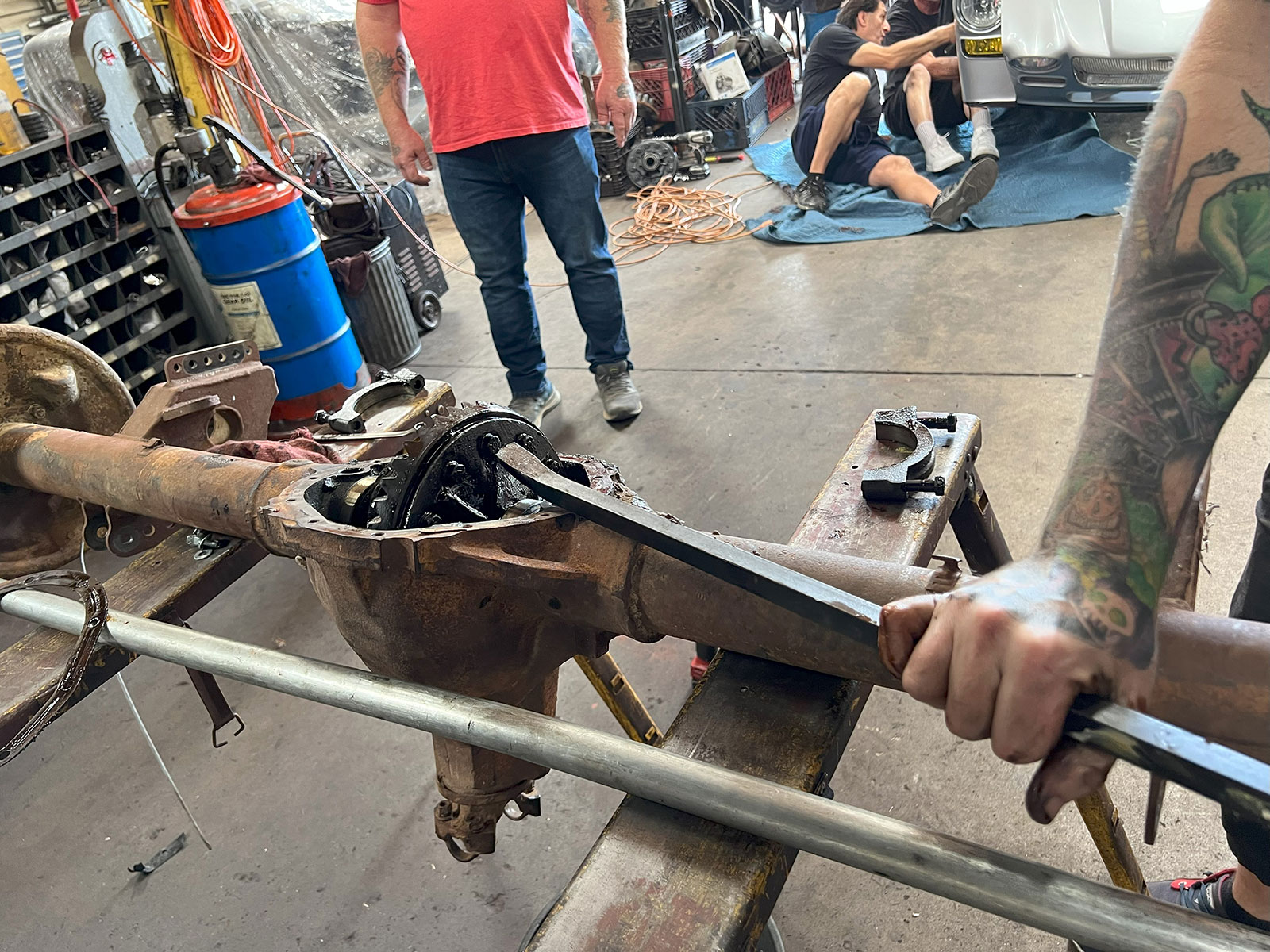
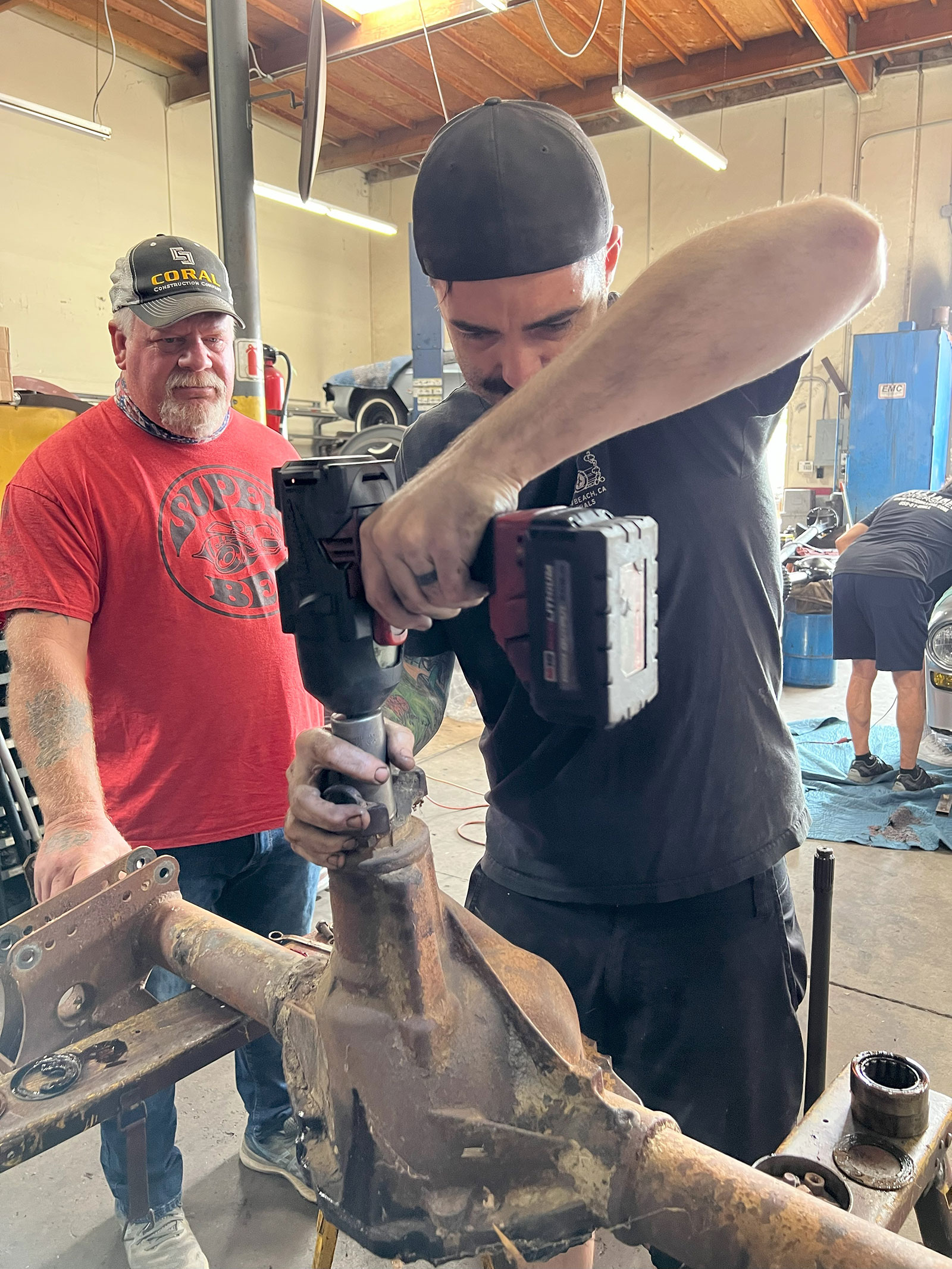
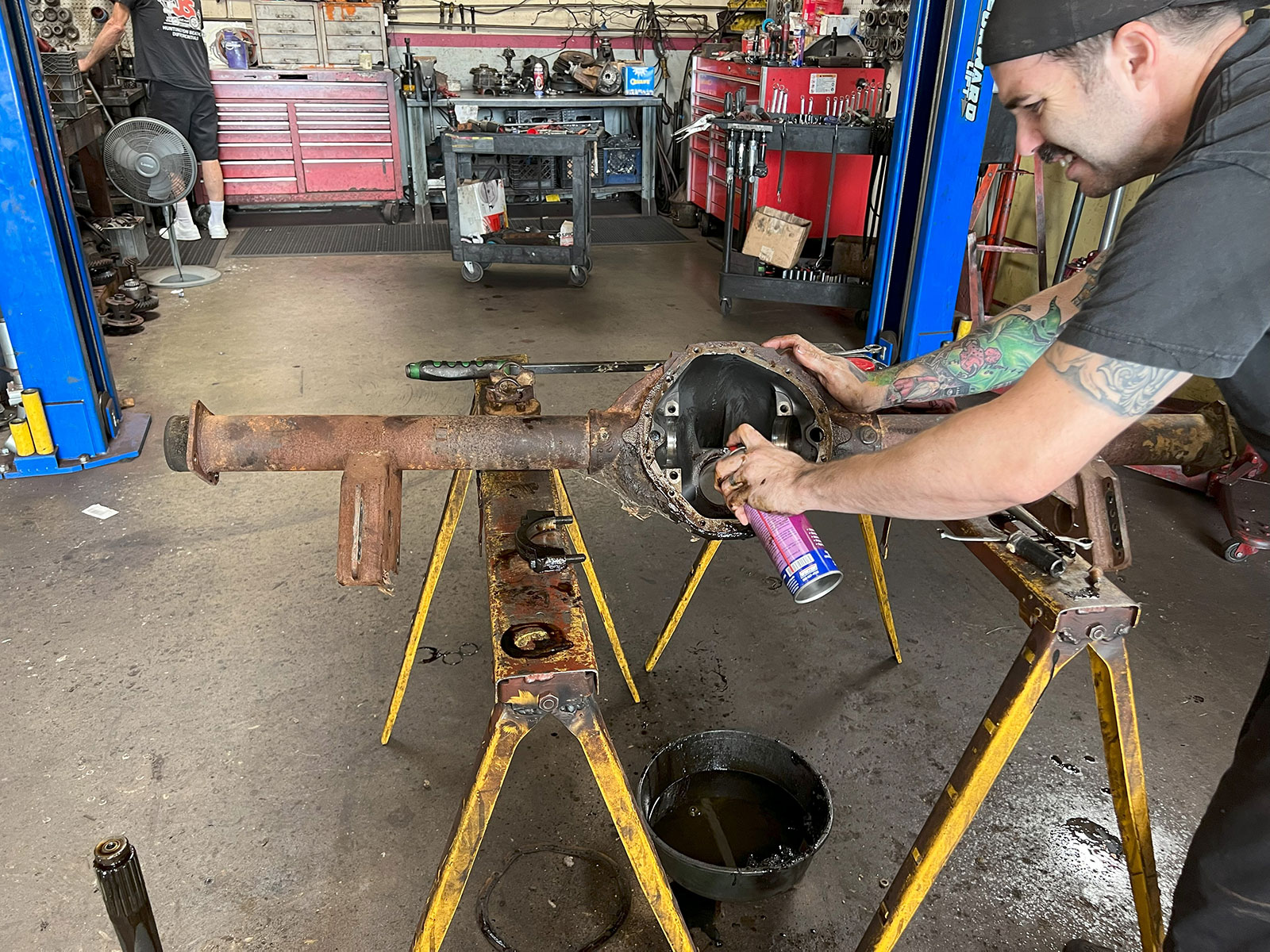
