Could This Be the Ultimate 4×4 Chassis?
By Ron Ceridono
Art Morrison has a long history of building performance vehicles. As a teenager he collected a number of trophies with his homebuilt, big-block–powered, straight-axle–equipped ’54 Chevy. Morrison’s passion for performance ultimately led him to open Art Morrison Enterprises (AME) in 1971, which quickly grew into one of the leading drag race chassis and component manufacturers in the country.
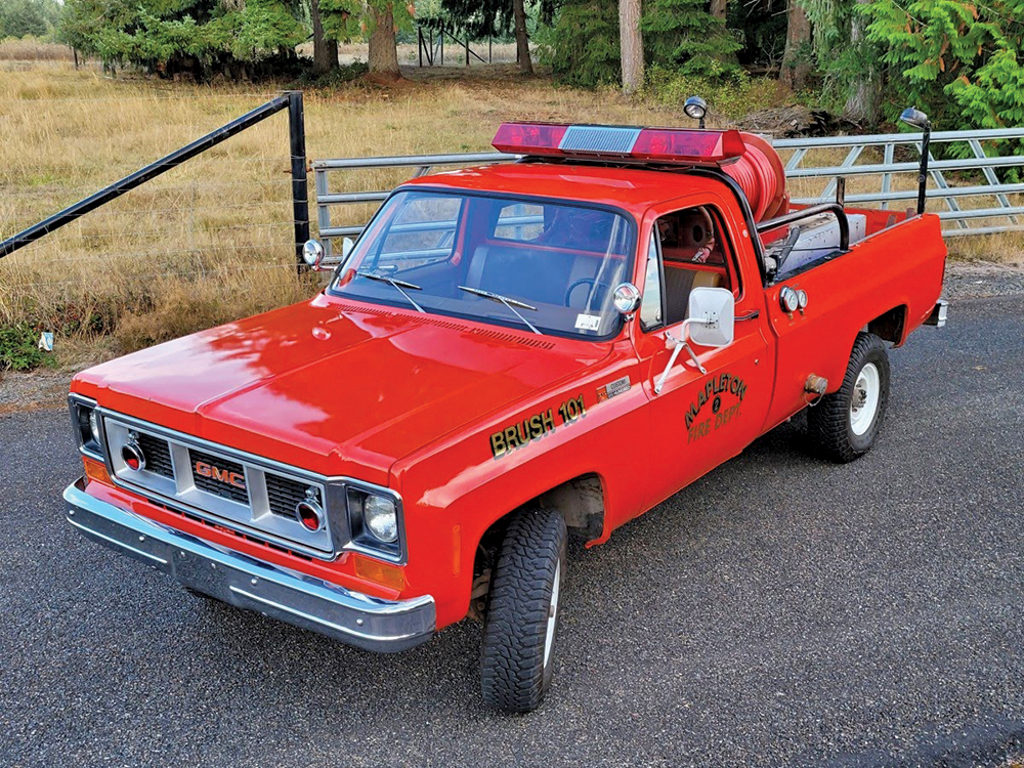
Ever the innovators, AME grew in size as the company broadened its scope by including components for high-performance street vehicles. That led to the revolutionary direct-replacement chassis for ’55-57 Chevrolets. Introduced in 2002, the all-new suspension design gave these vintage vehicles the best in contemporary ride and handling characteristics. Today AME offers direct-replacement performance chassis for a variety of cars and trucks, custom one-off chassis for virtually any vehicle imaginable, and B-body Mopar K-members with coilover suspension.
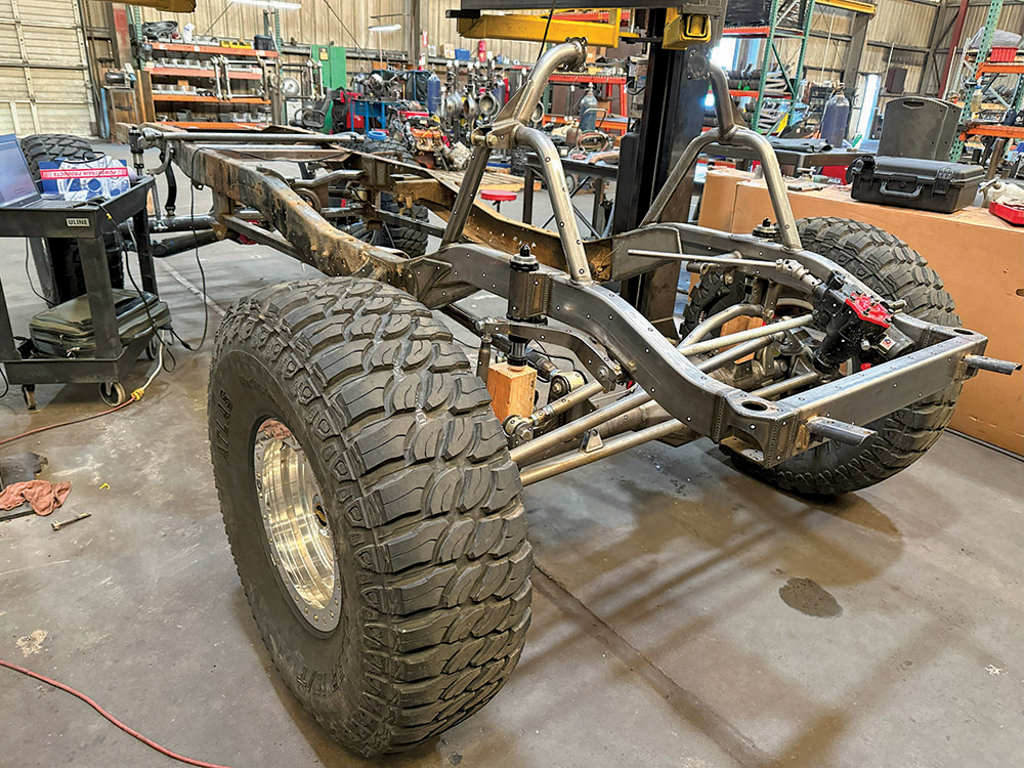
After 51 years in business, Morrison decided to step down and turn the reins of AME over to Matt Jones. Jones has been with the company since 2004, serving first in the engineering department, then as operations manager, and now as president. Under Jones’ leadership AME continues to develop new products, the latest being a new 4×4 chassis for ’73-87 Chevrolet/GMC pickups and Blazers with ’67-72 applications to follow.
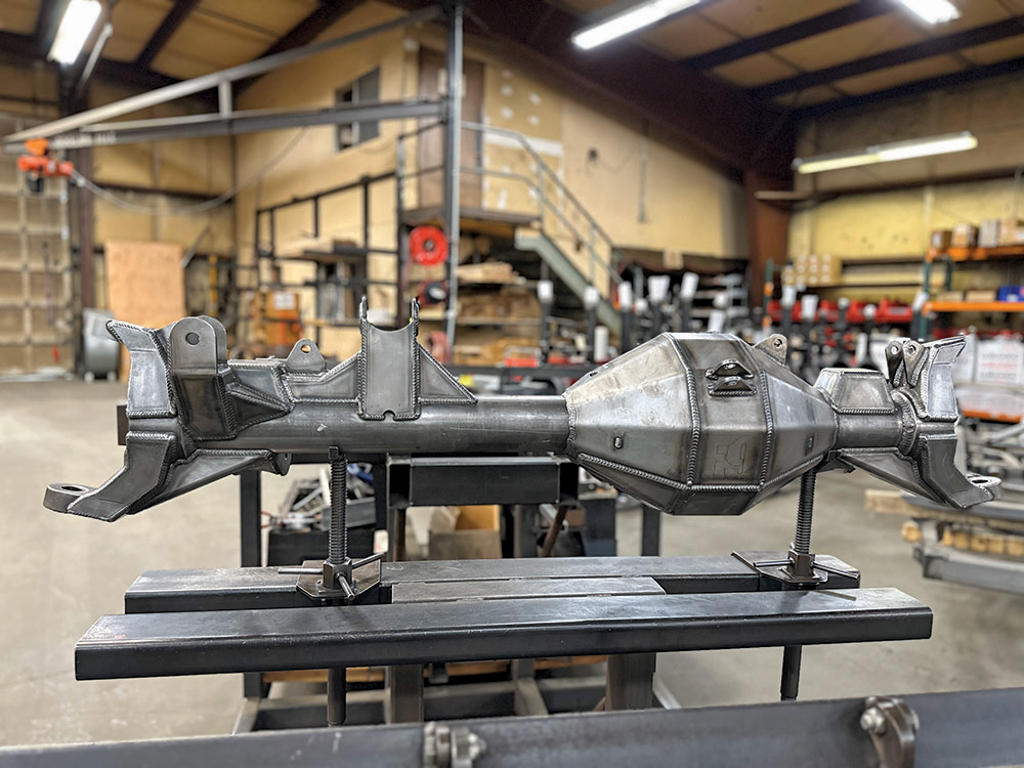
This new AME 4×4 chassis has been under wraps for some time. The test mule for the development of the suspension and frame was a ’74 GMC 2500 with a 350ci small-block and a four-speed transmission. A retired Mapelton, Utah, fire department truck, “Brush 101,” showed a mere 15,000 miles on the odometer.
