Long Bed to Short Bed Conversion With Golden Star Classic Auto Parts
By Ryan Manson – Photography by the Author
With our longbed-to-shortbed conversion on our 1969 Ford F100 a wrap as far as the chassis goes, it’s time to turn our attention to the part that will really bring to life the transformation, the short bed truck sheet metal. In the past there was no easy way to convert the long bed truck sheet metal down to short bed specs. Slicing a full 16-inch section out of the front bedsides and floor, as well as an additional 4-inch section out back, makes for a ton of cutting and welding, not to mention the grinding and sanding involved to get the sheet metal smooth enough for body and paint. A challenge on the double-walled smooth bedsides to be sure, but grinding the two seams nice and smooth on the corrugated steel floor would be something akin to Chinese water torture. For most home builders this puts the conversion out of reach as far as skill set or budget resources allowed. But thanks to the recent introduction of reproduction steel bedsides from Golden Star Classic Auto Parts, converting that long bed Ford down to a short box Fleetside Ford is a simple matter of swapping a few sheet metal components.
Read More: 1967-1972 Ford F100 Short Bed Conversion Part 1
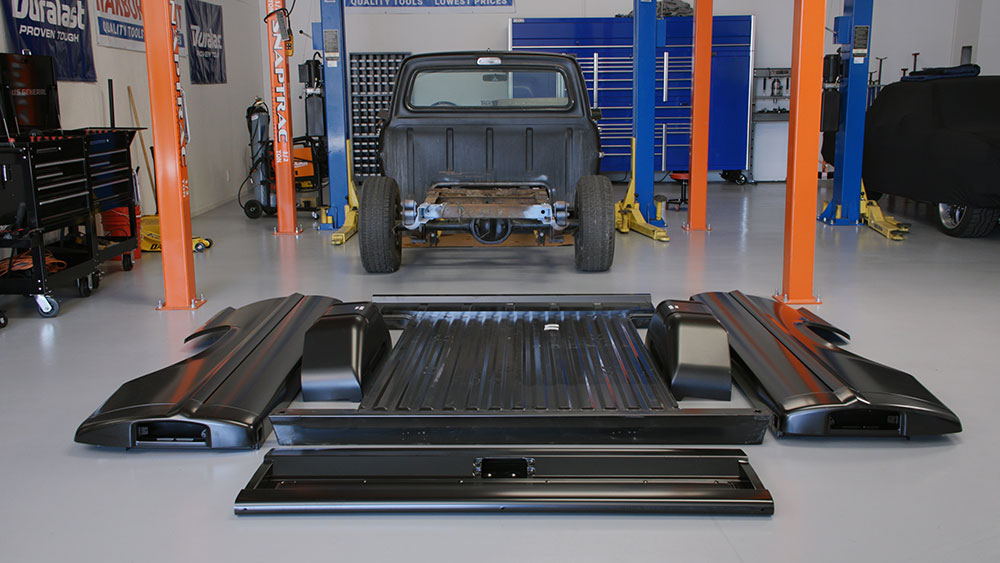
Now, before we get too carried away with the simplicity of this portion of the project, it should be mentioned that unlike the GM trucks of the era, the Ford truck beds were assembled by spot welding multiple sheet metal components, as opposed to GM’s simpler, screwed-together assembly. Due to this fact, we opted to replace our entire bed assembly with new sheet metal, all thankfully available from Golden Star Auto. While this may seem like a large pill to swallow at its onset, after considering the probable shape of the few panels that can be reused in addition to the labor involved in drilling out the spot welds and removing said panels, one is likely money ahead by springing for the entire truck bed package.
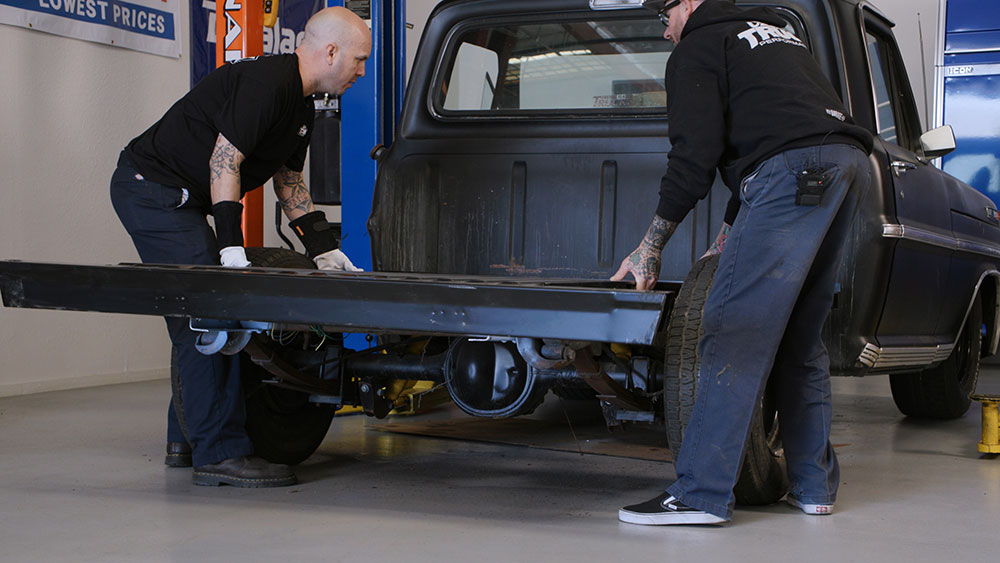
In fact, considering the front bed panel and tailgate being the two panels that are the best candidates for reuse, these are also likely to be the most damaged two panels of the bed, making another argument for complete replacement. Of course, every build is different and swapping out your stock tailgate onto that new bed is completely possible, provided it’s in decent shape. But other than those two and the pair of wheelhouse panels, there aren’t any other panels that interchange when going from a long bed to short.