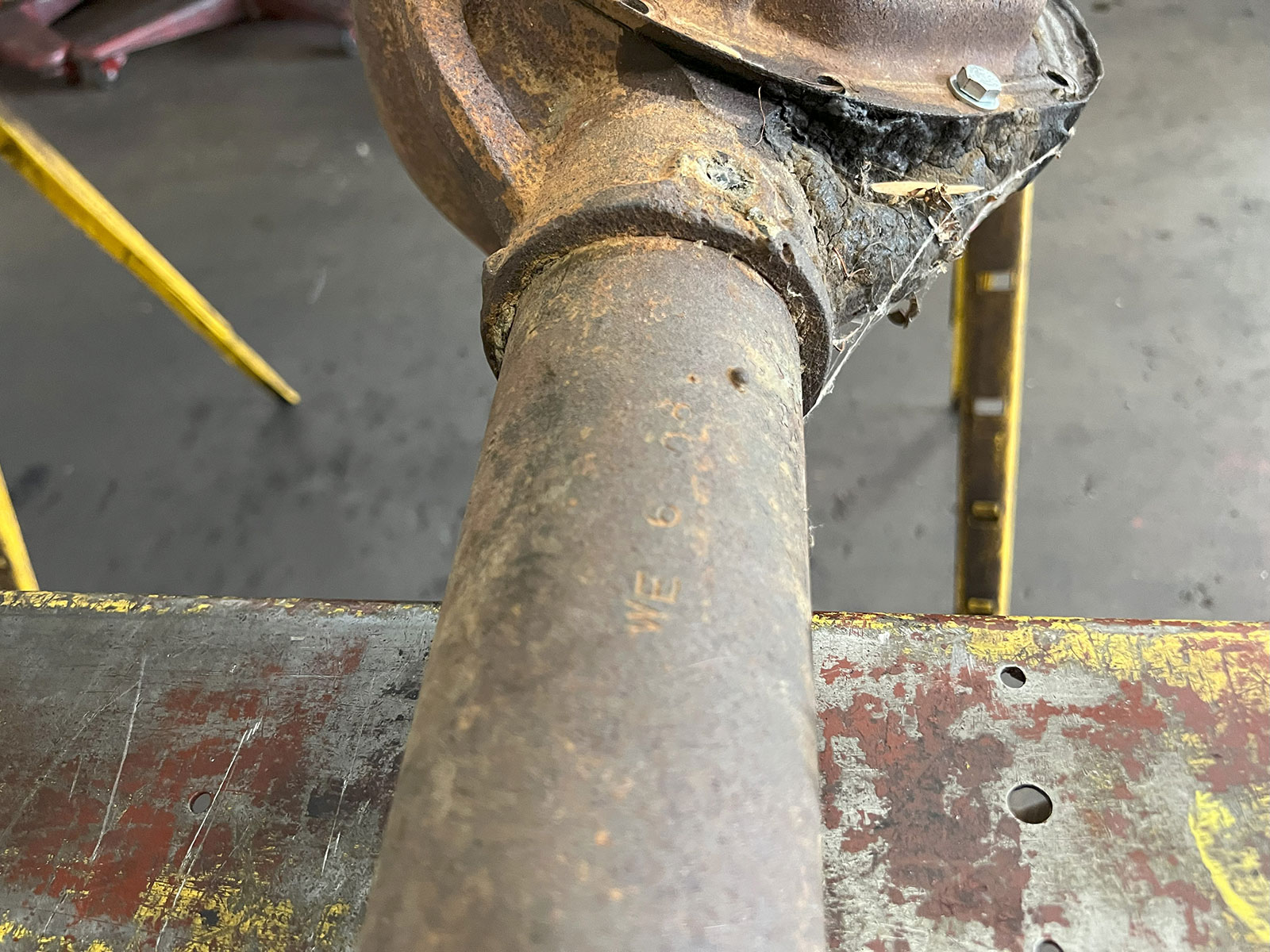
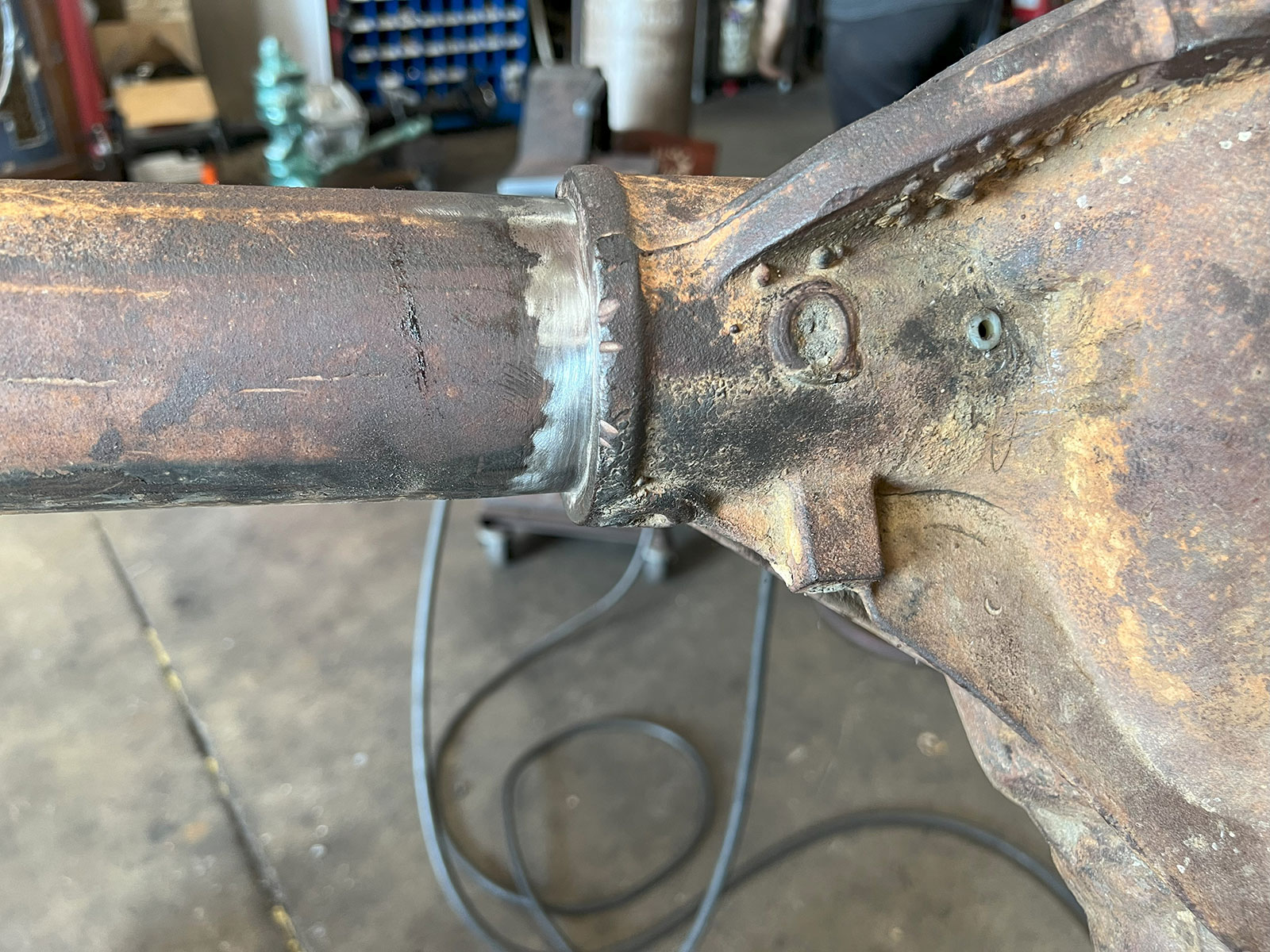
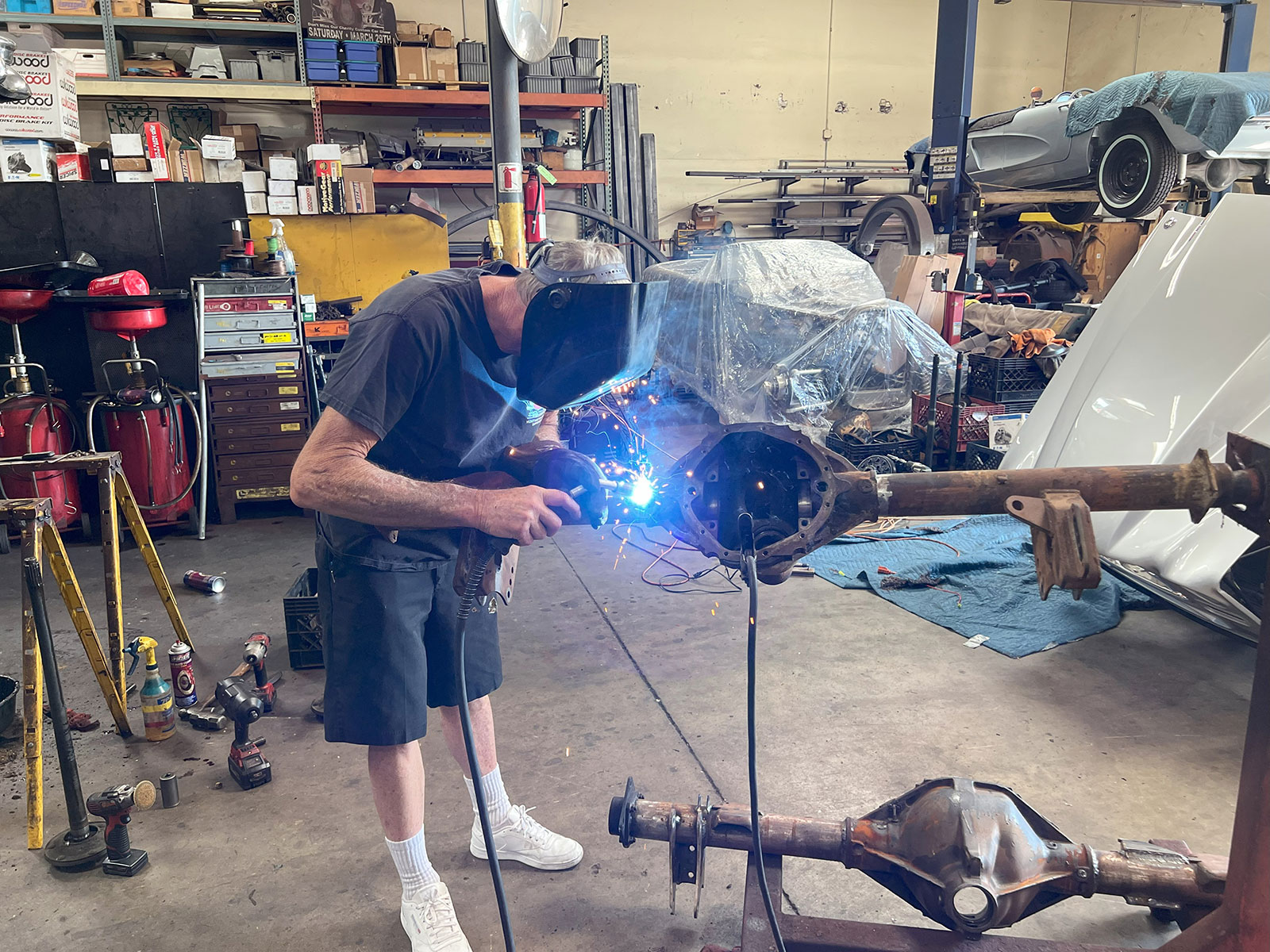