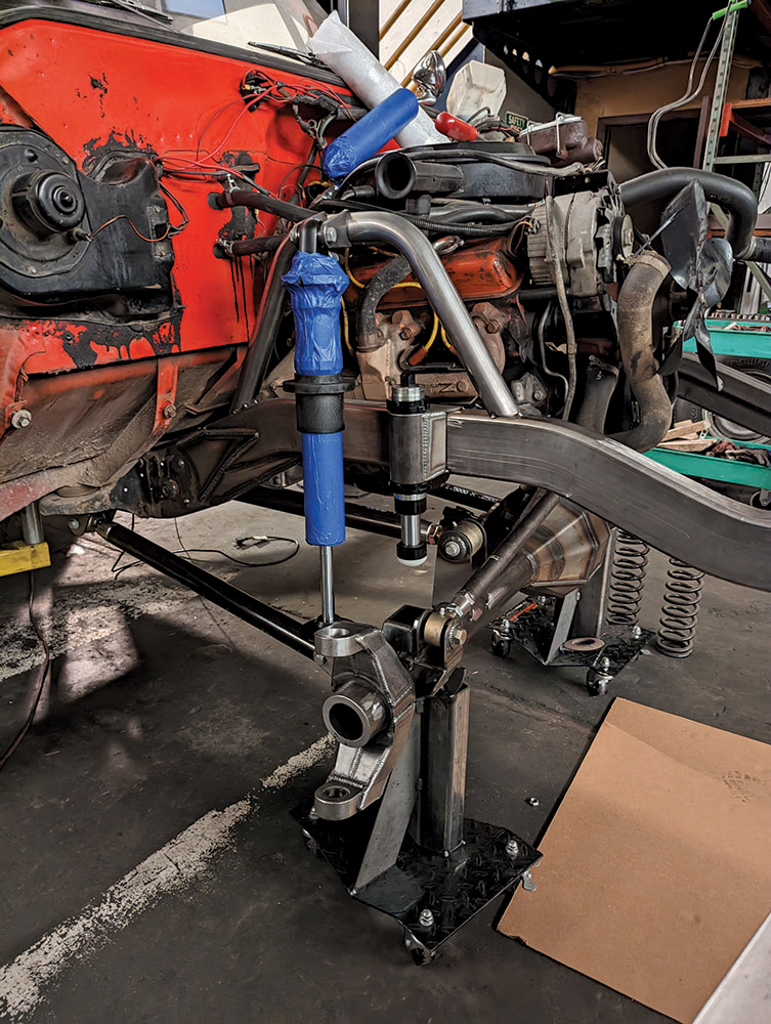
The initial development of the suspension was done by adding a 2×4-inch rectangular tube clip to the GMC framerails. The three-link front suspension used a Panhard bar and coilover shocks. During the development process two front axle assemblies were developed, one with 8-lug hubs the other with 6-lug. Both axles use large-diameter, heavy-duty tubes with fabricated ends that mount fabricated steering knuckles with Super Duty hubs. In both cases axles are 35-spline. The major difference between the 6- and 8-lug axles is the centersection—the 6-lug uses an OEM-style 9-inch housing while the 8-lug uses a fabricated 9-inch housing. On production chassis a variety of Currie gearsets and traction devices will be available; in the case of GMC “Brush 101” 5.13:1 gearsets were installed in both ends with ARB air lockers. To match the capabilities of the front suspension, the rear was set up with triangulated four-bars and coilovers. As with the front axles, 6- and 8-lug versions of the rear axle assembly will be offered.
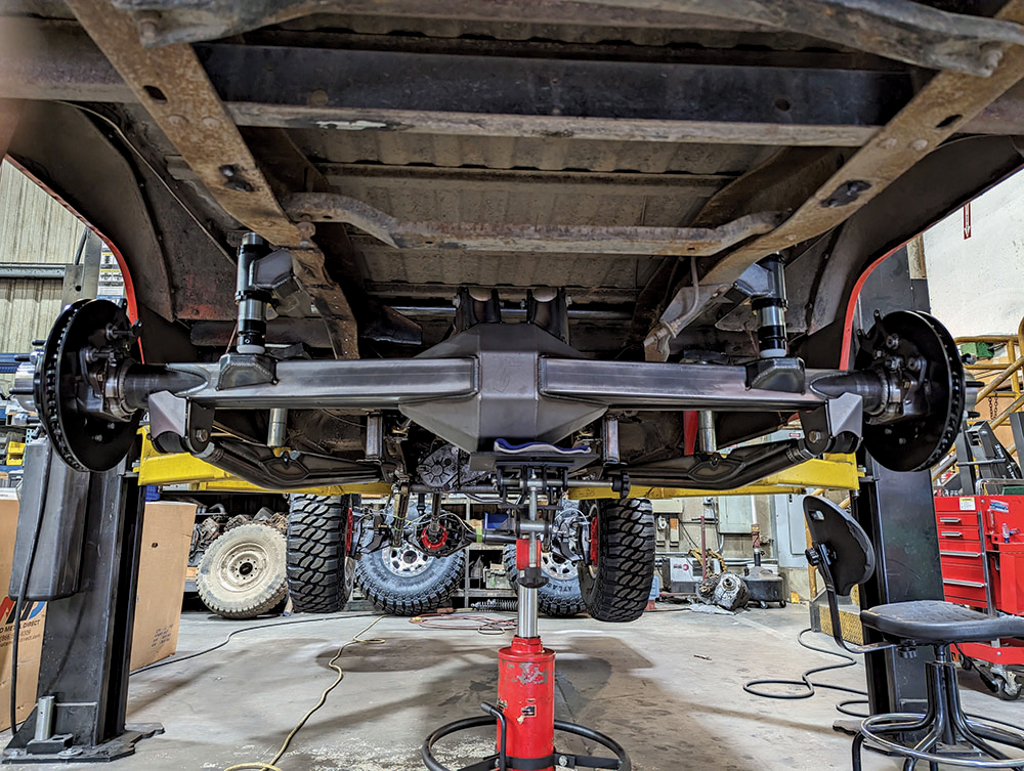
With the front and rear suspension thoroughly tested, the AME engineering staff went about designing a new frame. The main rails are fabricated from 2×6-inch rectangular tubing blended into mandrel-bent 2×4 rectangular tubing at each end; frames will be available for short and long wheelbase applications. These new frames are much stronger than the originals, providing a much more stable platform for the long travel suspension. But don’t let the rugged look fool you, this chassis is as at home on the road as it is off of it—and no cutting is required for installation.
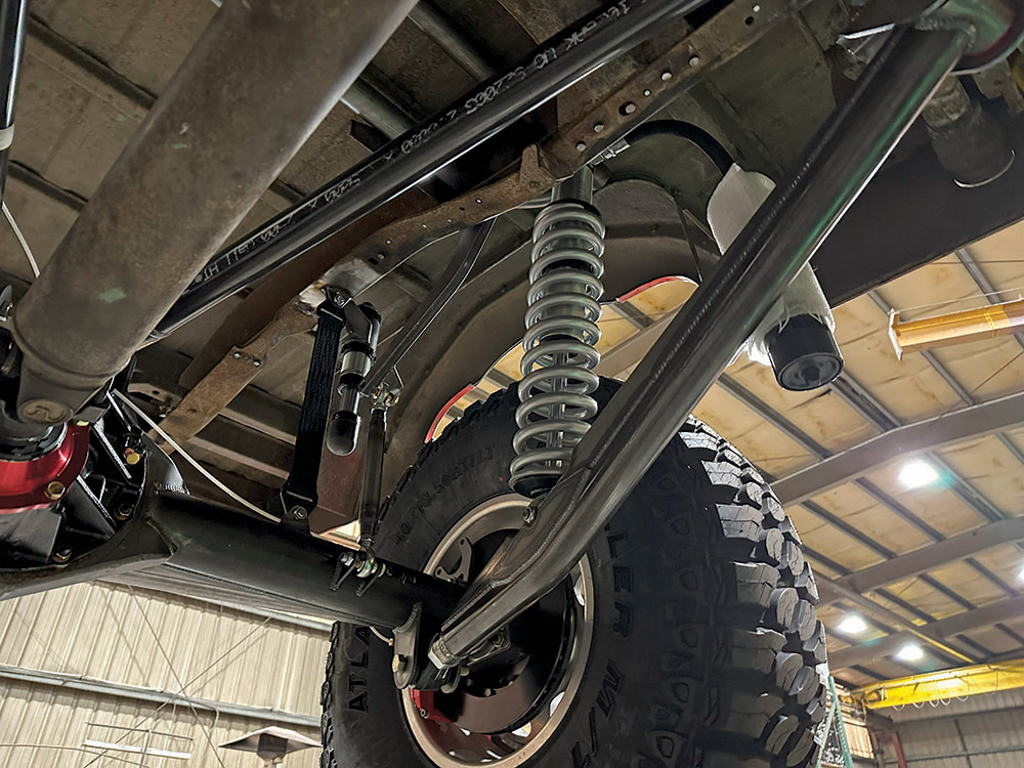
AME broke new ground with the development of replacement automotive chassis that gave owners of vintage vehicles the opportunity to experience the best in contemporary handling characteristics. Now AME is bringing that same level of performance to four-wheel drive fans as well. Think of it as the new ground being broken regardless of whether it’s asphalt or dirt.