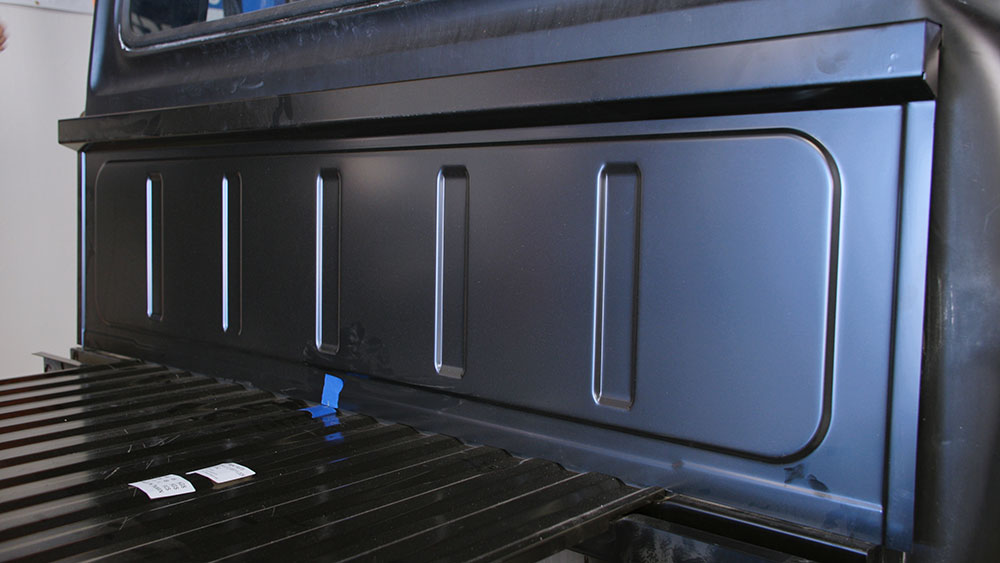
Read More: How Roadster Shop Improved The 1953-1955 F100 Chassis
The fact that the Ford truck beds were welded together makes assembly of the new sheetmetal a slightly more difficult task than the assembly of a GM truck bed. Where the GM components may have had a few holes on each panel to aid in lining up said panels during rough assembly, the Ford tin needs to be carefully assembled, first using a series of clamps, followed by a few carefully placed sheet metal screws or Clecos to hold things together as the assembly progresses. This process also requires the complete assembly of the bed panels before any welding can be performed, due to the necessity to check for final fit of said panels, bed square, and proper assembly process and panel overlap. We’ll be mimicking the factory spot weld process by punching holes in the overlying panels and then welding the two panels together. Similar in nature to the factory spot welds, this process is known as rosette or plug welding. To do this, we’ll need to know the precise location of where each panel overlaps so as to not only punch the hole in the proper location, but where to remove the e-coating (the rust-preventing factory coating Golden Star Auto applies to every panel) so a proper, clean weld can be achieved.
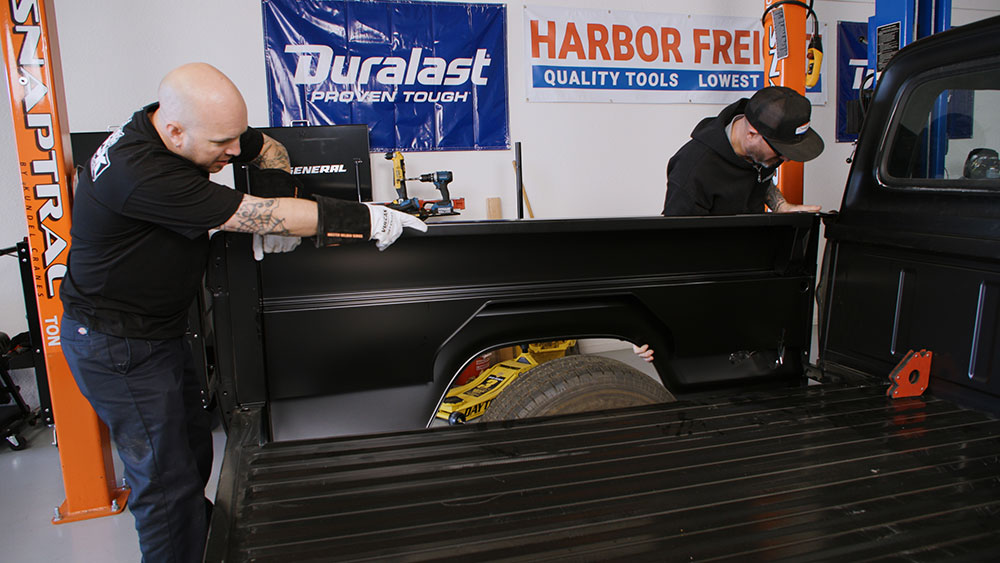
Read More: The Perfect Ford F100?