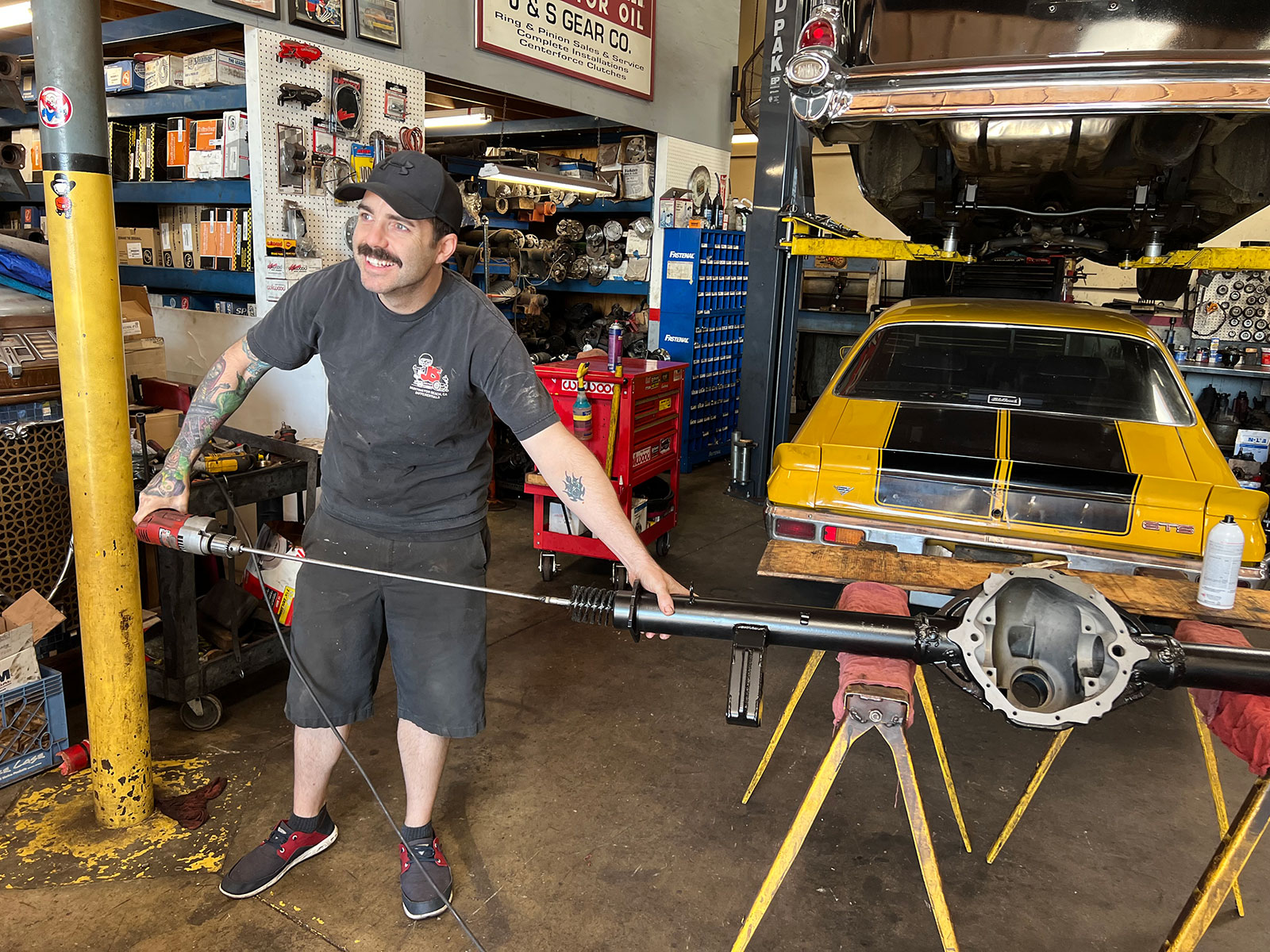
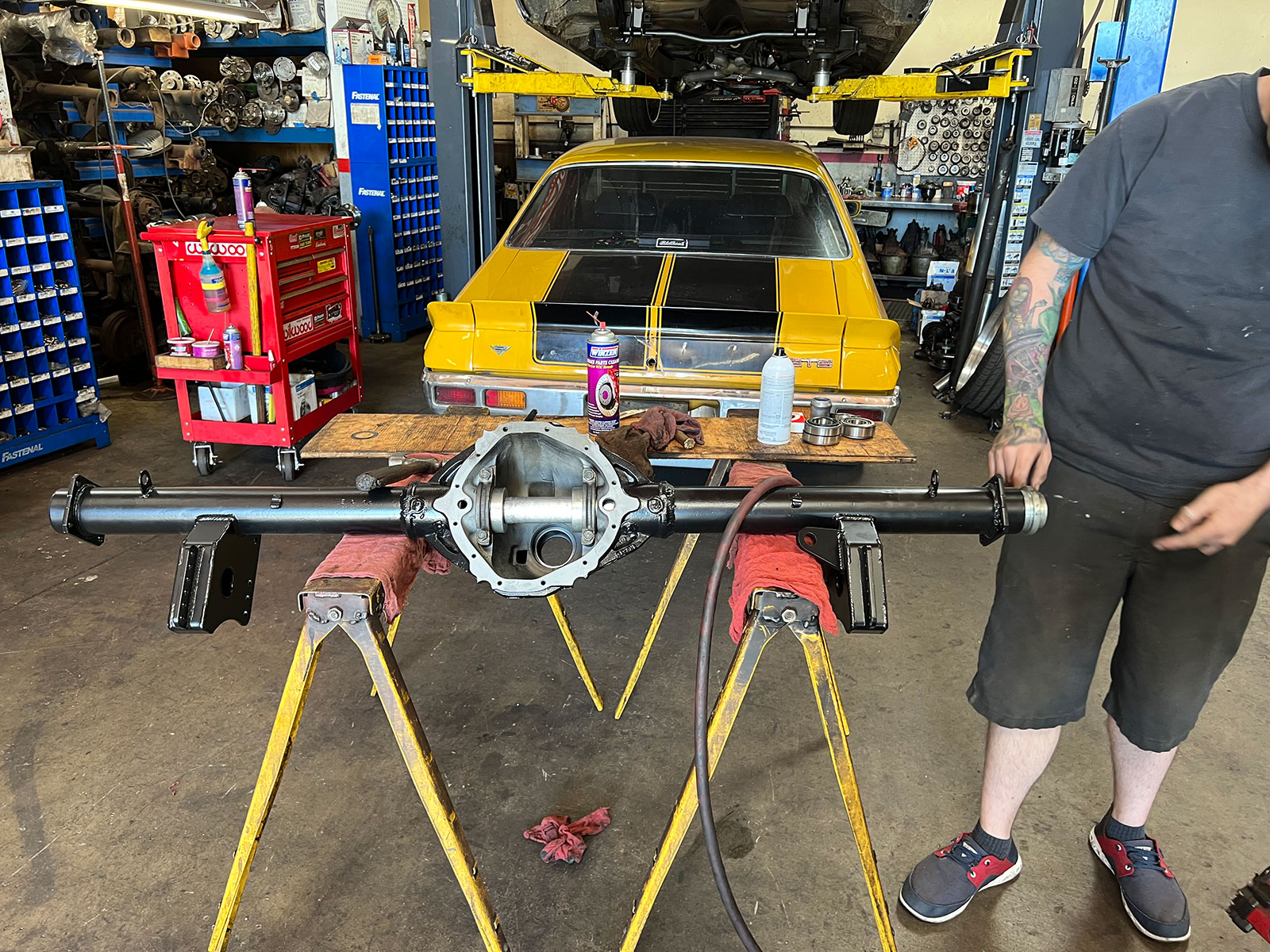