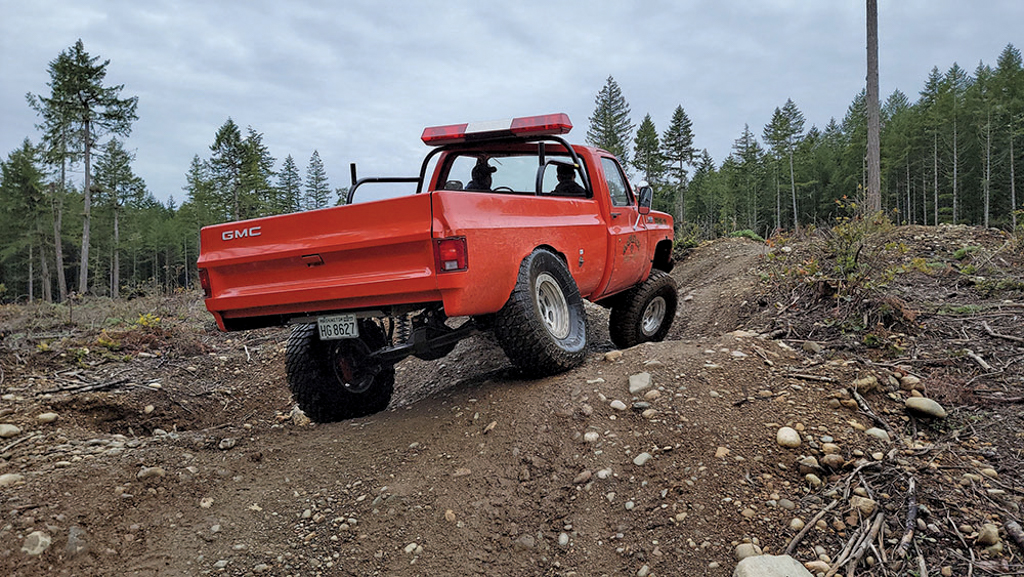
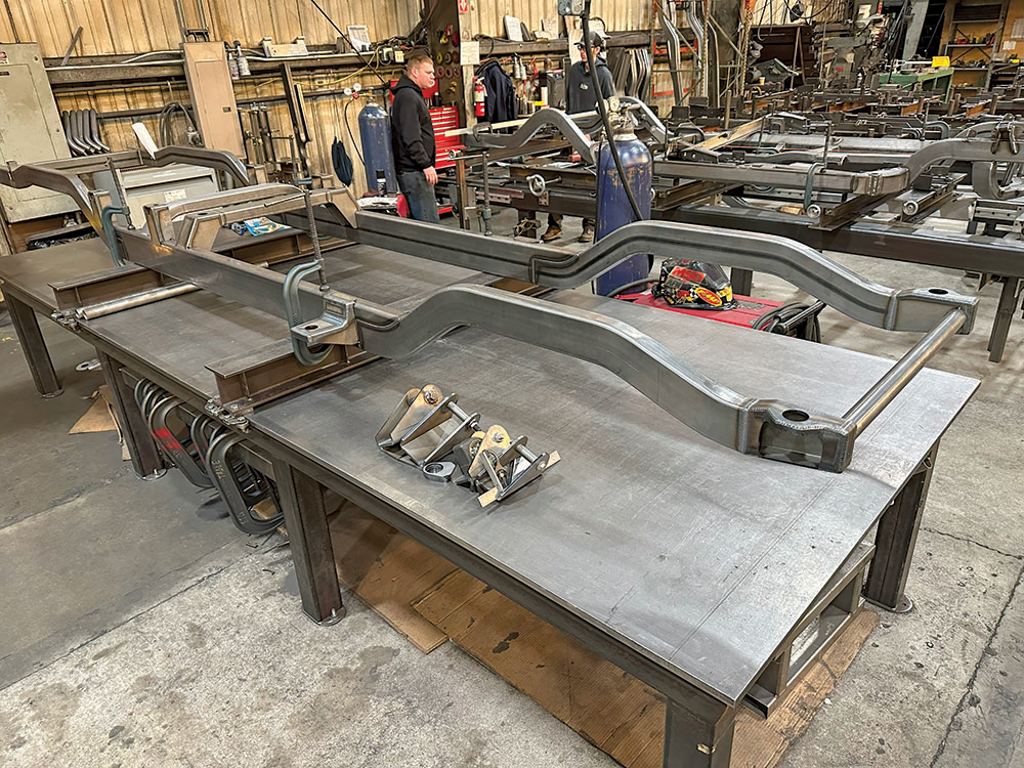
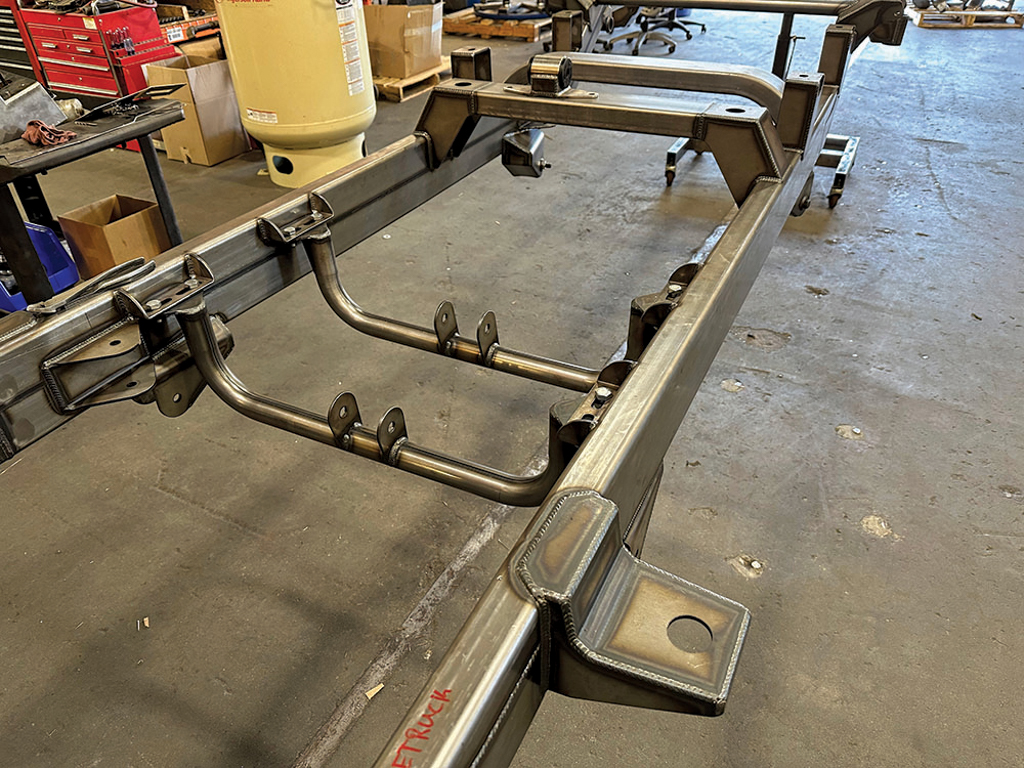
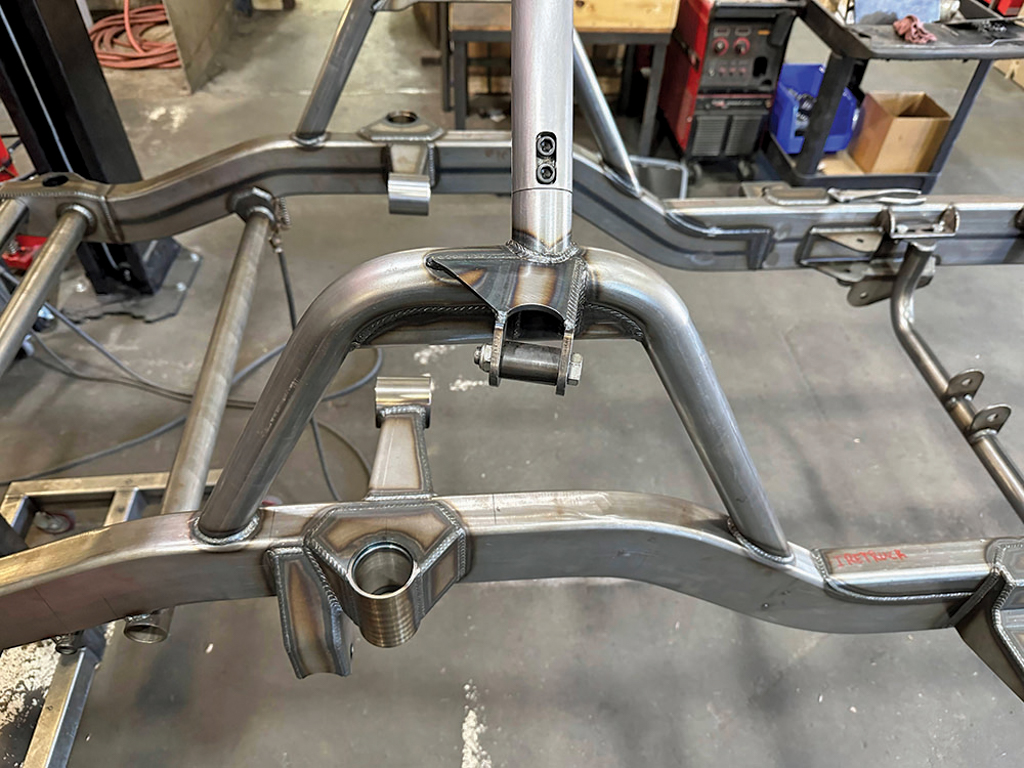