While this might sound labor intensive, assembling the bed and welding the panels together for our project F100 was accomplished in less than a day. Compared to modifying all the panels that are required to be sliced and diced to take the long bed sheetmetal down to short bed specs, this process is not only much faster, but will result in a product that is ready to send straight to the paint shop, with minimal bodywork required. Spending a little more money up front, while saving a massive amount of time, labor, and money on the back end, makes assembling a new short bed out of Golden Star Auto sheet metal a much more sensible approach. CTP
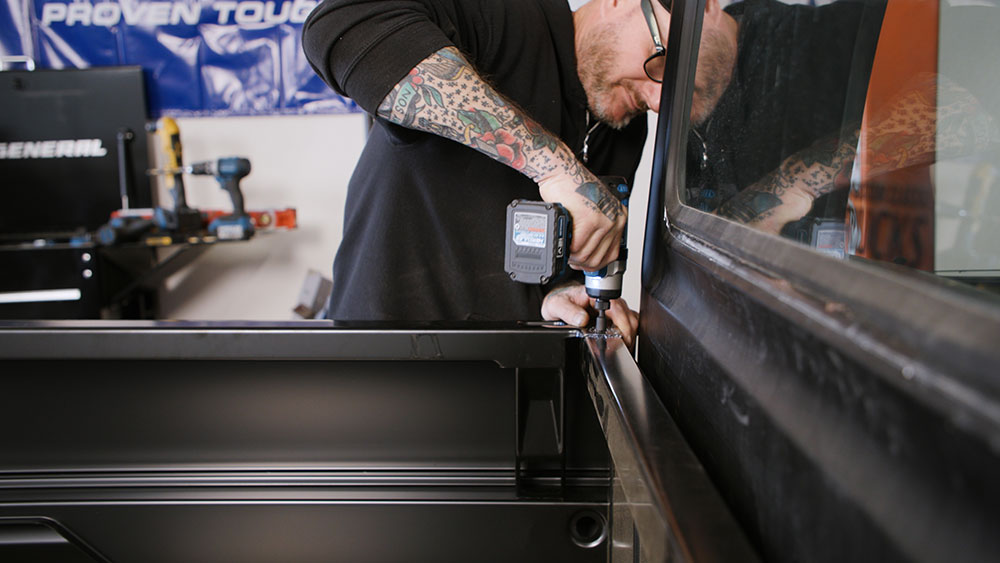
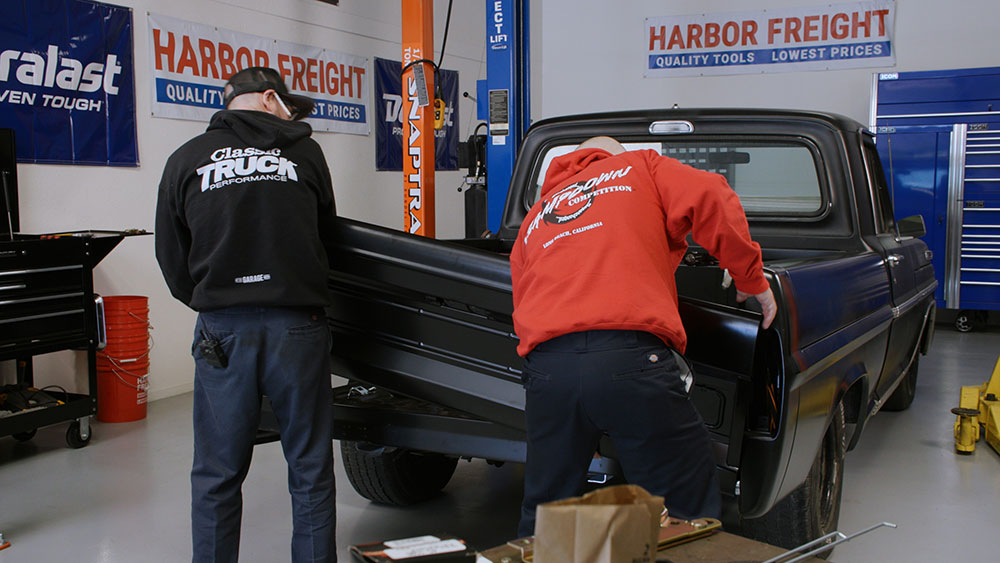
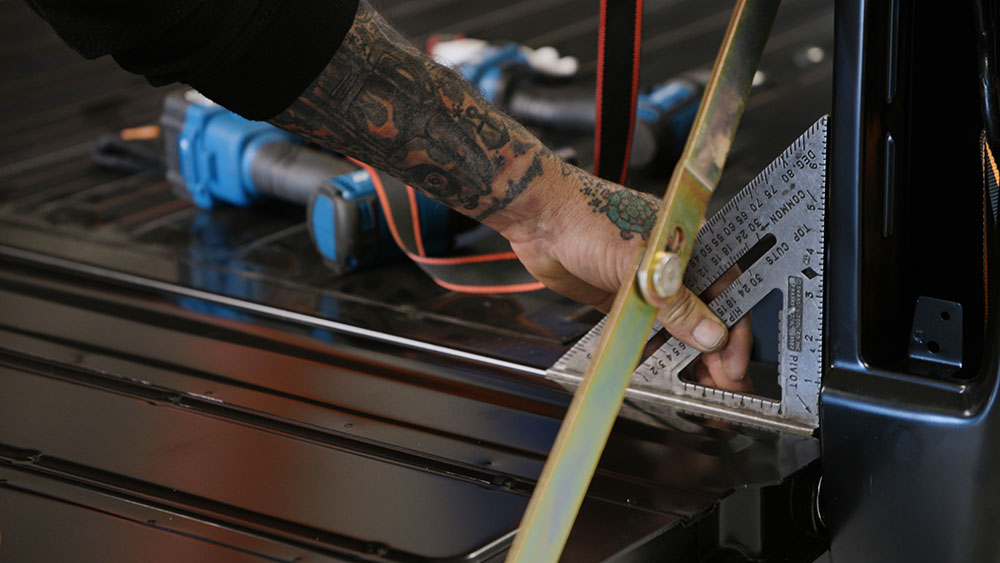
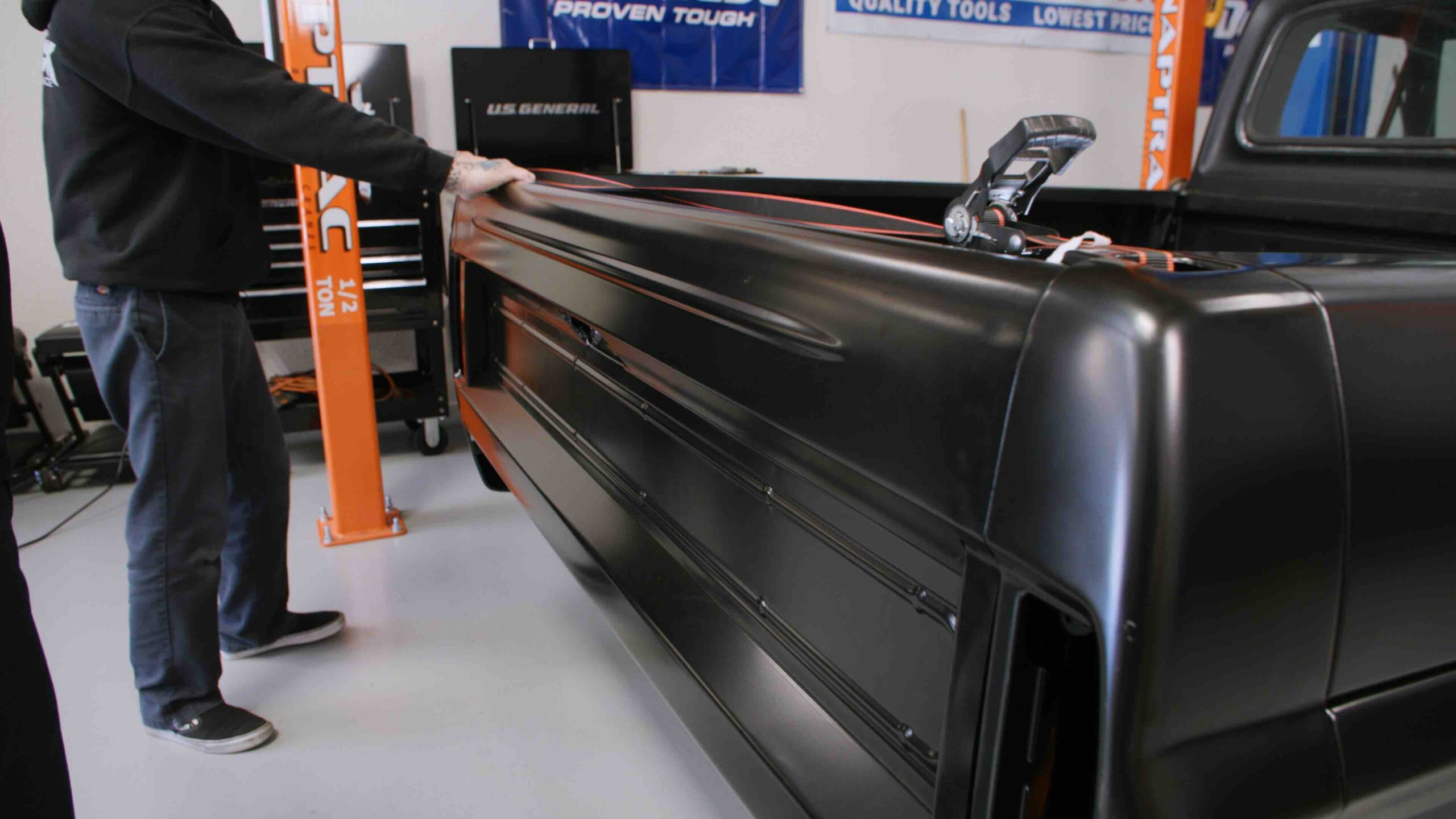