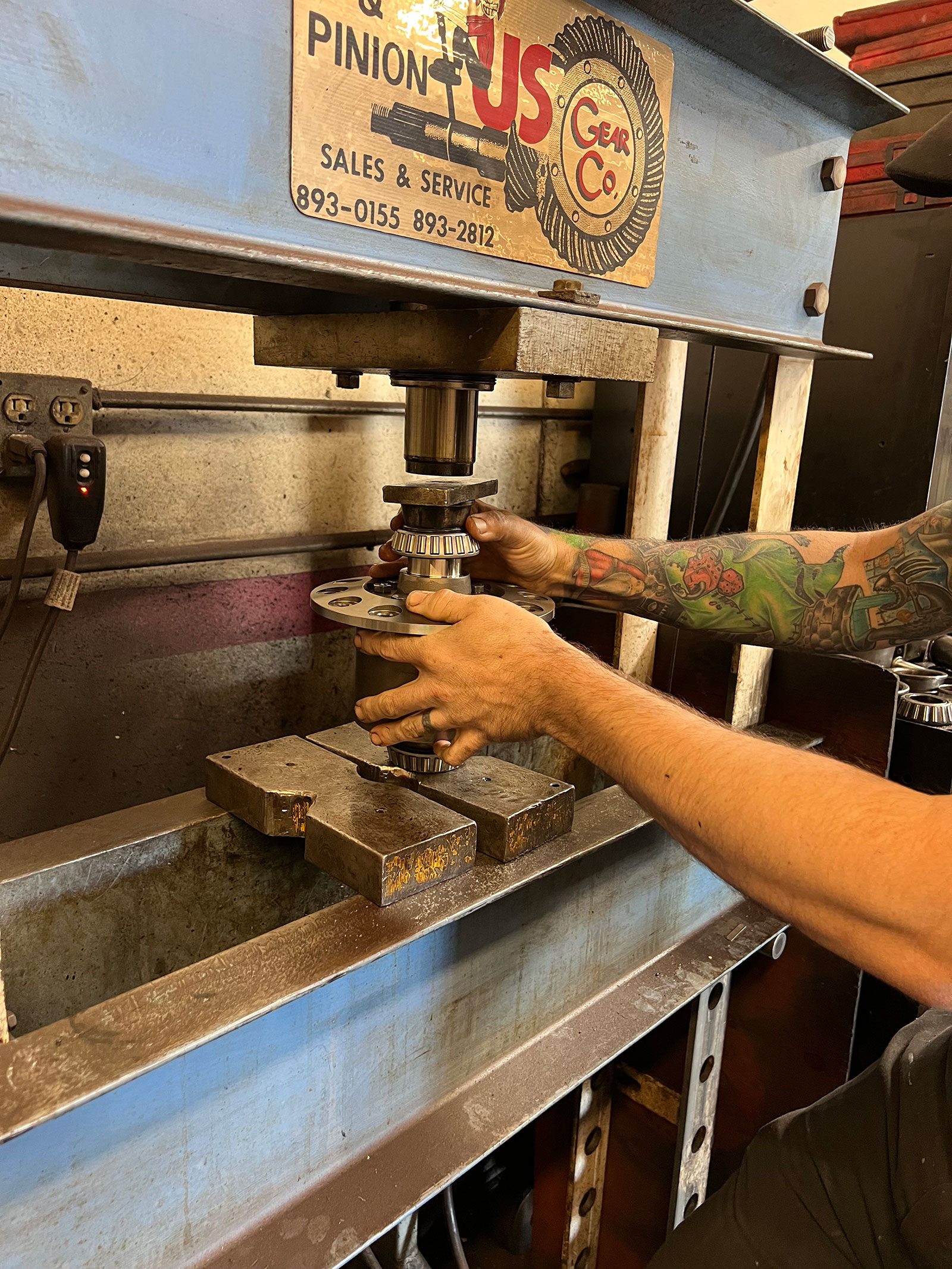
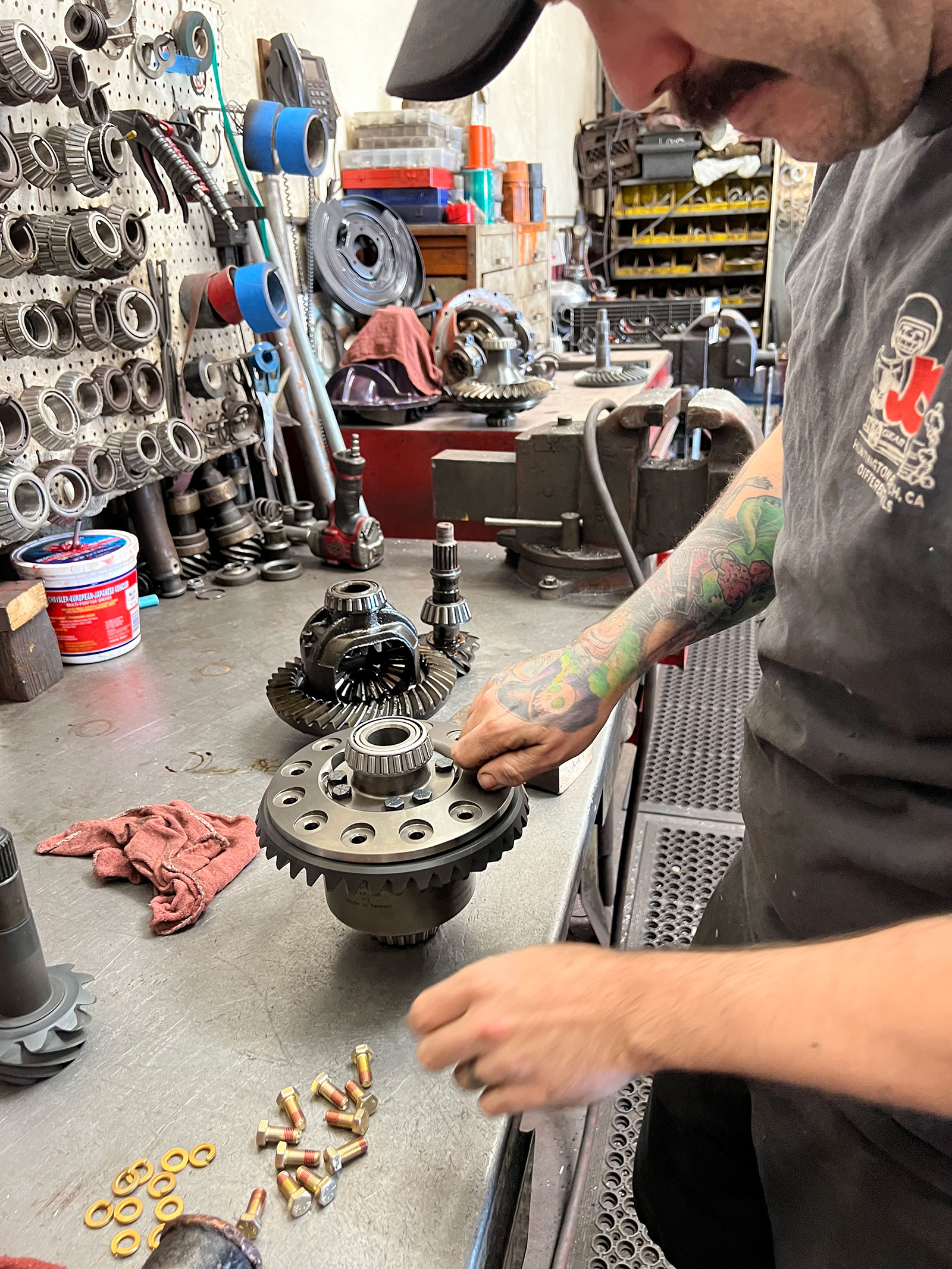
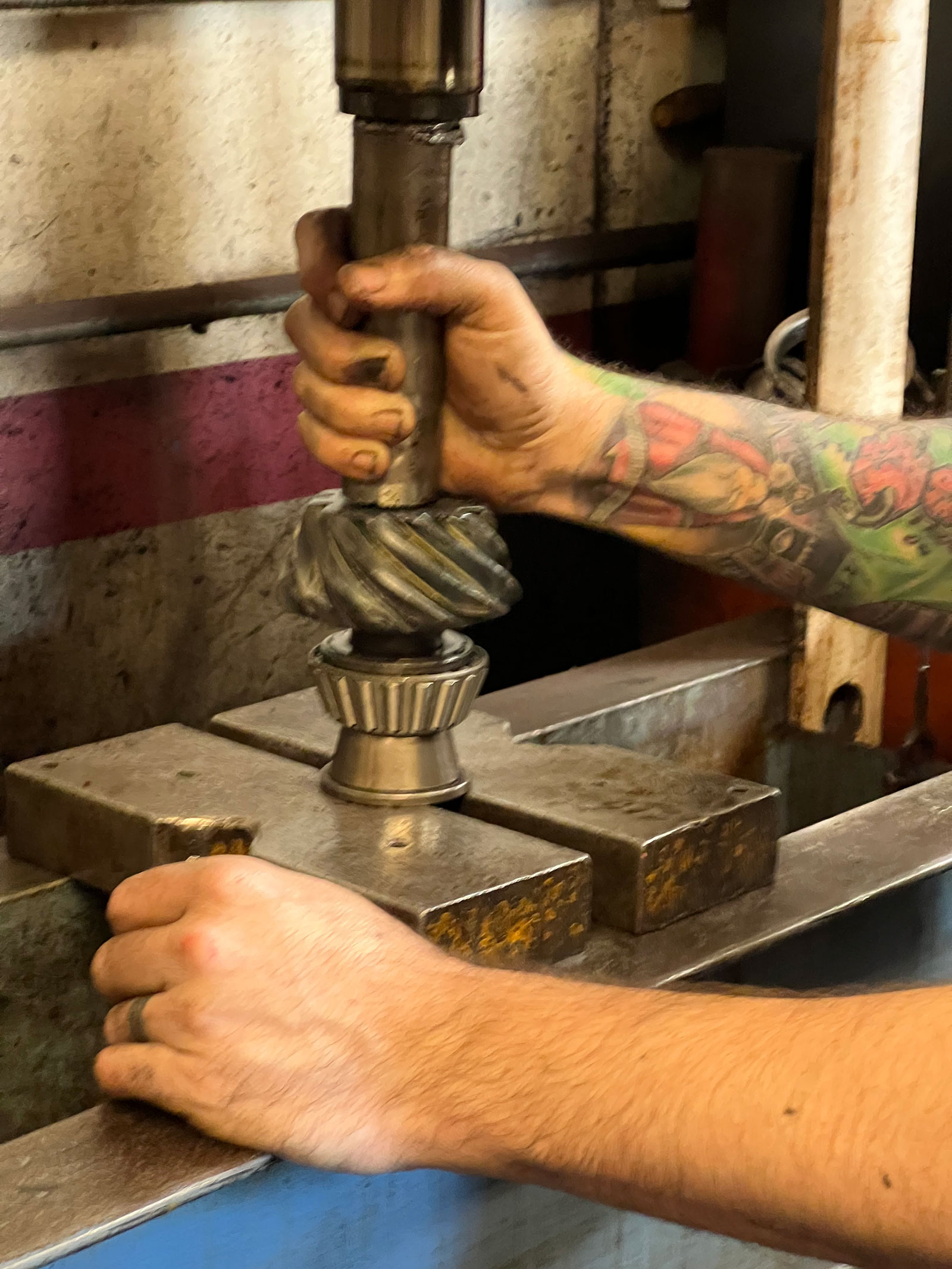