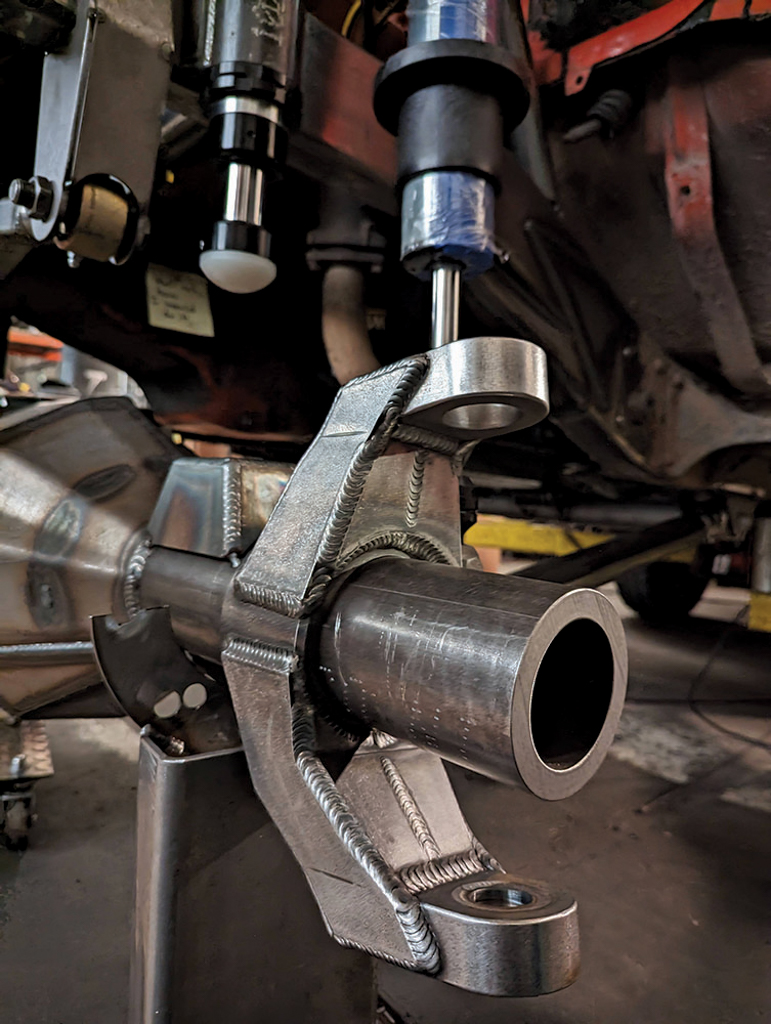
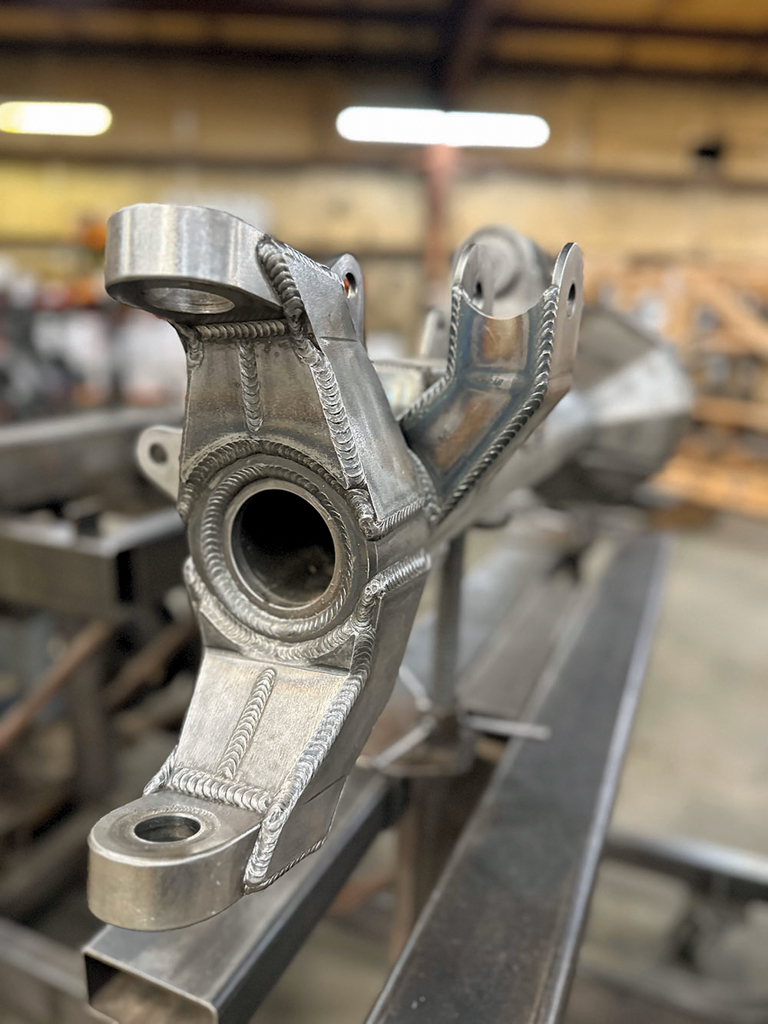
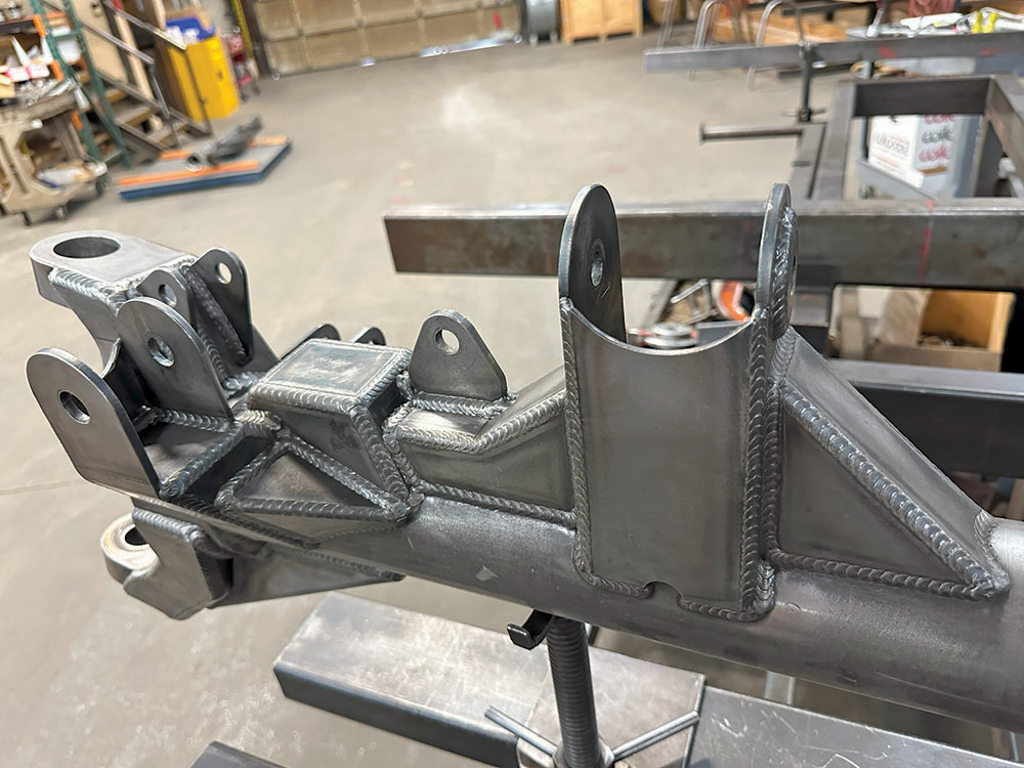
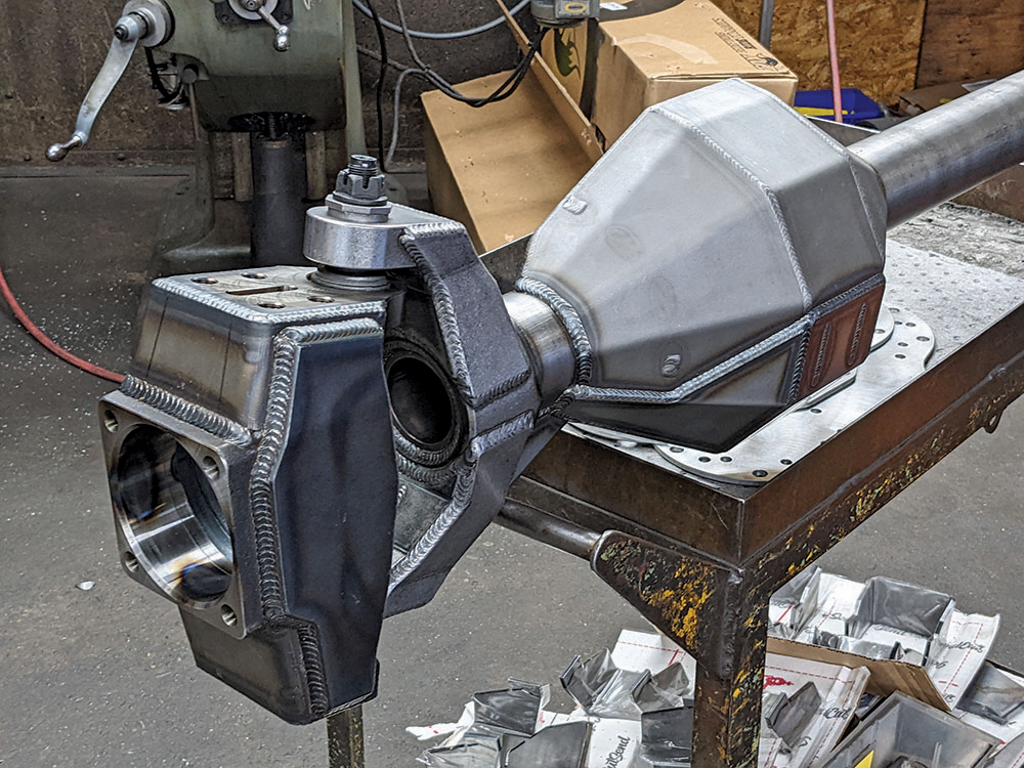