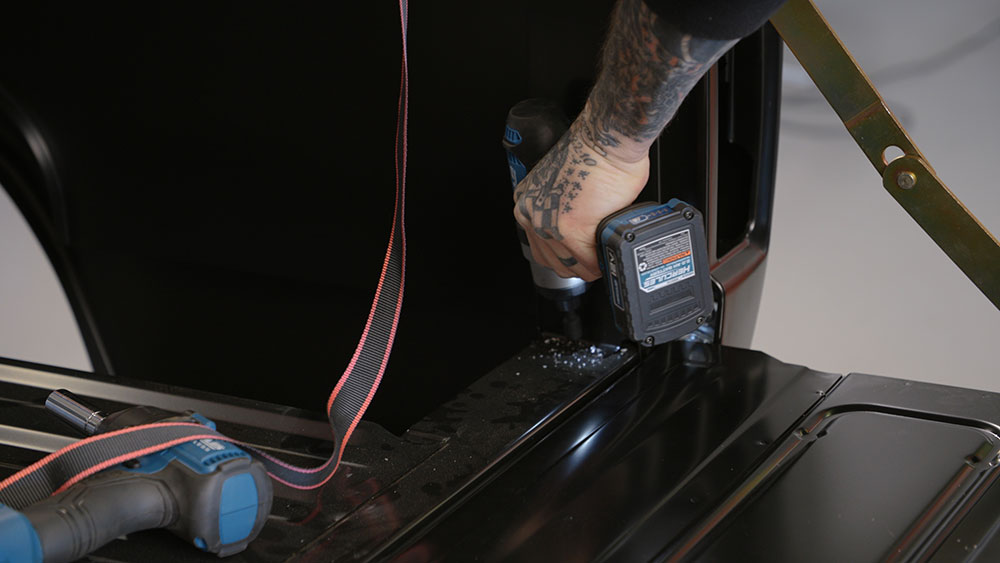
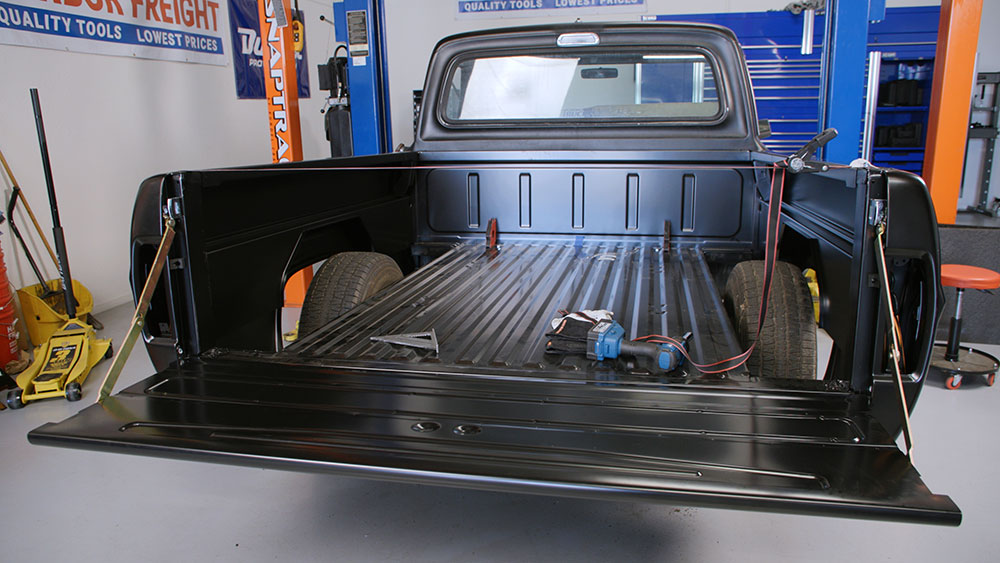
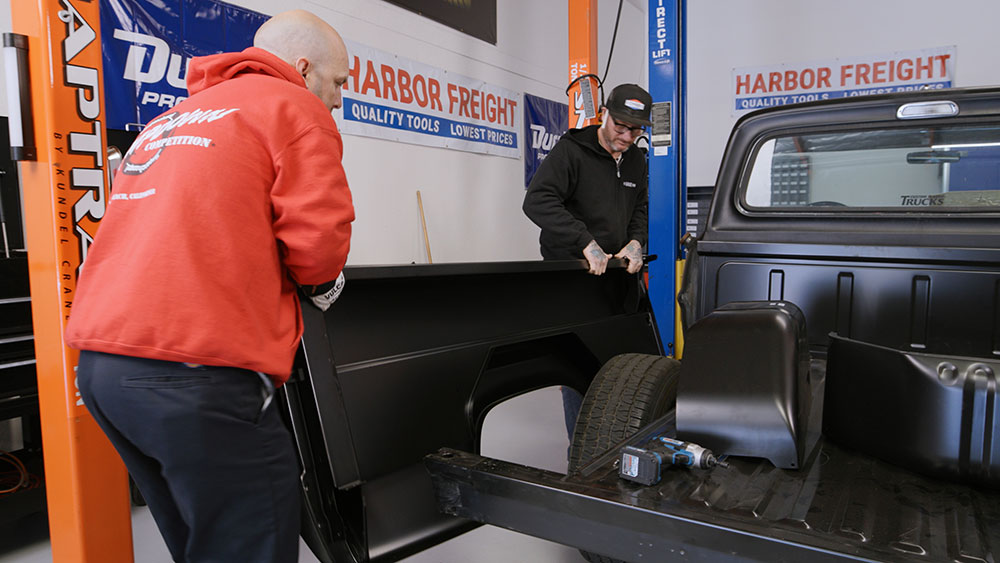
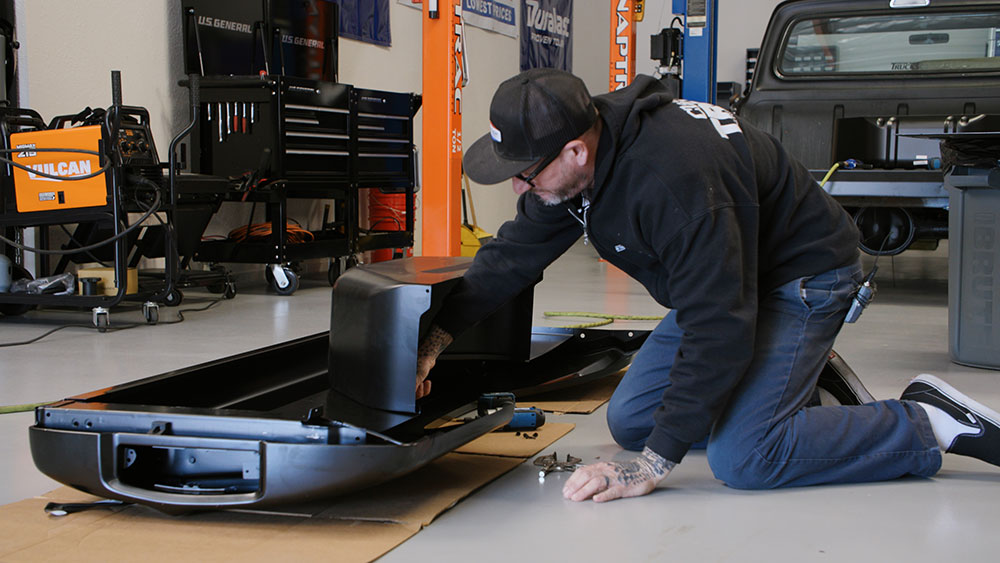
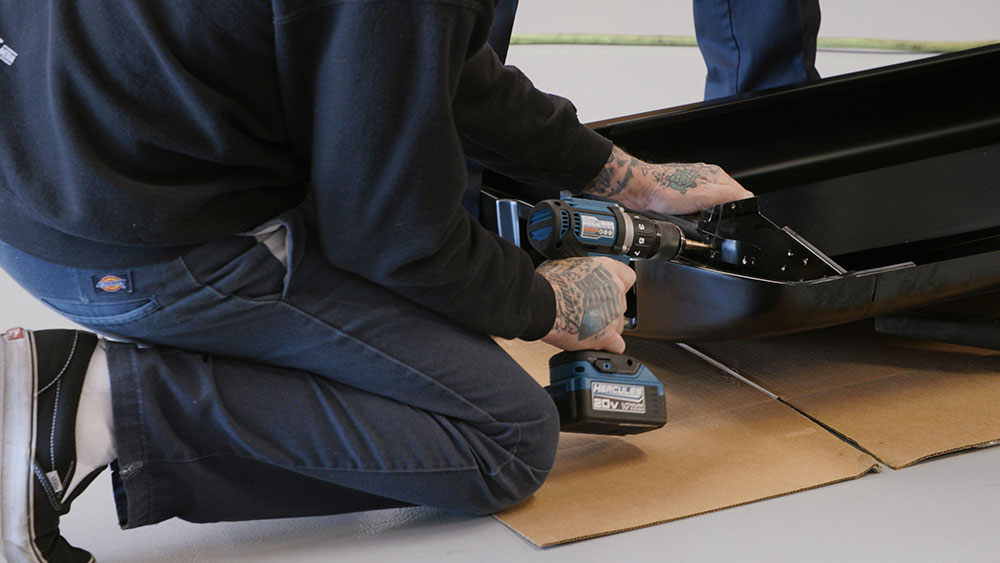
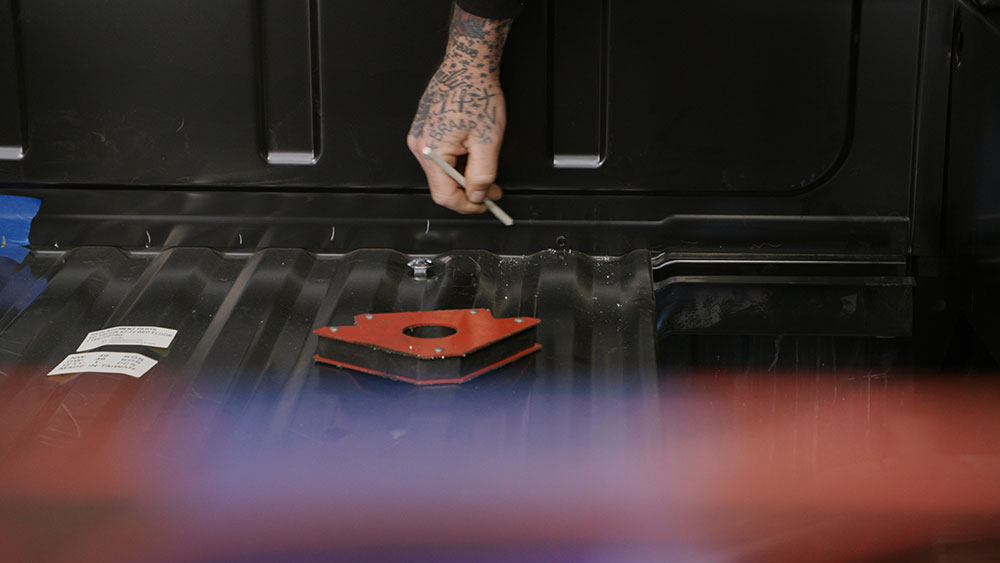