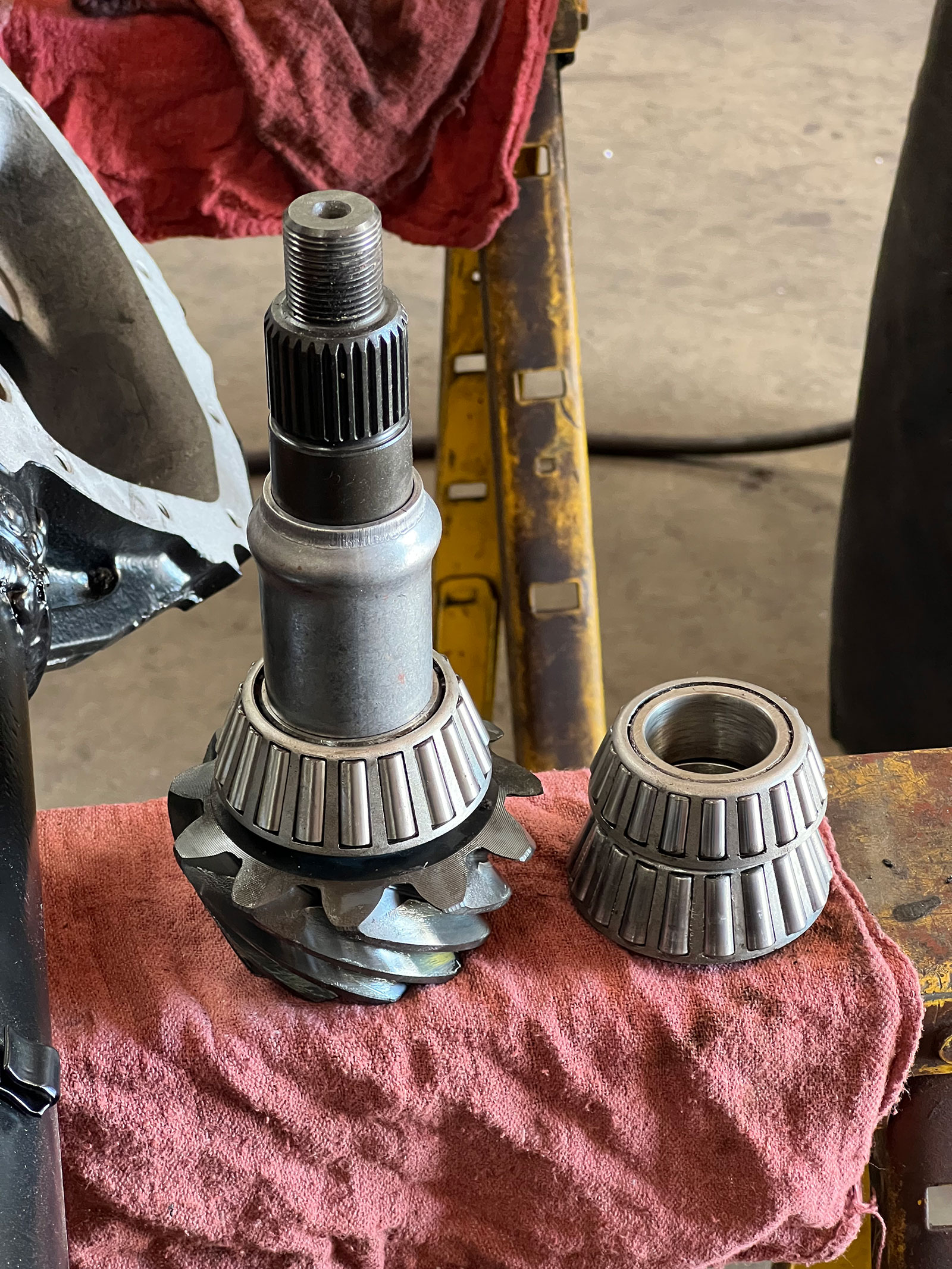
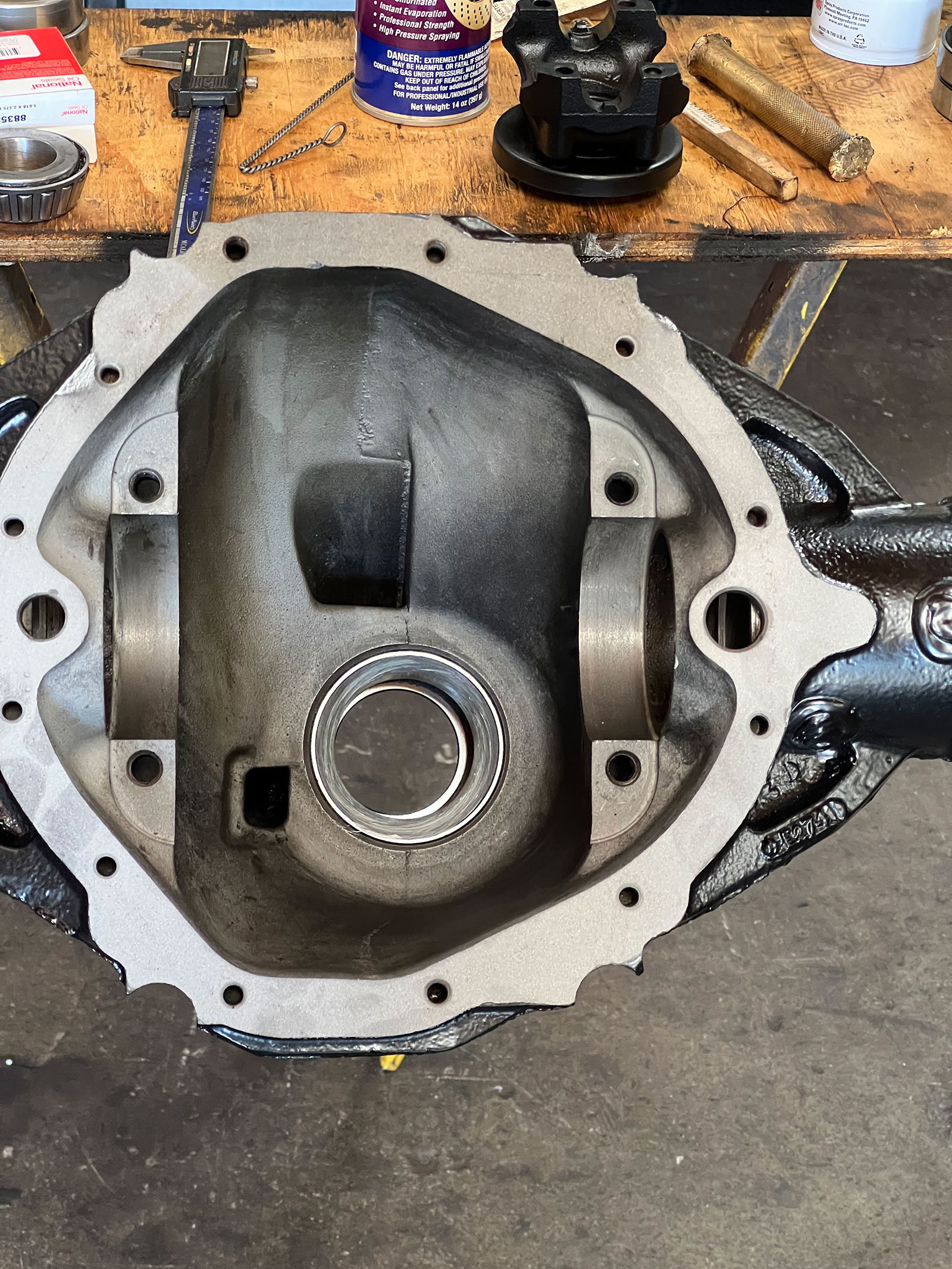
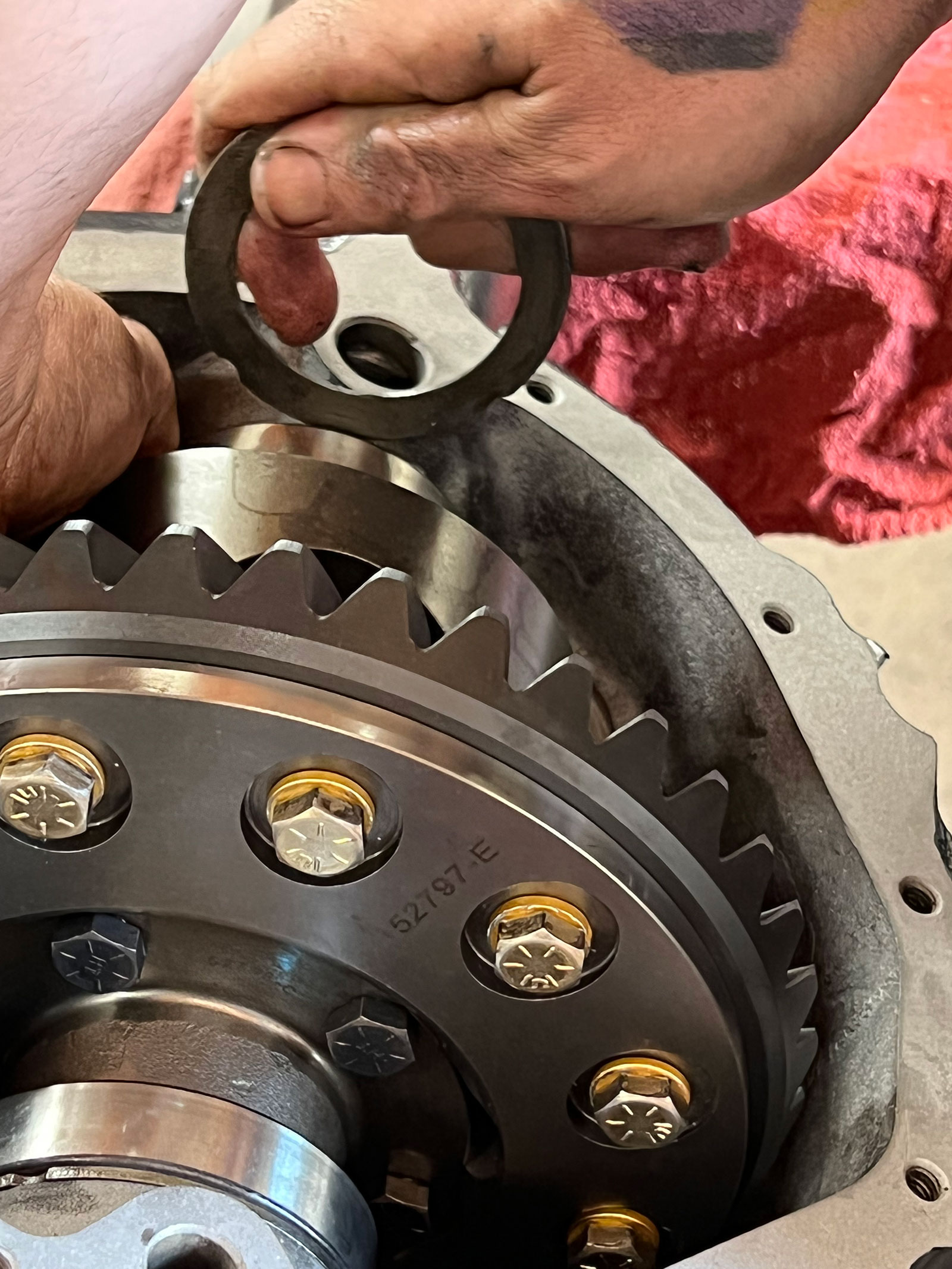