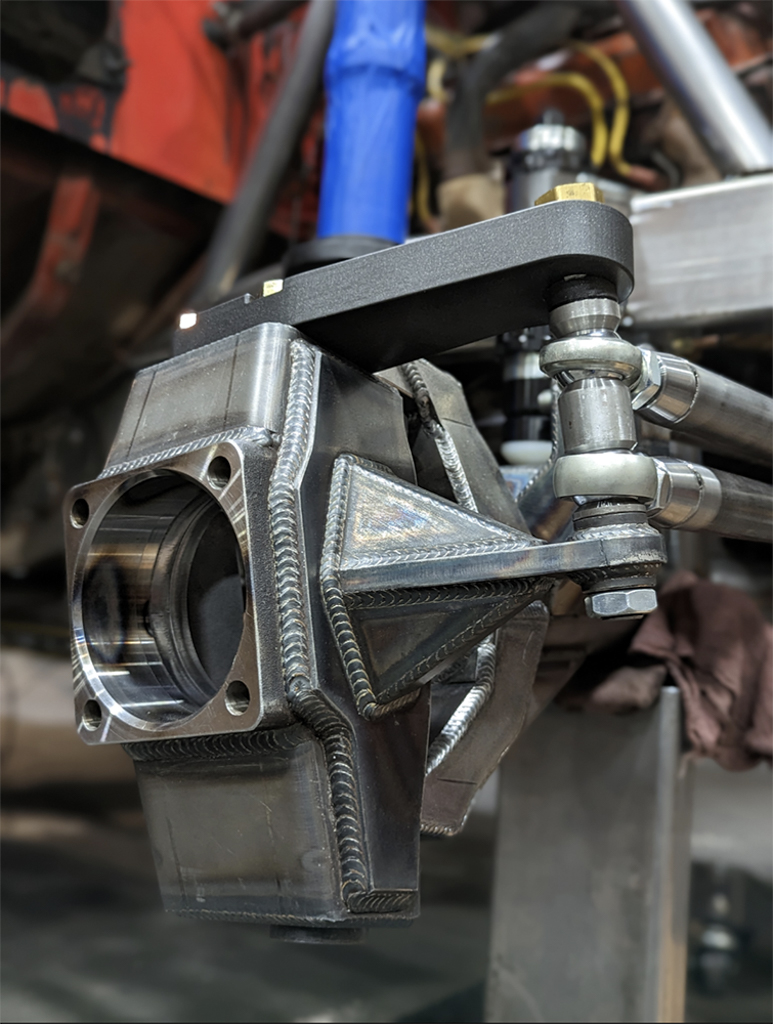
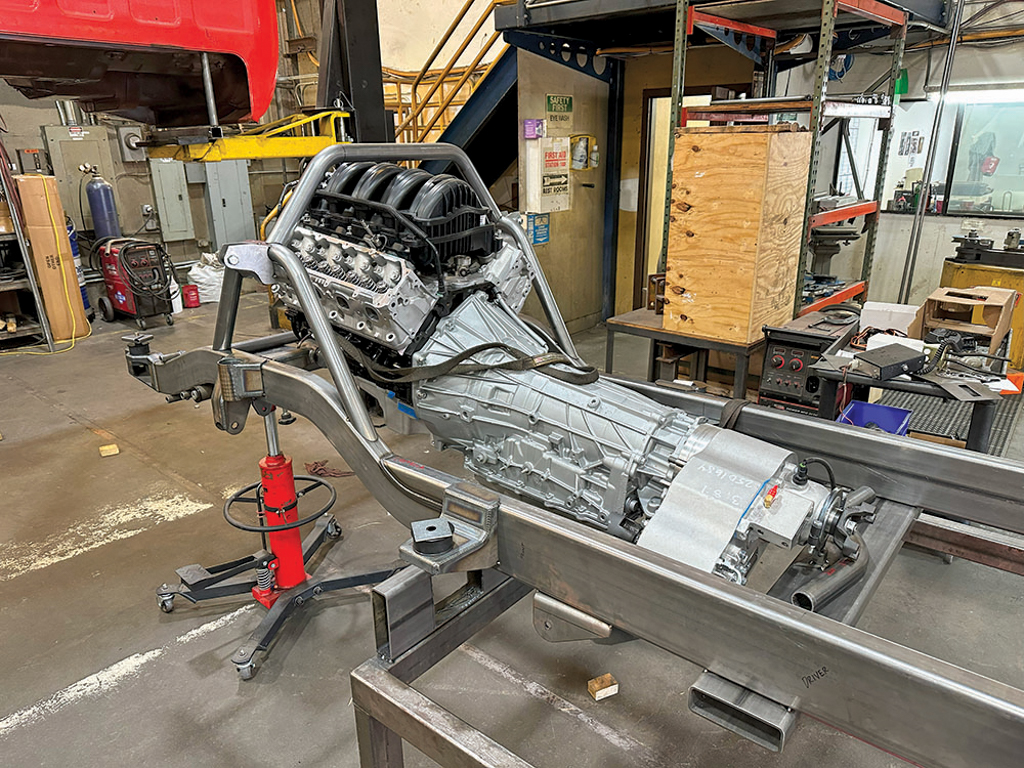
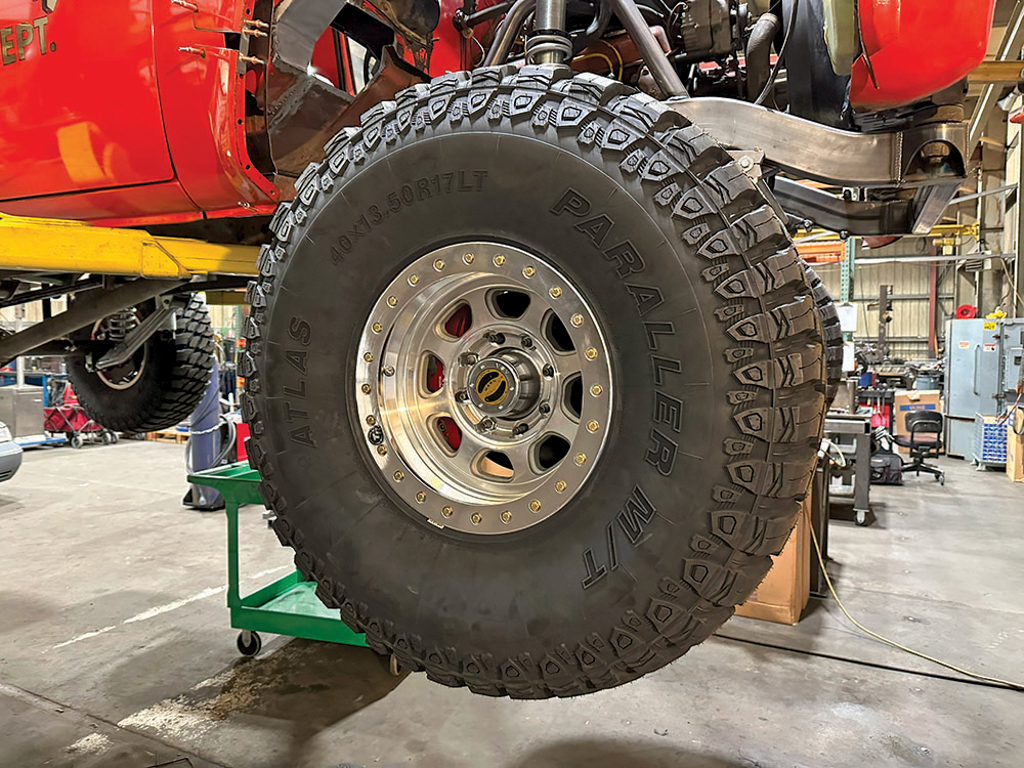
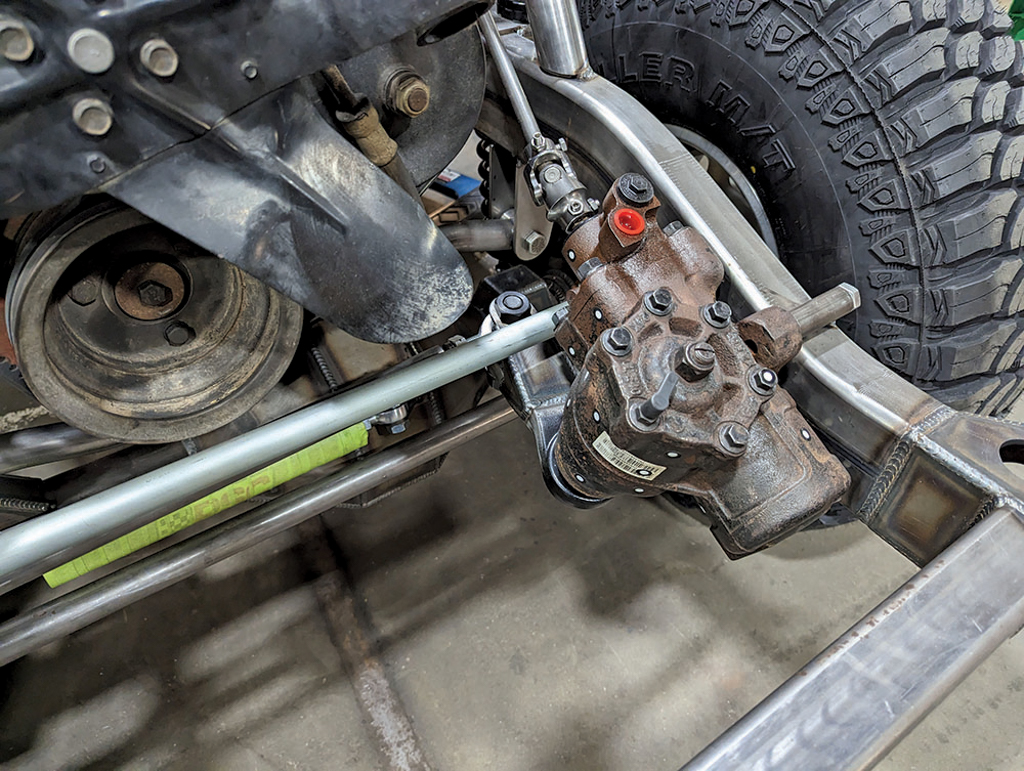