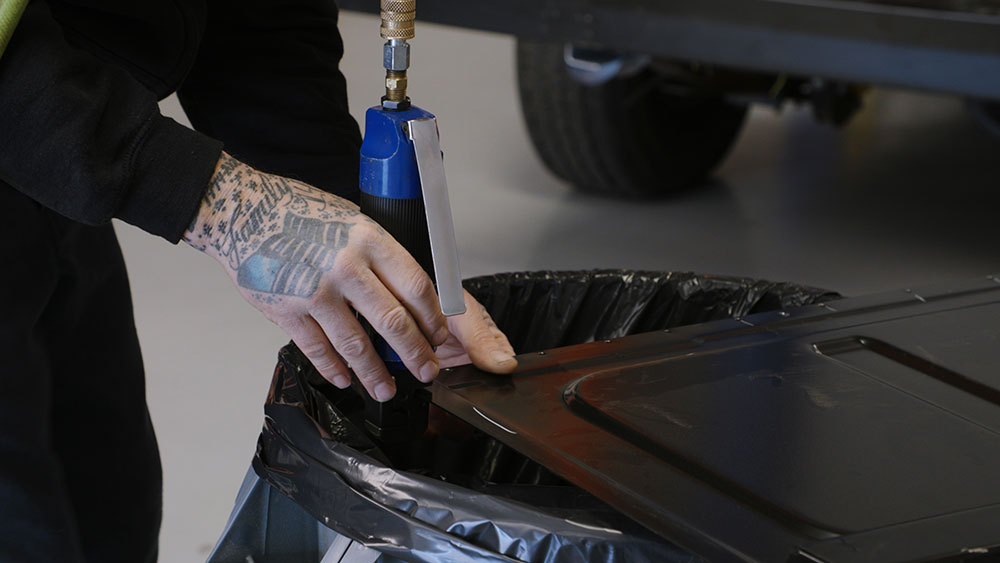
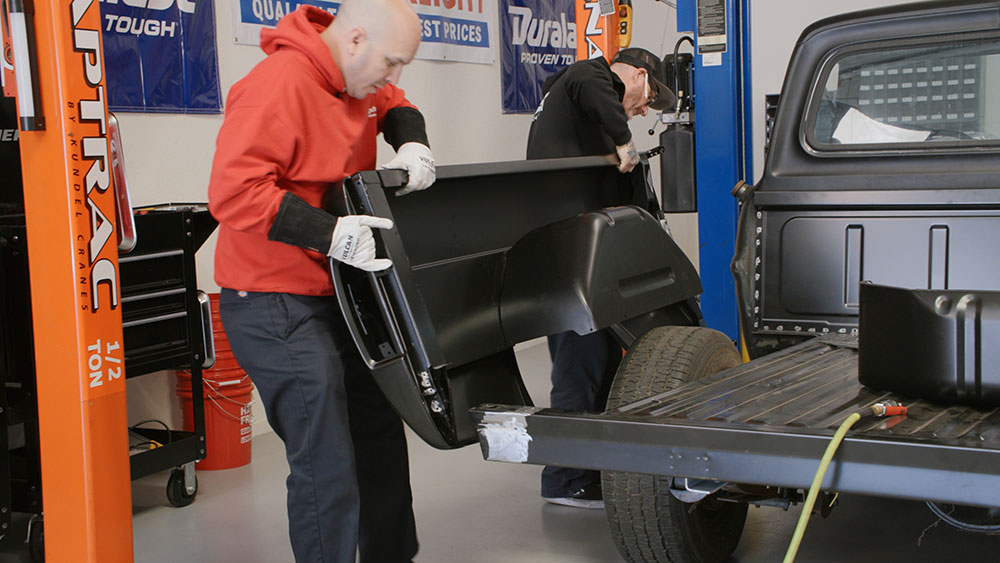
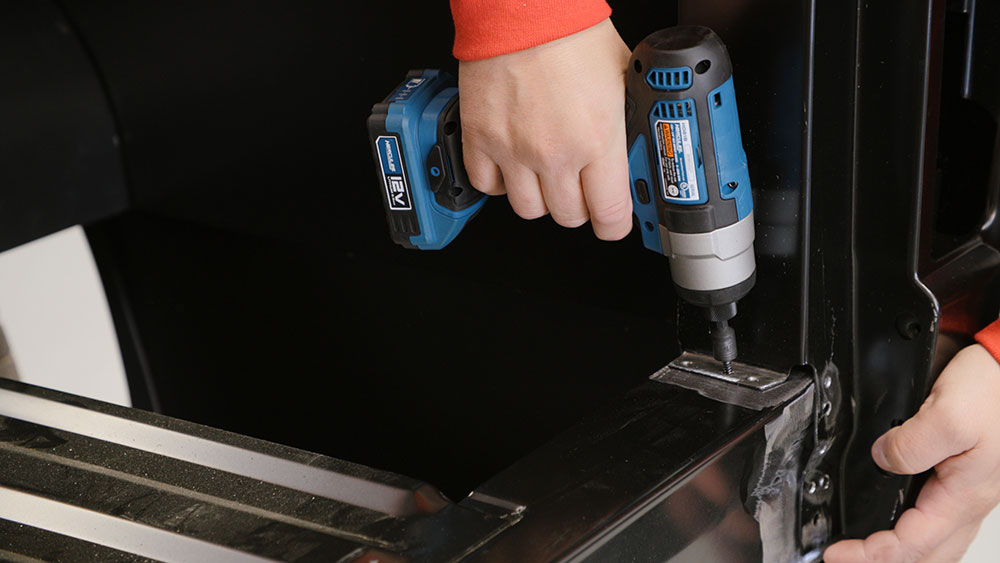
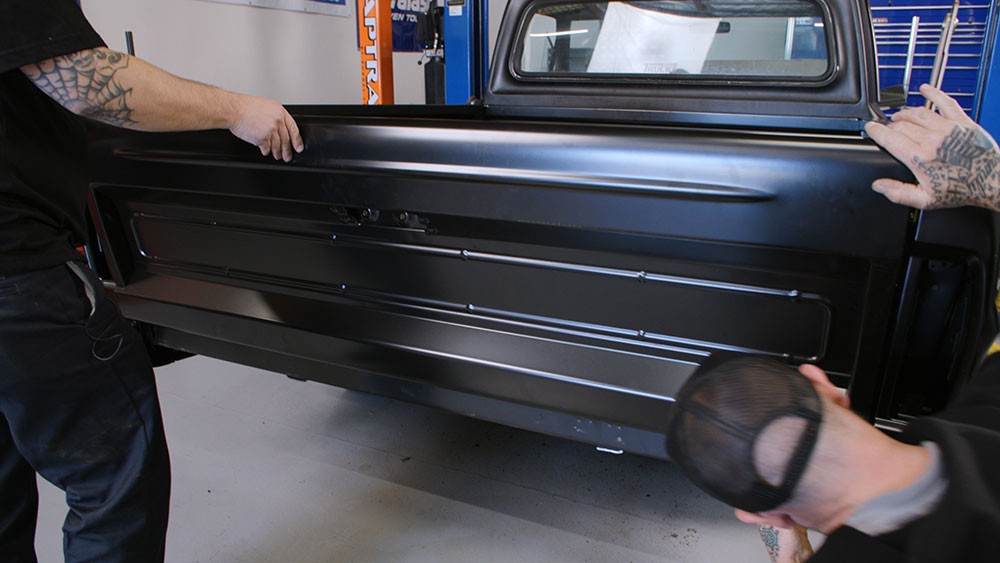
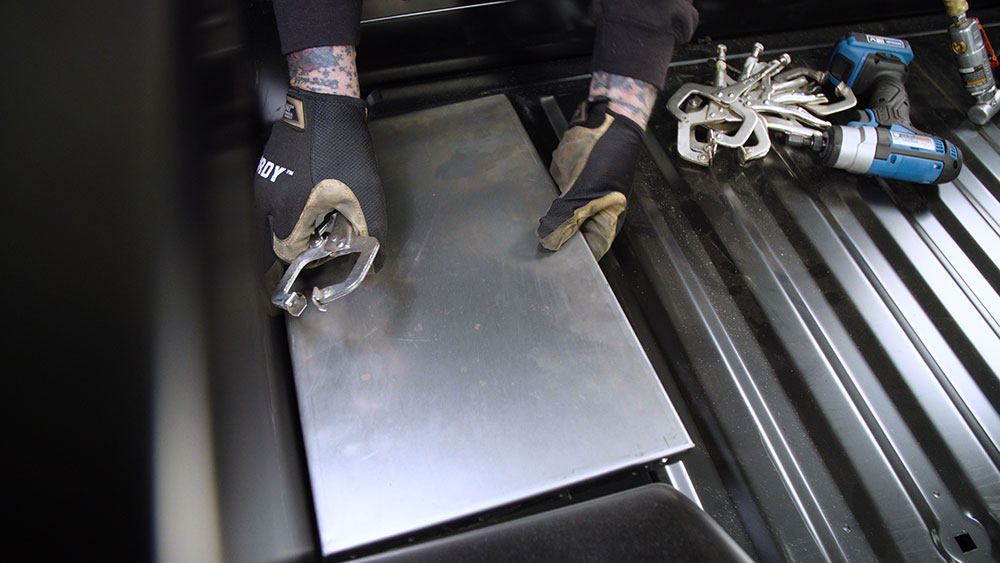
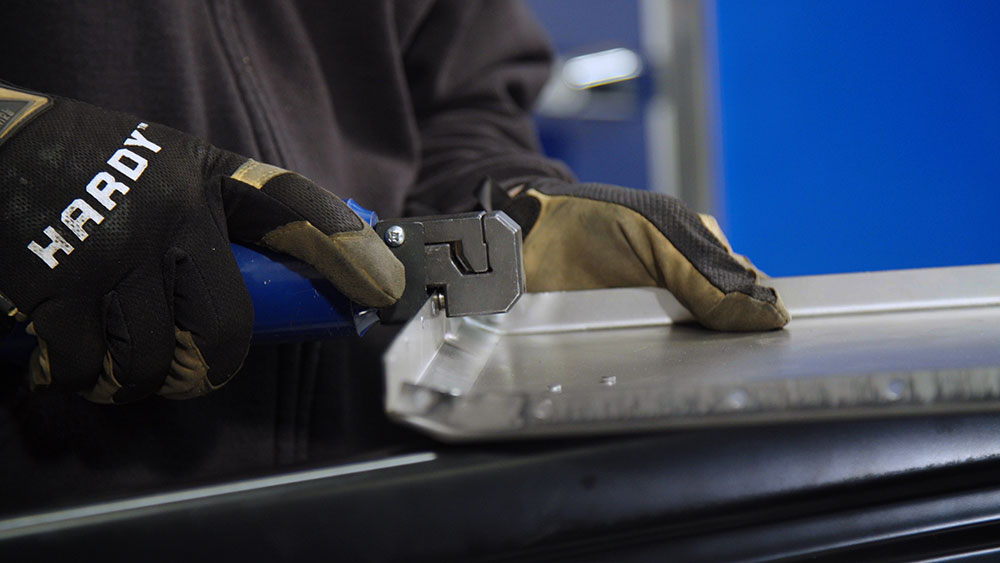
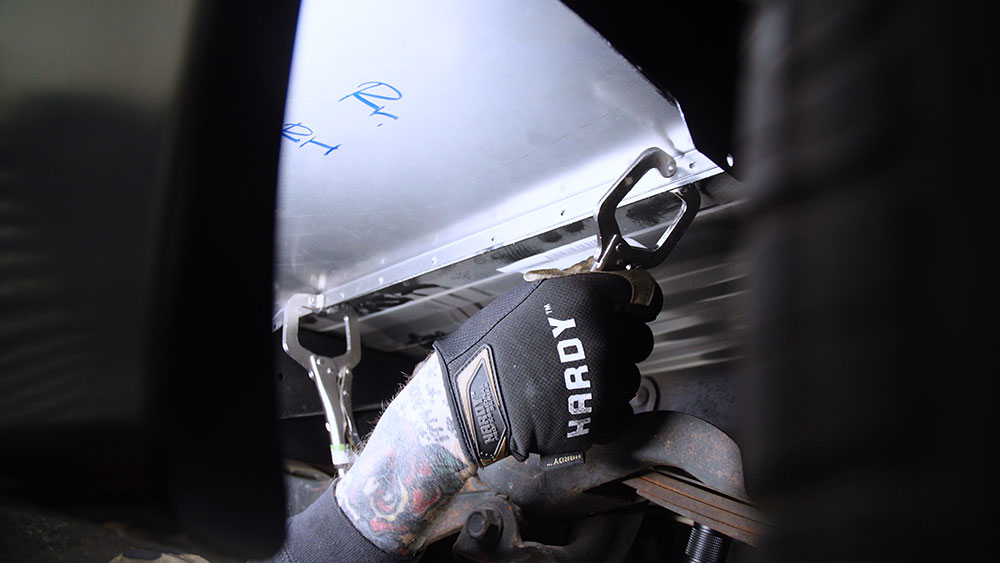