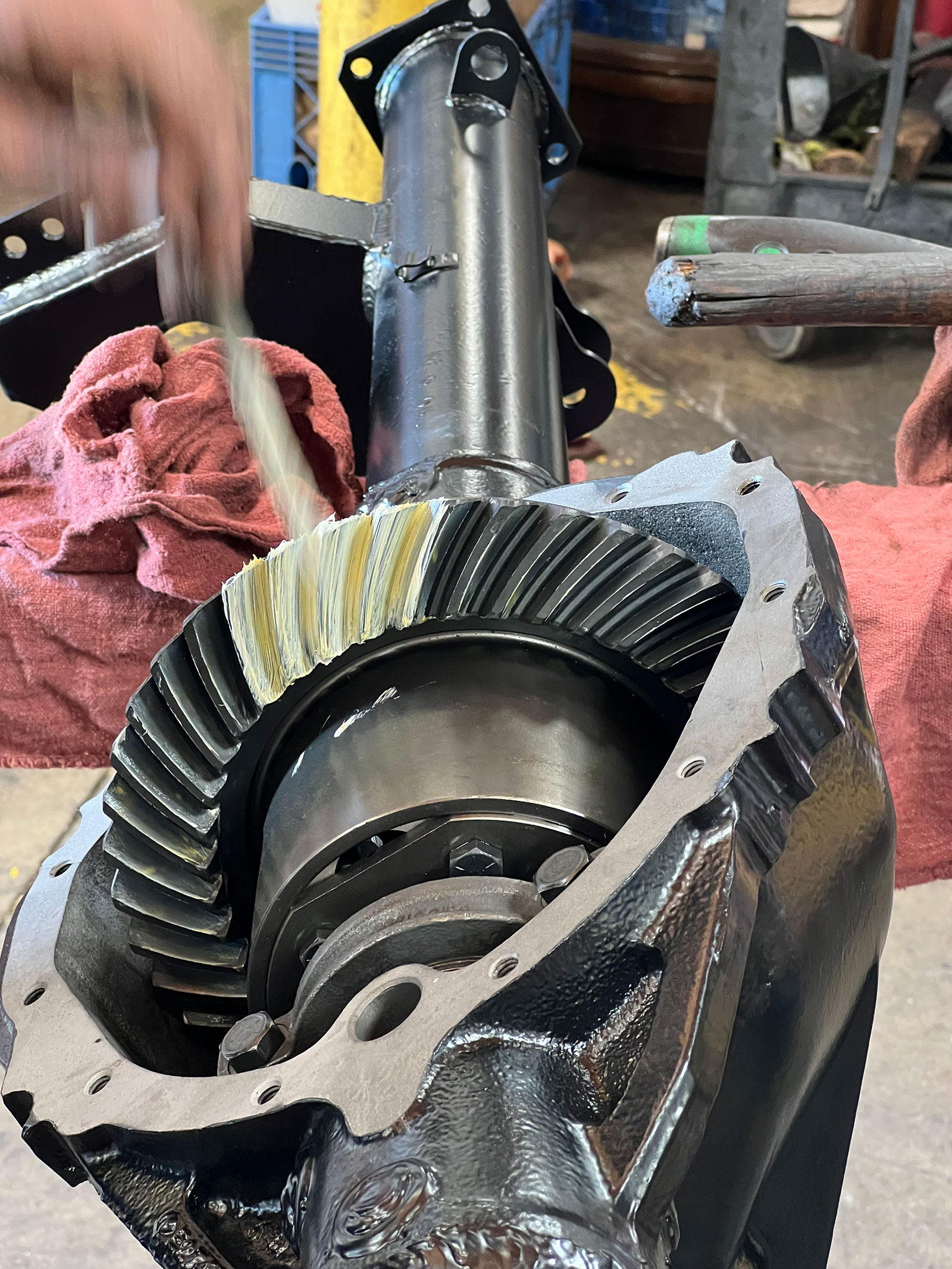
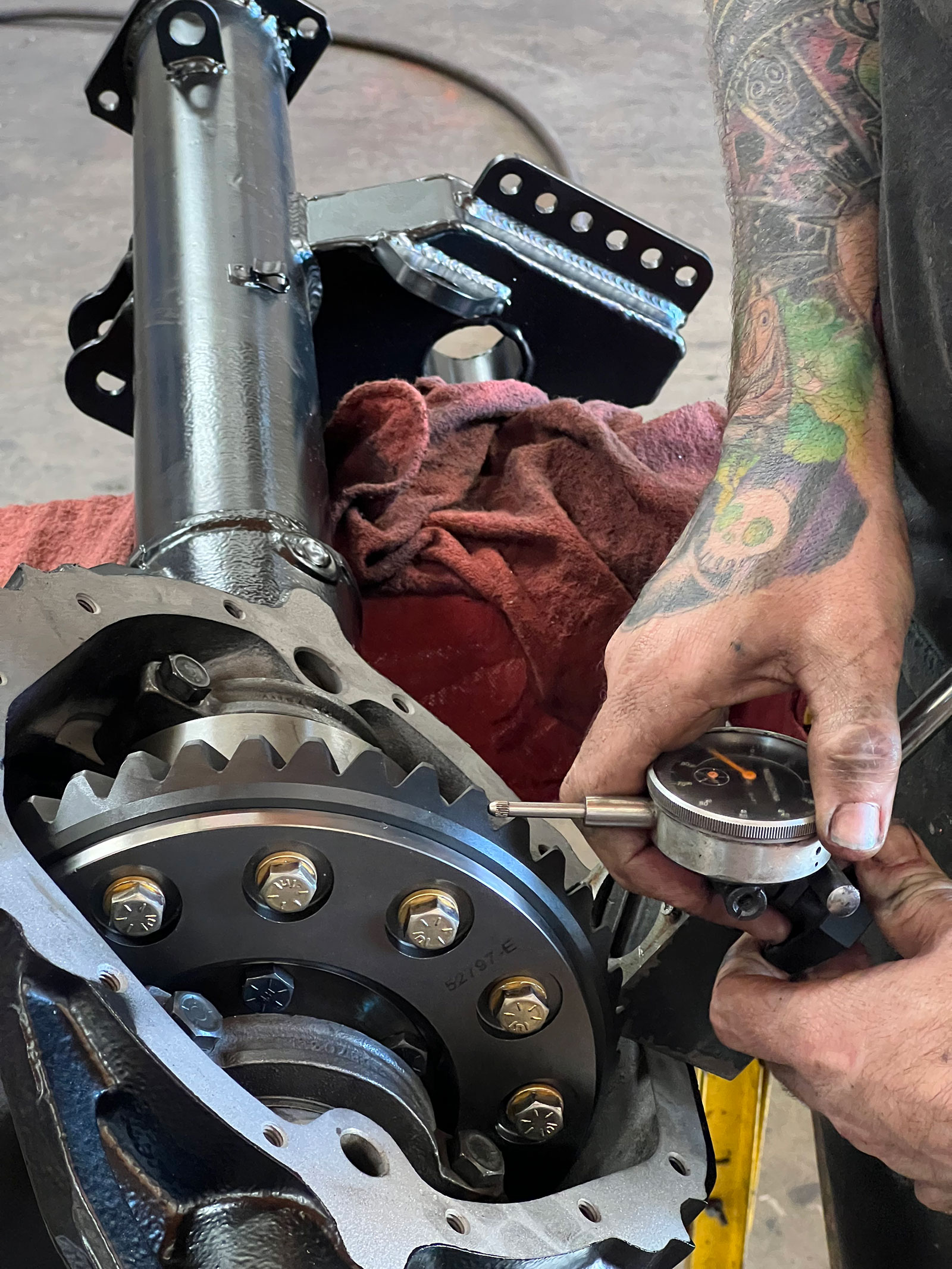
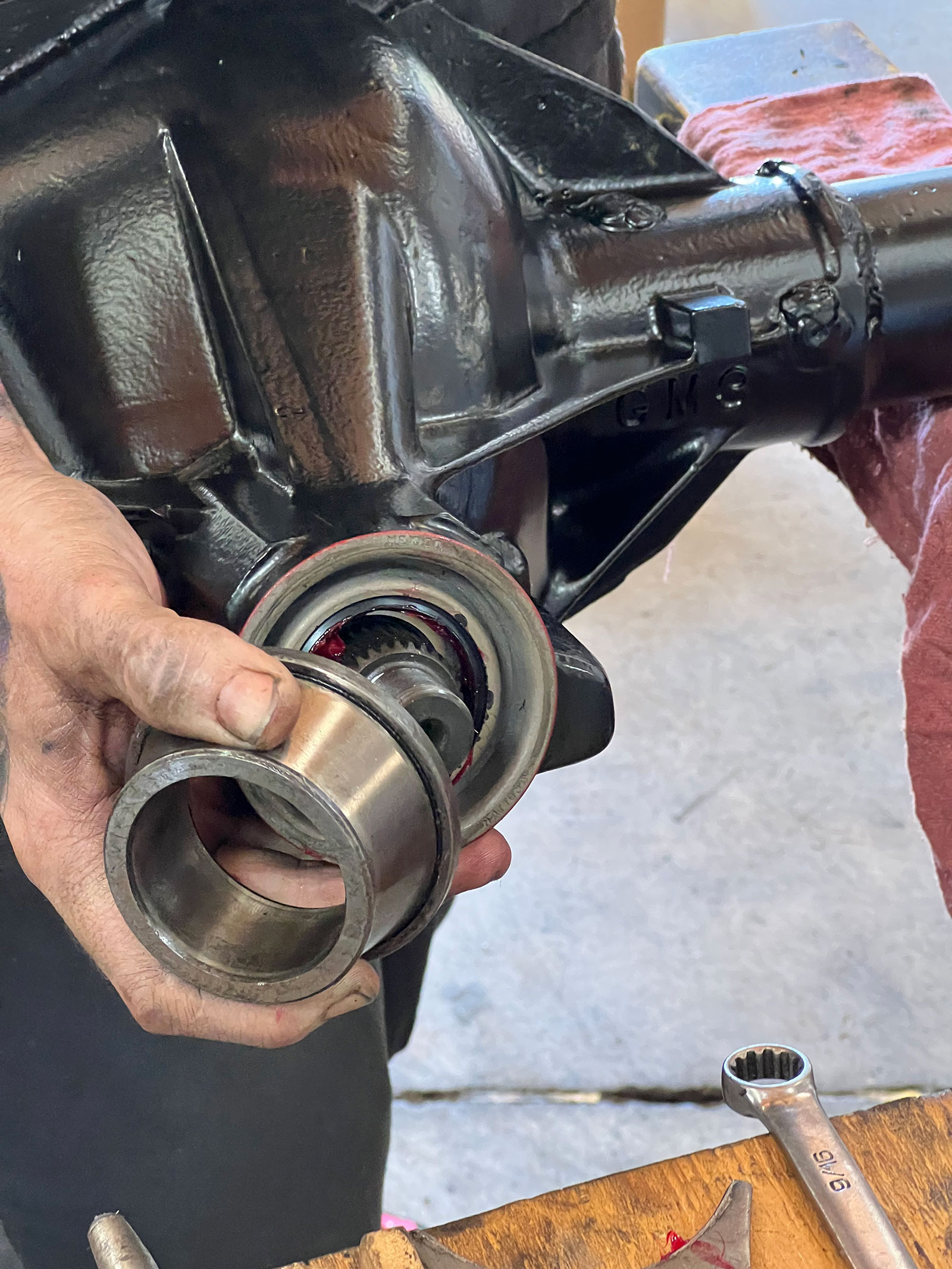