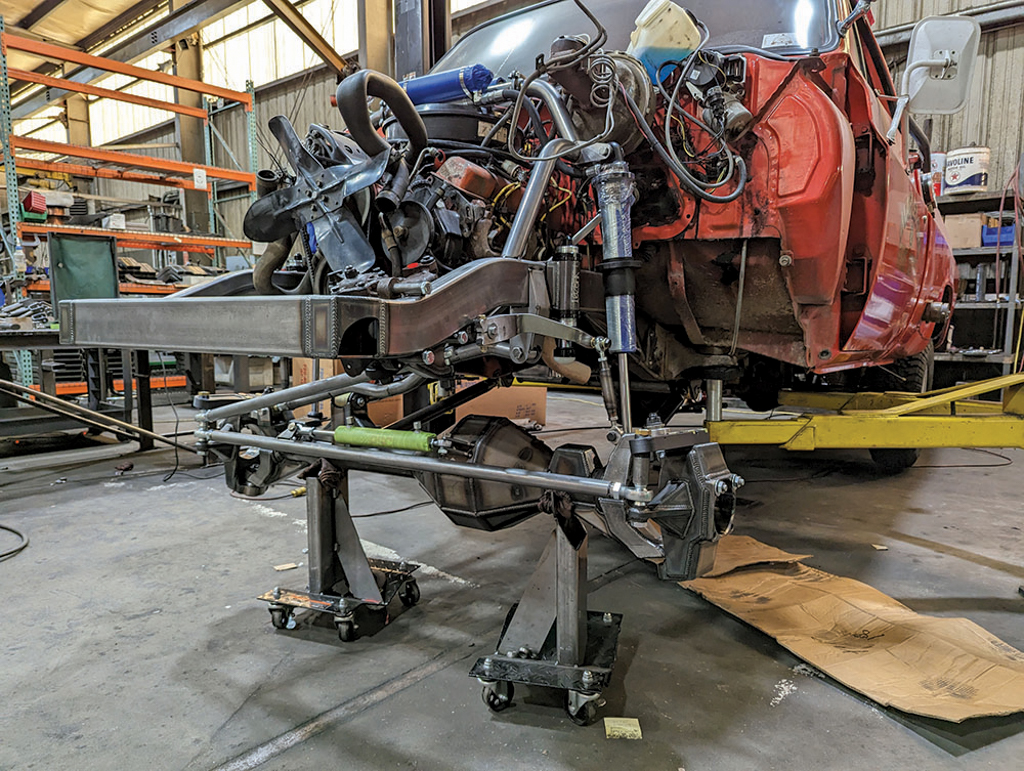
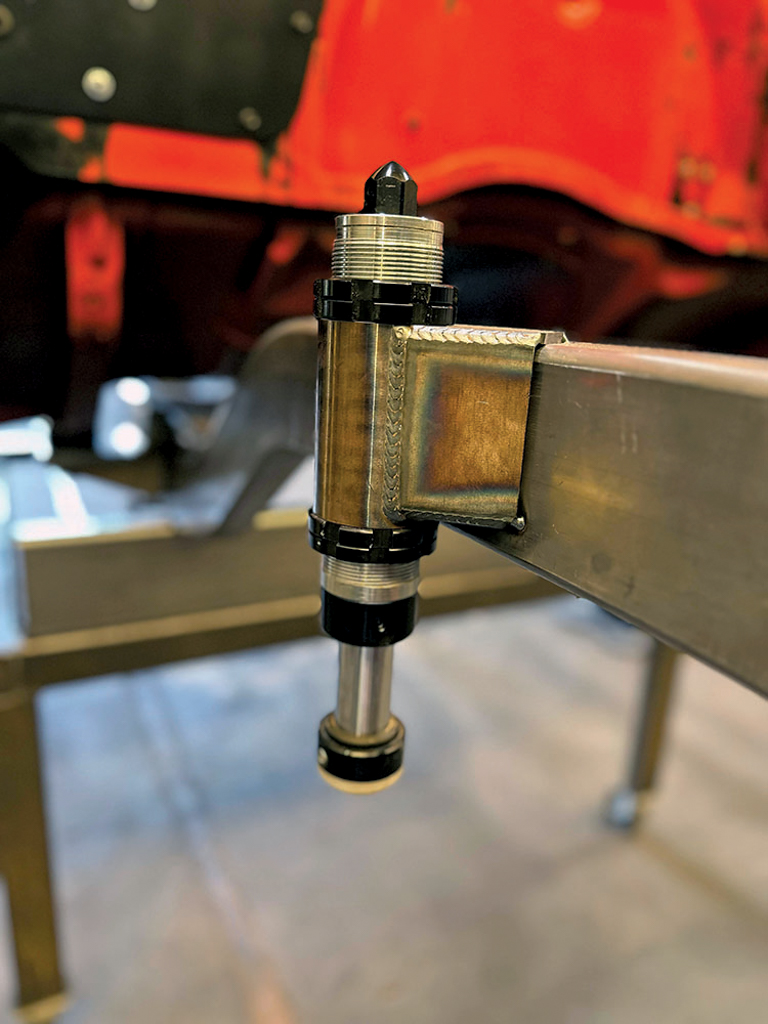
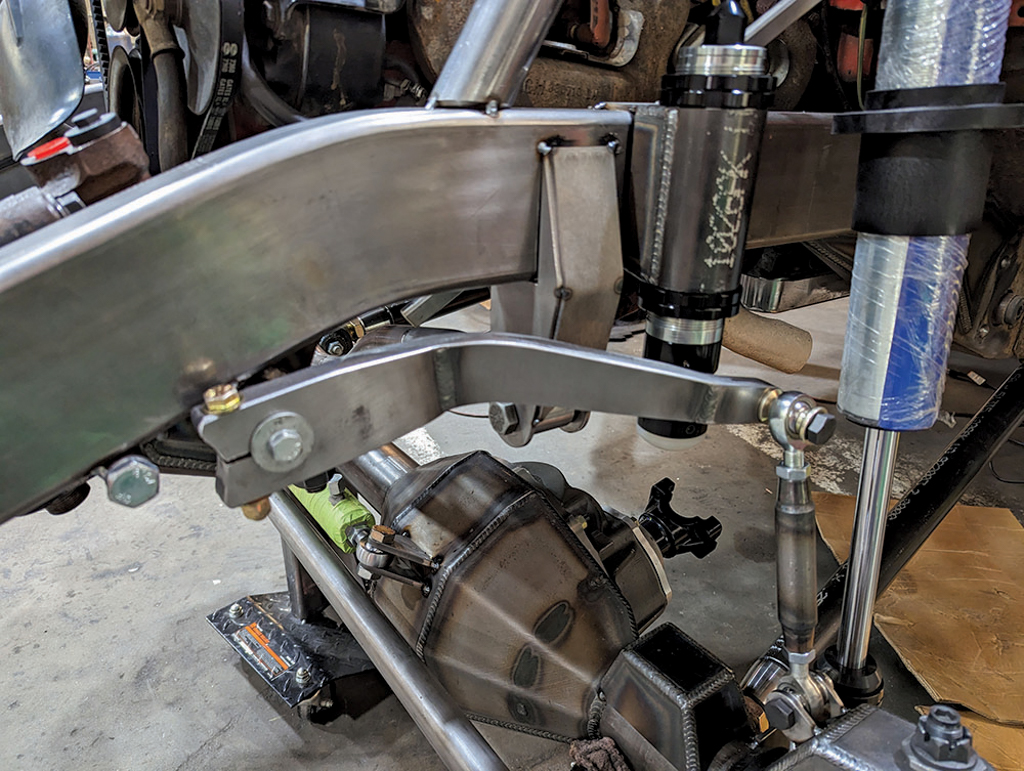
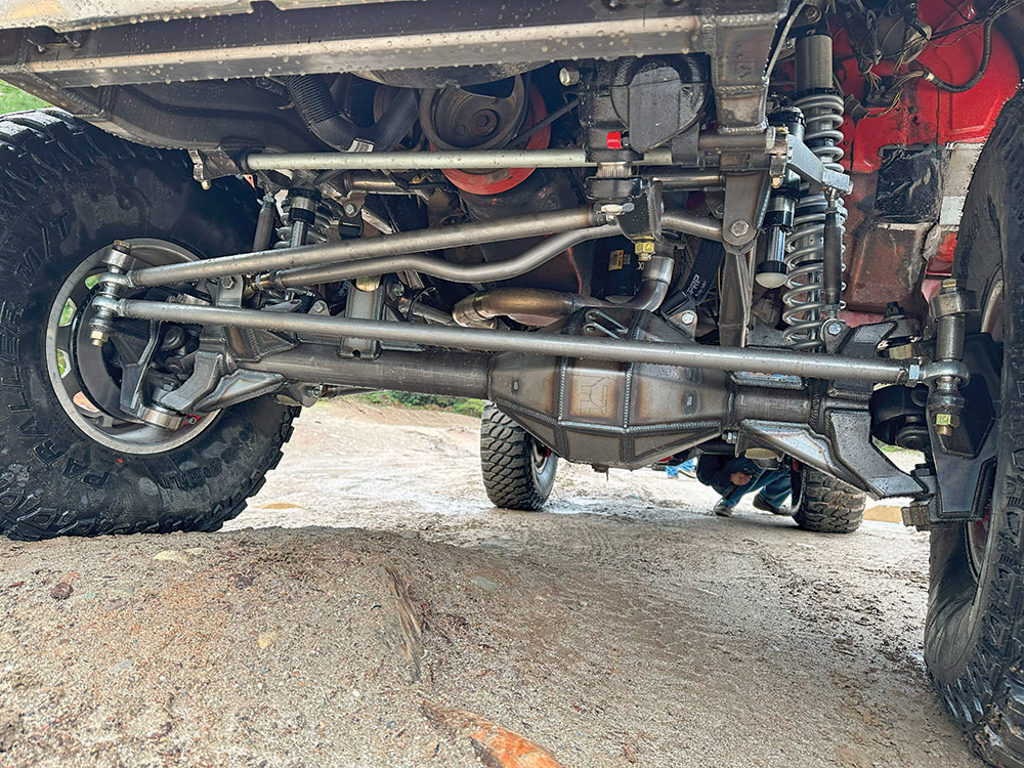