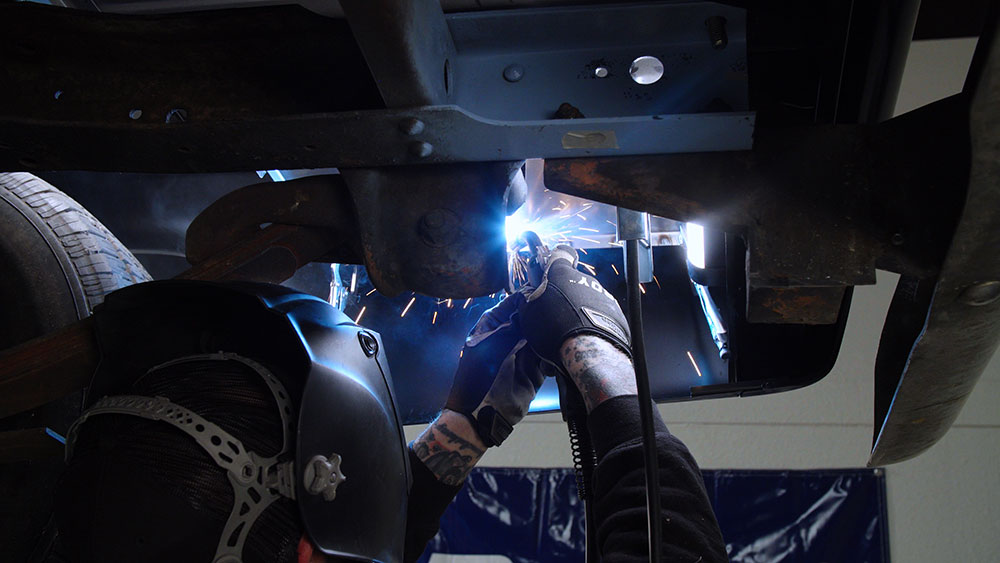
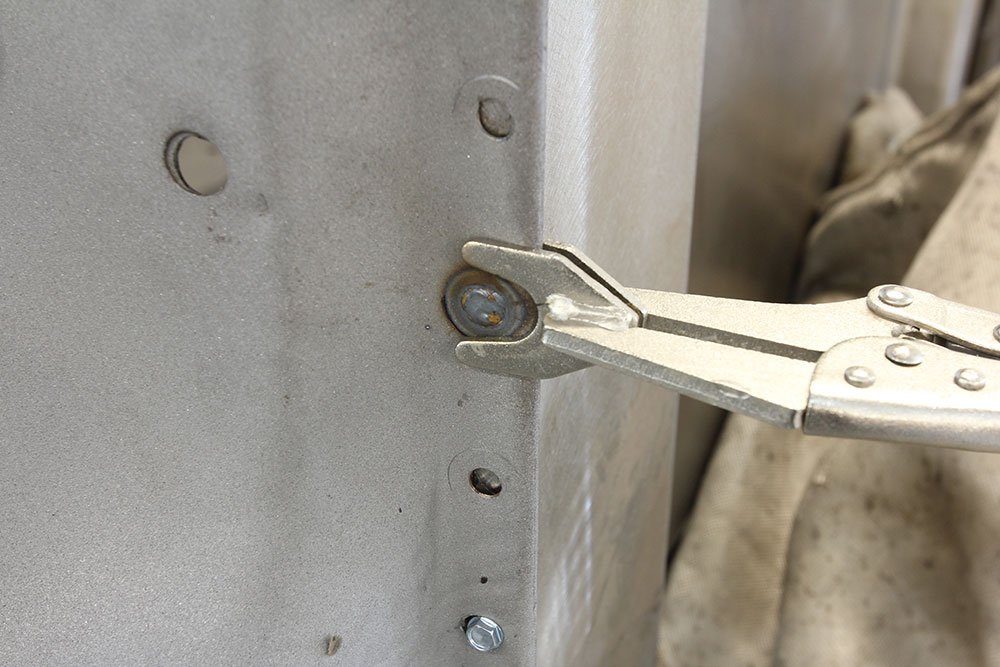
Sources
Classic Performance Products
(800) 760-7438
classicperform.com
Golden Star Classic Auto Parts
(972) 315-3758
goldenstarauto.com
Harbor Freight
harborfreight.com