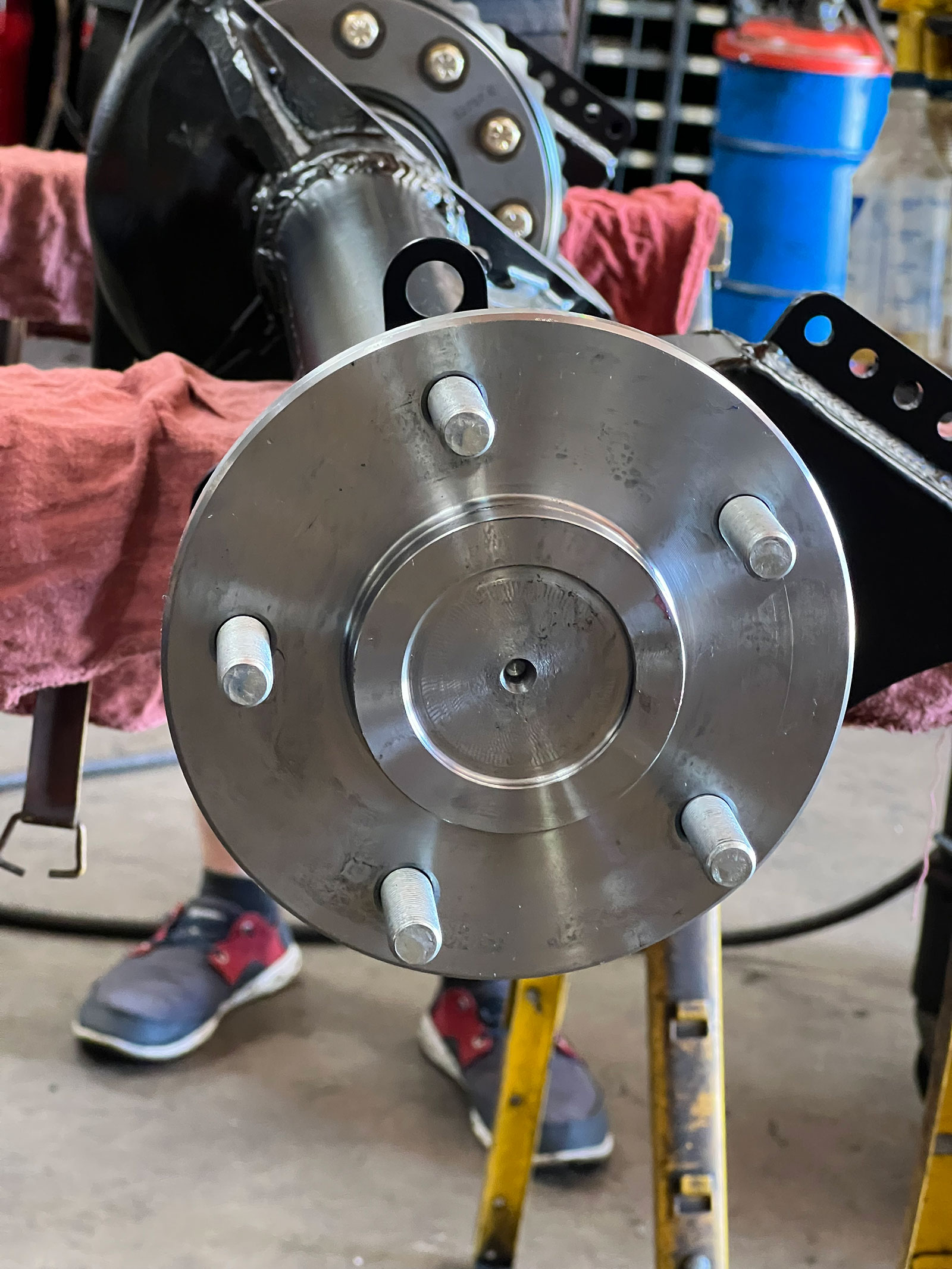
Sources
Classic Performance Products
(800) 760-7438
classicperform.com
J&S Gear
(714) 841-4545
jandsgears.com
Summit Racing Equipment
(800) 230-3030
summitracing.com