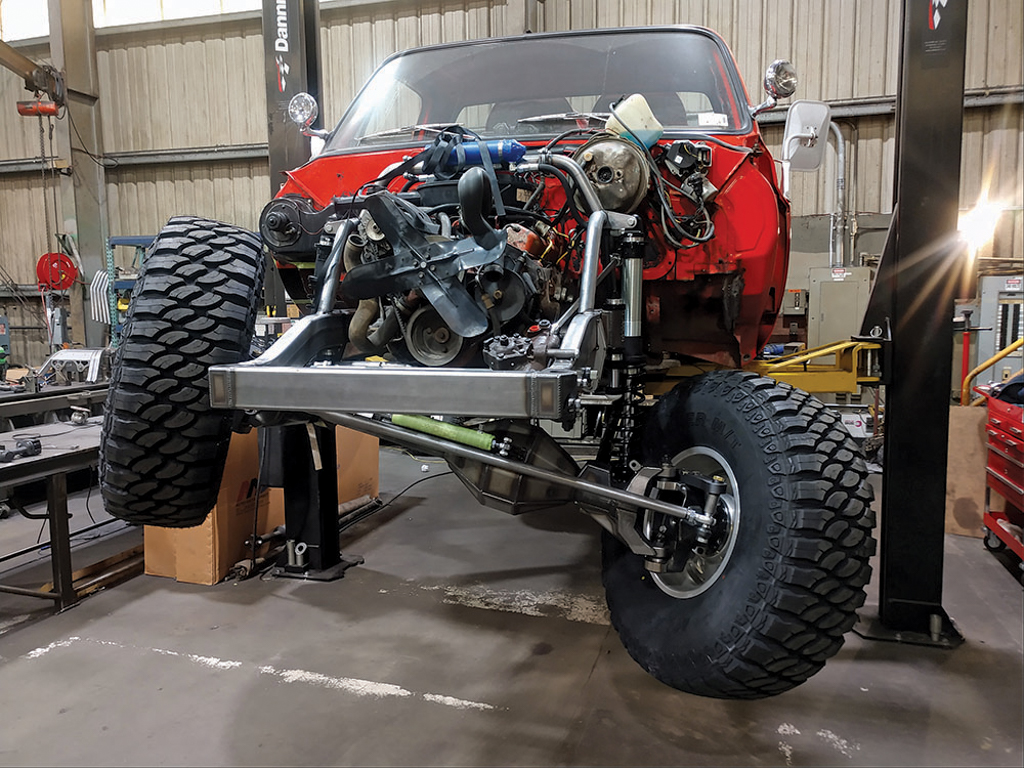
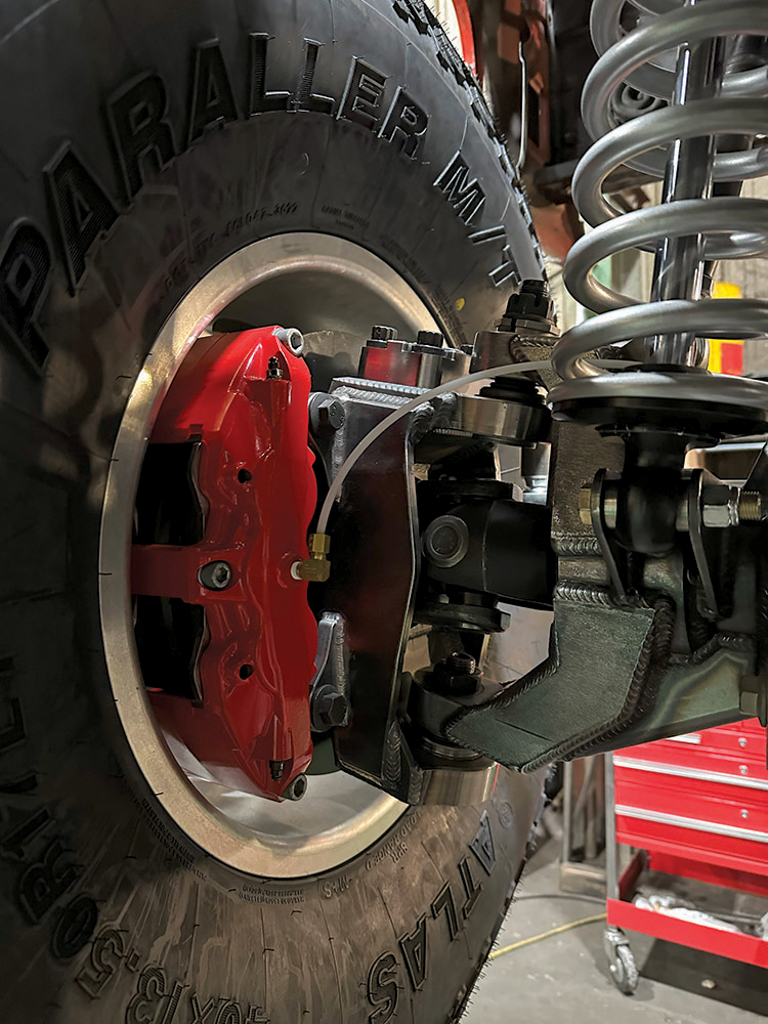
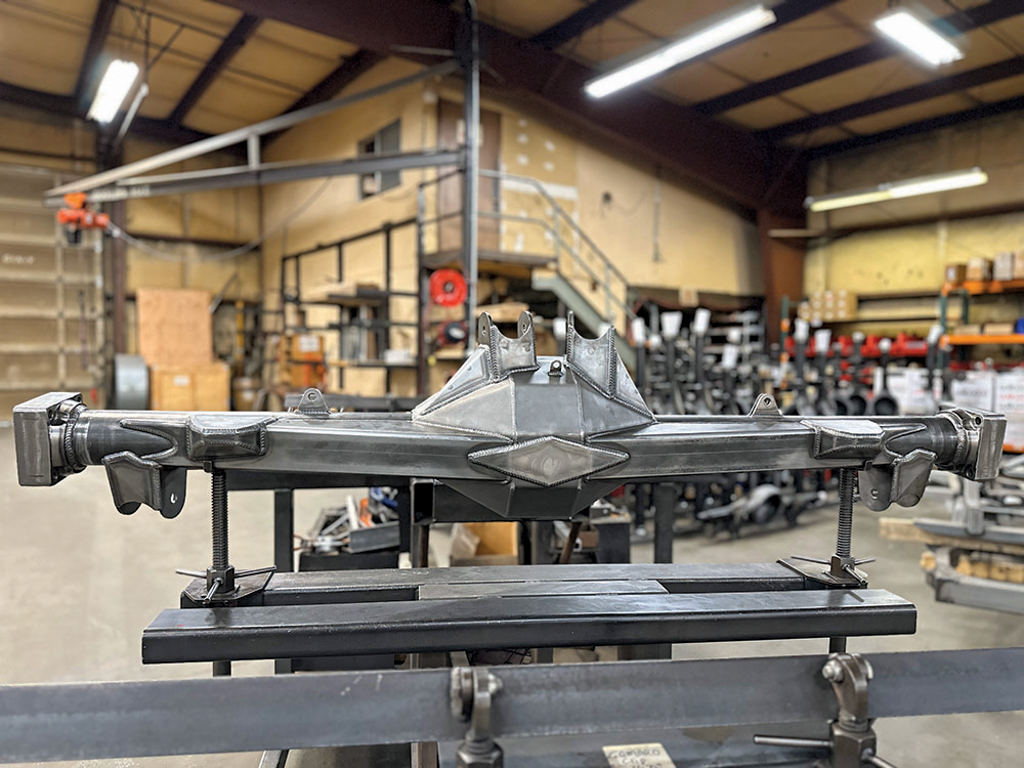
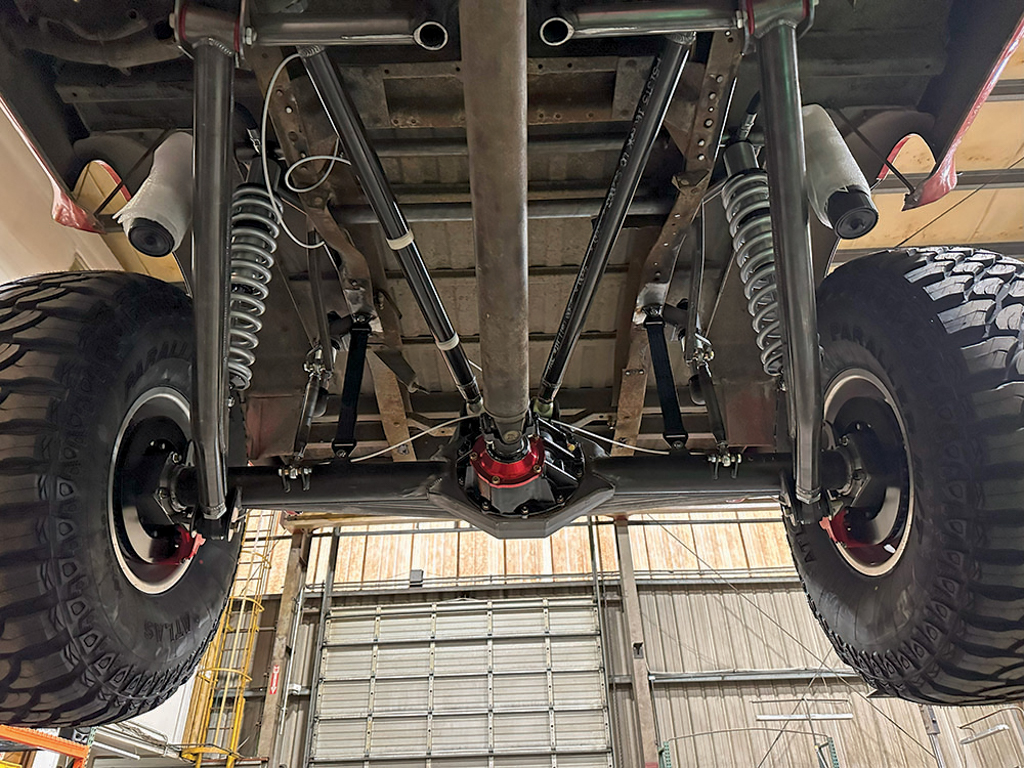
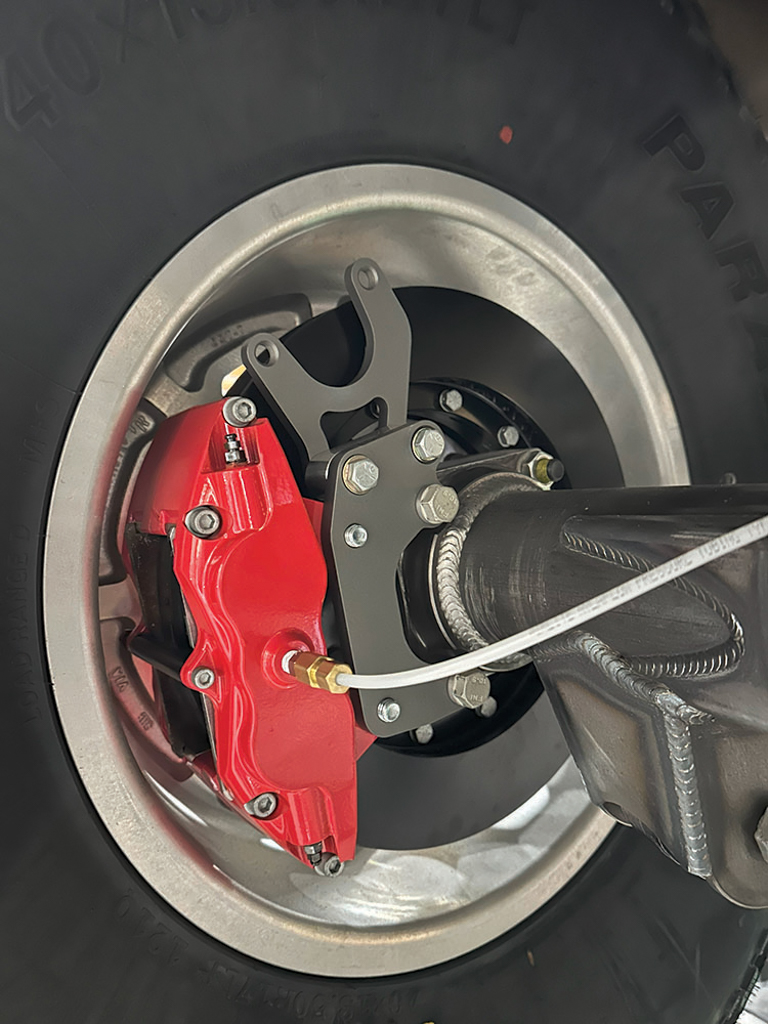
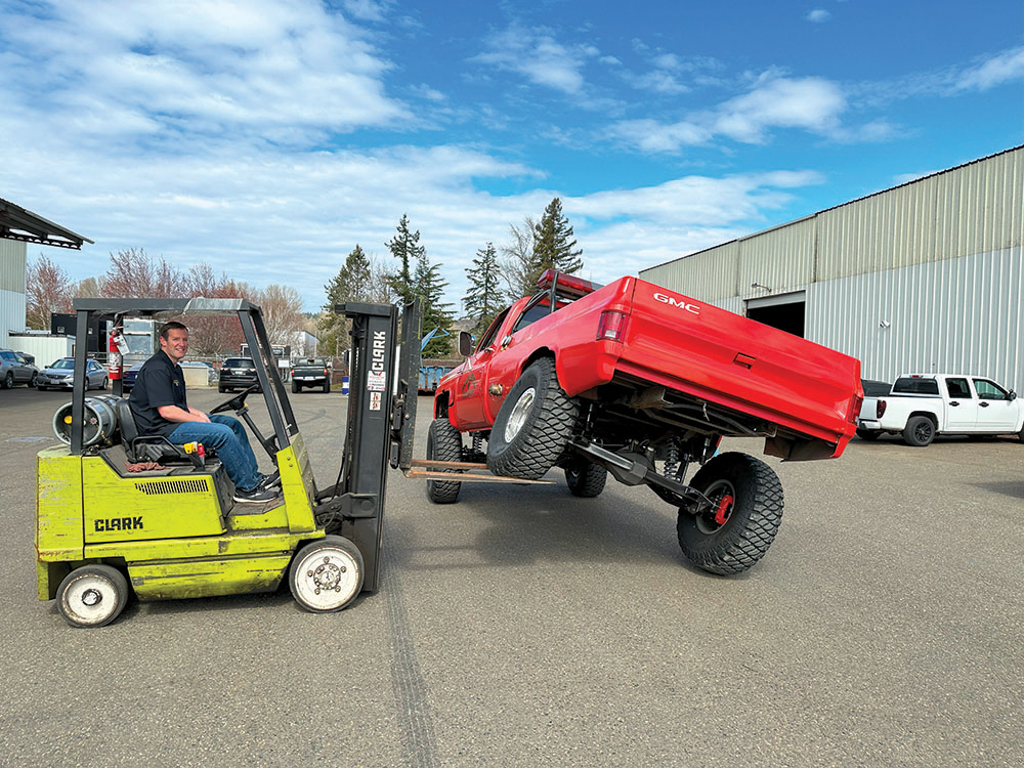
SOURCE
Art Morrison Enterprises
(800) 929-7188
artmorrison.com